Material 718 is a nickel-based superalloy that offers exceptional high temperature strength, oxidation resistance, and corrosion resistance. It is widely used in aerospace, power generation, and industrial applications where materials must withstand extreme environments. This comprehensive guide provides key details about material 718 to help engineers, designers, and procurement professionals understand its properties, applications, specifications, installation, and more.
Overview of Material 718
Material 718, also known by trade names like Inconel 718, IN718, and NS163, is a precipitation hardened nickel-chromium alloy containing significant amounts of iron, niobium, and molybdenum along with trace amounts of aluminum and titanium.
Key properties and characteristics of material 718:
Table 1: Properties and Characteristics of Material 718
Properties | Details |
---|---|
Composition | Nickel-chromium alloy with niobium, molybdenum, iron, aluminum, titanium |
Density | 8.19 g/cm3 |
Melting Point | 1260-1335°C |
Strength | Excellent strength from -253 to 704°C |
Hardness | 36-41 HRC |
Toughness | Withstands vibration, thermal shock, fatigue |
Corrosion Resistance | Resists pitting, crevice corrosion even at high temperatures |
Oxidation Resistance | Forms protective oxide layer up to 1000°C |
Weldability | Welds well using GTAW, GMAW, SMAW |
Manufacturability | Hot worked or cold drawn into various forms |
Cost | Higher cost than carbon steels |
The unique properties of material 718 make it well suited for use in extreme temperature, pressure, corrosive, and high stress environments where high strength, hardness, and corrosion resistance are critical.
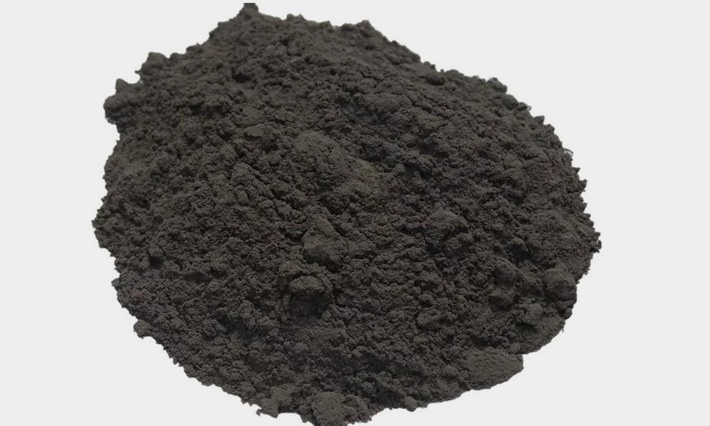
Applications and Uses of Material 718
The exceptional properties of material 718 make it ideal for use in demanding applications including:
Table 2: Applications and Uses of Material 718
Application | Uses |
---|---|
Aerospace | Jet engine and airframe components, blades, discs, fasteners, casings, brackets |
Oil & Gas | Downhole tools, drill collars, wellhead equipment, valves, pumps |
Power Generation | Gas turbine blades, generators, steam turbine parts, heat exchangers |
Automotive | Turbocharger parts, valves, exhaust components |
Chemical Processing | Reactors, piping, heat exchangers, pressure vessels |
Pollution Control | Smokestack scrubbers, waste incinerators, hot gas filters |
Tooling | Extrusion dies, injection molds for plastics, hot work tools |
Medical | Implants, prosthetics that contact bone |
Marine | Seawater pumps, desalinization equipment, offshore rigs |
Heat Treating | Fixtures, trays, baskets, hot work tools |
The combination of strength, corrosion resistance, and high temperature performance makes 718 invaluable for critical parts exposed to extreme environments in key industries.
Specifications of Material 718
Material 718 is manufactured to exacting specifications that govern its chemical composition, mechanical properties, microstructure, and other quality parameters.
Table 3: Specifications and Standards for Material 718
Specification | Details |
---|---|
UNS Number | N07718 |
AMS Specification | AMS 5662, AMS 5663, AMS 5664 |
ASTM Specification | ASTM B637 |
ISO Specification | ISO 6207 |
Chemical Composition | Ni 50-55%, Cr 17-21%, Nb 4.75-5.5%, Mo 2.8-3.3%, Ti 0.65-1.15%, Al 0.2-0.8%, C 0.08% max |
Density | 8.19 g/cm3 |
Melting Range | 1260-1335°C |
Mechanical Properties | Tensile strength 1241 MPa, Yield strength 1034 MPa, Elongation 12% |
Grain Size | ASTM 6 or finer |
Hardness | 36-41 HRC |
Microstructure | Austenitic face centered cubic (FCC) matrix with precipitation hardening |
Meeting the certified specifications ensures that material 718 performs consistently across applications. Rigorous quality control and testing is done during manufacturing.
Key Design Considerations for Material 718
To leverage the full potential of material 718, engineers must design components appropriately considering factors like:
Table 4: Key Design Factors for Material 718
Design Consideration | Details |
---|---|
Strength Requirements | Balance high strength with workability, match strength levels needed |
Fatigue Resistance | Design for cyclic stress conditions, utilize precipitation hardening |
Corrosion Resistance | Account for operating environment, temperatures, stresses |
Tolerances | Maintain tight tolerances for fit, clearance, dimensions |
Weight Reduction | Optimize designs to reduce weight where possible |
Cost Reduction | Balance performance needs with cost, utilize trades between machining vs casting/forging |
Manufacturability | Account for forming, machining, joining characteristics |
Inspection | Include access for inspection of critical areas |
Testing | Validate designs meet specifications via testing |
Codes | Adhere to required industrial codes for the application |
Thoughtful design considering these factors allows engineers to fully utilize the advantages of 718 while mitigating limitations.
Forms and Processing of Material 718
Material 718 is available from suppliers in a wide array of forms, shapes, and processing conditions to suit specific design requirements:
Table 5: Forms and Processing Options for Material 718
Form/Processing | Details | Applications |
---|---|---|
Bar Stock | Hot rolled, cold drawn rounds, squares, hexes | Machined parts, pump shafts, fasteners |
Plate | Hot rolled plate, sheared plate | Structural parts, casings, brackets |
Sheet | Hot rolled, cold rolled, sheared sheet | Shrouds, ducts, covers |
Tubing | Seamless, welded | Piping, heat exchangers, cylinders |
Castings | Investment cast, sand cast | Complex shaped parts, housings |
Extrusions | Hot extruded | Aircraft struts, channels |
Forgings | Closed die forgings | Rings, discs, fasteners |
Welding | GTAW, GMAW, SMAW | Fabricated components and assemblies |
Heat Treatment | Solution anneal and age, stabilize | Optimize final properties |
Coatings | Electroplated, conversion coatings | Corrosion protection |
Additive Mfg | Powder bed, directed energy deposition | Complex geometries |
Choosing the optimal form and processing route enables designers to achieve the right balance of properties, performance, and cost for their specific application.
Suppliers and Availability of Material 718
As a widely used superalloy, material 718 is readily available from leading global suppliers of high performance alloys:
Table 6: Leading Suppliers of Material 718
Supplier | Product Designations | Forms Available |
---|---|---|
Haynes International | Haynes 718 alloy | Bar, sheet, plate, tube |
Carpenter Technologies | Pyromet 718 | Bar, billet, wire |
Special Metals Corp | Inconel 718 | Bar, plate, sheet, tube, welding wire |
VSMPO | EI-718 | Plate, sheet, bar |
Allegheny Technologies | U718 | Bar, billet, plate, sheet |
Sandvik Materials | Sanicro 718 | Bar, wire |
Material 718 is readily available with short lead times from distributors in various forms including bar, plate, sheet, tube, and welding consumables. Custom forgings, castings, and fasteners are also procurable from approved suppliers.
Table 7: Price Ranges for Material 718
Form | Price Range |
---|---|
Plate | $8-12 per lb |
Bar | $7-10 per lb |
Sheet | $12-18 per lb |
Tube | $15-22 per lb |
Forging | $15-25 per lb |
Castings | $18-30 per lb |
Prices vary based on order volume, size, lead time, testing/inspection requirements, and supplier. Large volume OEM agreements can reduce costs significantly.
Installation of Material 718 Components
Proper installation of material 718 components requires adherence to specifications, use of qualified procedures, and thorough documentation:
Table 8: Material 718 Installation Guidelines
Parameter | Recommendations |
---|---|
Handling | Use proper lifting equipment, avoid surface damage |
Storage | Keep indoors, away from chemical exposure |
Fastening | Use specified torque values, anti-seize compounds |
Gaskets | Select compatible gasket materials, replace as needed |
Sealing | Ensure leak-tight seals, quality welds for pressure containment |
Connections | Double check ratings for pipes, valves, fittings |
Documentation | Record torque values, leak checks, any anomalies |
Testing | Validate pressure tests, integrity tests prior to operation |
Safety | Wear personal protective equipment, safe work permits |
Following qualified installation procedures is vital to prevent leaks, damage, or unsafe conditions when putting 718 systems into service. Thorough documentation provides quality records.
Operation and Maintenance of Material 718 Equipment
To achieve reliable performance and long service life from material 718 equipment, proper operation and maintenance protocols must be implemented:
Table 9: Material 718 Operation and Maintenance Guidelines
Activity | Recommendations |
---|---|
Monitoring | Continuously monitor pressures, flows, temps, vibration |
Inspection | Regularly inspect for wear, corrosion, cracks |
Lubrication | Maintain proper lube oil levels, change filters |
Seals | Replace worn or damaged seals and gaskets |
Fasteners | Check and re-torque critical fasteners |
Cleaning | Follow proper procedures to remove deposits and avoid damage |
Overhaul | Disassemble, inspect, and repair components per schedule |
Documentation | Record operating parameters, maintenance actions |
Training | Ensure personnel are properly trained on procedures |
Safety | Use lock-out tag-out, personal protective equipment |
Operating and maintaining 718 equipment according to OEM guidelines ensures safe, reliable long-term performance.
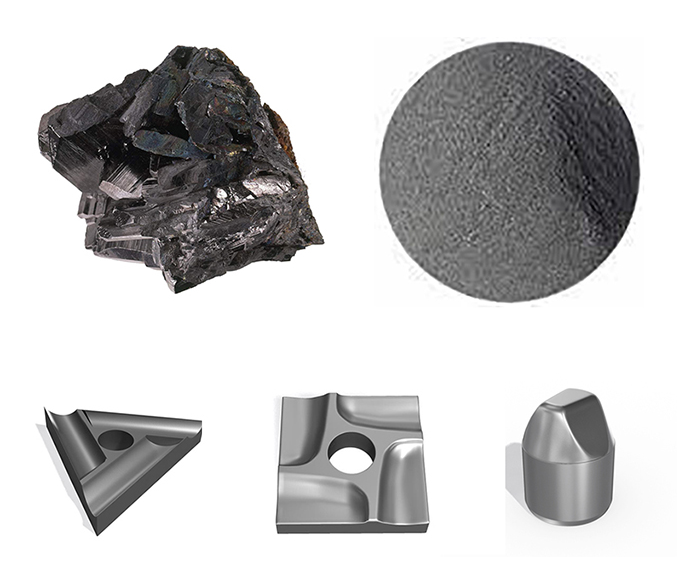
Choosing a Reliable Material 718 Supplier
With so many suppliers offering material 718, choosing a reliable source is key to ensuring high quality consistent components:
Table 10: How to Choose a Reliable Material 718 Supplier
Consideration | Best Practices |
---|---|
Reputation | Select established suppliers with proven track records |
Quality Systems | ISO 9001 and AS9100 certifications |
Testing Capabilities | Supplier should have extensive in-house lab testing capabilities |
Inventory | Look for distributors with a large stock of standard sizes to enable quick delivery |
Lead Times | Ask about current lead times and availability for your specific needs |
Technical Support | Supplier should provide knowledgeable technical support |
Documentation | Manufacturer mill certifications should be provided |
Quality Assurance | Ability to provide third party inspection services |
Reliability | On time delivery and complete orders are vital |
Value Add | Some offer additional services like heat treating, machining, coating |
Choosing suppliers with in-depth material 718 expertise and capabilities ensures buyers get products that consistently meet specifications.
Pros and Cons of Material 718
Material 718 provides excellent performance in demanding applications, but has some limitations to consider:
Table 11: Pros and Cons of Material 718
Pros | Cons |
---|---|
Excellent strength at high temperatures | More expensive than lower alloys |
Resists creep, rupture, and fatigue failure | Subject to strain-age cracking during forming |
Withstands thermal shock and cycling | Lower corrosion resistance than stainless steels |
Oxidation resistant up to 1000°C | Requires heat treatment to achieve full properties |
Welds readily for fabrication | Sensitive to contamination during processing |
Machinable using high performance tooling | Difficult to join dissimilar metals |
Formable into complex shapes | Limited to continuous use up to 704°C |
For optimal results, design and process engineers must work to maximize the advantages of 718 while minimizing Limitations through proper design, manufacturing, inspection, and operation.
Material 718 versus Other Superalloys
Material 718 is part of the nickel-chromium superalloy family. It offers an optimal balance of properties when compared to other superalloys:
Table 12: How Material 718 Compares to Other Superalloys
Alloy | Strength | Toughness | Weldability | Corrosion Resistance | Temperature Resistance | Cost |
---|---|---|---|---|---|---|
718 | Excellent | Excellent | Excellent | Moderate | Excellent | Moderate |
Waspaloy | Excellent | Good | Fair | Moderate | Excellent | High |
Rene 41 | Good | Moderate | Good | Moderate | Excellent | Moderate |
Hastelloy X | Moderate | Excellent | Excellent | Excellent | Good | Very High |
Haynes 230 | Excellent | Moderate | Good | Excellent | Excellent | High |
Inconel 625 | Moderate | Excellent | Excellent | Excellent | Moderate | Moderate |
Material 718 provides the best all-around combination of strength, weldability, and corrosion resistance for many demanding applications, especially where cost is a consideration.
Material 718 and Additive Manufacturing
Additive manufacturing (AM) enables fabrication of complex 718 parts that would be extremely difficult or impossible to make via traditional methods. AM with 718 provides benefits like:
- Ability to produce complex geometries not feasible with casting or forging
- Reduced lead times and costs for small production volumes
- Ability to optimize designs for performance rather than manufacturability
- Reduced waste compared to subtractive fabrication methods
- Ability to repair or add features to existing components
- Potential to consolidate assemblies into single printed parts
Limitations of AM with 718 include:
- Higher cost for large production volumes
- Slower build rates than traditional manufacturing
- Post-processing may be required to achieve final properties
- Anisotropic material properties may require design adjustments
- Qualification testing required to validate printed part performance
- Supply chain maturity lags behind conventional production
As the technology develops, AM with 718 will see increased adoption for complex, high value applications in aerospace, energy, and industrial markets.
FAQs
Q: What is material 718 used for?
A: Material 718 is most widely used in jet engines, gas turbines, chemical and petrochemical plants, and other applications requiring exceptional strength and corrosion resistance at elevated temperatures.
Q: Is material 718 weldable?
A: Yes, 718 can be readily welded using Gas Tungsten Arc Welding (GTAW), Gas Metal Arc Welding (GMAW), Shielded Metal Arc Welding (SMAW), and other welding processes. Proper procedures must be followed to avoid cracking.
Q: What is the difference between Inconel 718 and Haynes 718?
A: Both are trademarked names for alloy 718. Inconel 718 is produced by Special Metals Corporation, while Haynes 718 is produced by Haynes International. The alloys have nearly identical compositions and properties.
Q: What is the tensile strength of 718?
A: The minimum specified tensile strength of annealed and aged 718 is 1241 MPa. Actual strength can reach 1370 MPa or higher depending on processing.
Q: What metals can 718 be welded to?
A: 718 can be welded to steels, stainless steels, and dissimilar nickel alloys with proper procedures. Joint design, filler material, and post weld heat treatment are critical factors.
Q: What is the maximum operating temperature of 718?
A: While 718 has useful strength up to 1095°C, it is typically limited to continuous use up to 704°C for most applications. Higher temp capability is possible depending on loading and environment.
Q: Is material 718 compatible with 316 stainless steel?
A: Yes, 718 and 316 stainless can be successfully joined and used together when proper design, surface preparation, dissimilar welding procedures are followed.
Q: What is the difference between 718 and 725 alloys?
A: Alloy 725 has slightly improved strength and corrosion resistance thanks to additions of tantalum and niobium. 725 is more expensive but offers advantages for demanding chemical process industry applications.