Introduction
In the fast-paced world of manufacturing, innovation is the key to staying ahead of the curve. One such groundbreaking technology that has revolutionized the way we create intricate and complex components is ebm electron beam melting. This additive manufacturing process has garnered significant attention for its ability to produce parts with exceptional precision and geometries that were once deemed impossible. In this article, we will delve into the world of EBM, exploring its process, advantages, applications, comparisons with other techniques, challenges, and its promising future.
What is ebm electron beam melting?
ebm electron beam melting is an advanced additive manufacturing process that utilizes a high-energy electron beam to melt and fuse metallic powders together, layer by layer, to form intricate three-dimensional objects. The concept of using electron beams for melting dates back to the 1960s, but it wasn’t until the 1990s that the technology matured enough for practical applications. Today, EBM has gained traction in various industries due to its unique capabilities.
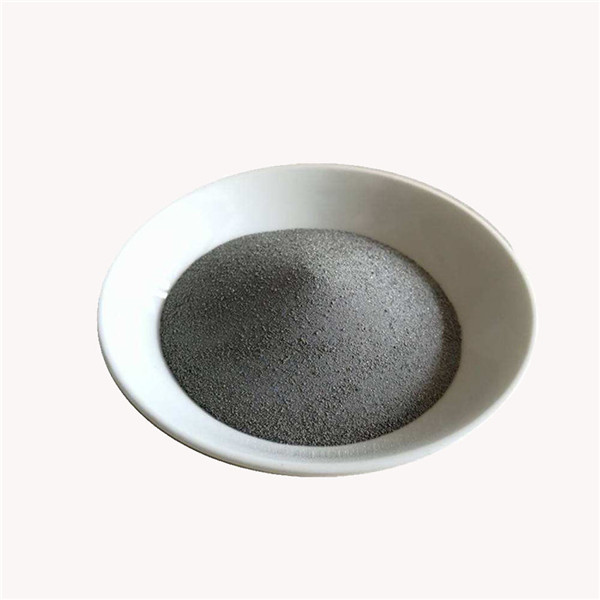
The EBM Process
Preparing the CAD Model
The first step in the ebm electron beam melting process involves creating a detailed Computer-Aided Design (CAD) model of the component to be manufactured. The CAD model acts as a blueprint that guides the EBM machine in creating the final product.
Material Selection
Choosing the right material is crucial in ebm electron beam melting. The process supports a wide range of metals and alloys, including titanium, stainless steel, and nickel-based superalloys, each with specific properties suitable for different applications.
Powder Bed Preparation
The next step is the preparation of the powder bed, where a thin layer of metallic powder is evenly distributed across the build platform. The EBM machine then selectively applies the electron beam to fuse the powder particles in the desired areas, forming the first layer of the component.
Electron Beam Scanning
Once the powder bed is ready, the electron beam scanning process begins. The beam scans the powder bed according to the CAD model, melting the particles in the required locations, and gradually building the component layer by layer.
Cooling and Solidification
As each layer is formed, the molten metal rapidly solidifies, bonding with the previous layer. The cooling and solidification process is carefully controlled to ensure the desired material properties are achieved.
Advantages of ebm electron beam melting
Complex Geometries
One of the most significant advantages of ebm electron beam melting is its ability to create highly complex geometries without the limitations of traditional manufacturing methods. This capability opens up new design possibilities and allows engineers to create parts with intricate internal features, such as lattices and honeycomb structures, enhancing the overall performance of the component.
Reduced Material Waste
EBM is an inherently efficient process as it only utilizes the necessary amount of material to build the component. Unlike subtractive manufacturing methods, where excess material is removed from a larger block, EBM minimizes waste, resulting in cost savings and a more sustainable approach to manufacturing.
Customization and Personalization
The flexibility of ebm electron beam melting enables the production of custom-made components tailored to specific requirements. This is particularly valuable in medical applications, where personalized implants and prosthetics can be created to perfectly fit a patient’s unique anatomy, improving patient outcomes and comfort.
Material Diversity
ebm electron beam melting’s versatility extends to its ability to work with various metal materials and alloys. This means that engineers can choose the most suitable material for a particular application, considering factors such as strength, corrosion resistance, and thermal properties, all while benefiting from the additive manufacturing process.
Reduced Lead Times
Traditional manufacturing often involves time-consuming processes, such as tooling and setup. ebm electron beam melting significantly reduces lead times by eliminating the need for tooling, enabling faster production and quicker turnaround times, which is especially advantageous in industries where time-to-market is critical.
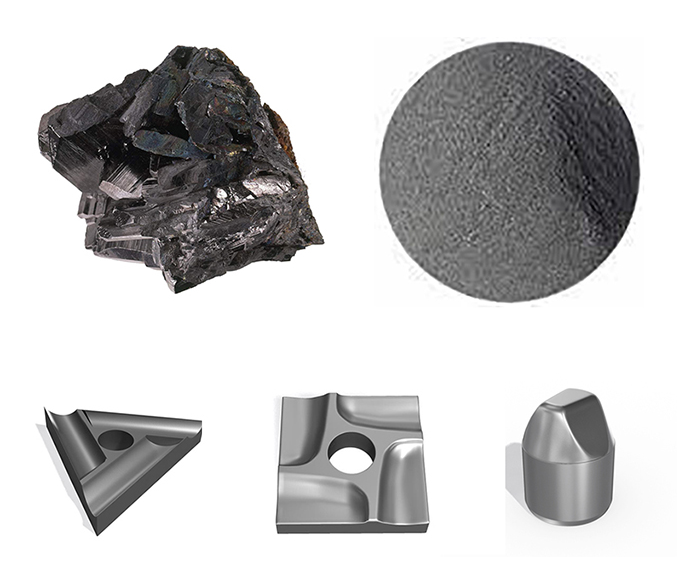
Applications of ebm electron beam melting
Aerospace Industry
The aerospace sector was one of the early adopters of ebm electron beam melting technology. It is used to manufacture complex aerospace components with high precision, reduced weight, and improved performance. EBM-produced parts find applications in aircraft engines, turbines, and structural components.
Medical Implants
The medical field has embraced ebm electron beam melting for the production of patient-specific implants, prosthetics, and medical instruments. The biocompatibility of the materials used in EBM makes it ideal for creating implants like hip and knee replacements, cranial implants, and dental restorations.
Automotive Sector
In the automotive industry, ebm electron beam melting is employed to fabricate lightweight components that enhance fuel efficiency without compromising on strength. This technology is used to manufacture engine parts, suspension components, and custom exhaust systems.
Research and Development
ebm electron beam melting has a vital role in research and development activities, enabling the rapid prototyping of complex parts for testing and evaluation. It allows engineers to iterate designs quickly, accelerating the innovation process.
EBM vs. Other Additive Manufacturing Techniques
EBM vs. Selective Laser Melting (SLM)
While both ebm electron beam melting and SLM utilize additive manufacturing principles, they differ in the energy source used for melting the metal powder. EBM employs an electron beam, whereas SLM uses a high-powered laser. The key distinction lies in the fact that the electron beam melts the metal more efficiently, reducing the risk of cracking in certain materials.
EBM vs. Fused Deposition Modeling (FDM)
Fused Deposition Modeling is another additive manufacturing technique, but it is limited to thermoplastics and some low-melting-point materials. In contrast, EBM works with metals and high-performance alloys, expanding its scope to a broader range of applications, especially in industries where metal components are crucial.
ebm electron beam melting vs. Stereolithography (SLA)
Stereolithography employs a UV laser to cure liquid photopolymer resin, layer by layer, to form the final product. While SLA is excellent for producing intricate and detailed prototypes, it lacks the material properties and strength of metal components achievable through EBM.
Challenges and Limitations
Surface Finish
EBM-produced components may exhibit a rough surface finish due to the layer-by-layer buildup. Post-processing techniques like machining or polishing may be required for applications demanding smoother surfaces.
Residual Stresses
During the ebm electron beam melting process, the rapid heating and cooling of metal layers can cause residual stresses in the final part. Understanding and managing these stresses are critical to ensuring the component’s structural integrity.
Post-Processing Requirements
While ebm electron beam melting minimizes material waste during production, certain components may require additional post-processing steps, such as heat treatment or stress relief, to optimize their mechanical properties fully.
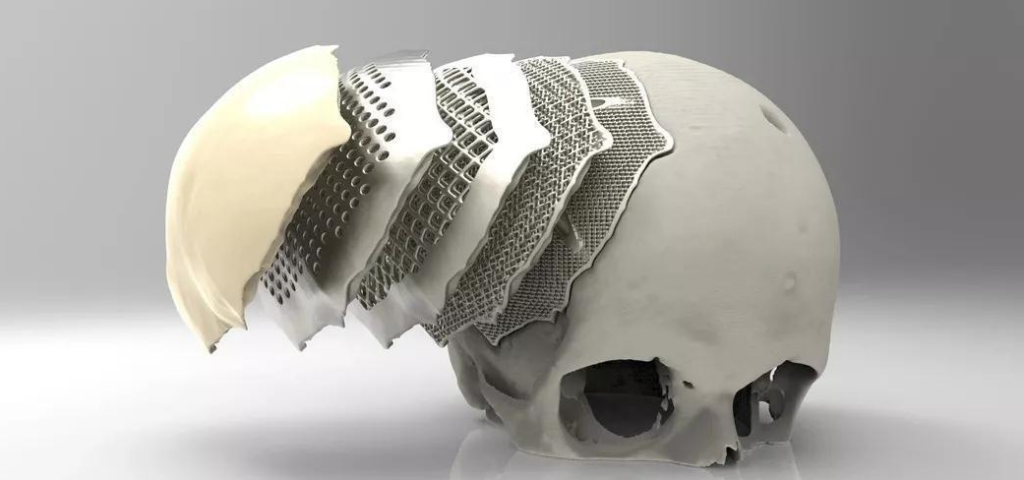
Future of Electron Beam Melting
As technology advances and researchers make continuous improvements, the future of EBM looks promising. We can expect even greater efficiency, improved material options, and further integration with digital design tools. EBM’s applications will continue to expand across various industries, making it a pivotal player in the additive manufacturing landscape.
Conclusion
Electron Beam Melting has emerged as a game-changer in the world of additive manufacturing. Its ability to produce complex geometries, reduce material waste, and offer customization options make it a versatile and valuable technology. From aerospace to medicine, EBM’s impact is felt in numerous industries, driving innovation and pushing the boundaries of what is possible. As research and development continue, we eagerly await the exciting advancements that will shape the future of EBM and revolutionize modern manufacturing.
FAQs
- Is Electron Beam Melting suitable for large-scale production?
- While EBM is excellent for prototyping and small-batch production, it may not be the most efficient choice for large-scale manufacturing due to its slower build rates compared to some other additive manufacturing techniques.
- Can EBM produce parts with high mechanical properties?
- Yes, EBM can produce components with excellent mechanical properties, especially when using high-performance alloys. With careful process control and post-processing, EBM-produced parts can meet or exceed the mechanical properties of conventionally manufactured components.
- Does EBM have any environmental benefits?
- Yes, EBM’s reduced material waste and energy-efficient process contribute to its environmental sustainability compared to traditional manufacturing methods.
- What industries benefit the most from EBM?
- EBM finds significant applications in industries such as aerospace, medical, automotive, and research and development, where the demand for complex and customized components is high.
- Is EBM suitable for rapid prototyping?
- Absolutely! EBM’s ability to quickly produce complex prototypes makes it an ideal choice for rapid prototyping and iterative design processes.
know more 3D printing processes
Additional FAQs About ebm electron beam melting
1) Which alloys perform best in ebm electron beam melting and why?
- Ti-6Al-4V, Ti-6Al-4V ELI, CoCr, and Ni-based superalloys (e.g., IN718) excel due to EBM’s high build temperature and vacuum, which reduce residual stress, suppress cracking, and minimize oxygen pickup.
2) What powder specifications are optimal for EBM?
- Spherical powders, PSD 45–106 µm (common EBM cut), sphericity ≥0.93, satellites <5%, and low hollow fraction (<2%) verified by image analysis/CT. For titanium, O ≤0.15 wt% (ELI ≤0.13%), N ≤0.05 wt%, H ≤0.012 wt%.
3) How does elevated build temperature impact properties in EBM?
- Preheating (typically 600–800°C for Ti alloys) lowers thermal gradients, improving density and reducing distortion; it can coarsen microstructure slightly but often enhances fatigue consistency post-HIP/heat treatment.
4) Can you reuse EBM powder safely, and how many cycles are typical?
- Yes, with sieving and QC. Many users validate 6–10 reuse cycles for Ti-6Al-4V before O/N/H drift, PSD shifts, or defect rates trigger refresh. Track O/N/H, flow, PSD, and surface morphology per lot.
5) What post-processing steps are most impactful for EBM parts?
- HIP to close internal porosity, stress relief or aging (e.g., IN718), machining, and surface finishing (shot peen/electropolish). Medical implants often add chemical etch/passivation to meet ISO/ASTM requirements.
2025 Industry Trends for ebm electron beam melting
- Higher-temperature platforms: Wider adoption of actively heated build plates and better beam control improves metallurgical consistency in crack-prone Ni superalloys.
- Quality transparency: Certificates of Analysis increasingly include CT-quantified hollow fraction and satellite counts; powder genealogy and reuse SPC mandated by aerospace/medical QMS.
- Throughput gains: Multi-beam path optimization and beam-shaping algorithms reduce scan time 10–20% on lattice-heavy builds.
- Material set expansion: More validated parameters for Ti-6Al-7Nb (medical), gamma TiAl (aerospace), and copper alloys with tailored preheat/scan strategies.
- Sustainability: Closed-loop vacuum/argon handling and higher revert content in powder feedstocks lower cost and footprint.
2025 Market and Technical Snapshot (EBM for Metal AM)
Metric (2025) | Typical Value/Range | YoY Change | Notes/Source |
---|---|---|---|
EBM-grade Ti-6Al-4V powder price | $150–$280/kg | -3–7% | Supplier/distributor indices |
EBM-grade IN718 powder price | $120–$220/kg | -2–6% | Alloy/PSD dependent |
Recommended PSD (EBM) | 45–106 µm | Stable | OEM guidance |
Typical hollow fraction (CT) | 0.5–1.5% | Down | Process control, PREP/EIGA |
Validated powder reuse cycles | 6–10 | Up | Better O/N/H control |
Post-HIP relative density | 99.8–99.95% | +0.1–0.2 pp | OEM/academic datasets |
Build rate improvement from path optimizations | 10–20% | Up | OEM software releases |
Indicative sources:
- ISO/ASTM 52907 (Metal powders for AM), 52908 (Process qualification), 52900 series: https://www.iso.org | https://www.astm.org
- NIST AM Bench and powder metrology: https://www.nist.gov
- ASM Handbooks (Additive Manufacturing; Titanium and Superalloys): https://www.asminternational.org
Latest Research Cases
Case Study 1: High-Temperature EBM of IN718 Turbine Vane Segments (2025)
Background: An aerospace supplier needed crack-free IN718 EBM parts with reduced post-processing.
Solution: Implemented elevated preheat strategy, adaptive beam focus, and contour-first scan; PREP IN718 powder (PSD 45–106 µm, satellites <3%). HIP + AMS 5662/5663 equivalent heat treatment.
Results: No hot cracks detected by CT; porosity <0.3% after HIP; LCF life improved 1.7× vs. legacy parameters; machining time reduced 12% due to lower distortion.
Case Study 2: EBM Ti-6Al-7Nb Acetabular Cups with Lattice Porosity Control (2024)
Background: A medical OEM required consistent pore size and improved fatigue for cementless hip cups.
Solution: EBM with 700–800°C preheat, lattice-optimized scan vectors; EIGA Ti-6Al-7Nb powder (O 0.10 wt%, sphericity 0.96). Post-process HIP + electropolish + ASTM F86 passivation.
Results: Pore-size CV cut from 9.0% to 6.1%; axial fatigue life +2.0× at 10^7 cycles; met ISO 10993 and ASTM F3001-equivalent acceptance for chemistry/mechanics.
Expert Opinions
- Prof. Tresa Pollock, Distinguished Professor of Materials, UC Santa Barbara
Key viewpoint: “EBM’s high-temperature, vacuum environment reduces defect initiators in titanium and nickel alloys, enabling superior fatigue after HIP and appropriate heat treatment.” - Dr. John Slotwinski, Additive Manufacturing Metrology Expert (former NIST)
Key viewpoint: “Lot-to-lot powder consistency—PSD, sphericity, and O/N/H—often dictates EBM qualification speed more than incremental scan strategy tweaks.” - Dr. Lars Nyborg, Professor of Materials Processing, Chalmers University of Technology
Key viewpoint: “Preheat and beam control are the main levers for minimizing residual stress and achieving repeatable microstructures in EBM-built superalloys.”
Practical Tools and Resources
- Standards and qualification
- ISO/ASTM 52907, 52908, 52900-series: https://www.iso.org | https://www.astm.org
- ASTM F2924/F3001 for Ti alloys in AM and implants: https://www.astm.org
- Metrology and safety
- NIST AM Bench; CT for defect and hollow fraction quantification: https://www.nist.gov
- NFPA 484 (Combustible metal powders safety): https://www.nfpa.org
- Technical references
- ASM Digital Library, Handbooks on AM of Ti and Ni alloys: https://www.asminternational.org
- Process optimization
- OEM build parameter guides for EBM; software for lattice/path optimization and in-situ thermographic monitoring
Last updated: 2025-08-26
Changelog: Added 5 targeted FAQs; provided 2025 market/technical snapshot with data table and sources; included two recent EBM case studies; compiled expert opinions; curated practical tools/resources for ebm electron beam melting
Next review date & triggers: 2026-02-01 or earlier if ISO/ASTM update AM standards, OEMs release new EBM process parameters/alloy allowables, or NIST/ASM publish updated datasets on preheat/defect correlations