Introduction of spherical titanium powder
Spherical titanium powder is a form of pure titanium powder with a spherical morphology and controlled particle size distribution. It offers excellent flowability, mixability, and consistency which makes it suitable for advanced metal manufacturing processes across industries.
Composition and Characteristics
Table 1: Composition and Key Characteristics of Spherical Titanium Powder
Parameter | Details |
---|---|
Chemical Composition | >99% Titanium. Remaining trace elements like Nitrogen, Oxygen, Carbon, Hydrogen. |
Particle Shape | Highly spherical morphology |
Particle Size Range | Typically 15-45 microns |
Flowability | Excellent due to spherical shape |
Apparent Density | Around 2.7 g/cm3 |
Tap Density | Up to 73% solid titanium density i.e. ~4 g/cm3 |
The precise particle size distribution, oxygen and nitrogen content, flow rates and tap density can be customized as per application requirements.
Manufacturing Process
Spherical titanium powder is manufactured through advanced methods that involve melting titanium feedstock, atomizing and rapidly solidifying droplets into highly spherical powder particles:
- Plasma Atomization uses high energy plasma torches and inert gas jets
- Electrode Induction Gas Atomization (EIGA) relies on induction melted electrodes
- Rotating Electrode Process (REP) generates molten metal streams from tips of spinning titanium electrodes
The key is rapid solidification in an inert atmosphere which results in purity and spherical morphology. Post-production sieving and classification leads to strict fractions.
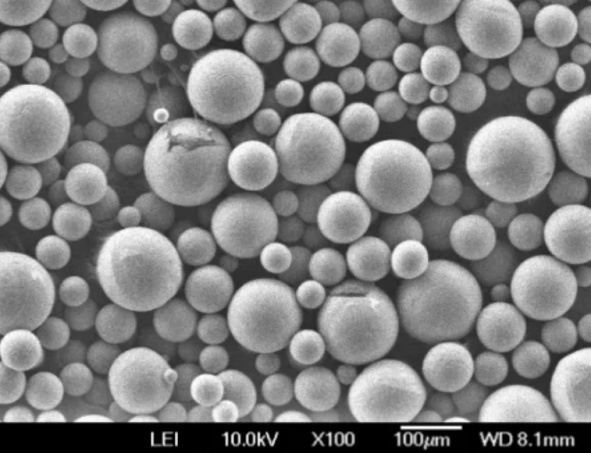
spherical titanium powder Applications and Uses
The unique properties of spherical titanium powder make it suitable for:
Table 2: Major Applications of Spherical Titanium Powder
Area | Applications |
---|---|
Additive Manufacturing | 3D printing implants, aerospace components via DMLS, SLM, EBM |
Powder Metallurgy | Pressing and sintering to make titanium automotive and aircraft parts |
Investment Casting | Injection molds and tooling manufacture |
Biomedical | Porous structures for bone grafts |
Pigments and Catalysts | Chemical and plastics industry |
The high purity, flowability, mixability and consistency of particle size distribution allows reliable high-performance use across powder-based manufacturing processes like metal 3D printing.
Specifications
Spherical titanium conforms to specifications like ASTM B988 and ASTM F3049. Typical values are:
Table 3: Typical Specifications of Spherical Titanium Powder
Parameter | Specification |
---|---|
Particle Size | 15-45 microns |
Oxygen Content | <0.20% |
Nitrogen Content | <0.05% |
Hydrogen Content | <0.015% |
Tap Density | Up to 4 g/cm3 |
Flow Rate | >25 s/50 g |
Particle Size Distribution | D10 > 20 microns; D90 < 63 microns |
Customization of properties like tap density, flow rates, oxygen and nitrogen content is possible based on application requirements.
Price of spherical titanium powder
Table 4: Spherical Titanium Powder Price Ranges of Key Suppliers
Supplier | Price Per Kg |
---|---|
Advanced Powders & Coatings | $100–$200 |
AP&C | $90–$180 |
TLS Technik GmbH & Co | $120–$250 |
Sandvik Osprey | $80–$220 |
Prices depend on order volumes, grades, and customization needs. High purity grades for medical uses are premium priced. Recycled powder can cost 50% less but has lower and inconsistent quality.
Comparison With Alternatives
Table 5: Pros and Cons of Spherical Titanium Powder
Pros | Cons |
---|---|
Excellent flowability and spreadability | Higher cost than alloy variants |
Mixes without segregation | Limited global suppliers, scarce supply |
Allows high density AM printed parts | Reactive, requires inert handling |
Isotropic properties | Post-processing like HIP is a must |
Highest strength-to-weight ratio | Lacks niche alloy properties |
Despite higher costs, spherical titanium powder enables lighter and stronger titanium components across aerospace, automotive, medical, and general engineering domains – applications where properties like corrosion resistance and biocompatibility are vital.
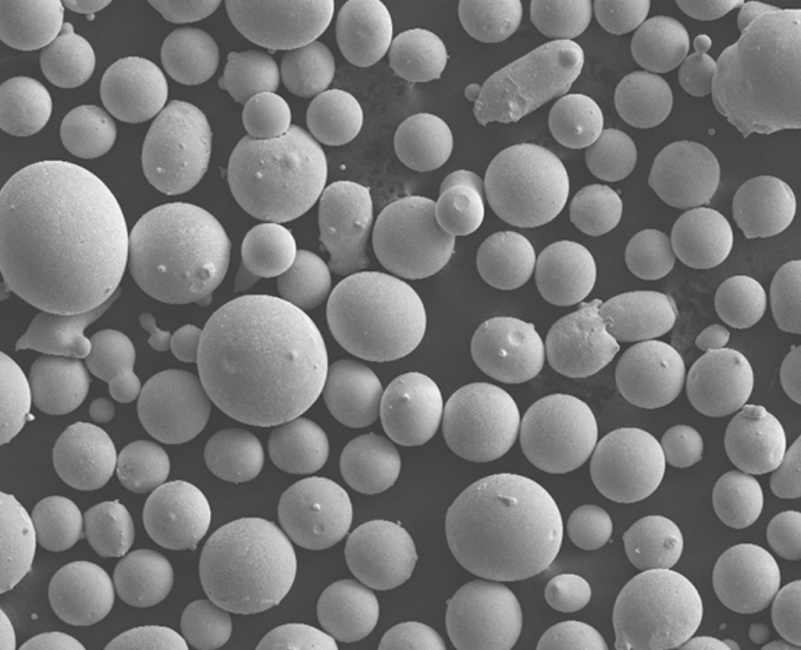
FAQs
What role does particle shape play in metal AM processes?
Spherical shape leads to uniform and dense powder layers during additive manufacturing methods like SLM and DMLS to minimize porosity in printed titanium parts. This results in higher mechanical strength.
How is full density achieved for sintered titanium parts?
Hot Isostatic Pressing (HIP) post-treatment on sintered titanium compacts is vital to eliminate internal pores and voids and achieve full theoretical density. This maximizes strength.
Are there health hazards associated with handling titanium powder?
Like most fine metal powders, handling precautions are vital as titanium powder can be reactive, explosive or cause skin/respiratory sensitization. Use of argon gloves boxes, protective equipment is recommended.