Introduction
In the world of manufacturing and production, innovative technologies continue to revolutionize traditional processes. One such advancement is Selective Laser Melting (SLM) metal printing, which has gained significant popularity and attention in recent years. SLM metal printing enables the creation of complex and intricate metal parts with exceptional precision and accuracy. This article delves into the concept of SLM metal printing, its working principles, advantages, applications, challenges, and future trends.
What is SLM Metal Printing?
SLM metal printing, also known as laser powder bed fusion, is an additive manufacturing technique that utilizes high-powered lasers to selectively melt and fuse metallic powders layer by layer. It falls under the category of powder bed fusion processes, where a laser selectively sinters or melts a powdered material to create a solid object. SLM metal printing allows for the production of intricate and complex metal parts directly from a 3D computer-aided design (CAD) model.
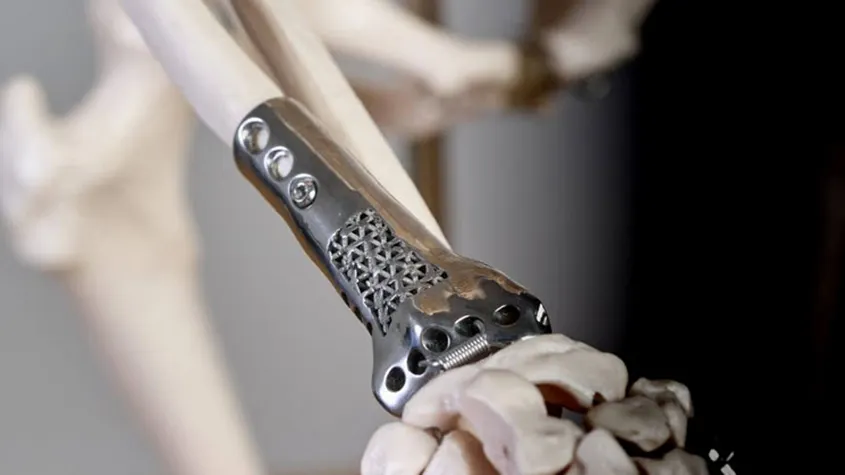
How Does SLM Metal Printing Work?
The process of SLM metal printing begins with the preparation of a digital 3D model of the desired part. This model is sliced into thin layers, typically ranging from 20 to 100 micrometers, which are then sent to the SLM metal printer. The printer spreads a thin layer of metallic powder across the build platform and uses a high-powered laser to selectively melt and fuse the powder according to the cross-sectional shape of the part.
Advantages of SLM Metal Printing
SLM metal printing offers several advantages over traditional manufacturing methods, making it a preferred choice for various industries.
- High Precision and Accuracy: SLM metal printing provides exceptional precision and accuracy, allowing for the creation of intricate and complex geometries with tight tolerances. The layer-by-layer approach ensures that each detail of the design is accurately reproduced, resulting in parts that meet the desired specifications.
- Design Freedom: With SLM metal printing, designers have unparalleled design freedom. Unlike conventional manufacturing processes that have limitations in terms of complexity, SLM metal printing enables the production of parts with intricate internal structures, hollow features, and optimized lightweight designs. This freedom allows for innovative and highly functional designs that were previously unattainable.
- Complex Geometries: SLM metal printing excels in producing parts with complex geometries, including internal channels, lattice structures, and organic shapes. The layering process enables the creation of intricate details and intricate internal features, which are challenging to achieve using traditional methods. This capability opens up new possibilities for engineering and design.
- Material Variety: SLM metal printing supports a wide range of materials, including various metals and alloys. From titanium and stainless steel to nickel-based superalloys, SLM metal printing accommodates diverse material choices to suit different applications. This versatility allows for the production of parts with specific mechanical properties, corrosion resistance, or biocompatibility.
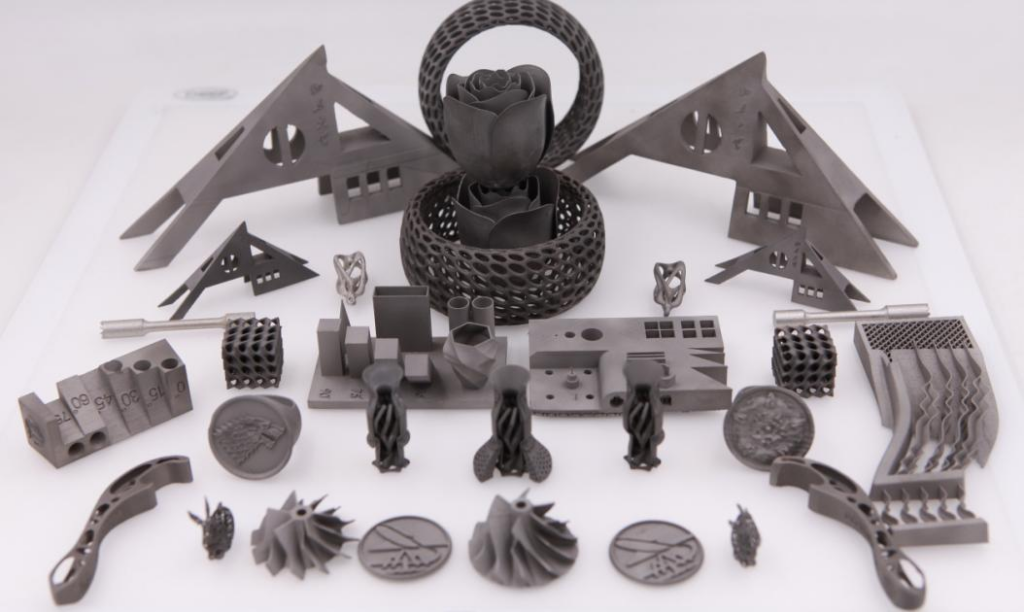
Applications of SLM Metal Printing
SLM metal printing finds applications across multiple industries, where its unique capabilities are leveraged to enhance manufacturing processes and product performance.
- Aerospace Industry: The aerospace industry benefits greatly from SLM metal printing due to its ability to produce lightweight and complex components with excellent strength-to-weight ratios. Parts such as turbine blades, fuel nozzles, and structural components can be manufactured using SLM metal printing, reducing weight and improving fuel efficiency.
- Automotive Industry: In the automotive sector, SLM metal printing is utilized for prototyping, tooling, and the production of high-performance parts. It enables the creation of lightweight and customized components, such as engine parts, exhaust manifolds, and suspension components, which contribute to improved performance and fuel efficiency.
- Medical Field: SLM metal printing has made significant advancements in the medical field. It allows for the production of patient-specific implants, surgical instruments, and prosthetics with complex geometries and tailored designs. The ability to create customized medical devices improves patient outcomes and enhances the overall efficiency of healthcare practices.
- Jewelry and Fashion Industry: SLM metal printing has revolutionized the jewelry and fashion industry by offering the capability to create intricate and personalized designs. Jewelers can now produce unique and complex pieces with intricate details, textures, and patterns that were previously challenging to achieve through traditional manufacturing methods.
Challenges and Limitations of SLM Metal Printing
While SLM metal printing offers numerous benefits, there are also challenges and limitations that need to be considered.
- Material Limitations: Although SLM metal printing supports a wide range of materials, not all metals can be effectively processed using this technique. Some materials may exhibit poor powder flowability, high reactivity, or excessive thermal conductivity, making them difficult to print. Continuous research and development are addressing these limitations to expand the range of printable materials.
- Post-Processing Requirements: Parts produced through SLM metal printing often require post-processing steps such as heat treatment, surface finishing, and machining to achieve the desired mechanical properties and surface quality. These additional steps increase the overall production time and cost.
- Production Speed: SLM metal printing is a relatively slow process compared to traditional manufacturing methods. Building complex parts layer by layer requires time, and the production speed is influenced by factors such as part geometry, size, and complexity. While advancements are being made to improve printing speed, it remains a consideration in large-scale production scenarios.
- Cost: SLM metal printing can be more expensive compared to traditional manufacturing methods, especially for small-scale production. The cost of specialized equipment, high-quality metal powders, post-processing steps, and skilled operators contribute to the overall expenses. However, as the technology continues to evolve and adoption increases, economies of scale and advancements in materials may help reduce costs.
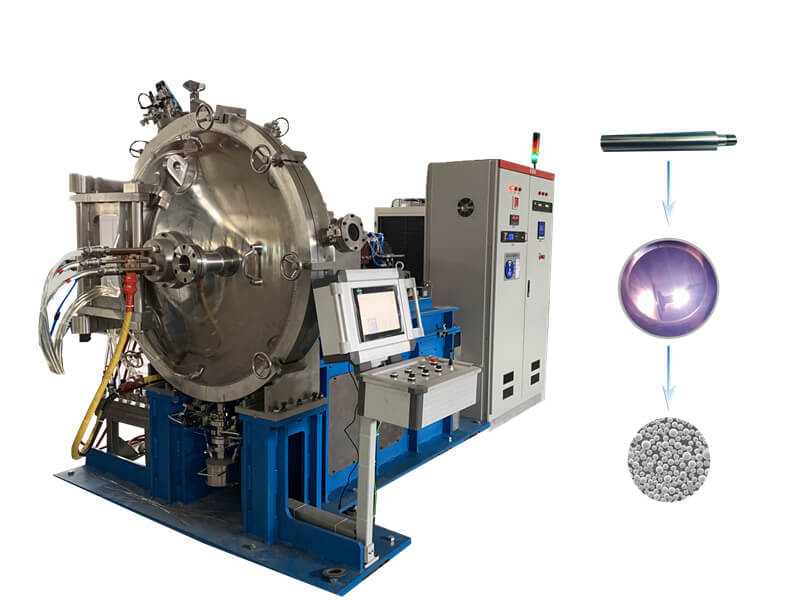
Future Trends in SLM Metal Printing
The future of SLM metal printing looks promising, with several trends and developments on the horizon.
- Increased Material Options: Research and development efforts are focused on expanding the range of materials compatible with SLM metal printing. This includes the exploration of new alloys, composites, and even multi-material printing capabilities. Increased material options will further enhance the versatility and applicability of SLM metal printing across industries.
- Enhanced Printing Speed: Improving printing speed is an ongoing area of research. Advancements in laser technology, scanning strategies, and optimization algorithms are being pursued to accelerate the printing process without compromising the quality and precision of the final parts. Faster production speeds will drive efficiency and enable larger-scale manufacturing applications.
- Integration of AI and Machine Learning: The integration of artificial intelligence (AI) and machine learning (ML) in SLM metal printing is expected to revolutionize the technology. AI algorithms can optimize part designs for improved performance and efficiency, predict potential defects or failures, and optimize process parameters to achieve better outcomes. The combination of AI/ML and SLM metal printing will unlock new possibilities for advanced manufacturing.
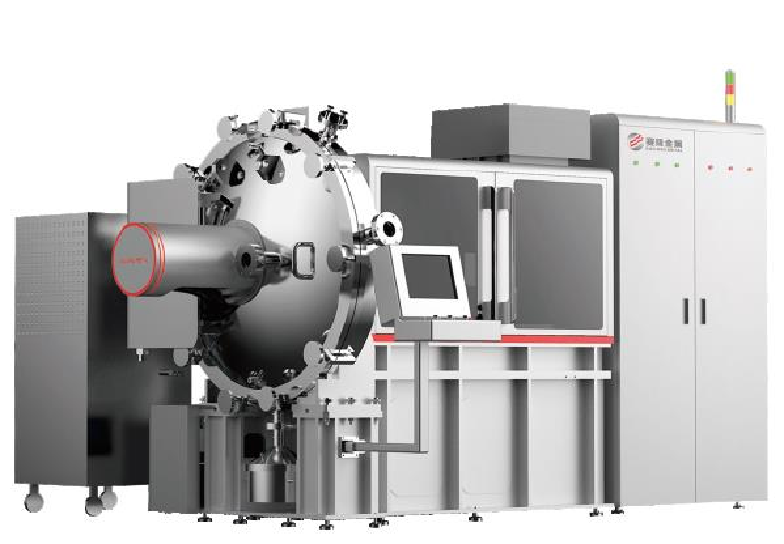
Conclusion
SLM metal printing has emerged as a game-changing technology in the world of manufacturing. Its ability to produce complex and precise metal parts with design freedom has revolutionized various industries, including aerospace, automotive, medical, and jewelry. While challenges such as material limitations, post-processing requirements, and cost remain, ongoing research and development are addressing these issues. The future of SLM metal printing holds exciting possibilities with increased material options, enhanced printing speed, and the integration of AI and machine learning. As the technology continues to evolve, SLM metal printing will continue to reshape the manufacturing landscape and unlock new levels of innovation.
FAQs
- Is SLM metal printing the same as 3D printing? No, SLM metal printing is a specific type of 3D printing that focuses on selectively melting and fusing metallic powders to create metal parts. It is a subset of the broader category of additive manufacturing.
- Can SLM metal printing be used for large-scale production? While SLM metal printing is suitable for small to medium-scale production, it may face challenges in terms of production speed and cost-effectiveness for large-scale manufacturing. However, ongoing advancements are addressing these limitations.
- What are the main advantages of SLM metal printing over traditional manufacturing methods? The main advantages of SLM metal printing include high precision and accuracy, design freedom, the ability to produce complex geometries, and a wide range of material options.
- Does SLM metal printing require any post-processing steps? Yes, parts produced through SLM metal printing often require post-processing steps such as heat treatment, surface finishing, and machining to achieve the desired mechanical properties and surface quality.
- What are the potential applications of SLM metal printing in the medical field? SLM metal printing is utilized in the medical field for producing patient-specific implants, surgical instruments, and customized prosthetics with complex geometries and tailored designs. It offers improved patient outcomes and enhances healthcare practices.