1. Introduction
In recent years, additive manufacturing has revolutionized the manufacturing industry by offering new possibilities for creating complex and high-performance components. One material that stands out in this field is Inconel 625, a nickel-based superalloy renowned for its exceptional properties. In this article, we will explore the intersection of Inconel 625 additive manufacturing, examining the benefits, applications, challenges, and future prospects of this exciting combination.
2. What is Inconel 625?
Inconel 625 is a nickel-chromium-based superalloy known for its excellent resistance to extreme temperatures, corrosion, and mechanical stress. It contains a balanced composition of nickel, chromium, molybdenum, and niobium, with smaller amounts of other elements. This unique combination of elements provides Inconel 625 with remarkable strength, toughness, and resistance to oxidation and pitting.
3. The Rise of Additive Manufacturing
Additive manufacturing, also known as 3D printing, has gained significant traction across industries due to its ability to fabricate complex geometries and reduce material waste. Unlike traditional manufacturing methods, which involve subtractive processes such as cutting or milling, additive manufacturing builds objects layer by layer using computer-aided design (CAD) models. This approach offers unparalleled design freedom and opens up new opportunities for creating intricate and customized components.
4. Inconel 625 and Additive Manufacturing: A Perfect Match
The combination of Inconel 625 and additive manufacturing brings together the benefits of both the material and the process. Inconel 625’s high-temperature strength, corrosion resistance, and fatigue resistance make it an ideal candidate for demanding applications. Additive manufacturing complements these properties by enabling the production of complex geometries that are difficult or even impossible to achieve using conventional methods.
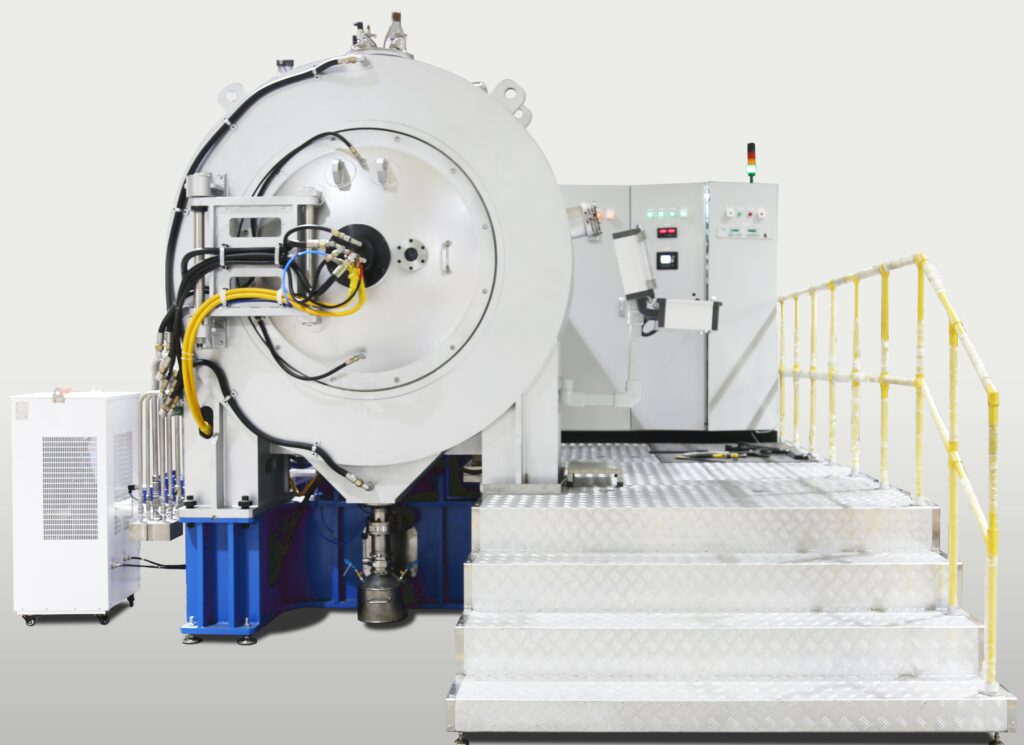
5. Benefits of Inconel 625 Additive Manufacturing
1. Design Freedom and Complexity
One of the key advantages of Inconel 625 additive manufacturing is the freedom it offers in design. Traditional manufacturing methods often have limitations when it comes to complex shapes and internal structures. With additive manufacturing, intricate designs can be easily realized, allowing for optimized performance and reduced weight in aerospace, automotive, and other industries.
2. Cost and Time Efficiency
Additive manufacturing can significantly reduce production costs and lead times compared to traditional methods. By eliminating the need for tooling and minimizing material waste, manufacturers can achieve cost savings. Additionally, the ability to produce components on-demand reduces inventory costs and enables rapid prototyping and iterative design improvements.
3. Superior Material Properties
Inconel 625 already possesses exceptional material properties, and additive manufacturing further enhances its performance. The layer-by-layer deposition process allows for improved control over the microstructure, resulting in components with enhanced strength, fatigue resistance, and corrosion resistance. This makes Inconel 625 additive manufacturing suitable for critical applications in harsh environments.
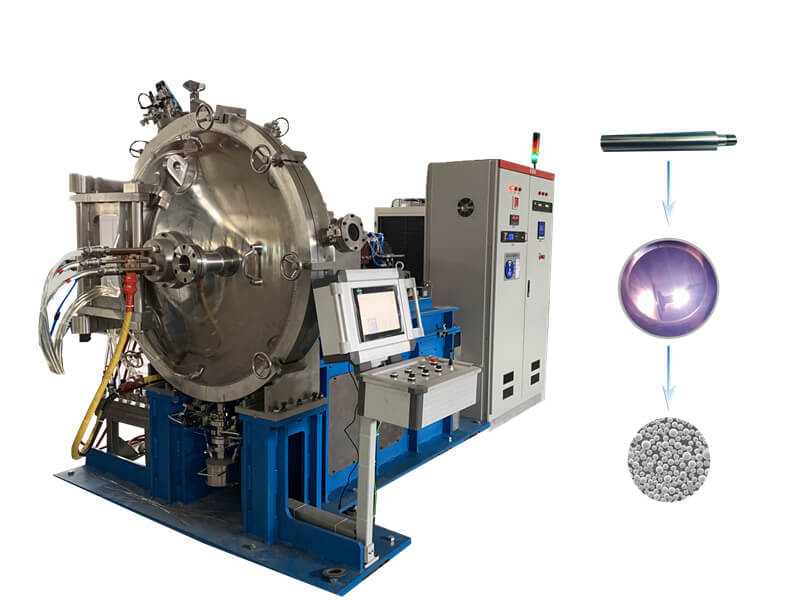
6. Applications of Inconel 625 Additive Manufacturing
Inconel 625 additive manufacturing finds applications in various industries due to its unique combination of material properties and the advantages offered by the additive manufacturing process.
1. Aerospace Industry
The aerospace industry demands components that can withstand extreme temperatures, high mechanical stress, and corrosive environments. Inconel 625 additive manufacturing provides a solution by enabling the production of complex aerospace components such as turbine blades, engine parts, and structural elements. The high strength, heat resistance, and excellent fatigue properties of Inconel 625 make it an ideal choice for aerospace applications where reliability and performance are paramount.
2. Oil and Gas Sector
In the oil and gas sector, equipment operates in challenging conditions including high temperatures, corrosive environments, and exposure to harsh chemicals. Inconel 625 additive manufacturing allows for the fabrication of components such as valves, couplings, and downhole tools with superior resistance to corrosion and erosion. The ability to produce intricate geometries also enhances the efficiency and durability of these components.
3. Medical Field
In the medical field, Inconel 625 additive manufacturing has gained prominence in the production of implants and surgical instruments. Its biocompatibility, excellent mechanical properties, and resistance to corrosion make it suitable for applications such as orthopedic implants, dental prosthetics, and surgical instruments. Additive manufacturing enables the customization of implants, ensuring a better fit and improved patient outcomes.
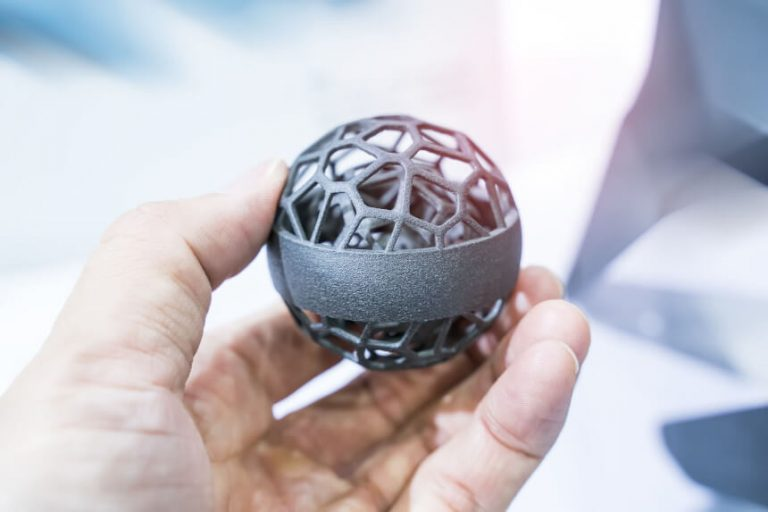
7. Challenges and Limitations
While Inconel 625 additive manufacturing offers numerous benefits, there are also challenges and limitations that need to be considered.
1. High Material and Equipment Costs
Inconel 625 is an expensive material, and additive manufacturing processes using this superalloy can be cost-prohibitive, particularly for large-scale production. The high material cost and the need for specialized equipment, such as high-powered lasers or electron beam machines, can pose financial challenges for manufacturers.
2. Process Complexity
Additive manufacturing processes, including those using Inconel 625, can be complex and require skilled operators. Optimizing parameters such as laser power, scanning speed, and powder feed rate is crucial to achieve the desired quality and properties in the printed components. Process optimization and control are ongoing areas of research to further enhance the reliability and efficiency of Inconel 625 additive manufacturing.
3. Quality Control and Certification
Maintaining quality control and ensuring the certification of Inconel 625 additive manufactured components can be challenging. The layer-by-layer nature of the process introduces the potential for defects, such as porosity or inhomogeneity, which can affect the mechanical properties of the final product. Strict quality control measures, non-destructive testing, and certification processes are essential to ensure the reliability and performance of Inconel 625 additive manufactured components.
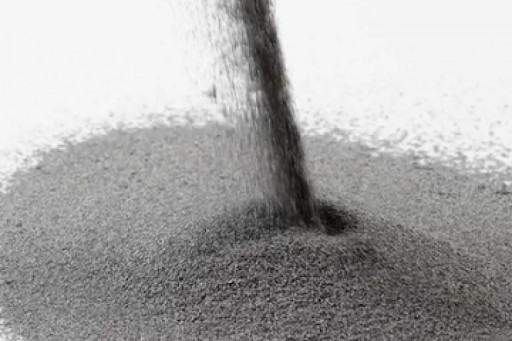
8. Future Outlook
The future of Inconel 625 additive manufacturing looks promising. Ongoing research and development efforts are focused on further optimizing the process parameters, improving material properties, and reducing production costs. Advances in post-processing techniques and quality control methods will enhance the reliability and quality of Inconel 625 additive manufactured components.
As the technology matures and becomes more accessible, we can expect to see increased adoption of Inconel 625 additive manufacturing across various industries. The ability to produce customized, high-performance components with reduced lead times and material waste will continue to drive its application in sectors such as aerospace, oil and gas, and medical fields.
9. Conclusion
Inconel 625 additive manufacturing combines the exceptional material properties of Inconel 625 with the design freedom and efficiency of additive manufacturing. This powerful combination opens up new possibilities for creating complex, high-performance components in industries such as aerospace, oil and gas, and medical fields. While there are challenges to overcome, ongoing research and development efforts are paving the way for further advancements in process optimization, cost reduction, and quality control.
The benefits of Inconel 625 additive manufacturing are clear. It offers design freedom, allowing for the creation of intricate and customized components that were previously difficult or impossible to manufacture. The cost and time efficiency of additive manufacturing reduce production costs, lead times, and inventory requirements. Moreover, the superior material properties of Inconel 625, including its strength, corrosion resistance, and fatigue resistance, are further enhanced through additive manufacturing, making it suitable for demanding applications in harsh environments.
The aerospace industry is leveraging Inconel 625 additive manufacturing to produce turbine blades, engine parts, and structural elements that can withstand extreme conditions. In the oil and gas sector, components such as valves, couplings, and downhole tools benefit from the corrosion and erosion resistance of Inconel 625. In the medical field, the biocompatibility and mechanical properties of Inconel 625 make it an excellent choice for orthopedic implants, dental prosthetics, and surgical instruments.
However, challenges exist in the adoption of Inconel 625 additive manufacturing. The high material and equipment costs, as well as the complexity of the process, can pose financial and operational hurdles for manufacturers. Ensuring quality control and certification of Inconel 625 additive manufactured components is also crucial to guarantee their reliability and performance.
Looking ahead, the future of Inconel 625 additive manufacturing is promising. Ongoing research aims to optimize process parameters, improve material properties, and reduce production costs. Advancements in post-processing techniques and quality control methods will further enhance the reliability and quality of Inconel 625 additive manufactured components.
In conclusion, Inconel 625 additive manufacturing represents a significant advancement in the manufacturing industry. Its combination of exceptional material properties and the design flexibility offered by additive manufacturing opens up new opportunities for creating complex, high-performance components. While challenges exist, ongoing research and development efforts are addressing them, and the future outlook for Inconel 625 additive manufacturing is bright.
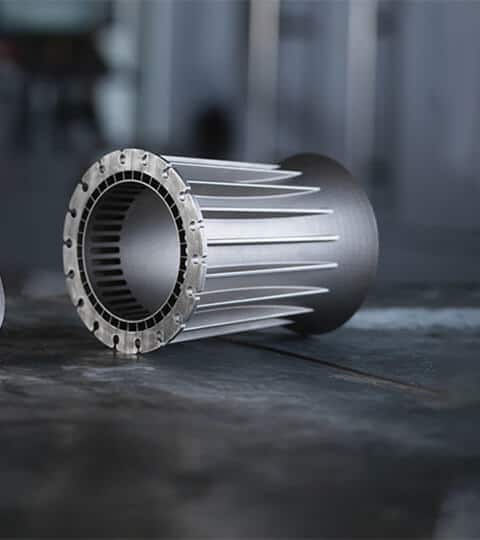
10. FAQs
1. Can Inconel 625 be used in traditional manufacturing processes? Yes, Inconel 625 can be used in traditional manufacturing processes such as casting and machining. However, additive manufacturing offers unique advantages in terms of design freedom and the ability to create complex geometries.
2. Is Inconel 625 suitable for high-temperature applications? Yes, Inconel 625 is renowned for its excellent high-temperature strength and oxidation resistance, making it suitable for applications that involve extreme temperatures.
3. Are there alternative materials to Inconel 625 for additive manufacturing? Yes, there are other nickel-based superalloys and high-performance materials that can be used in additive manufacturing. However, Inconel 625 is widely recognized for its excellent properties and has established itself as a preferred choice in many industries.
4. Can Inconel 625 additive manufacturing reduce material waste? Yes, additive manufacturing processes, including Inconel 625, can significantly reduce material waste compared to traditional manufacturing methods. The layer-by-layer deposition allows for precise material placement, minimizing waste.
5. What are the future prospects of Inconel 625 additive manufacturing? The future of Inconel 625 additive manufacturing looks promising, with ongoing research focused on optimizing processes, improving material properties, and reducing costs. Continued advancements will drive wider adoption across industries and enable the production of even more complex and high-performance components.