Introduction
SLM additive manufacturing, also known as Selective Laser Melting, is a revolutionary technique that has transformed the manufacturing industry. This advanced manufacturing process enables the creation of complex, high-quality metal parts with exceptional precision. In this article, we will explore the ins and outs of SLM additive manufacturing, including its working principle, advantages, applications, challenges, and future prospects.
What is SLM Additive Manufacturing?
SLM additive manufacturing is a 3D printing technique that utilizes a high-powered laser to selectively melt and fuse metallic powders together, layer by layer, to create a solid object. It falls under the category of powder bed fusion processes, where a thin layer of powdered material is evenly distributed onto a build platform. The laser scans and selectively melts the powder according to the digital design, solidifying it to form the desired shape. This additive manufacturing method is commonly used with metals such as titanium, aluminum, stainless steel, and cobalt-chromium alloys.
How Does SLM Additive Manufacturing Work?
The process of SLM additive manufacturing involves several key steps. First, a 3D CAD model is created using specialized software, which is then sliced into multiple cross-sectional layers. These layers serve as a blueprint for the additive manufacturing machine to follow. The metal powder, typically in the form of fine particles, is uniformly spread across the build platform.
Next, the SLM machine employs a high-powered laser that is precisely controlled by a scanning system. The laser beam selectively heats and melts the metal powder particles, causing them to fuse together. The melted material solidifies almost instantly, creating a solid layer. The build platform is then lowered, and a new layer of metal powder is spread on top of the previous one. This process is repeated layer by layer until the entire object is formed.
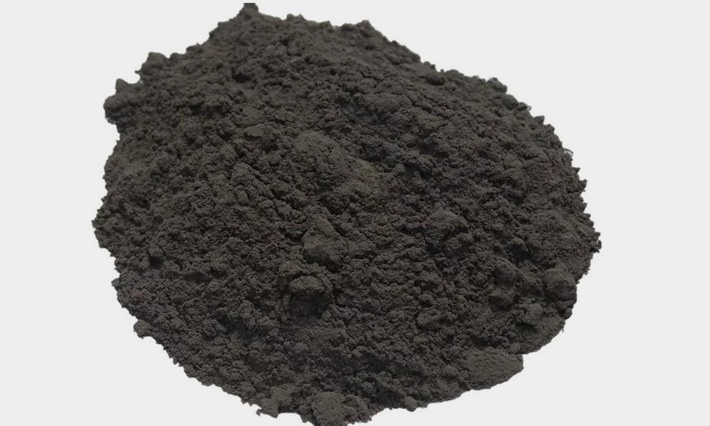
Advantages of SLM Additive Manufacturing
Design Freedom
SLM additive manufacturing offers unparalleled design freedom, allowing engineers and designers to create complex geometries that were previously unachievable through traditional manufacturing methods. The layer-by-layer approach enables the production of intricate internal structures, cavities, and undercuts, opening up new possibilities for innovative product designs.
Material Efficiency
One of the significant advantages of SLM additive manufacturing is its exceptional material efficiency. Unlike subtractive manufacturing processes where excess material is wasted, SLM only utilizes the necessary amount of metal powder required for building the object. This reduces material waste and makes the process more cost-effective and environmentally friendly.
Complex Geometry
SLM additive manufacturing excels at producing parts with complex geometries. The layer-by-layer construction method allows for the creation of intricate shapes, including internal lattices and hollow structures. This capability is particularly advantageous in industries such as aerospace and medical, where lightweight and optimized designs are crucial.
Faster Prototyping
With SLM additive manufacturing, the production of prototypes becomes faster and more streamlined. Traditional prototyping methods often involve multiple iterations and extensive tooling, resulting in time and cost inefficiencies. SLM enables rapid iteration and on-demand manufacturing of prototypes, accelerating the product development cycle.
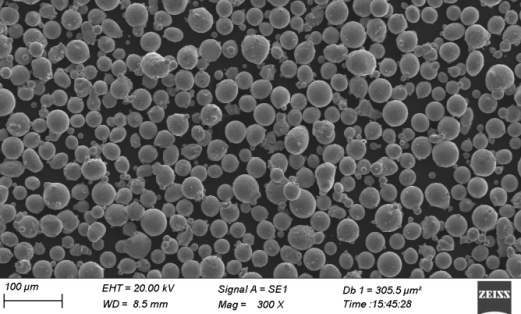
Applications of SLM Additive Manufacturing
Aerospace Industry
The aerospace industry has widely embraced SLM additive manufacturing due to its ability to produce lightweight, high-strength components. From complex turbine blades to structural brackets, SLM enables the creation of parts with intricate geometries and reduced weight. This leads to improved fuel efficiency, enhanced performance, and reduced costs in the aerospace sector.
Medical Field
In the medical field, SLM additive manufacturing has revolutionized the production of customized implants and medical devices. By utilizing patient-specific data, medical professionals can create implants tailored to the individual’s unique anatomy. This technology has found applications in orthopedics, dental implants, prosthetics, and even patient-specific surgical instruments.
Automotive Sector
The automotive industry benefits from SLM additive manufacturing by leveraging its potential for lightweight design and optimization. Components such as engine parts, heat exchangers, and suspension elements can be manufactured with reduced weight, leading to improved fuel efficiency and overall vehicle performance. Additionally, the ability to produce on-demand spare parts reduces inventory costs and enhances supply chain management.
Jewelry Design
SLM additive manufacturing has gained traction in the jewelry industry for its ability to create intricate and customizable designs. Jewelers can produce unique, high-quality pieces with complex geometries, textures, and patterns that were previously challenging to achieve. This technology enables greater creativity and personalization in jewelry design.
Challenges in SLM Additive Manufacturing
Limited Material Selection
While SLM additive manufacturing offers a wide range of compatible materials, the selection is still more limited compared to traditional manufacturing processes. The availability of specific alloys or material combinations may be constrained, limiting the full potential of SLM in certain applications. However, ongoing research and development aim to expand the material options for SLM.
Post-Processing Requirements
After the SLM additive manufacturing process, post-processing steps are often necessary to achieve the desired surface finish and mechanical properties. This may involve removing support structures, heat treatment, machining, or surface treatments. Post-processing adds time, cost, and complexity to the overall manufacturing process.
Build Time and Cost
SLM additive manufacturing can be a relatively slow process compared to traditional manufacturing methods, particularly for large and complex parts. The build time is influenced by factors such as the layer thickness, part size, and complexity. Additionally, the cost of SLM equipment and the raw materials used can be higher compared to conventional manufacturing technologies.
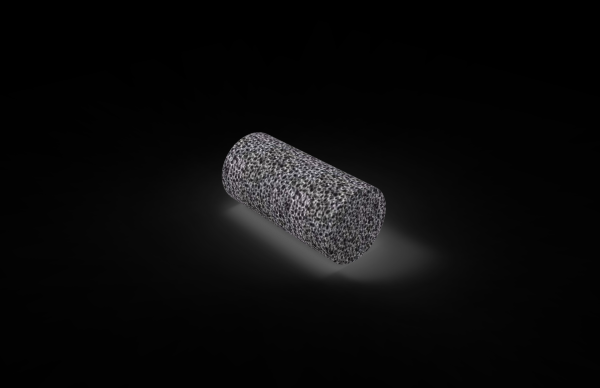
Future Prospects of SLM Additive Manufacturing
Improved Material Selection
Researchers are actively working to expand the range of materials compatible with SLM additive manufacturing. This includes exploring new alloys, composites, and even multi-material printing capabilities. Increasing the material selection will unlock new applications and enable the production of more diverse and functional parts.
Enhanced Process Control
Process control and optimization are key areas of development in SLM additive manufacturing. Improvements in laser technology, scanning systems, and process monitoring techniques aim to enhance the overall process reliability, repeatability, and quality control. Achieving better process control will contribute to wider industrial adoption of SLM.
Industrial Adoption
As SLM additive manufacturing continues to evolve and overcome its current limitations, its adoption in various industries is expected to increase significantly. Industries such as aerospace, automotive, medical, and jewelry are already benefiting from the advantages offered by SLM. As the technology matures and becomes more cost-effective, it is likely to find broader applications across different sectors.
The ability to produce lightweight, complex, and customized parts makes SLM particularly attractive for industries that value design optimization, performance improvement, and cost reduction. As more research is conducted and material options expand, SLM additive manufacturing will offer even greater versatility and feasibility for a wider range of applications.
Moreover, advancements in process control and monitoring will enhance the reliability and consistency of SLM additive manufacturing. This will build trust and confidence in the technology, leading to increased adoption by industrial manufacturers. As companies witness the benefits of SLM firsthand, they will be more inclined to integrate it into their production processes, ultimately driving its industrial adoption.
In conclusion, SLM additive manufacturing, or Selective Laser Melting, is a transformative technology that enables the creation of complex metal parts with exceptional precision. Its advantages, including design freedom, material efficiency, and the ability to produce intricate geometries, make it highly valuable in industries such as aerospace, medical, automotive, and jewelry. While challenges exist, ongoing research and development are addressing them, leading to improved material selection, enhanced process control, and increased industrial adoption. As SLM additive manufacturing continues to evolve, its impact on manufacturing processes and product innovation is expected to grow significantly.
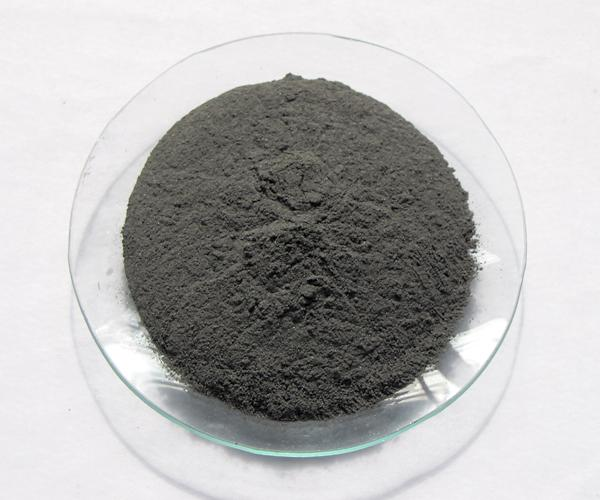
FAQs
1. Is SLM additive manufacturing only applicable to metals?
SLM additive manufacturing is primarily used with metals such as titanium, aluminum, stainless steel, and cobalt-chromium alloys. However, research is underway to explore the use of other materials, including ceramics and polymers, expanding the possibilities of SLM in different industries.
2. What are the main advantages of SLM additive manufacturing over traditional manufacturing methods?
SLM additive manufacturing offers several advantages over traditional manufacturing methods. These include design freedom, material efficiency, the ability to produce complex geometries, faster prototyping, and customization.
3. Are there any limitations to SLM additive manufacturing?
While SLM additive manufacturing has numerous benefits, there are some limitations to consider. These include limited material selection compared to traditional methods, post-processing requirements for surface finish and mechanical properties, and longer build times and higher costs for large and complex parts.
4. How is SLM additive manufacturing used in the aerospace industry?
SLM additive manufacturing is extensively used in the aerospace industry to produce lightweight, high-strength components. It enables the creation of complex geometries and optimized designs, resulting in improved fuel efficiency, enhanced performance, and cost reduction.
5. Can SLM additive manufacturing be used for mass production?
While SLM additive manufacturing is currently more suitable for low to medium volume production, ongoing advancements in process optimization and cost reduction may enable its application in mass production scenarios in the future.