Introduction
Electron Beam Melting (EBM) is an advanced additive manufacturing technology that utilizes an electron beam to melt and fuse metallic powders, creating complex and highly precise three-dimensional (3D) objects. This article explores the intricacies of electron beam melting, its working principles, advantages, applications, challenges, and future trends.
What is Electron Beam Melting (EBM)?
EBM is a powder-bed fusion additive manufacturing process that involves the selective melting of metal powders using an electron beam. It was developed by the Swedish company Arcam AB (now part of GE Additive) and has gained prominence in various industries due to its ability to produce intricate geometries and functional parts with excellent material properties.
How Does Electron Beam Melting Work?
In the electron beam melting process, a thin layer of metal powder is spread across a build plate, which is then placed in a vacuum chamber. An electron beam, generated by an electron gun, selectively scans the surface of the powder layer according to the desired shape of the object. The high-energy electrons heat and melt the powder particles, causing them to fuse together.
The process is repeated layer by layer, with each new layer of powder being spread on top of the previously melted layer. The un-melted powder acts as a support structure for the part being built, eliminating the need for additional support structures.
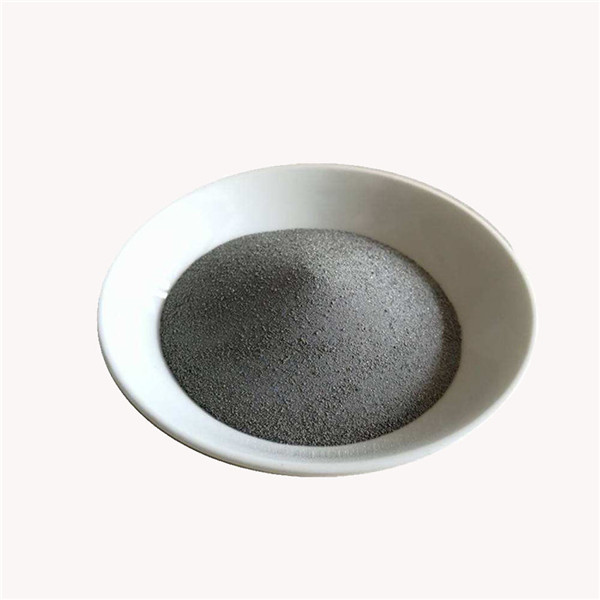
Advantages of Electron Beam Melting
High Precision and Complex Designs
EBM allows for the creation of highly intricate and complex designs that would be difficult or even impossible to produce using traditional manufacturing methods. The precise control of the electron beam enables the fabrication of parts with intricate internal channels, lattices, and lightweight structures.
Material Efficiency
EBM boasts high material efficiency as it only utilizes the necessary amount of metal powder required for the build. This reduces waste and lowers material costs compared to conventional subtractive manufacturing processes.
Reduced Lead Times
With EBM, the production of complex parts can be achieved in a shorter time frame compared to traditional methods. The layer-by-layer additive process eliminates the need for complex tooling, reducing the lead time for manufacturing customized or low-volume parts.
Enhanced Material Properties
The localized melting and solidification of metal powders in EBM can result in parts with excellent material properties. The rapid solidification process can lead to a fine microstructure, reducing grain growth and improving mechanical properties.
Sustainability Benefits
EBM offers sustainability advantages as it generates less waste compared to traditional manufacturing processes. The ability to produce lightweight structures can also contribute to energy savings and reduced emissions in industries such as aerospace and automotive.
Applications of Electron Beam Melting
Aerospace and Defense
The aerospace and defense industries benefit greatly from EBM technology. It enables the production of lightweight, high-strength components with intricate geometries, such as turbine blades, fuel nozzles, and structural parts for aircraft and spacecraft.
Medical and Dental
EBM finds applications in the medical and dental fields for the fabrication of patient-specific implants, prosthetics, and orthopedic devices. The ability to create complex and porous structures in biocompatible materials facilitates better osseointegration and patient outcomes.
Automotive
In the automotive industry, EBM is used for prototyping and the production of lightweight, high-performance components. It allows for the optimization of part designs, improved fuel efficiency, and reduced vehicle weight.
Tooling and Prototyping
EBM is also valuable in tooling and prototyping applications. It enables the rapid production of complex tooling inserts and molds, reducing lead times and costs associated with traditional manufacturing methods.
Research and Development
EBM plays a crucial role in research and development activities, allowing engineers and scientists to explore new material compositions, optimize designs, and study the effects of process parameters on the final product.
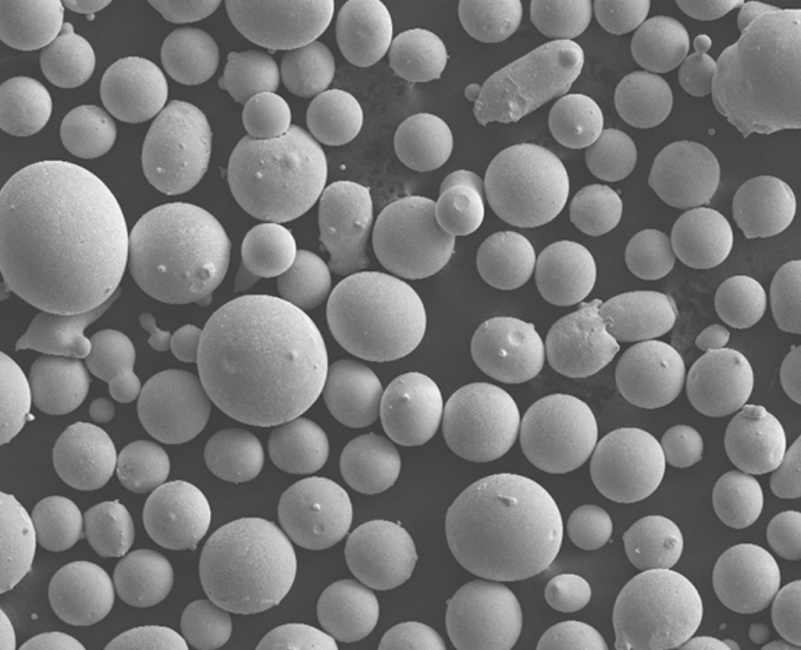
Challenges and Limitations of Electron Beam Melting
Cost of Equipment and Operation
The initial investment cost for EBM equipment is relatively high, making it less accessible for small businesses or individual users. Additionally, the cost of operation, including the consumption of electricity and the need for specialized facilities, should be considered.
Limited Material Options
Although the range of materials compatible with EBM is expanding, the available options are still limited compared to traditional manufacturing processes. This can pose challenges when specific material properties are required for a particular application.
Post-Processing Requirements
After the EBM process, post-processing steps may be necessary to achieve the desired surface finish, dimensional accuracy, or mechanical properties. These additional steps can increase production time and costs.
Size and Scalability Constraints
EBM machines have certain limitations in terms of the size of the build chamber and the maximum dimensions of the parts that can be produced. Large-scale production of bulky objects may not be feasible using current EBM technology.
Future Trends in Electron Beam Melting
The field of electron beam melting continues to evolve, and several trends are emerging:
- Expansion of Material Options: Research and development efforts are focused on expanding the range of materials compatible with EBM, including high-temperature alloys, composites, and biomaterials.
- Improved Process Control: Advancements in process monitoring and control systems will enhance the precision and reliability of EBM, leading to higher quality and more consistent parts.
- Increased Automation: Automation in EBM systems will streamline the manufacturing process, reducing manual intervention and improving productivity.
- Integration with Other Technologies: The integration of EBM with other additive manufacturing technologies, such as wire arc additive manufacturing, may unlock new possibilities and synergistic benefits.
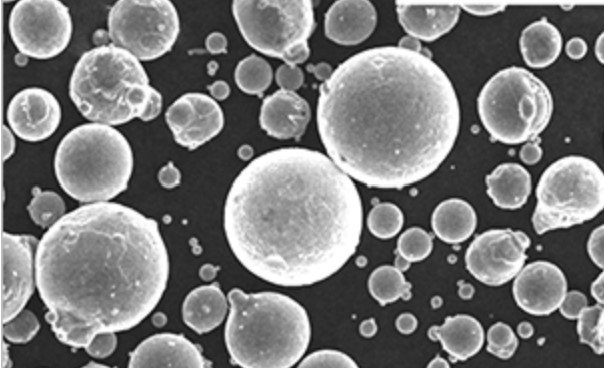
Conclusion
Electron Beam Melting (EBM) is a powerful additive manufacturing technology that enables the production of complex and high-performance parts with excellent material properties. Its advantages include high precision, material efficiency, reduced lead times, and sustainability benefits. EBM finds applications in various industries, including aerospace, medical, automotive, and research and development. However, challenges such as cost, limited materials, post-processing requirements, and size constraints should be considered. The future of EBM holds promise with the expansion of materials, improved process control, increased automation, and integration with other additive manufacturing technologies.
FAQs
Is electron beam melting the same as 3D printing?
Electron beam melting is a specific type of 3D printing or additive manufacturing process. It utilizes an electron beam to selectively melt metal powders and build up layers to create a final object.
What types of materials can be used in electron beam melting?
Electron beam melting is primarily used with metal powders, including titanium, stainless steel, nickel alloys, and aluminum. However, the range of compatible materials is continuously expanding.
Are parts produced through electron beam melting structurally sound?
Yes, parts produced through electron beam melting can have excellent structural integrity and material properties. The localized melting and solidification process can result in parts with fine microstructures and desirable mechanical characteristics.
How does electron beam melting compare to other additive manufacturing processes?
Electron beam melting offers unique advantages, such as high precision, material efficiency, and the ability to create complex designs. However, it has limitations in terms of material options, equipment cost, and size scalability compared to other additive manufacturing processes like selective laser melting or fused deposition modeling.
Can electron beam melting be used for mass production?
While electron beam melting is suitable for low-volume production and customized parts, it may not be the most efficient process for mass production due to the limitations of build chamber size and production speed. However, ongoing advancements in the technology may address these limitations in the future.