Metal atomization is a process where metal is converted from a bulk solid form into fine powder. The fine metallic powder produced through atomization has unique properties and plays an important role across various industries and applications.
Why atomize metal?
Atomization allows for the production of metal powders with precise particle sizes and characteristics. Some key benefits of atomized metal powders include:
- Increased reactivity – Due to the high surface area to volume ratio, atomized powders are more chemically reactive allowing improved performance in applications like catalysts.
- Enhanced mechanical properties – Atomized powder can be used to manufacture parts with superior mechanical properties compared to those made from cast or wrought metal.
- Better blending – Fine homogeneous mixing of different metals and alloying elements is possible with atomized powders. This allows for unique alloys and microstructures.
- Improved flowability – Spherical atomized powders have excellent flow characteristics which helps in automated handling, transport and precision metering.
- Higher density – Parts manufactured from atomized powders can achieve close to full density. This allows lighter parts to be made for weight sensitive applications.
- Net-shape manufacturing – Atomization followed by powder consolidation enables net-shape manufacturing. This reduces machining costs and material waste.
- Pure compositions – High purity metal powders can be produced through vacuum atomization where reactive elements like aluminum are protected from oxidation.
So in summary, atomization converts metals into extremely fine powders with customized compositions, sizes and morphologies. This opens up a whole range of manufacturing techniques and applications across automotive, aerospace, biomedical, chemical, defense and other key industries.
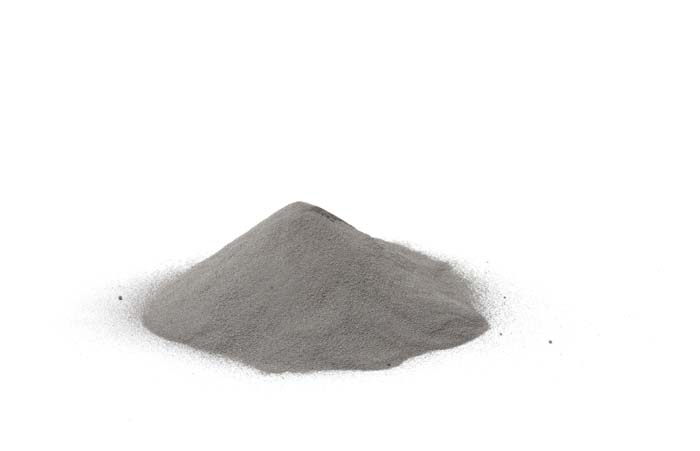
Methods of metal atomization
There are two widely used techniques for atomizing metal into fine powders:
Gas atomization
This method uses compressed air or an inert gas like nitrogen or argon to convert the metal into powder. The process involves:
- Heating the metal to around 30-50% above melting point. Common examples are nickel, cobalt, aluminium, steels, titanium, superalloys etc.
- Forcing the molten metal stream through a nozzle at high pressures of 5-20 bars.
- Breaking up the metal stream into fine droplets using high velocity jets of compressed gas.
- Solidifying the droplets into powder by extracting heat rapidly as they fall through the atomization chamber.
- Collection of the atomized powder in vessels at the bottom. Particle size distribution is controlled by the gas flow rate.
Gas atomized powders have a spherical shape and are popular for metal injection molding (MIM), thermal spray coatings and powder metallurgy parts.
Water atomization
In this method, high pressure water jets are used to atomize molten metal alloys into fine powders. The steps involve:
- Induction heating of the metal charge to above melting point. Iron, nickel, cobalt and copper alloys are commonly atomized.
- Pouring the liquid metal into the atomization chamber where multiple water jets strike the metal stream at pressures over 150 bars.
- The water jets break up the molten metal into fine droplets which solidify into powder.
- Collection of the powder once the water is drained. Irregular, more angular powders are formed.
Water atomized powders with higher oxygen pick-up are used in sintered parts, friction materials and welding electrodes.
Centrifugal atomization and ultrasound gas atomization are some other methods used for specialized applications.
Key process parameters
Some important parameters that influence the properties and quality of atomized powders are:
- Metal composition – Alloying elements, impurities and volatility of components affect particle formation.
- Superheat temperature – Higher metal superheat promotes finer atomization. But too high temperatures can cause alloying element vaporization.
- Nozzle design – Nozzle diameter, number of nozzles and nozzle geometry impacts molten metal flow rate, droplet size and cooling rate.
- Atomizing fluid – Gas or water flow rate determines the degree of atomization and powder particle size.
- Droplet flight distance – Longer droplet flight time in the atomization chamber improves solidification and sphericity.
- Cooling rate – Rapid solidification rates (~104-106 K/s) produces finer metastable microstructures in the powder.
By optimizing these parameters, atomization process can be tailored to obtain powders with desired grain size, particle size distribution, shape and microstructure.
Key applications
Some major applications that utilize atomized metal powders are:
Metal injection molding (MIM)
MIM is a powder metallurgy process to manufacture small, complex parts in high volumes. Feedstock made using ultrafine (<10 μm) gas or water atomized powders is injection molded and then sintered. High mechanical strength components are produced with excellent dimensional accuracy for automotive and consumer product applications.
Additive manufacturing
Also known as 3D printing, specially designed atomized powders are used in selective laser sintering, direct metal laser sintering and other additive technologies to directly fabricate finished parts from CAD models. Near net-shape parts with customized alloys and microstructures can be produced using these methods.
Thermal spray coatings
In this technique, atomized powders are heated to melt or near-melt conditions and sprayed onto a surface at high velocities to form a protective coating. Hardfacing alloys and wear-resistant coatings are applied on turbine blades, engine components, biomedical implants etc. using thermal spraying.
Metal matrix composites
Atomized powders can be blended with reinforcing ceramics like silicon carbide to synthesize advanced metal matrix composites. This results in materials with very high strength-to-weight ratios suitable for aerospace applications.
Welding consumables
Special purpose welding electrodes and filler wires are manufactured using irregular, water atomized powders. The rapid solidification microstructures provide excellent weldability.
P/M structural parts
Water atomized iron and steel powders are compacted and sintered to produce self-lubricating bearings and other structural parts with good dimensional tolerance and mechanical properties.
Other applications
Fine metal hydrides, magnets, catalysts, drug delivery agents and pyrotechnic compositions are synthesized using highly reactive atomized powders. They are also used in MIM feedstocks, brazing pastes, electrical contacts etc.
So in summary, atomized powders cater to a diverse cross-section of advanced manufacturing techniques and high-performance applications across key industries.
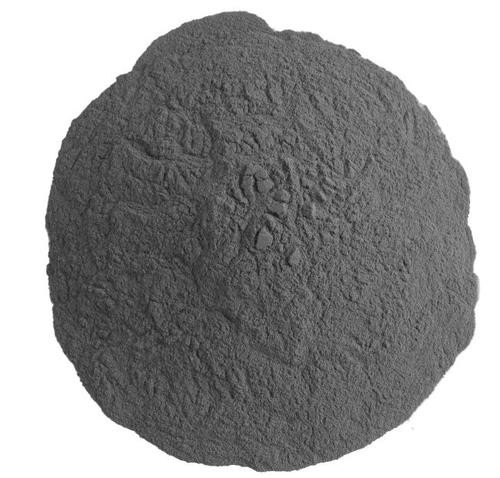
Economic and environmental benefits
Some of the key economic and environmental benefits realized from metal atomization are:
- Reduced machining – Near net shape fabrication using MIM and AM decreases raw material costs and machining.
- Scrap reuse – Atomization accommodates scrap metal and small lot sizes unsuitable for casting.
- Energy efficiency – Parts made from atomized powder require lower melting energy. Minimum material waste also improves sustainability.
- Just-in-time production – Atomized powders can be quickly produced on-demand enabling flexible inventories and production.
- Superior performance – Enhanced mechanical properties of atomized powder components reduce wear, failures and part replacements.
- Less processing steps – Combined melting, alloying and atomizing in one process chain decreases energy usage and carbon emissions.
- Lower inventories – On-site atomization allows lean Just-In-Time powder inventories avoiding storages and logistics costs.
So optimizing metal atomization parameters provides significant cost benefits while also minimizing material waste, energy consumption and carbon footprint.
Future outlook
Several trends point towards increased adoption of atomization technology:
- New alloys with improved properties and performance will drive the need for atomized powders. Research is ongoing on titanium alloys, aluminum composites, high entropy alloys, amorphous alloys etc.
- Metal additive manufacturing will continue strong double-digit growth as new 3D printed components get flight certified and approved for biomedical use.
- Applications like thermal spray coatings and metal matrix composites will benefit from reactive and multi-component atomized specialty powders.
- Hybrid manufacturing combining additive, thermal spray, welding and machining will create demand for tailored atomized powders.
- Increased focus on sustainability will expand use of recycled scrap and on-demand micro-scale atomization systems.
- Advanced modeling of atomization physics and powder characteristics will improve process efficiencies and powder quality.
- Nanocrystalline and ultrafine microstructures obtainable via rapid solidification will enable next generation of high performance atomized powders.
In summary, metal atomization is a versatile technology that will continue to grow in importance driven by new materials, manufacturing techniques and sustainability trends. Research and development focus on atomized powder quality, modeling and simulation will help expand the technology into new applications and industries.
FAQ
What is the typical particle size of atomized powder?
Atomized powders can range from micron sizes of 1-100 μm for metal injection molding up to large sizes of 500-1000 μm for thermal spray coatings. Gas atomization normally produces finer powders below 100 μm while water atomization gives more coarse powder fractions.
How spherical are gas atomized powders?
Gas atomized powders have high sphericity of around 0.9 on a scale of 0 to 1. This spherical shape provides good packing and flow properties. Water atomized powders on the other hand have more irregular shapes.
What is the role of inert gas purity in atomization?
High purity inert gases like argon are used in gas atomization to prevent powder contamination and oxidation. Traces of oxygen can lead to powder degradation during additive manufacturing.
How is powder production rate determined in atomization?
Production rate is dependent on factors like nozzle size, metal flow rate, gas pressure and number of nozzles. Multiple nozzle gas atomizers can produce up to 1000 kg/hour of fine stainless steel powders for MIM industry.
What is the benefit of vacuum atomization?
Vacuum atomization involves creating a low pressure inert atmosphere in the chamber. This prevents oxidation of reactive alloys like titanium and aluminum allowing production of pure, high reactivity powders.
What is the typical cost of atomized powders?
Atomized powder cost varies widely from $5-10 per kg for common steels to $100-500 per kg for highly alloyed grades for aerospace applications. Exotic metal powders can cost thousands of dollars per kg.
What is the effect of cooling rate on powder microstructure?
Faster cooling rates above 104 K/s, achievable in atomization, produces finer grain size, extended solid solubility and metastable phases in powders through rapid solidification. This provides superior mechanical properties.
What causes powder degradation during additive manufacturing?
Factors like partial sintering, oxidation and vaporization can degrade atomized powder over repeated thermal cycling in AM. This necessitates recycling and replenishing with fresh powder to maintain part quality.
How is powder removed from inert gas after atomization?
Cyclone separators recover over 99% of the powder from the gas stream. Bag house filters can also be used. The clean gas is then recirculated back into the process in a closed loop system.
What are the different methods used to sieve atomized powders?
Vibratory sieving and sonic sifting classify powders into narrow size fractions. Air and microflows classifiers are also used. Sieving improves packing density and flow properties of the powders.
know more 3D printing processes
Frequently Asked Questions (Supplemental)
1) What determines whether gas atomization or water atomization is better for my application?
- Choose gas atomization (argon/nitrogen; VIGA/EIGA) for high sphericity, low oxygen, and AM/MIM feedstocks. Choose water atomization for cost-effective iron/steel powders for PM structural parts, friction materials, and welding consumables where irregular morphology is acceptable.
2) How does “metal atomization” impact additive manufacturing part quality?
- Atomization controls particle size distribution, sphericity, and surface chemistry (O/N/H). These drive layer packing, laser/e-beam absorptivity, and defect rates (lack-of-fusion, gas porosity). Tight PSD and low satellites reduce variability and improve density and fatigue.
3) What are best practices to limit oxygen pickup during atomization?
- Use high-purity inert gas, vacuum-induction melting, EIGA (no crucible) for reactive alloys, short melt residence, low-leak chambers, and closed-loop gas recirculation with in-line O2/H2O analyzers. Rapid collection and cool-down further minimize oxidation.
4) Can atomization support recycled feedstock without sacrificing quality?
- Yes, with certified scrap, chemistry control, filtration/degassing, and powder passports documenting PSD and O/N/H. Many producers achieve equivalent AM performance using recycled Ti/SS/Ni inputs within narrow specifications.
5) What specifications should buyers request for AM-grade atomized powders?
- Certificate of Analysis with PSD (laser diffraction), morphology (SEM), O/N/H (LECO), apparent/tap density (ASTM B212/B329), flow (Hall/Carney), moisture, satellite/void counts, and reuse guidance aligned to ISO/ASTM 52907.
2025 Industry Trends and Data
- Adoption of “powder passports” linking atomization batch data to part certification in aerospace/medical supply chains.
- Growth of copper and aluminum AM enabled by oxide‑controlled gas atomization and green/blue lasers.
- Sustainability push: higher recycled content, life-cycle reporting (EPDs), and gas recirculation to cut argon consumption.
- Equipment advances: multi-jet gas atomizers with adaptive nozzles; inline sensors for O2/H2O and particle diagnostics.
- Qualification convergence: broader use of ISO/ASTM 52907 methods and ASTM process specifications (e.g., F3302) for consistent feedstock acceptance.
KPI (metal atomization) | 2023 Baseline | 2025 Typical/Target | Relevance | Sources/Notes |
---|---|---|---|---|
AM LPBF PSD window (Ti/SS) | 20–53 μm | 15–45 μm; span <1.7 | Layer quality, density | ISO/ASTM 52907; OEM specs |
Oxygen limit (Ti‑6Al‑4V ELI powder) | ≤0.15 wt% | ≤0.13 wt% routine | Ductility/fatigue | ASTM F136/F3001 |
Satellite content (gas‑atomized, post‑conditioning) | 8–12% | <3–5% by count | Flow, defect reduction | Supplier QC studies |
Gas consumption per kg powder (argon GA) | 20–40 Nm³/kg | 12–25 Nm³/kg with recirculation | Cost, footprint | Producer case data |
Recycled content in AM powders | <10% | 15–40% certified streams | Sustainability | EPD/LCA disclosures |
Inline O2/H2O monitoring adoption | Limited | Common on new GA lines | Quality control | OEM/plant reports |
As‑built density (LPBF Ti/IN718) | 99.5% | 99.7–99.9% | Mechanical properties | Peer‑reviewed/OEM data |
Authoritative references:
- ISO/ASTM 52907 (powder characterization): https://www.iso.org
- ASTM F3302 (metal AM process control), F2924/F3001 (Ti alloys): https://www.astm.org
- NIST AM Bench datasets: https://www.nist.gov/ambench
- ASM Handbook, Powder Metallurgy & AM: https://www.asminternational.org
- FDA AM medical device guidance: https://www.fda.gov/regulatory-information/search-fda-guidance-documents
Latest Research Cases
Case Study 1: Argon-Recirculating Gas Atomization Cuts Oxygen and Cost (2025)
- Background: A Tier‑1 AM powder supplier sought to reduce argon usage and improve O2 control for Ti‑6Al‑4V ELI.
- Solution: Installed closed‑loop argon recirculation with catalytic dryers and inline O2/H2O sensors; optimized superheat and multi‑jet nozzle geometry.
- Results: Argon consumption reduced 32%; powder oxygen lowered from 0.14 wt% to 0.11–0.12 wt%; LPBF porosity median fell from 0.28% to 0.10% across three lots; cost/kg decreased by 8–12% while meeting ASTM F136.
Case Study 2: Water‑Atomized Steel Powder Upgraded for MIM via Post‑Spheroidization (2024)
- Background: An automotive MIM plant needed better flow and density from budget water‑atomized 4600 series steel powder.
- Solution: Applied plasma spheroidization and fine classification; implemented carbon/oxygen control and lubricant optimization in feedstock.
- Results: Hall flow improved 20%; tap density +0.2 g/cm³; sintered density +0.4%; defect rate in thin‑wall parts dropped 35% with no cycle‑time penalty.
Expert Opinions
- Prof. Paul C. T. Lee, Chair in Powder Metallurgy, University of Sheffield
- Viewpoint: “Inline atmosphere analytics and adaptive nozzle control are transforming metal atomization from a batch art into a controlled, data‑driven process suitable for safety‑critical AM.”
- Dr. Anne Meyer, VP Materials Engineering, AP&C (GE Additive)
- Viewpoint: “Powder passports that trace atomization parameters, PSD, and surface chemistry through to part properties are the fastest path to scaling qualification in aerospace and medical.”
- Dr. Sebastian Thrun, Head of Materials Qualification, Fraunhofer IFAM
- Viewpoint: “Hybrid routes—gas atomization followed by targeted spheroidization—deliver near‑PA morphology at GA economics for many steels and Ni alloys.”
Practical Tools/Resources
- Standards and methods: ISO/ASTM 52907; ASTM B214/B822 (PSD), B212/B329 (apparent/tap density), B213 (Hall flow)
- Safety and handling: NFPA 484 Combustible Metals (https://www.nfpa.org)
- Metrology: LECO O/N/H analyzers (https://www.leco.com); SEM/EDS labs; moisture analyzers
- Data/benchmarks: NIST AM Bench (https://www.nist.gov/ambench); Senvol Database (https://senvol.com/database)
- Technical hubs: ASM International resources (https://www.asminternational.org); GE Additive knowledge center (https://www.ge.com/additive); Fraunhofer IFAM publications (https://www.ifam.fraunhofer.de)
Last updated: 2025-08-22
Changelog: Added 5 supplemental FAQs; introduced 2025 atomization trends with KPI table and sources; provided two recent case studies; included expert viewpoints; compiled practical tools/resources for metal atomization.
Next review date & triggers: 2026-02-01 or earlier if ISO/ASTM 52907 is revised, major OEMs update powder acceptance specs, or new argon‑recirculation/inline monitoring data is published.