Titanium alloy powders refer to titanium-based metallic materials in powder form used for additive manufacturing processes like selective laser sintering (SLS) and electron beam melting (EBM). Powder metallurgy allows creation of complex titanium components with superior mechanical properties compared to wrought products.
Titanium alloys are valued for their high strength-to-weight ratio, fatigue resistance, and corrosion resistance. When processed into fine powders, they can be used to 3D print intricate and lightweight parts for aerospace, medical, dental, automotive, and other applications.
This guide provides a comprehensive look at various types of titanium alloy powders, their characteristics, applications, specifications, suppliers, costs, installation, operation and maintenance of powder-based AM equipment, and more.
Types of Titanium Alloy Powders
Titanium alloys are generally categorized into alpha, alpha-beta, and beta alloys. Common titanium powders include:
Type | Composition | Characteristics |
---|---|---|
Ti-6Al-4V | 6% aluminum, 4% vanadium | Alpha-beta alloy, most popular for aerospace components due to strength, weldability |
Ti-6Al-7Nb | 6% aluminum, 7% niobium | Alpha-beta alloy, higher strength than Ti-6Al-4V |
Ti-5Al-5Mo-5V-3Cr | 5% each of aluminum, molybdenum, vanadium and chromium | Near alpha alloy, excellent corrosion resistance and high-temperature strength |
Ti-5553 | 5% aluminum, 5% molybdenum, 4% niobium, 3% vanadium, 1% zirconium | Near alpha alloy, used for compressor parts due to fatigue strength |
Ti-10V-2Fe-3Al | 10% vanadium, 2% iron, 3% aluminum | Beta alloy, highest strength of all titanium alloys but lower ductility |
Characteristics of Titanium Alloy Powders
Key characteristics of titanium alloy powders:
Characteristic | Details |
---|---|
Particle shape | Mostly spherical, some irregular shapes, affects flowability and packing density |
Particle size distribution | Narrow distribution between 15-45 microns common, affects final part density and quality |
Flowability | Depends on shape, size distribution, surface structure – improve with spheroidization and flow agents |
Apparent density | Around 2.5-3.5 g/cc based on composition, processing method – higher is better |
Tap density | Around 60-80% of theoretical density based on packing – higher improves final part density |
Oxide content | Present as thin surface layer, higher levels can cause defects in final parts |
Recyclability | Depends on oxygen and nitrogen absorption – often up to 20 reuse cycles are possible |
Applications of Titanium Alloy Powders
Titanium alloy powders are used to additively manufacture critical components across industries:
Industry | Applications |
---|---|
Aerospace | Structural airframe components, jet engine parts, airframes, turbines |
Medical | Orthopedic and dental implants, prosthetics, surgical instruments |
Automotive | Engine parts, powertrain components, under-the-hood parts |
Industrial | Tooling, moldmaking, robotics, manufacturing equipment |
Oil and gas | Valves, pumps, wellhead components, pipes |
Chemical | Process equipment, reactors, heat exchangers |
Benefits include weight savings, customization, simplified assemblies, faster prototyping, and improved lifecycle costs versus traditional manufacturing.
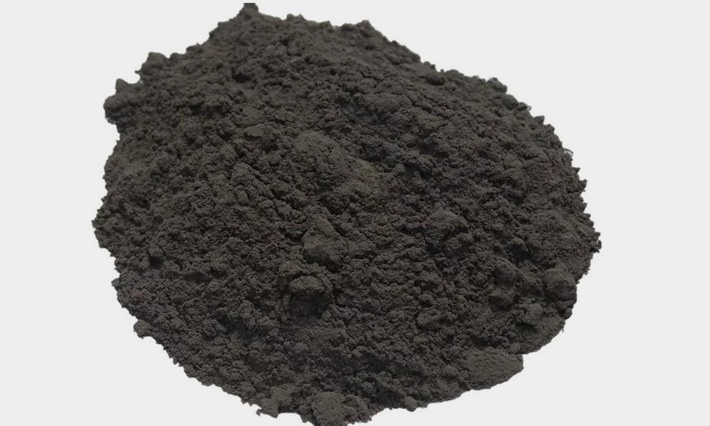
Specifications of Titanium Alloy Powders
Titanium alloy powders must meet exacting chemical, physical and microstructure specifications for use in AM processes:
Parameter | Typical Specification |
---|---|
Purity | >99% titanium, low O, C, N, H contamination |
Particle shape | Predominantly spherical |
Particle size | 15 to 45 microns |
Size distribution | D10 > 10 microns, D90 < 100 microns |
Apparent density | >2.5 g/cc |
Tap density | >3.5 g/cc |
Hausner ratio | <1.25 |
Flow rate | >25 s/50 g |
Surface oxide | <3000 ppm |
Bulk oxygen | <2000 ppm |
Nitrogen | <400 ppm |
Hydrogen | <150 ppm |
Microstructure | alpha, alpha-beta or beta phase |
Meeting powder quality standards is critical for defect-free builds, good mechanical properties and surface finish.
Suppliers of Titanium Alloy Powders
Leading global suppliers of titanium alloy powders include:
Supplier | Powder Grades | Quality Standards |
---|---|---|
AP&C | Ti-6Al-4V, Ti-6Al-7Nb, Ti-5Al-5Mo-5V-3Cr | ASTM B348, ASTM F2924, ASTM F3049 |
Carpenter Additive | Ti-6Al-4V ELI, Ti-6Al-4V, Ti 6-4, Ti CP2, Ti SP700 | ASTM F2924, ASTM F3001 |
LPW Technology | Ti-6Al-4V, Ti-6Al-4V ELI, Ti-6Al-7Nb, Ti 5553 | ASTM F2924, ISO 23301 |
Praxair | Ti-6Al-4V, Ti-6Al-4V ELI, Ti CP-2, Beta-C | ASTM F2924, ASTM F3001 |
TLS Technik | Ti-6Al-4V, Ti-6Al-4V ELI, Ti-5Al-5Mo-5V-3Cr | ASTM F2924, ASTM F3001 |
Specialized grades can also be sourced for specific applications.
Cost of Titanium Alloy Powders
Titanium alloy powder costs vary based on:
Factor | Details |
---|---|
Alloy composition | Ti-6Al-4V most common and economical |
Quality grade | Aerospace grades more expensive than industrial |
Order volume | Powder price reduces at higher quantities |
Particle size range | Fine powders below 30 microns more costly |
Supplier | Pricing differs between brands |
Processing method | Gas atomized powders costlier than plasma atomized |
Typical price ranges:
- Ti-6Al-4V: $150 to $450 per kg
- Ti-6Al-4V ELI: $250 to $600 per kg
- Ti-6Al-7Nb: $400 to $750 per kg
- Ti 5553: $500 to $800 per kg
Scrap titanium recycling can reduce costs by 40-60%.
Powder Handling, Storage and Preparation
Proper handling, storage and preparation of titanium alloy powders is essential:
Activity | Procedure |
---|---|
Handling | Use powder hoods, vacuum transfer systems to minimize exposure |
Storage | Store sealed containers in a moisture-free argon atmosphere |
Blending | Mix powders and recycling material in correct ratios |
Drying | Remove moisture at 200°C for 2-4 hours to prevent defects |
Sieving | Screen powders through fine mesh to break up agglomerates |
Flow conditioning | Add 0.1-0.5% flow agents like silica nanoparticles |
Contamination and oxygen intake must be minimized to ensure high reused yield and end part quality.
Selective Laser Sintering Process
SLS process overview:
- Powder is spread in thin layers and selectively fused by a high power laser
- Support structures are built simultaneously with the part
- Parts are embedded within the unfused powder bed until completion
- Excess powder is removed to reveal the 3D part
SLS of titanium alloys requires:
- Particle size between 15-45 microns with spherical morphology
- Low oxygen and nitrogen content
- Precise laser energy density optimization
- Inert gas environment to prevent contamination
- Stress relieving heat treatment of parts
SLS enables complex geometries but surface finish and tolerances are lower than EBM.
Electron Beam Melting Process
EBM process overview:
- Titanium powder layers are preheated before fusing
- Parts are built on a plate instead of platform for better heat dissipation
- Electron beam selectively melts the powder in a vacuum
- No support structures required and unused powder can be recycled
EBM of titanium alloys requires:
- Fine powder sizes between 45-105 microns
- High beam power ≥ 3kW and accelerating voltages 30-60 kV
- Vacuum levels below 5 x 10-5 mbar
- High temperature preheating up to 750°C
EBM allows higher build speeds, better material properties and surface finish compared to SLS.
Post-Processing of Titanium Parts
Titanium parts made by AM require post-processing:
Process | Purpose |
---|---|
Powder removal | Remove loose powder from internal cavities |
Thermal stress relief | Reduce residual stresses using heat treatment |
Hot isostatic pressing | Eliminate internal voids and increase density |
Machining | Improve dimensional accuracy and surface finish |
Surface treatments | Apply coatings or treatments to tailor properties |
Support structures are easily removed since they are made of the same titanium material.
Operation and Maintenance of Metal AM Equipment
Reliable operation and maintenance of metal AM systems requires:
- Training operators on machine capabilities, software, materials
- Establishing SOPs for parameter optimization, quality control, workflows
- Monitoring and documenting build processes using sensors, cameras
- Regular replacement of filters, sieves, wipers, rollers
- Checking laser optics, electron beam emitters and focusing
- Calibrating powder layer and energy delivery systems
- Tracking and replacing argon, helium, nitrogen supplies
- Cleaning build chambers and material handling systems
- Periodic upkeep as per OEM recommendations
Proactive maintenance improves uptime, maximizes equipment lifetime and ensures optimal quality of printed parts.
Choosing a Titanium Alloy Powder Supplier
Factors for choosing a titanium alloy powder supplier:
Consideration | Details |
---|---|
Powder grades | Range of alloys and compositions supported |
Quality certifications | Compliance with ASTM, ISO and other standards |
Customization | Ability to produce specialized powders for applications |
Batch analysis reports | Composition, characteristics and test results for each lot |
Testing capabilities | Scope of quality tests conducted on incoming materials |
Sampling services | Provision of free samples for evaluation |
Lead times | Inventory levels and production rates to meet delivery targets |
Minimum order quantities | Flexibility with small trial orders |
Technical expertise | Metallurgy and application knowledge to assist customers |
Customer service | Responsiveness to inquiries, issues and custom needs |
Pricing | Competitive and transparent pricing, discounts on higher volumes |
Choosing reputable suppliers with strict quality control ensures a reliable source of high-performance titanium alloy powders tailored to AM processes.
Pros and Cons of Titanium Alloy Powders
Advantages:
- High strength-to-weight ratio
- Corrosion and fatigue resistance
- Bio-compatibility for medical uses
- Customized alloys can be manufactured
- Complex, lightweight geometries produced by AM
- Faster and cheaper than subtractive machining
- Reduced lead times and inventories
Limitations:
- Powders are expensive compared to other materials
- Limited supplier and AM equipment availability
- Difficult to achieve high density and surface finish
- Secondary processing often required
- Susceptible to contamination during handling
- Post-processing can be costly and time consuming
- Lack of codes and standards for quality control
With ongoing developments in AM technology, titanium alloy powders offer exciting potential across manufacturing sectors weighed against processing challenges that are continually improving.
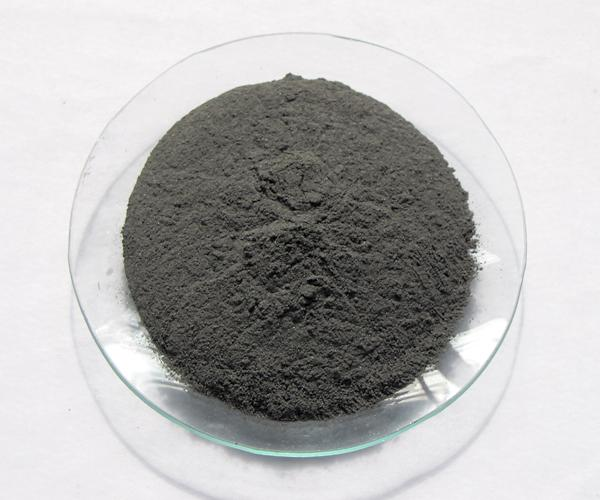
FAQ
Q: What are the main titanium alloys used in powder metallurgy?
A: Ti-6Al-4V is the most common titanium alloy powder due to its excellent strength, corrosion resistance and weldability. Other alloys include Ti-6Al-7Nb for higher strength and Ti 6-4 ELI for biomedical uses.
Q: How does titanium alloy powder quality affect properties of AM parts?
A: Powder characteristics like particle size distribution, shape, tap density, oxygen content directly affect density, surface finish, microstructure and mechanical performance of final parts.
Q: What precautions are required when handling titanium powders?
A: Exposure to air causes contamination so titanium powders must be handled in a moisture-free inert gas environment using gloves and respirators. Storage containers must be vacuum sealed.
Q: What is the typical pricing range for Ti-6Al-4V alloy powder?
A: For standard industrial grade Ti-6Al-4V powders suitable for AM, pricing is usually between $150 to $450 per kg depending on quantity and supplier. Aerospace grades are more expensive.
Q: What are the main advantages of SLS versus EBM for titanium alloys?
A: SLS can produce complex, lightweight geometries without supports. EBM allows higher build speed, better material properties and surface finish.
Q: Why is post-processing needed on AM titanium parts?
A: Steps like Hot Isostatic Pressing, heat treatment and machining help to relieve stresses, close internal voids, improve dimensional accuracy and enhance surface finish.
Q: How can powder recyclability and reuse yields be maximized?
A: By minimizing exposure to air during handling, drying powders before reuse, and blending with small ratios of fresh powder to prevent accumulation of impurities.
Q: What standards are used to specify the quality of titanium alloy powders?
A: Key standards are ASTM F2924, ASTM F3001 and ISO 23301 which provide compositional limits, acceptable test methods, and sampling procedures.