Overview of molybdenum titanium powders
Molybdenum titanium powders refer to powders composed of molybdenum and titanium metals. They exhibit a unique combination of properties from each element, making them suitable for applications requiring high strength, heat resistance, and electrical conductivity.
Key details about molybdenum titanium powders:
- Composition – Varies, commonly 20-80% molybdenum with balance titanium
- Particle sizes – Ranging from micrometer to nanometer scale
- Production methods – High energy ball milling, gas/water atomization, plasma rotating electrode process
- Common applications – Additive manufacturing, thermal spray coatings, braze alloys
- Key properties – High strength, excellent corrosion resistance, electrical conductivity, low thermal expansion
Molybdenum titanium powders provide enhanced properties compared to the individual metals alone. By tuning the composition, powder characteristics can be tailored for different high-performance applications.
Types
Type | Composition | Description |
---|---|---|
Molybdenum-rich | 80% Mo, 20% Ti | Highest hardness and strength, thermal conductivity. Lower oxidation resistance than titanium-rich alloys. |
Titanium-rich | 20% Mo, 80% Ti | Excellent corrosion resistance with useful strength and conductivity. More ductile than molybdenum-rich types. |
Intermediate | 40-60% Mo, balance Ti | Balanced combination of molybdenum and titanium properties. General purpose alloy. |
Nanocomposite | Mo and Ti nanoparticles | Excellent strength due to fine grain size. Used in high performance coatings and structures. Lower ductility. |
Table 1: Types of molybdenum titanium powders and their typical composition
Composition and Production
Molybdenum titanium powders contain between 20-80% molybdenum with the balance as titanium. Other alloying elements like nickel, chromium, aluminum may be added in small quantities to modify specific properties.
Production Method | Description | Particle Characteristics |
---|---|---|
High energy ball milling | Repeated cold welding and fracturing of powder particles using grinding media | Broad size distribution, irregular morphology, composite particles |
Gas atomization | Rapid cooling of molten alloy by high pressure gas | Spherical morphology, fine microstructure, tight size distribution |
Water atomization | Uses water jet instead of gas for atomization | Less spherical particles compared to gas atomization, wider size range |
Plasma rotating electrode process | Electrode spinning and rapid melting/solidification | Control over particle size distribution and morphology |
Table 2: Overview of production techniques for molybdenum titanium powders
Gas atomization and the plasma rotating electrode process allow the greatest control over powder characteristics like particle size distribution, shape and internal alloy structure.
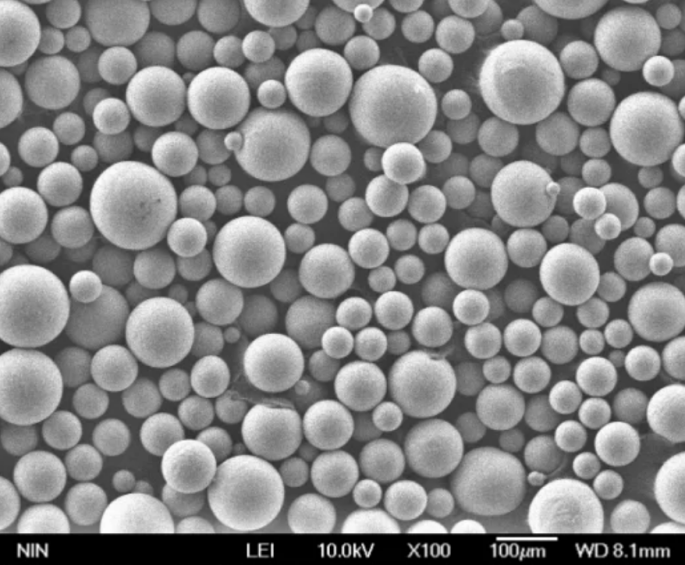
Properties of molybdenum titanium powders
Property | Contributing Element | Details |
---|---|---|
Strength | Molybdenum | Very high yield and tensile strength from solid solution/dispersion strengthening by molybdenum |
Hardness | Molybdenum | Up to Rockwell 60 HRC depending on composition |
Corrosion Resistance | Titanium | Excellent resistance to many acids, marine environments etc. due to protective surface oxides |
Oxidation Resistance | Titanium | Resists oxidation up to approx. 600°C. Molybdenum-rich alloys have lower resistance. |
Thermal Conductivity | Molybdenum | Useful for high heat flux applications like electrodes, thermal management components |
Electrical Conductivity | Molybdenum | Used in specialty conductive-reactive materials, thermal spray coatings |
Thermal Expansion | Titanium | Approximately 30% lower expansion than steels, improving thermal fatigue resistance |
Table 3: Overview of key properties of molybdenum titanium powders and the contributing element
The high strength comes mainly from molybdenum’s intrinsic properties and solid solution strengthening of titanium, while titanium imparts useful corrosion resistance. By tuning composition, resistance, conductivity and other properties can be balanced.
Applications
Molybdenum titanium powders are used in advanced applications where their special combination of properties is needed:
Application | Uses and Benefits |
---|---|
Additive Manufacturing | High hardness parts with strength exceeding wrought materials. Excellent corrosion resistance. |
Thermal Spray Coatings | Wear protection, electrical contacts with useful conductivity and temperature resistance. |
Braze Filler Alloys | Joins titanium alloys or dissimilar metal combinations with matching expansion coefficients. |
Sintered Structural Parts | Net-shape high performance parts with tailored physical properties. |
Specialty Reactive Materials | High energy outputs when formulated as thermites or intermetallic reactive composites. |
Table 4: Overview of applications and uses for molybdenum titanium powders
The ability to 3D print high strength, customizable shapes makes additive manufacturing a major growth area. The powders also enable protective coatings and advanced joining applications not easily achieved by other methods.
Specifications of molybdenum titanium powders
Molybdenum titanium powders are available under various industry and national specifications:
Standard | Description |
---|---|
ASTM B939 | Covers molybdenum alloys with >50% molybdenum content for thermal spray applications |
AMS 7758 | Nickel-base alloy powder and processing standard including titanium-molybdenum blends |
MIL-PRF-32495 | Performance standard for molybdenum and molybdenum alloy powders |
ISO 21818-1 | Additive manufacturing powder specification giving composition, sizes, production and testing |
Table 5: Industry and military specifications for molybdenum titanium powders
These specifications aim to standardize powder quality and ensure batch-to-batch consistency for mission-critical applications. They are continually evolving to meet industry demands.
Suppliers and Pricing
Molybdenum titanium powders are available from major metal powder suppliers and specialty additive manufacturing companies:
Supplier | Starting Price per kg |
---|---|
Sandvik Osprey | $450 |
Carpenter Powder Products | $200 |
Erasteel | $250 |
AP&C | $500 |
American Elements | $3000 |
Table 6: Overview of some molybdenum titanium powder suppliers and indicative pricing
Prices can vary widely depending on purity, powder characteristics and order quantities from hundreds of dollars per kg to several thousand. Custom alloys and particle optimization may have minimum order quantities.
Comparison
Molybdenum Titanium Powders vs. Molybdenum Metal Powders
Parameter | Molybdenum Titanium Powder | Pure Molybdenum Powder |
---|---|---|
Density | 5-6 g/cc | 10 g/cc |
Strength | Very high (>1 GPa) | High |
Oxidation Resistance | Good due to titanium | Poor, requires protective atmospheres |
Thermal Conductivity | Moderate (~100 W/m.K) | Very high (140 W/m.K) |
Cost | High ($250-500 per kg) | Low ($30-50 per kg) |
Table 7: Comparison of molybdenum titanium powders against pure molybdenum powders
Molybdenum titanium powders have much greater corrosion and oxidation resistance compared to pure molybdenum but lose some thermal conductivity. The titanium addition also lowers density. Cost is higher but justifiable for applications needing the alloy’s unique performance.
Molybdenum Titanium Powders vs. Stainless Steel Powders
Parameter | Molybdenum Titanium Powder | Stainless Steel Powder |
---|---|---|
Strength | Very high | Medium |
Hardness | Up to Rockwell 60 HRC | Max. Rockwell 45 HRC |
Corrosion Resistance | Excellent due to titanium oxide layer | Good for 300 series stainless steels |
Thermal Conductivity | Moderate (~100 W/m.K) | Poor (~20 W/m.K) |
Cost | High ($250-500 per kg) | Low ($5-30 per kg) |
Table 8: Comparison of molybdenum titanium powders versus stainless steel powders
Molybdenum titanium powders offer both higher strength and corrosion resistance compared to standard stainless steel grades. They provide much greater thermal conductivity as an added benefit. Cost is higher but worthwhile for specialized applications.
Advantages and Limitations
Advantages
- Extremely high strength exceeding wrought/forged materials
- Tailorable physical properties by adjusting molybdenum/titanium ratio
- Excellent corrosion resistance from titanium oxide protective layer
- Useful thermal and electrical conductivity from molybdenum
- Low coefficient of thermal expansion compared to steels
- Suitable for additive manufacturing and emerging applications
Limitations
- More expensive than conventional alloys like stainless steels
- Lower maximum use temperature than pure molybdenum
- Brittle molybdenum-rich compositions have poor ductility/fracture toughness
- Reactive with molten metals restricting welding/brazing options
- Controlled atmosphere processing required for parts with high molybdenum content
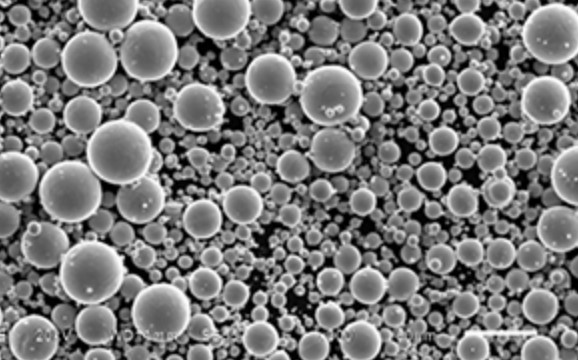
Frequently Asked Questions
Q: What is the main advantage of using molybdenum titanium powders instead of pure metal powders?
A: Molybdenum titanium powders provide a synergistic combination of corrosion resistance, high strength, useful thermal/electrical conductivity and controlled expansion behavior that the individual metals alone do not offer. This facilitates specialized applications in extreme environments.
Q: How are molybdenum titanium powders made?
A: Gas atomization and the plasma rotating electrode process allow the greatest control over powder characteristics. High energy ball milling produces composite powders by fracturing and cold welding feedstock materials.
Q: What industries use molybdenum titanium powders?
A: Aerospace, oil and gas, chemical processing, power generation, and medical implants drive adoption of molybdenum titanium parts made by additive manufacturing or sintering. The unique properties also suit niche applications like reactive materials and conductive coatings.
Q: Is additive manufacturing the primary application for these powders?
A: Additive manufacturing is the fastest growing application segment because of the high performance parts enabled. However, molybdenum titanium powders also have considerable use as thermal spray coatings and specialty braze filler alloys in other key industries.
Q: How do costs compare against common alternatives like stainless steels or tungsten alloys?
A: Molybdenum titanium powders range from 5-20 times more expensive than stainless steel grades per unit mass. However, they offer drastically improved mechanical properties and corrosion resistance. They are more affordable substitutes for tungsten alloys in terms of both raw material and finished part costs.
know more 3D printing processes
Frequently Asked Questions (FAQ)
1) What particle size distribution is optimal for Molybdenum Titanium Powders in AM vs. thermal spray?
- AM (LPBF): typically 15–45 μm (or 20–63 μm by supplier); higher sphericity improves spreadability. Thermal spray often uses coarser cuts (45–106 μm) to match feed and deposition rates.
2) Gas-atomized vs. ball-milled Mo–Ti powders: which should I choose?
- Gas/plasma-atomized: spherical, tight PSD, best for LPBF and consistent flow. High-energy ball-milled: composite/lamellar particles, useful for reactive brazes or certain HVOF coatings; less ideal for LPBF due to irregular morphology.
3) How does composition (Mo/Ti ratio) affect corrosion and oxidation resistance?
- Ti-rich alloys (≤40% Mo) form robust TiO2 surface films, improving corrosion/oxidation up to ~600–700°C. Mo-rich grades (>60% Mo) boost strength/conductivity but require stricter atmospheres and may oxidize faster.
4) Can Molybdenum Titanium Powders be reused in AM workflows?
- Yes, with inert handling, sieving, and blend rules. Track O/N/H, PSD shift, flow, and density per ISO/ASTM 52907 and ASTM E1019. Typical practice supports 5–8 cycles before blending with virgin powder.
5) What post-processing is common for Mo–Ti AM parts?
- Stress relief, HIP (if density targets require), machining/EDM, and surface finishing. For corrosion-critical uses, consider passivation or thin ceramic/metallic barrier coatings depending on service environment.
2025 Industry Trends: Molybdenum Titanium Powders
- Application pull from high-temp tooling and corrosive process hardware drives demand for intermediate Mo–Ti compositions (40–60% Mo).
- Plasma spheroidization gains share to improve sphericity of milled or water-atomized feeds for LPBF.
- Digital material passports (PSD, O/N/H, tap/apparent density, reuse count) adopted for cross-site qualification.
- Sustainability: argon recovery and powder circularity programs reduce atomization gas use 20–35% and extend reuse windows.
- Standards maturation: broader use of ISO 21818-1 for AM powders and alignment with ASTM chemistry/flow tests for Mo–Ti blends.
2025 KPI Snapshot for Molybdenum Titanium Powders (indicative ranges)
Metric | 2023 Typical | 2025 Typical | Notes/Sources |
---|---|---|---|
Sphericity (atomized AM grades) | 0.90–0.94 | 0.93–0.97 | Close-coupled atomization, plasma spheroidization |
LPBF build rate (cm³/h per laser) | 20–35 | 28–50 | Multi-laser + path optimization |
As-built relative density (optimized) | 98.0–99.4% | 98.5–99.7% | HIP to ≥99.9% when needed |
Oxygen content, wt% (AM grade) | 0.05–0.12 | 0.04–0.10 | Improved inert handling |
Reuse cycles before blend | 3–6 | 5–8 | With digital passports + sieving |
Reported recycled feed fraction | Rare | 5–15% | Supplier sustainability disclosures |
References: ISO/ASTM 52907; ISO 21818‑1; ASTM E1019; ASTM B212/B213/B703; OEM atomizer notes; NIST AM‑Bench insights
Latest Research Cases
Case Study 1: Plasma-Spheroidized Mo–Ti Powder for LPBF Thin-Wall Consistency (2025)
Background: A chemical equipment OEM saw recoater streaks and porosity in 0.6–1.0 mm walls using water-atomized Mo–Ti (60/40).
Solution: Introduced plasma spheroidization to lift sphericity >0.94, implemented tighter PSD (20–53 μm), and optimized hatch/contour strategy; added inert closed-loop powder handling.
Results: Layer defects −40%; apparent density +0.30 g/cm³; as-built density +0.6% absolute; scrap rate −22% across three part families.
Case Study 2: Corrosion-Fatigue Improvement of Ti-Rich Mo–Ti AM Manifolds (2024)
Background: A process plant required chloride-resistant, lightweight manifolds with superior fatigue in wet service.
Solution: Printed Ti‑80/Mo‑20 manifolds, applied HIP and fine shot peening followed by tailored passivation; validated per ASTM G48 and rotating-bending tests.
Results: Pitting resistance equivalent number (PREN proxy) performance matched design targets; corrosion-fatigue life +25% vs 316L baseline at equal mass; weight −30% vs machined alloy alternative.
Expert Opinions
- Dr. John Slotwinski, Materials Research Engineer, NIST
Key viewpoint: “Documenting PSD, O/N/H, and reuse history via digital passports is essential to make Molybdenum Titanium Powders portable across platforms and sites.” https://www.nist.gov/ - Prof. Ian Gibson, Professor of Additive Manufacturing, University of Twente
Key viewpoint: “Intermediate Mo–Ti compositions are emerging as practical choices for LPBF where corrosion and strength must be co-optimized without resorting to heavier refractory systems.” - Dr. Anushree Chatterjee, Director, ASTM International AM Center of Excellence
Key viewpoint: “Expect closer alignment of Mo–Ti powder QA with ISO 21818‑1 and broader adoption of standardized artifacts for qualification in regulated industries.” https://amcoe.astm.org/
Practical Tools/Resources
- ISO/ASTM 52907: Feedstock characterization for AM powders
https://www.iso.org/standard/78974.html - ISO 21818‑1: Additive manufacturing — Test methods for metal powders
https://www.iso.org/ - ASTM standards: E1019 (O/N/H), B212/B213/B703 (density/flow)
https://www.astm.org/ - NIST AM‑Bench: Benchmark datasets for AM validation
https://www.nist.gov/ambench - Senvol Database: Machine/material data for Mo–Ti applications
https://senvol.com/database - HSE ATEX/DSEAR guidance for combustible metal powders handling
https://www.hse.gov.uk/fireandexplosion/atex.htm
Last updated: 2025-08-27
Changelog: Added five targeted FAQs, 2025 KPI table, two recent case studies, expert viewpoints, and authoritative tools/resources specific to Molybdenum Titanium Powders.
Next review date & triggers: 2026-03-31 or earlier if ISO/ASTM standards update, major OEMs release Mo–Ti parameter sets, or new datasets on powder circularity and corrosion performance are published.