Overview
Aluminum powder refers to fine aluminum metal particles used as feedstock for manufacturing techniques like additive manufacturing, thermal spraying, powder metallurgy pressing and welding rods. Controlling aluminum powder characteristics like particle size distribution, morphology, oxide levels and microstructure is critical to properties of finished aluminum components.
There are various methods used for producing aluminum powders including:
- Gas atomization
- Air atomization
- Explosive wire fragmentation
- Milling and grinding
- Electrolytic process
- Chemical methods
Each aluminum powder production technique results in powders with different properties suited to specific applications.
Aluminum Powder Production Methods
Method | Key Characteristics | Main Applications |
---|---|---|
Gas Atomization | Spherical powders, moderate oxygen levels | Metal AM, thermal spray coatings |
Air Atomization | Irregular powder shapes, controlled oxide levels | Automotive parts, powder extrusion |
Explosive Wire | Very fine spherical powders | Additive manufacturing, rocket fuel |
Ball Milling | Composite aluminum powders | Energetic materials, pyrotechnics |
Electrolytic | Flake, angular and dendritic powders | Explosives, thermite reactions |
Chemical | Ultrafine to nanoscale particles | Pyrotechnic compositions |
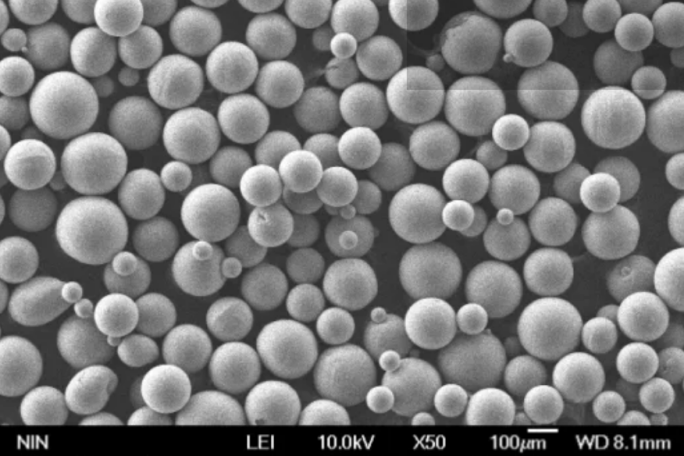
Aluminum Powder Production Methods
There are a variety of commercial methods used for producing aluminum powders depending on required material characteristics and end-use applications:
Gas Atomization
In gas atomization process, molten aluminum is disintegrated by high pressure inert gas jets into fine droplets which solidify into powder particles. Gas atomized aluminum powders have a spherical shape with sizes ranging from 10 microns to 350 microns based on processing parameters. This is the predominant technique for reactive aluminum powder production with lower oxygen pickup than liquid metal atomization.
Parameter | Description |
---|---|
Particle shape | Spherical morphology |
Particle size | 10 – 350 μm typical |
Oxide content | <3% by weight |
Production scale | Hundreds of tons per year |
Cost | Higher |
Air Atomization
In air atomization, molten aluminum stream is disrupted by compressed air jets, leading to formation of fine irregular aluminum particles containing higher surface oxide levels from oxygen in air. Air atomization facilitates economic, high volume aluminum powder production for structural P/M parts and aluminothermic reactions.
Parameter | Description |
---|---|
Particle shape | Irregular particle shape |
Particle size | 20 – 180 μm |
Oxide content | 3-8% by weight |
Production scale | Thousands of tons per year |
Cost | Very economical |
Rotating Electrode Process (REP)
In REP technique, molten aluminum metal in the form of wire or rod electrodes is rotated at high speeds, melting it using electrical arcing. Centrifugal forces eject the molten droplets producing very fine spherical aluminum particles ideal for specialized applications.
Parameter | Description |
---|---|
Particle shape | Highly spherical |
Particle size | 5 – 60 μm |
Oxide content | <1% by weight |
Production scale | Lower volumes |
Cost | Higher pricing |
Ball Milling
High energy ball milling of aluminum metal flakes, particles and chemical powders is done to form composite aluminum powders by embedding reinforcing particulates providing specialized mechanical, chemical or explosive reactivity.
Parameter | Description |
---|---|
Particle shape | Flattened and composite particles |
Particle size | 1 – 100 μm |
Oxide content | Coated particles |
Production scale | Small batches |
Cost | Moderate |
Electrolytic Process
In molten salt electrolysis process, aluminum ions are electro-deposited onto cathodes producing dendritic or irregular shaped particles with porous surface morphology ideally suited for pyrotechnic thermites.
Parameter | Description |
---|---|
Particle shape | Dendrites and irregular |
Particle size | 1 – 75 μm |
Oxide content | High from morphology |
Production scale | Lower volume |
Cost | Economical for niche applications |
Aluminum Powder Compositions
Most aluminum powders constitute high purity aluminum with over 98% Al content. The main considerations in composition are:
1. Alloying Elements
Small quantities of silicon, magnesium, zinc or other elements are added to impart specific properties.
Alloy Additions | Wt % Range | Effect |
---|---|---|
Silicon | 0.5 – 12% | Increase hardness and wear resistance |
Magnesium | 1 – 5% | Improves strength |
Zinc | 1 – 8% | Higher elevated temperature strength |
2. Oxide Content
Processing methods determine if thin protective oxide layers or heavier non-adherent oxides are present on particle surfaces.
Oxide Level | Suitability |
---|---|
<3% | High performance alloys, AM components |
3-8% | P/M structural parts |
>10% | Thermites, pyrotechnics |
3. Hydrogen Content
Moisture pickup during handling and storage of very reactive aluminum powder surface needs monitoring to prevent fire or detonation hazards. Manufacturing atmospheres with minimal humidity is beneficial.
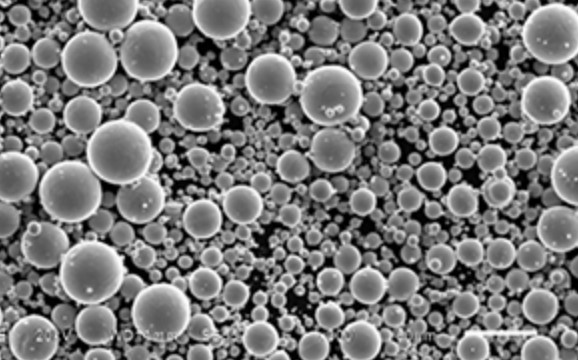
Properties of Aluminum Powders
Key attributes considered in qualifying aluminum powders include:
Powder Particle Size Distribution
Laser diffraction particle analyzers or sieve analyses provide full range granulometry from submicron to 500 microns size fractions. Typical size parameters reported are:
Parameter | Description |
---|---|
D10, D50, D90 | Particle diameter below which 10%, 50% and 90% particles by volume fall |
Mean, modal size | Measure of central tendency |
Span = (D90-D10)/D50 | Width of distribution – lower span indicates narrower distribution |
Matching particle sizes to production method capabilities allows maximizing density and properties in finished components.
Particle Morphology
Scanning electron microscopy reveals fine details of particle shape which dictates powder behavior. Smooth rounded particles improve flow and packing density. Irregular shapes provide mechanical interlocking.
Apparent and Tap Density
These indicate powder consolidation and handling behavior using standardized test procedures. Higher densities ease densification during compaction.
Parameter | Typical Range |
---|---|
Apparent density | 0.2 – 0.6 g/cc |
Tap density | 0.7 – 1.3 g/cc |
Flow Characteristics
Time for 50 g powder to flow through a Hall flowmeter funnel correlates well with spreading performance during layer filling in binder jet 3DP and filling die cavities in powder metallurgy compaction. Smooth spherical particles show improved flow rates.
Surface Area
Measured BET gas absorption surface area is used to calculate thicknesses of surface oxide layers present which impact initiation behavior in aluminothermic reactions or pyrotechnic combustion performances.
Applications of Aluminum Powders
Unique properties of reactive aluminum powders make them critical for various industries:
Metal Additive Manufacturing
Spherical aluminum powders are used as feedstock for selective laser melting, electron beam melting and binder jetting additive manufacturing after classifying powder particle size distribution to meet machine requirements.
Thermal Spray Coatings
Specialized low oxide aluminum powders plasma or wire sprayed create protective aluminum coatings offering high reflectivity combined with corrosion resistance.
Powder Metallurgy
Compacting and sintering aluminum powders produce high volume precision components like automotive parts with excellent dimensional control and performance unachievable by other techniques.
Energetic Materials
Fine aluminum powders thermite reactions with metal oxides or pyrotechnic combustions provide intense exothermic outputs for military, aerospace, or civil applications ranging from explosives and propellants to illumination, gas generation or heating.
Al-Mg Alloy Strips
Compacted aluminum powder preforms are hot extruded into Al-Mg alloy strips and coiled sheets ideal for armor plate fabrication. Powder metallurgy enables microstructural refinements and uniformity unfeasible in conventionally cast alloys.
Specifications and Standards
Aluminum powder producers must carefully control production atmospheres, processing techniques and handling procedures to meet certified standards for critical markets including:
AMS Metal Powder Specifications
- AMS 4200 steel shot and grit
- AMS 4205 aluminum powders for thermal spray
ASTM Standards
- B215 for gas atomized powders
- B951 for pressed and sintered aluminum powder extrusions
- B937 for gas atomized additively-manufactured aerospace parts
ISO Standards
- ISO 14361 thermal spray coatings
- ISO 22068 design of aluminium alloy die castings
CEN Standards
- EN 10204 3.1 material quality certification
SAE Aerospace Material Specifications (AMS)
- AMS 4200 shot/grit
- AMS 4205 gas atomized aluminum powder
Maintaining rigorous quality control to satisfy mandated chemistry limits on impurities like iron, silicon and zinc coupled with verifying powder characteristics fulfills application needs and safety in sensitive domains.
Aluminum Powder Market Analysis
Global demand for aluminum powders is estimated to reach 1.6 million metric tons by 2027 driven by:
1. Growth in Metal Additive Manufacturing
- Lightweighting benefits for aerospace components
- Healthcare implants and instruments from biocompatible Al alloys
2. Momentum in Automotive Lightweighting
- P/M aluminum parts replacing cast iron and steel
3. Innovation in Reactive Aluminum Energetic Formulations
- Defense, space, civil industries
Leading international aluminum powder producers are:
Supplier | Headquarters | Production Capabilities |
---|---|---|
Toyo Aluminium K.K. | Japan | Gas, air, vacuum atomization |
UC Rusal | Russia | Air atomization |
Alcoa Corporation | USA | Air atomization |
Luxfer Magtech | USA | Gas, air and centrifugal atomization |
Hoganas AB | Sweden | Air atomization |
Pricing varies based on:
- Production volume
- Purity levels
- Additional screening or milling
Grade | Price Estimate |
---|---|
Air atomized Al powders | $3 – $5 per kg |
Gas atomized spherical Al powder | $15 – $30 per kg |
Specialty Al alloy grades | Up to $50 per kg |
Benefits and Challenges
Advantages
- Lightweighting compared to steel or titanium
- Economical compared to other structural metals
- Reactive formulations providing intense exothermic outputs
- Recyclable and reusable
Challenges
- Highly exothermic oxidation requiring controlled inert handling and storage
- Hydrogen embrittlement decreasing mechanical properties
- Limited use temperatures up to 200°C for most formulations
Comparing aluminum powders to alternatives:
Parameter | Aluminum Powder | Stainless Steel | Titanium |
---|---|---|---|
Density | Low | Higher | Higher |
Cost | Low | Moderate | High |
Reactivity | High | Low | Moderate |
Environmental stability | Fair | Excellent | Very Good |
Food contact approvals | ✅ Yes | ✅ Yes | Some grades |
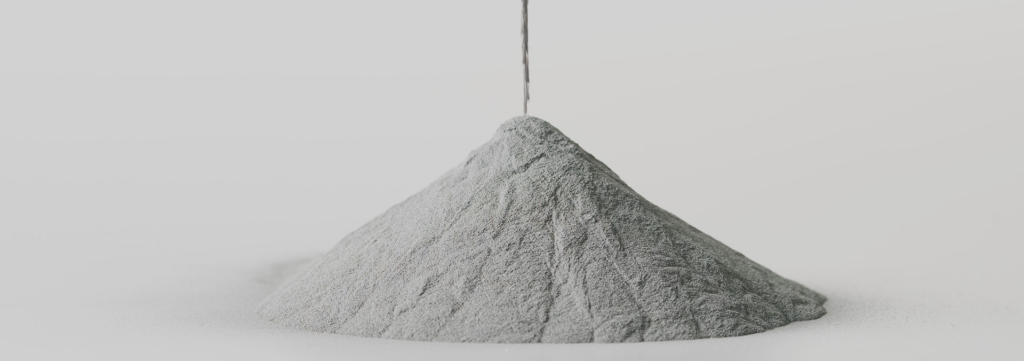
FAQs
Q: What particle size distribution is typically used with aluminum alloy powders for additive manufacturing?
A: In powder bed fusion AM, the aluminum particle size range is generally between 15 – 63 microns. Finer powders can improve resolution but make handling more difficult. Matching distributions to machine parameters is vital.
Q: What affects the shelf life of aluminum powders for energetic formulations?
A: Reactivity increases over time as storage humidity causes formation of aluminum hydroxides and hydrates on particle surfaces, releasing hydrogen and potential buildup flammable conditions. Inert sealed packaging and regulated humidity storage (<30%) is essential.
Q: What are common standards specified for aluminum powders used in thermal spray coatings?
A: Stringent chemistry limits on heavy metals regulated by FDA and USDA ensure finish coatings with no leachable impurities. Key standards include AMS 4205and ASTM B215 controlling Fe, Si, Cu trace elements. Thermal spray wire feedstock also follows ISO 14361.
Q: What aluminum alloy is preferred for additive manufacturing biomedical implants?
A: Aluminum alloy AlSi10Mg meets stringent chemistry requirements and offers excellent biocompatibility, strength and corrosion resistance combined with lower density than titanium or stainless steel alloys. Spherical powders enable complex printed geometries.
Q: How is risk of pyrophoric ignition handled when machining aluminum P/M components?
A: Low temperature annealing heat treatments are applied prior to any second machining operations to transform residual magnesium and aluminum particles present from explosive reactive states back into more stable intermetallic phases to safely enable conventional machining.