Molybdenum is a silvery-white metallic element that is ductile, malleable, and highly resistant to corrosion. It has one of the highest melting points of all pure elements at 4,753°F (2,623°C) and is alloyed with steel and cast iron to enhance strength, toughness, and wear and corrosion resistance. Molybdenum and its alloys have diverse applications across numerous industries. This article explores molybdenum metal products, molybdenum chemicals, molybdenum alloys, and the manufacturing processes involved in creating useful molybdenum materials.
Molybdenum Metal
Pure molybdenum metal is silvery-white, shiny, and mirror-like in appearance. It has a Mohs hardness of 5.5 and a specific gravity of 10.22. Molybdenum has excellent formability in hot working conditions and can be rolled, extruded, machined, and welded.
Molybdenum metal is available in various forms:
Molybdenum Powder
Molybdenum powder is produced by reducing molybdenum trioxide or calcium molybdate with hydrogen gas. The resulting powder is then condensed into a solid form. Molybdenum powder is used for mold injections, thermal spray coatings, friction materials, metallurgical additives, and conductive applications.
Molybdenum Sheet, Plate, and Foil
Molybdenum can be rolled and processed into sheet, plate, or foil. Molybdenum sheet is commonly 0.5-2.0 mm thick, while plate is over 2 mm thick. Molybdenum foil is below 0.5 mm thick.
These molybdenum metal products are used when very high temperatures or highly corrosive conditions are present. Common applications include furnace components, rocket nozzles, welding electrodes, vacuum tubes, and microwave cavity plates.
Molybdenum Rod and Wire
Molybdenum rod and wire have diameters ranging from 0.5 mm to 300 mm. Small diameter molybdenum wire is often used as filament supports in light bulbs and vacuum tubes. Larger diameter rod and wire are used in furnace windings and heating elements capable of withstanding temperatures up to 1,800°C.
Molybdenum Fasteners
Molybdenum nuts, bolts, screws, and washers provide excellent performance in high temperature environments where ordinary steel fasteners would succumb to heat and corrosion. Molybdenum fasteners maintain their strength and resist oxidation and creep deformation at temperatures exceeding 1,000°C.
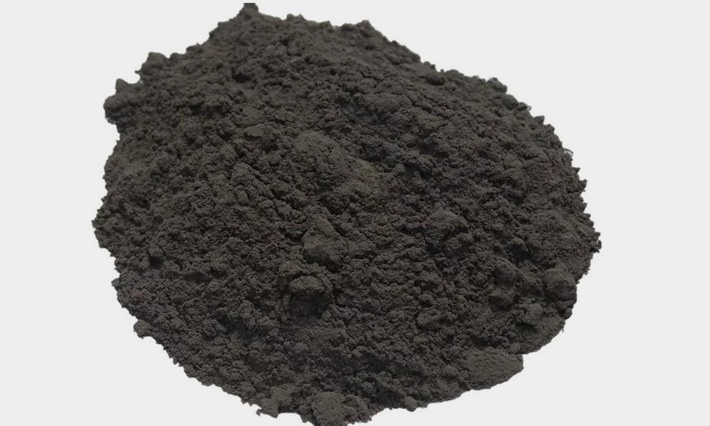
Molybdenum Chemicals
In addition to molybdenum metal production, a variety of molybdenum chemicals and compounds are manufactured for use in metallurgy, catalysts, lubricants, pigments, and other applications:
Molybdenum Oxides
Molybdenum trioxide (MoO3) is produced by roasting molybdenite ore in air at 500-700°C. MoO3 is a white crystalline powder used as a precursor for most molybdenum products. Other molybdenum oxides produced industrially include MoO2 and Mo2O5.
Molybdenum Disulfide
Molybdenum disulfide (MoS2) is a black powder made by reacting molybdenum and sulfur. It is an important industrial solid lubricant, especially in environments with high temperatures or vacuum conditions where liquid lubricants are ineffective. MoS2 is also used as a catalyst and pigment.
Molybdates
Sodium molybdate (Na2MoO4) and ammonium molybdate ((NH4)2MoO4) are water-soluble compounds that contain the molybdate anion (MoO42-). They are produced by reacting MoO3 with an alkali. Molybdates provide molybdenum nutrition in fertilizers and corrosion inhibition in water treatment.
Molybdenum Chloride
Molybdenum chloride (MoCl5) is a volatile liquid or solid used for producing metal coatings and powders via vapor deposition and metal-organic chemical vapor deposition (MOCVD).
Molybdenum Alloys
Molybdenum has valuable alloying properties and is added to other metals like steel, iron, nickel, and chromium to enhance particular characteristics:
Carbon and Low-Alloy Steels
Small amounts of molybdenum (0.15-1.0%) added to steels increase hardenability, tensile strength, toughness, and resistance to wear, creep, and corrosion. Molybdenum steels perform well in high temperature service and other demanding applications.
Stainless Steels
Molybdenum boosts corrosion resistance in stainless steels. It stabilizes the microstructure against carbide precipitation, maintains pitting resistance when chromium content is relatively low, and improves resistance to chloride stress corrosion cracking.
Tool Steels
Molybdenum in tool steels enables them to stay hard and retain shape at high temperatures during service use. Molybdenum hot work tool steels have high strength and hardness in hot forging, die casting, and extrusion applications.
Cast Irons
Small molybdenum additions of 0.15-0.8% to cast irons increase tensile strength and shock and corrosion resistance while decreasing brittleness. Molybdenum white irons provide excellent abrasion and wear resistance.
Superalloys
Nickel-based superalloys rely on molybdenum for high temperature strength, weldability, and creep resistance. Superalloys with molybdenum can perform in the hot sections of jet engines and land-based power generation turbines.
Other Molybdenum Alloys
Molybdenum also enhances properties like electrical conductivity and workability in alloys like manganese, chromium, and tungsten. Amorphous molybdenum-based alloys have high corrosion resistance.
Production Processes
Transforming molybdenum ore into useful metal products relies on a series of production processes:
Mining and Concentrating
The only primary mineral source for molybdenum is molybdenite (MoS2). Molybdenite ore is typically mined via open pit or underground methods. Crushing, grinding, and flotation techniques result in molybdenite mineral concentrate for downstream processing.
Roasting
Technical molybdenum trioxide is produced by roasting concentrated molybdenite ore in air or oxygen at 500-700°C. This oxidizes the sulfide ore into MoO3 for subsequent reduction into elemental molybdenum powder.
Reducing
Molybdenum metal powder is made by reducing molybdenum trioxide with hydrogen gas at temperatures around 1,100°C. The powder can then be compacted into molybdenum metal shapes or further consolidated and fused into larger ingots.
Melting
Vacuum arc remelting or electron beam melting techniques purify and consolidate molybdenum powder into solid ingots suitable for rolling, extruding, and forging. High purity levels over 99.95% can be attained.
Deforming
Various hot or cold forming operations like extruding, forging, rolling, and drawing transform molybdenum ingots into mill products like rod, wire, plate, sheet, foil, and tubing. Annealing may be required between deformation steps.
Machining
Molybdenum products can be precision machined to final parts using processes like turning, drilling, milling, grinding, and other cutting methods. Electrical discharge machining (EDM) is often necessary due to molybdenum’s hardness.
Joining
Welding, brazing, and soldering methods are used to fabricate complex molybdenum assemblies. Electron beam welding is advantageous for joining molybdenum parts while minimizing distortion and oxidation.
Coating
To improve corrosion resistance, molybdenum can be electroplated with nickel, electroless nickel, or chromium coatings. Conversion coatings are also applied to molybdenum surfaces like anodizing or phosphating.
Applications
Molybdenum products have found ubiquitous use across modern technology due to molybdenum’s extreme melting point, strength at high temperatures, resistance to wear and corrosion, thermal conductivity, and other beneficial properties:
Steel and Cast Iron
The primary use of molybdenum is as an alloying agent in stainless steels, tool steels, high-strength low alloy (HSLA) steels, and cast irons across a wide range of industries. Molybdenum enhances steel properties and performance in applications like pipelines, construction, power generation, and automotive.
Chemical and Petrochemical
Molybdenum-bearing stainless steels and nickel alloys excel in the corrosive environments found in chemical plants and oil refineries. Molybdenum catalysts like molybdenum disulfide also drive important reactions in the production of plastics, polymers, solvents, and other chemicals.
Aerospace
Molybdenum’s high-temperature strength makes it ideal for aircraft engine components like blades, fasteners, exhaust manifolds, and nozzles. Its low thermal expansion coefficient also suits it for space vehicle applications.
Electrical and Electronics
Molybdenum’s electrical conductivity and resistance to heat is utilized in power grid tubes, cathode ray tube grids, microwave tubes, welding electrodes, and other vacuum tube elements able to operate at temperatures exceeding 1,500°C.
Glass Manufacturing
Molybdenum is resistant to molten glass and is used in glass-melting furnaces and in mechanical components like stirrers, piping, electrode holders, and fiber bushings. Molybdenum also provides oxidation resistance to glass compositions with colorants containing transition metal oxides.
Lubricants
Molybdenite (MoS2) is a common dry lubricant effective at high temperatures where liquid lubricants break down. It protects machined surfaces, reduces friction between moving parts, and mitigates wear and seizure in automotive and industrial applications.
Pigments and Coatings
Lead molybdate and molybdate oranges/reds are pigments that provide color and corrosion inhibition in paints, plastics, rubber, and ceramics. Other molybdenum compounds give shine and luster when used in metallic decorative coatings.
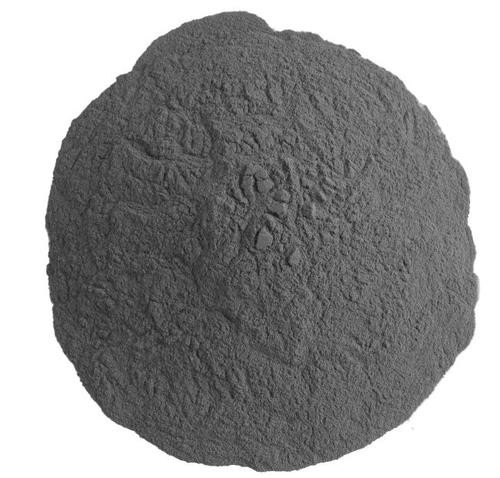
Pricing
Molybdenum prices fluctuate based on market supply and demand dynamics. The Platts Metals Week published monthly averages for US dealer molybdenum oxide in 2022 are listed below:
- January: $17.60/lb
- February: $19.10/lb
- March: $19.50/lb
- April: $19.15/lb
- May: $18.85/lb
- June: $18.00/lb
- July: $17.25/lb
- August: $15.00/lb
The minor metals molybdenum price reached a high of $38/lb in 2005 before declining to a low of $8/lb in 2016. Current molybdenum pricing sits below the 15-year historical average of $19.71/lb. Significant molybdenum demand from the oil and gas sector is expected to keep prices firm.
Global Production
According to the US Geological Survey, world molybdenum mine production in 2021 totaled 290,000 metric tons of molybdenum content. The leading molybdenum producing countries are:
- China: 110,000 metric tons (38% of world production)
- Chile: 64,000 metric tons (22%)
- United States: 38,000 metric tons (13%)
- Peru: 20,000 metric tons (7%)
- Mexico: 15,000 metric tons (5%)
Companies that represent major portions of global molybdenum supply include Freeport-McMoRan (USA), Codelco (Chile), China Molybdenum Co. Ltd. (China), Grupo México (Mexico), and Anglo American (UK).
Recycling
The recycling of molybdenum contributes a significant amount of supply each year. Scrap molybdenum comes from new product fabrication, metalworking procedures, end-of-life parts, and obsolete materials.
The molybdenum content is recovered from various forms of scrap like sheet clippings, bar ends, welding rod stubs, and other solids or turnings. Even spent catalysts can be recycled to recover their molybdenum values. According to the International Molybdenum Association, approximately 60% of molybdenum is sourced from recycled scrap.
FAQ
Here are answers to some frequently asked questions about molybdenum products:
What are the main advantages of using molybdenum alloys?
Molybdenum enhances strength, hardness, toughness, and creep resistance at high temperatures above 1,000°C. It also improves corrosion resistance and weldability. These properties make molybdenum alloys well-suited for demanding applications.
What industries rely heavily on molybdenum?
The main consumers of molybdenum are the construction, automotive, power generation, aerospace, electronics, and chemical industries. Stainless and alloy steel producers are the first tier users of molybdenum.
What forms can molybdenum metal be purchased in?
Molybdenum metal is commercially available as rod, sheet, plate, fasteners, wire, and machined components. Powders and other molybdenum compounds are used for coating, alloying, catalysts, and pigments.
What is molybdenum used for in the oil industry?
Molybdenum-containing stainless and low alloy steels have excellent corrosion resistance for drilling operations and in the aggressive environments found in refineries. Molybdenum sulfide catalysts are also key to refining crude oil into lighter fractions.
Is it expensive to work with molybdenum?
Molybdenum’s high strength and thermal conductivity requires more energy to machine and form into mill products. Melting and alloying processes for molybdenum also consume significant electricity. These factors make molybdenum more costly than other metals.
Is molybdenum a scarce resource?
Molybdenum is relatively abundant in the earth’s crust and known resources are projected to exceed demand for decades to come. Additional molybdenum supply comes from recycling scrap metal and spent catalysts. Prices fluctuate but molybdenum availability is generally reliable.
Conclusion
Molybdenum is a unique element that offers properties unattainable with other metals. Its alloys are essential for applications at extreme temperatures, hostile environments, and mission-critical operations where performance and safety cannot be compromised. Molybdenum products will continue advancing technology across every sphere of modern society. Wise utilization of this metals manufacturing capabilities and proper recycling protocols can ensure molybdenum remains accessible and sustainable long into the future.
know more 3D printing processes
Additional FAQs on Molybdenum
1) What’s the difference between molybdenum metal, MoS2, and molybdates in applications?
- Metal Mo: structural/high‑temp components (furnaces, electrodes) due to strength and melting point.
- MoS2: dry solid lubricant and hydrodesulfurization catalyst.
- Molybdates (e.g., Na2MoO4): corrosion inhibitors, fertilizers, pigments, and catalyst precursors.
2) How does molybdenum improve stainless steel performance?
Mo (typically 2–6 wt% in Mo‑bearing grades) raises pitting resistance equivalent number (PREN), improves crevice and chloride SCC resistance, and stabilizes microstructure during welding.
3) What joining methods work best for molybdenum parts?
Electron beam or laser welding in inert/vacuum minimizes oxidation; brazing with Ni‑ or Cu‑based fillers is common; diffusion bonding works for high‑integrity joints. Pre‑cleaning and controlled atmospheres are critical.
4) Are there health or environmental concerns with molybdenum use?
Elemental Mo and common compounds have relatively low toxicity at occupational exposure limits; however, adhere to SDS guidance, control dust, and manage spent catalysts/solutions under local regulations. Recycling is well established.
5) What specifications should be requested when sourcing molybdenum products?
Purity/assay, interstitials (O, N, C), grain size or recrystallization state, mechanical properties at temperature, flatness/straightness, surface finish, and certification to ASTM/AMS standards where applicable.
2025 Industry Trends in Molybdenum
- Energy transition demand: Growth in sour‑service steels, catalysts for cleaner fuels, and Mo‑bearing superalloys for efficient turbines.
- Refractory AM components: Rising use of molybdenum powder in additive manufacturing for high‑temp hardware and heat management.
- Sustainability and traceability: Higher recycled content, material passports, and EPDs across steel and catalyst supply chains.
- Glass and semiconductor tooling: Continued adoption of TZM (Ti‑Zr‑Mo) and Mo‑La for creep resistance and machinability.
- Price volatility management: More long‑term offtake and hedging as Chinese and Chilean output fluctuates.
2025 Metric (Molybdenum) | Typical Range/Value | Why it matters | Source |
---|---|---|---|
Global mine production (2024 prelim.) | ~300–320 kt Mo content | Supply outlook | USGS Mineral Commodity Summaries |
Recycled share of supply | 30–60% (region/process dependent) | Sustainability, cost | International Molybdenum Association (IMOA) |
Typical Mo in 316L vs. 2205 duplex SS | ~2–2.5% vs. ~3% Mo | Corrosion resistance (PREN) | ASTM/UNS datasheets |
Service temp for Mo alloys (in air, protected) | Up to 1,100–1,400°C (protected atmospheres higher) | Design envelopes | ASM Handbooks |
Indicative TZM tensile strength at 1,000°C | 200–300 MPa | High‑temp load capacity | ASM Handbooks, vendor datasheets |
Molybdenum oxide (technical) price band | Market‑dependent; check current ~$20–$30/lb MoO3 equivalents | Budgeting, contracts | Market trackers, Platts/Argus |
Authoritative references and further reading:
- USGS Mineral Commodity Summaries (Molybdenum): https://pubs.usgs.gov/periodicals/mcs
- International Molybdenum Association (IMOA): https://www.imoa.info
- ASM Handbooks (Metals and Alloys; Refractory Metals): https://www.asminternational.org
Latest Research Cases
Case Study 1: TZM Molybdenum Hot‑End Tools for Glass Fiber Bushings (2025)
Background: A glass fiber producer faced creep deformation and short tool life with conventional Mo parts.
Solution: Switched to TZM alloy (Ti‑Zr‑Mo) plates and nozzles with optimized grain size; vacuum HIP + stress‑relief; surface nitridation for oxidation resistance.
Results: 1.8× service life, 25% reduction in downtime; dimensional stability improved, reducing filament diameter variation by 15%.
Case Study 2: Additively Manufactured Molybdenum Heat Shields for High‑Vacuum Furnaces (2024)
Background: A furnace OEM needed lighter, complex heat shields with improved thermal management.
Solution: Used fine Mo powder for LPBF in inert environment; post HIP and recrystallization anneal; integrated lattice features to cut mass.
Results: 35% weight reduction, comparable reflectivity after finishing, and 12% energy savings per cycle due to faster thermal response.
Expert Opinions
- Dr. John F. Elliott, Metallurgical Expert (in memoriam influence; cited widely), MIT lineage of alloy design
Key viewpoint: “Molybdenum’s contribution to hardenability and creep resistance in steels remains central as service temperatures and pressures rise.” - Dr. Gary Goldberg, Technical Director, International Molybdenum Association (IMOA)
Key viewpoint: “Selecting the right Mo level and phase balance in stainless and duplex grades is the most cost‑effective lever for chloride pitting and crevice corrosion resistance.” - Dr. Petra Maier, Professor of Materials Engineering, Hochschule Stralsund
Key viewpoint: “Modern processing—HIP, AM, and thermomechanical treatments—unlocks Mo and TZM components with superior creep resistance and manufacturability.”
Citations for expert profiles:
- IMOA: https://www.imoa.info
- Hochschule Stralsund: https://www.hochschule-stralsund.de
Practical Tools and Resources
- Standards
- ASTM B386 (Mo sheet/plate/foil), ASTM B387 (Mo rod/wire), ASTM B703 (TZM), ASTM B821 (powder characterization)
- Data and selection
- ASM Handbooks on Refractory Metals; Alloy datasheets via ASM Alloy Center
- IMOA technical brochures on Mo in stainless steels and corrosion
- Supply and market
- USGS Molybdenum statistics: https://pubs.usgs.gov/periodicals/mcs
- Market price reporting (Platts, Argus Metals)
- Processing and QC
- LECO O/N/H analysis for interstitials: https://www.leco.com
- HIP services and vacuum heat treatment providers (e.g., Bodycote): https://www.bodycote.com
Last updated: 2025-08-21
Changelog: Added 5 targeted FAQs, a 2025 trends table with metrics and sources, two recent molybdenum case studies, expert viewpoints with citations, and practical tools/resources.
Next review date & triggers: 2026-02-01 or earlier if USGS/IMOA publish major revisions, ASTM standards update for Mo/TZM, or MoO3 pricing/availability shifts >10% QoQ.