1. Introduction
Metal powder additive manufacturing, also known as metal 3D printing, is a revolutionary manufacturing process that has gained significant attention in recent years. This innovative technique allows for the production of complex and customized metal parts, layer by layer, using powdered metal materials. In this article, we will explore the concept of metal powder additive manufacturing, its advantages, various processes involved, materials used, applications, challenges, and future trends in the field.
2. What is Metal Powder Additive Manufacturing?
Metal powder additive manufacturing is a process that involves the creation of three-dimensional objects by selectively melting or solidifying metal powders. Unlike traditional subtractive manufacturing methods, which involve cutting or shaping materials, additive manufacturing builds objects by adding material layer by layer. This approach allows for the creation of intricate and highly precise metal parts that would be challenging or impossible to produce using conventional techniques.
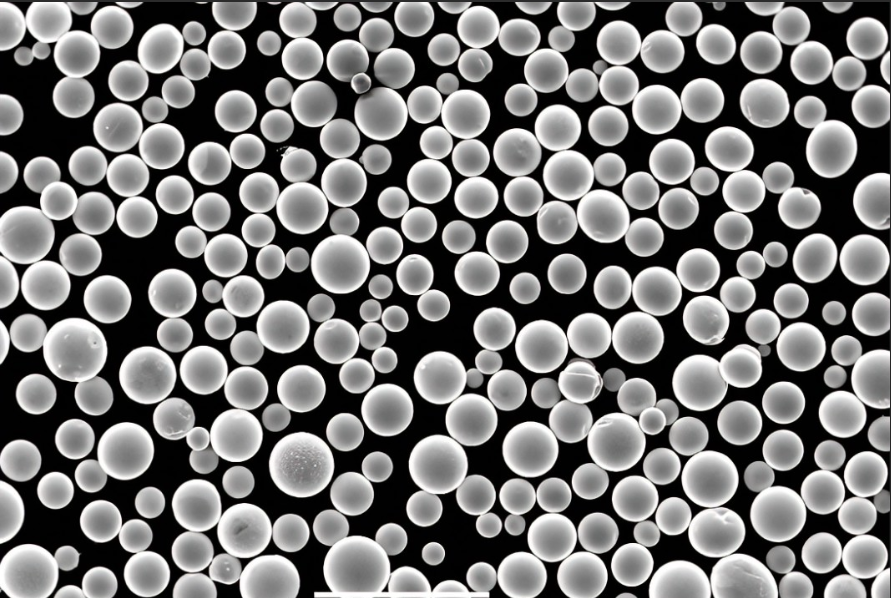
3. Advantages of Metal Powder Additive Manufacturing
3.1 Increased Design Freedom
Metal powder additive manufacturing offers unprecedented design freedom. The layer-by-layer approach enables the production of complex geometries, internal channels, and intricate lattice structures. Designers and engineers can unleash their creativity and develop innovative parts without the constraints imposed by traditional manufacturing processes.
3.2 Cost Reduction
Metal powder additive manufacturing can significantly reduce costs, especially for complex parts. By eliminating the need for tooling or molds, manufacturers can save substantial upfront expenses. Additionally, additive manufacturing can minimize material waste by only using the exact amount of metal powder required for the part, reducing material costs further.
3.3 Improved Time-to-Market
With metal powder additive manufacturing, the time required to bring a product to market can be significantly shortened. The elimination of tooling and the ability to produce parts on-demand allow for rapid prototyping and accelerated production cycles. This increased agility gives businesses a competitive edge by enabling faster product iterations and quicker responses to market demands.
3.4 Enhanced Material Properties
Metal powder additive manufacturing techniques can produce parts with unique material properties. The ability to control the microstructure and composition of the metal during the manufacturing process enables the creation of lightweight yet strong components. This opens up possibilities for applications where weight reduction, high temperature resistance, or specific mechanical properties are crucial.
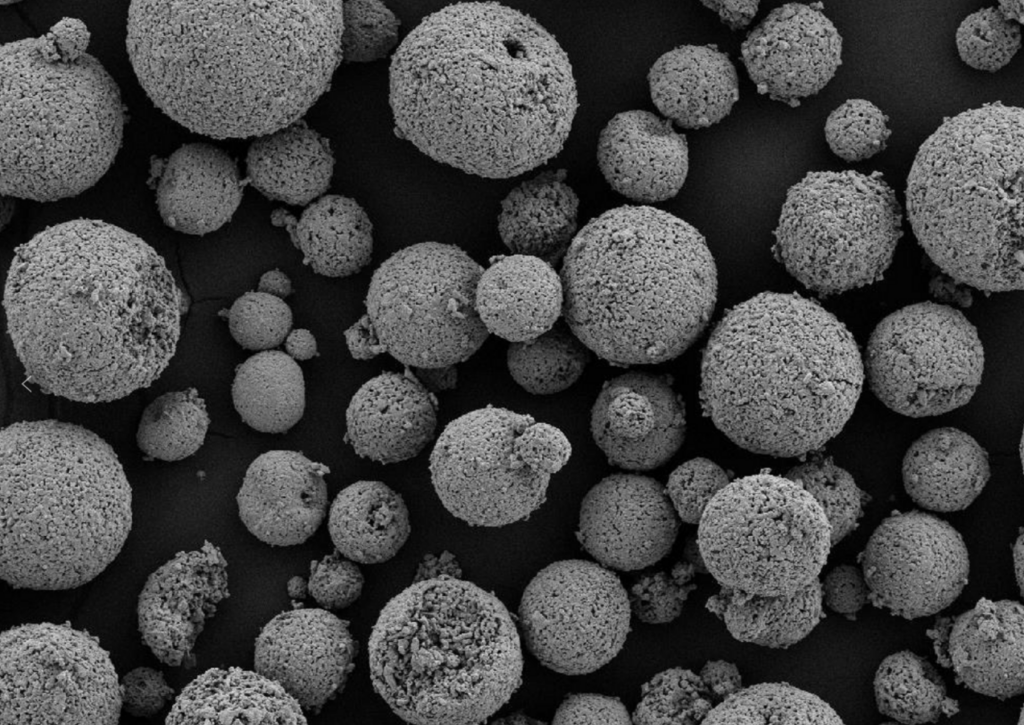
4. Types of Metal Powder Additive Manufacturing Processes
Metal powder manufacturing encompasses several processes, each with its own advantages and applications. Here are three commonly used techniques:
4.1 Powder Bed Fusion (PBF)
Powder Bed Fusion, also known as Selective Laser Melting (SLM) or Electron Beam Melting (EBM), is a widely adopted metal powder manufacturing process. It involves spreading a thin layer of metal powder on a build platform and selectively melting the powder using a laser or an electron beam. The melted powder solidifies, and the build platform is lowered, allowing the next layer of powder to be spread and melted. This process is repeated until the entire part is created.
4.2 Directed Energy Deposition (DED)
Directed Energy Deposition is a metal powder additive manufacturing technique that involves the precise deposition of metal powder using a nozzle or laser. The powder is simultaneously melted and fused onto a substrate or an existing part, creating layers and building up the desired shape. DED is often used for large-scale parts, repair applications, or creating complex geometries by adding material to an existing component.
4.3 Binder Jetting
Binder Jetting is a metal powder additive manufacturing process that involves selectively depositing a binder material onto layers of metal powder. This process is repeated layer by layer until the entire part is built. After the printing process, the green part is typically sintered in a furnace to remove the binder and fuse the metal particles together. Binder Jetting is known for its speed and scalability, making it suitable for high-volume production.
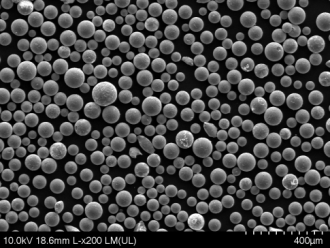
5. Materials Used in Metal Powder Additive Manufacturing
Metal powder manufacturing supports a wide range of materials, each with its unique properties. Some commonly used metals include:
5.1 Titanium Alloys
Titanium alloys are widely used in aerospace, medical, and automotive industries due to their excellent strength-to-weight ratio, corrosion resistance, and biocompatibility. Metal powder additive manufacturing allows for the production of complex titanium parts with optimized mechanical properties.
5.2 Stainless Steel
Stainless steel is known for its durability, corrosion resistance, and high-temperature resistance. Additive manufacturing enables the creation of stainless steel parts with intricate geometries and customized features, making it suitable for various industries, including automotive and medical.
5.3 Aluminum Alloys
Aluminum alloys are lightweight and offer excellent thermal conductivity. They find applications in aerospace, automotive, and consumer electronics industries. Metal powder additive manufacturing enables the production of complex aluminum parts with reduced weight and increased performance.
5.4 Nickel-Based Alloys
Nickel-based alloys exhibit excellent high-temperature resistance, corrosion resistance, and mechanical properties. They are commonly used in aerospace, energy, and chemical processing industries. Additive manufacturing allows for the production of nickel-based alloy parts with complex geometries and improved efficiency.
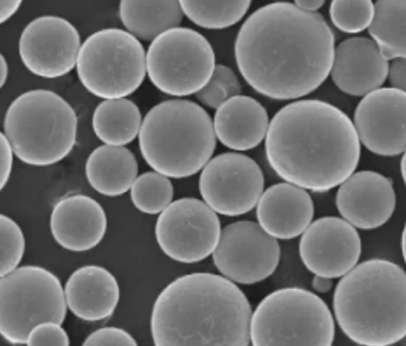
6. Applications of Metal Powder Additive Manufacturing
Metal powder additive manufacturing has found widespread applications across various industries. Here are some notable examples:
6.1 Aerospace and Defense
The aerospace and defense industries benefit greatly from metal powder additive manufacturing. It enables the production of lightweight yet strong components, reducing the weight of aircraft and enhancing fuel efficiency. Complex internal structures, such as cooling channels in turbine blades, can be easily produced, leading to improved performance and reliability.
6.2 Automotive
Metal powder additive manufacturing is revolutionizing the automotive industry. It enables the production of complex and lightweight parts, contributing to fuel efficiency and vehicle performance. Additive manufacturing also facilitates the customization of components, such as personalized interior elements or optimized engine parts.
6.3 Medical and Dental
In the medical field, metal powder additive manufacturing allows for the creation of patient-specific implants and prosthetics. Customized implants can be designed and manufactured based on individual patient scans, leading to better fit and improved patient outcomes. Metal powder additive manufacturing also enables the production of intricate dental structures, such as crowns, bridges, and orthodontic appliances, with high precision and accuracy.
6.4 Energy
Metal powder additive manufacturing plays a vital role in the energy sector. It is used for producing complex components for gas turbines, wind turbines, and nuclear power plants. Additive manufacturing allows for the optimization of part designs for improved energy efficiency, reduced emissions, and enhanced overall performance.
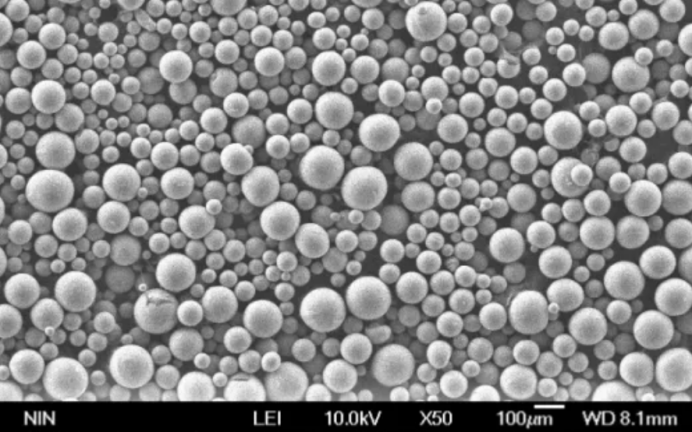
7. Challenges and Limitations of Metal Powder Additive Manufacturing
While metal powder additive manufacturing offers numerous advantages, there are some challenges and limitations to consider:
7.1 High Equipment Costs
The initial investment in metal powder additive manufacturing equipment can be significant. High-quality 3D printers, powder handling systems, and post-processing equipment require substantial financial resources. However, as the technology continues to advance and adoption increases, costs are gradually decreasing.
7.2 Limited Material Selection
Although the range of materials for metal powder additive manufacturing is expanding, it is still more limited compared to traditional manufacturing processes. Some materials may not be available in powder form or may exhibit challenges during the printing process. However, ongoing research and development efforts aim to broaden the range of printable materials.
7.3 Post-Processing Requirements
After the metal powder additive manufacturing process, post-processing steps may be necessary to achieve the desired part properties. These steps can include removing support structures, surface finishing, heat treatment, and quality inspection. Post-processing can add time and cost to the overall manufacturing process.
7.4 Quality Control and Certification
Ensuring consistent quality and meeting industry standards and certifications can be challenging in metal powder additive manufacturing. Process monitoring, material characterization, and non-destructive testing are crucial to validate the integrity and performance of printed parts. Robust quality control measures are essential to gain trust and acceptance in safety-critical industries.
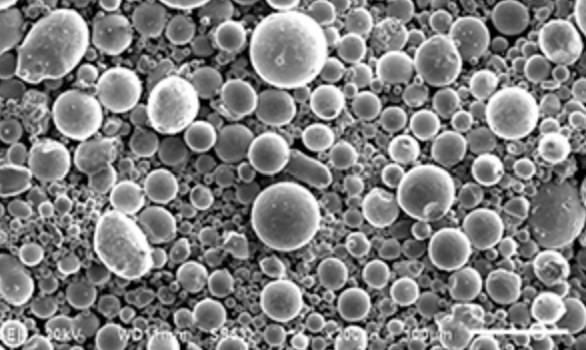
8. Future Trends in Metal Powder Additive Manufacturing
Metal powder additive manufacturing continues to evolve, and several future trends show great promise:
8.1 Multi-Material Printing
Advancements in metal powder additive manufacturing techniques are enabling the printing of multiple materials within a single part. This opens up possibilities for creating structures with graded material properties, such as combining lightweight and high-strength alloys in a single component.
8.2 Improved Process Monitoring
Enhanced process monitoring and control systems are being developed to ensure quality and consistency during the printing process. Real-time monitoring of temperature, laser power, powder distribution, and other parameters allows for better process optimization and detection of potential defects.
8.3 Scaling Up Production
Efforts are being made to scale up metal powder additive manufacturing for high-volume production. Increasing the printing speed, optimizing powder handling systems, and developing efficient post-processing techniques are key focus areas. The ability to produce large quantities of complex metal parts will further drive the adoption of additive manufacturing in various industries.
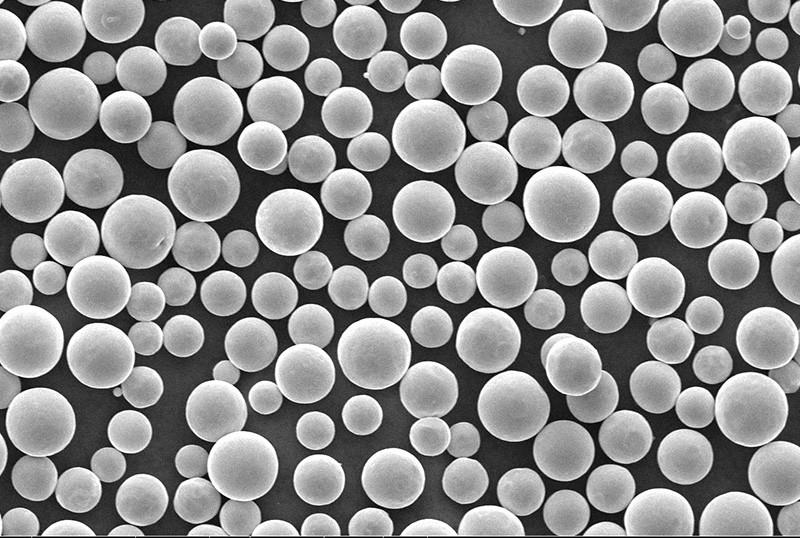
Conclusion
Metal powder additive manufacturing has revolutionized the manufacturing industry, enabling the production of complex, customized, and high-performance metal parts. With advantages such as increased design freedom, cost reduction, and improved time-to-market, this technology has found applications in aerospace, automotive, medical, and energy sectors, among others. While challenges and limitations exist, ongoing advancements in materials, processes, and quality control are addressing these issues. Exciting future trends, including multi-material printing and scaled-up production, promise further growth and innovation in the field of metal powder additive manufacturing.
FAQs
Q1: Is metal powder additive manufacturing cost-effective compared to traditional manufacturing methods? A: Metal powder additive manufacturing can be cost-effective, especially for complex parts with intricate geometries. It eliminates the need for expensive tooling or molds, reducing upfront costs. Additionally, additive manufacturing minimizes material waste by using only the necessary amount of metal powder, further reducing costs.
Q2: Can metal powder additive manufacturing produce parts with comparable strength to traditionally manufactured parts? A: Yes, metal powder additive manufacturing can produce parts with comparable strength and mechanical properties. The ability to control the microstructure and composition of the metal during the printing process allows for tailored material properties that can meet or exceed those of traditionally manufactured parts.
Q3: Are there any size limitations for metal powder additive manufacturing? A: Metal powder additive manufacturing can produce parts of varying sizes, from small intricate components to large-scale structures. However, the size of the build chamber or the printing platform may impose limitations on the maximum dimensions of the parts that can be printed in a single run.
Q4: Are there any environmental benefits associated with metal powder additive manufacturing? A: Metal powder additive manufacturing can contribute to environmental sustainability. It minimizes material waste by using only the necessary amount of metal powder, reducing the overall environmental footprint. Additionally, the ability to produce lightweight parts can lead to reduced fuel consumption and emissions in industries such as aerospace and automotive.
Q5: How does metal powder additive manufacturing impact the design process? A: Metal powder additive manufacturing offers unparalleled design freedom. Designers are not limited by traditional manufacturing constraints, enabling the creation of complex geometries, intricate lattice structures, and internal channels. This technology encourages innovative and optimized designs that were previously impractical or impossible to achieve.
In conclusion, metal powder additive manufacturing is a transformative technology that is reshaping the manufacturing landscape. With its advantages in design freedom, cost reduction, and material properties, it finds applications in diverse industries. Ongoing developments and future trends in multi-material printing, process monitoring, and scaling up production hold great promise for further advancements in this field. As the technology continues to evolve, metal powder additive manufacturing will continue to unlock new possibilities and drive innovation across industries.