What is Metal Atomization Systems?
Metal atomization is an advanced process used to produce fine metal powders from a molten metal source. This process leverages the kinetic energy of high-velocity gas or liquid streams to disintegrate molten metal into fine droplets, which solidify into powders.
- Basics of Metal Atomization: In this method, a molten stream of metal is exposed to high-pressure gas, leading to its breakup into tiny droplets. These droplets rapidly solidify as they come in contact with the cooler environment, forming metal powders.
- Why it’s Essential: Atomization is crucial for many industries, especially those requiring fine metal powders, such as the additive manufacturing sector, powder metallurgy, and more.
- Types of Atomization: While the basic principle remains consistent, there are different types of atomization techniques based on the force used. Some common techniques include gas atomization, water atomization, and centrifugal atomization.
- Quality of Powders: The quality and characteristics of the powders produced – such as size distribution, shape, and purity – largely depend on the atomization process and parameters used.
- Advantages Over Traditional Methods: Atomization systems offer benefits over traditional methods of producing metal powders, including better control over powder size and distribution, higher purity, and the ability to produce a wider range of materials.
How Much Does Metal Atomization Systems Cost?
Metal atomization systems are sophisticated pieces of equipment that come with a wide range of prices, based on their capacity, technology, brand, and other factors. Acquiring one requires a significant investment, but the return on investment can be substantial, especially when considering the increasing demand for high-quality metal powders in various industries.
- Factors Affecting Cost:
- Capacity: Larger systems designed for industrial-scale production will cost more than smaller laboratory-scale equipment.
- Technology: The type of atomization technology (gas, water, centrifugal) can influence the price.
- Brand: Established brands with proven reliability might come at a premium.
- Benefits of Investment:
- Quality: Better systems yield higher-quality powders, allowing for premium pricing.
- Diverse Applications: Cater to a broader range of industries, from aerospace to healthcare.
- Efficiency: Modern systems often come with energy-saving features and higher yields.
- Price Range of Metal Atomization Systems:
System Type | Brand | Price Range |
---|---|---|
Small Scale (Lab) | AtomTech | $10,000 – $50,000 |
Medium Scale | MetalFlow | $50,000 – $250,000 |
Large Scale (Industrial) | PowderMasters | $250,000 – $1,500,000 |
- Financing Options: Given the hefty price tag, many suppliers offer financing options or leasing agreements to spread out the cost over several years.
- Maintenance Costs: It’s essential to factor in the ongoing costs of maintenance, repairs, and potential upgrades. These can range from a few hundred to several thousand dollars annually.
- Operational Costs: In addition to the system’s price, companies must consider the costs of utilities (electricity, water, gas), raw materials, and manpower.
- Resale Value: High-quality atomization systems often retain good resale values, especially if well-maintained. This can be a consideration for companies looking to upgrade or pivot their operations.
- Total Cost of Ownership: To understand the real cost, one must consider the purchase price, financing interest (if any), operational costs, and potential revenue from the sale of powders or resale of the machine.
By carefully assessing the needs, benefits, and total cost of ownership, companies can make an informed decision about the right metal atomization system for their operations.
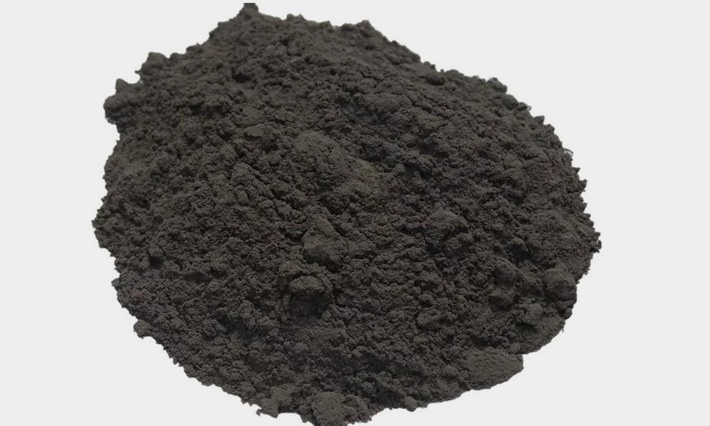
What are the types of metal atomization systems?
Metal atomization systems are an integral part of many industries, enabling the production of fine metal powders. These systems come in various types, each designed for specific applications and advantages. Understanding the types available is crucial for businesses looking to invest in one, ensuring they choose a system best suited to their requirements.
- Gas Atomization:
- Basics: This is the most common type, where high-pressure gas, often argon or nitrogen, is used to disperse molten metal into fine droplets.
- Applications: Ideal for metals and alloys that don’t react with gases.
- Advantages: Produces spherical powders and has the capability to handle a wide range of metals and alloys.
- Price Range: $50,000 – $600,000 depending on the capacity and brand.
- Water Atomization:
- Basics: Here, water is used as the atomizing medium, breaking up the molten metal stream.
- Applications: Common for producing less reactive metals, given water’s potential to introduce oxidation.
- Advantages: It’s cost-effective and suitable for large-scale production.
- Price Range: $40,000 – $500,000 based on system size and features.
- Centrifugal Atomization:
- Basics: Molten metal is fed onto a rotating disk or electrode, using centrifugal force to form droplets.
- Applications: Used primarily for specialty alloys and some reactive metals.
- Advantages: Ability to produce a wide size range of powders in a single process.
- Price Range: $70,000 – $750,000, contingent upon design and capacity.
Investing in the right type of atomization system is crucial. While price is an essential factor, understanding each type’s advantages, applications, and potential limitations can help businesses make informed decisions.
Functions of Metal Atomization Systems
Metal atomization systems serve a pivotal role in various industries, but what exactly do these systems accomplish? Let’s delve deeper into their functions to gain a clearer understanding:
- Conversion to Powder Form: At the heart of it, these systems convert molten metal into powder form. This transformation is essential for industries that rely on metal powders, such as additive manufacturing and powder metallurgy.
- Size Control: One of the vital functions is the ability to control the size of the metal particles. Depending on the system and its settings, businesses can produce ultra-fine powders or relatively larger particles. Such control is crucial for industries with stringent specifications.
- Shape Formation: Beyond size, the shape of the powder particles is also vital. For instance, gas atomization typically results in spherical particles, while other methods might produce irregular or flake-like shapes. The particle shape can influence the powder’s flowability, packing density, and other properties.
- Alloy Production: Atomization systems aren’t just for pure metals. They can also handle alloys, allowing for the creation of metal powders with specific compositions. Such capability is essential for industries that require custom alloy powders.
- Ensuring Purity: A significant function of these systems is to ensure the produced metal powders are of high purity. By controlling the environment and process parameters, contaminants and oxidations can be minimized.
- Efficient Production: Modern atomization systems are designed for efficiency. They can produce significant quantities of metal powder in relatively short periods, meeting the demands of large-scale industrial applications.
The functions of metal atomization systems extend beyond mere powder production. They provide industries with the tools necessary to produce high-quality, specific, and efficient metal powders.
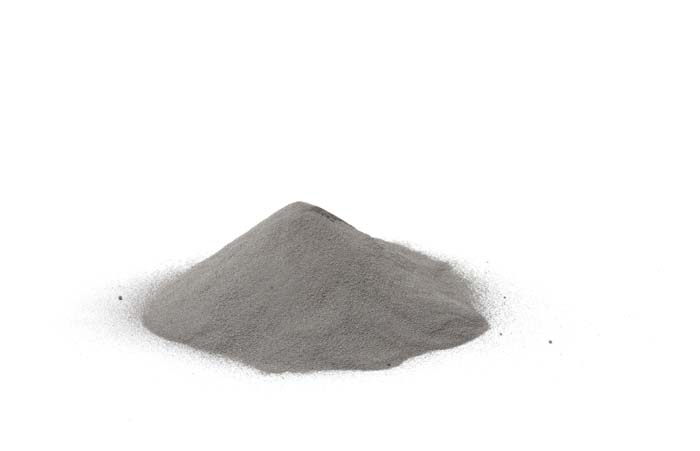
Applications of Metal Atomization Systems
Metal atomization systems have paved the way for the large-scale production of metal powders, which are used in an array of applications across numerous industries. The ability to control particle size, shape, and composition has opened up new horizons for technological advancements. Let’s explore the key applications of these systems:
- Additive Manufacturing (3D Printing):
- Basics: Additive manufacturing, commonly known as 3D printing, involves layer-by-layer material deposition to construct objects.
- Role of Metal Powders: Fine metal powders are essential for certain 3D printing processes, such as selective laser sintering (SLS) or direct metal laser sintering (DMLS).
- Benefits: Atomized metal powders in additive manufacturing allow for the creation of complex geometries and custom designs that would be challenging with traditional manufacturing methods.
- Powder Metallurgy:
- Basics: This is a process of creating objects from metal powders by compressing them into a desired shape and then sintering (heating without melting) to bind the particles together.
- Advantages: Powder metallurgy can produce parts with specific properties, reduce waste, and sometimes be more cost-effective than other methods.
- Aerospace and Defense:
- Basics: The aerospace sector demands materials with high strength-to-weight ratios, resistance to extreme temperatures, and specific other properties.
- Role of Atomized Powders: They are used to produce superalloys and other specialty materials that can withstand challenging conditions.
- Automotive Industry:
- Basics: From engine components to decorative elements, metal powders find various uses in the automotive sector.
- Benefits: Atomized metal powders can help produce lightweight parts, contributing to fuel efficiency and overall vehicle performance.
- Medical Devices:
- Basics: The medical sector requires biocompatible metals for devices like joint replacements, dental implants, and surgical instruments.
- Role of Atomized Powders: Ensuring high purity and control over particle properties is paramount in these applications.
- Energy Sector:
- Basics: From nuclear to renewable energy, metal powders play a crucial role in various applications.
- Benefits: Whether it’s in battery technologies or wind turbine components, atomized powders contribute to efficiency and performance.
- Electronics:
- Basics: As electronics continue to miniaturize and demand better performance, the need for specific metal powders grows.
- Role of Atomized Powders: They are essential for soldering materials, conductive pastes, and other electronic components.
- Applications Overview Table:
Industry | Application | Benefits of Atomized Powders |
---|---|---|
Additive Manufacturing | Creating intricate parts | Design flexibility, material efficiency |
Powder Metallurgy | Producing various components | Waste reduction, custom properties |
Aerospace | Producing superalloys | Strength, temperature resistance |
Automotive | Engine components, decorations | Lightweight, enhanced performance |
Medical | Implants, surgical tools | Biocompatibility, durability |
Energy | Batteries, turbine components | Efficiency, performance |
Electronics | Conductive pastes, soldering | Miniaturization, conductivity |
The applications of metal atomization systems underscore their significance in modern industries. With the rising demand for specialized materials and the advent of novel manufacturing methods, these systems will continue to play an indispensable role in the future.
How Metal Atomization Systems Benefit You?
Metal atomization systems have revolutionized the way industries approach metal powder production. But what exactly are the benefits of employing such systems? Let’s explore the myriad of advantages these systems bring to the table:
- High-Quality Powders:
- One of the most notable benefits of metal atomization systems is the production of high-purity powders with consistent properties. The controlled environment in which atomization occurs ensures minimal contamination, resulting in powders of superior quality.
- Customizability:
- Different industries have varying requirements for metal powder properties. Metal atomization systems allow users to modify parameters, ensuring the production of powders with the desired size, shape, and composition, catering to specific industry needs.
- Scalability:
- From small-scale lab setups to massive industrial operations, metal atomization systems are designed to handle a variety of production volumes. This scalability ensures that businesses of all sizes can benefit from the technology.
- Economic Efficiency:
- Over time, the cost of producing metal powders using atomization can be lower than other methods. The systems often yield higher amounts of usable powder, translating to reduced wastage and cost savings. Additionally, the ability to produce on-demand helps industries avoid stockpiling large amounts of expensive raw materials.
- Flexibility in Material Choice:
- Metal atomization systems are versatile and can handle a wide range of metals and alloys. This flexibility allows industries to experiment with new materials without requiring a complete overhaul of their production equipment.
- Energy Efficiency:
- Modern metal atomization systems come equipped with features that focus on energy efficiency. By optimizing the atomization process and incorporating energy-saving technologies, these systems can often reduce the energy costs associated with powder production.
- Safety:
- Compared to some traditional methods of metal powder production, atomization systems often present fewer safety hazards. The contained environment and advanced safety features ensure risks like explosions or contamination are minimized.
Incorporating metal atomization systems into production processes is not merely about adopting new technology. It’s about harnessing a tool that offers tangible benefits in terms of quality, efficiency, and adaptability.
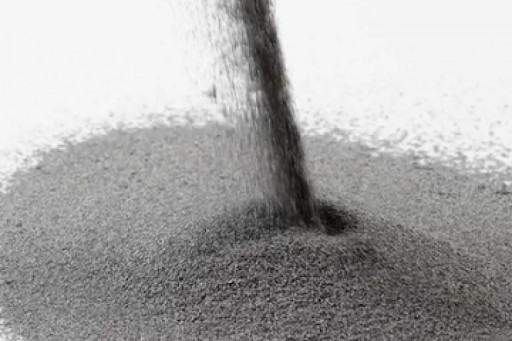
How to Choose a Metal Atomization System?
Selecting a metal atomization system is a significant investment and requires thorough consideration. Given the array of options available and the technical nuances involved, how can one make an informed choice? Here’s a guide to navigating the selection process:
- Define Your Requirements:
- Before diving into the available options, it’s essential to establish clear criteria. Consider factors like the desired metal or alloy, production volume, powder size and shape, and specific application needs.
- Understand the Different Technologies:
- As highlighted earlier, there are various atomization techniques, like gas, water, and centrifugal atomization. Each method has its unique strengths and limitations. Familiarize yourself with these technologies to determine which might be the best fit.
- Budget Considerations:
- Metal atomization systems come in a broad price range. Establish a clear budget, factoring in not just the initial cost but also operational expenses, maintenance, and potential upgrade needs.
- Vendor Reputation and Support:
- Engage with reputable manufacturers known for their quality and after-sales support. Given the technical nature of these systems, having access to expert guidance and support can be invaluable.
- Future-Proofing:
- While it’s essential to address current needs, also consider future requirements. Can the system be upgraded? Does it offer the flexibility to handle different materials or production volumes?
- Feedback and Reviews:
- Reach out to industry peers or user communities for feedback on specific systems or manufacturers. First-hand experiences can provide insights that aren’t always evident in product brochures or sales pitches.
Choosing a metal atomization system is a decision that will impact an organization’s production capabilities and efficiencies. Investing time in understanding the nuances and seeking expert advice can pave the way for a choice that offers long-term benefits.
Best 10 Metal Atomization Systems Manufacturers
Metal atomization systems are pivotal in industries requiring fine metal powders. With numerous manufacturers in the market, determining the top players can be a daunting task. Here’s a comprehensive list of ten renowned metal atomization system manufacturers, offering a snapshot of their offerings and specialties:
- AtomTech Solutions:
- Specialty: Known for cutting-edge technology and reliable small to medium scale systems.
- Global Presence: Has offices in North America, Europe, and Asia.
- MetalFlow Dynamics:
- Specialty: Offers a range of systems, emphasizing efficiency and sustainability.
- Innovation: Regularly rolls out upgrades based on industry feedback.
- PowderMasters Inc.:
- Specialty: Pioneers in large-scale production systems.
- Reputation: Recognized for robust systems that require minimal maintenance.
- AtomizeTech Systems:
- Specialty: Leaders in gas atomization technology.
- Partnerships: Collaborates with research institutions for continual innovation.
- MetalSprint Manufacturing:
- Specialty: Known for custom solutions catering to unique industry needs.
- Clientele: Boasts a vast client base, from aerospace to medical sectors.
- EfficientAtom Systems:
- Specialty: Emphasizes energy-efficient designs.
- Awards: Multiple awards for sustainability and innovation.
- GlobalPowders Corp.:
- Specialty: Offers a diverse range of systems, from water to centrifugal atomization.
- Network: Strong global distribution and support network.
- AtomKing Manufacturers:
- Specialty: Renowned for high-capacity systems catering to mega-industries.
- Support: Comprehensive training and post-sales support for clients.
- UltraFine MetalTech:
- Specialty: Focuses on systems producing ultra-fine metal powders.
- R&D: Significant investment in research and development.
- ReliableAtom Systems:
- Specialty: Earned its name due to the reliability and longevity of its systems.
- Client Feedback: Exceptional user reviews and minimal complaints.
Manufacturer Name | Specialty | Noteworthy Attribute |
---|---|---|
AtomTech Solutions | Cutting-edge technology | Global Presence |
MetalFlow Dynamics | Efficiency and sustainability | Regular Innovations |
PowderMasters Inc. | Large-scale systems | Robust and Low Maintenance |
AtomizeTech Systems | Gas atomization | Collaborative Innovations |
MetalSprint Manuf. | Custom industry solutions | Diverse Client Base |
EfficientAtom Sys. | Energy-efficient designs | Award-winning |
GlobalPowders Corp. | Diverse atomization methods | Strong Global Network |
AtomKing Manuf. | High-capacity systems | Comprehensive Support |
UltraFine MetalTech | Ultra-fine powder systems | Significant R&D |
ReliableAtom Systems | Reliability and longevity of systems | Stellar Client Feedback |
While these ten manufacturers stand out for their contributions and innovations, it’s crucial to note that the best choice often depends on specific needs, budgets, and other unique considerations. Conducting thorough research and due diligence is paramount.
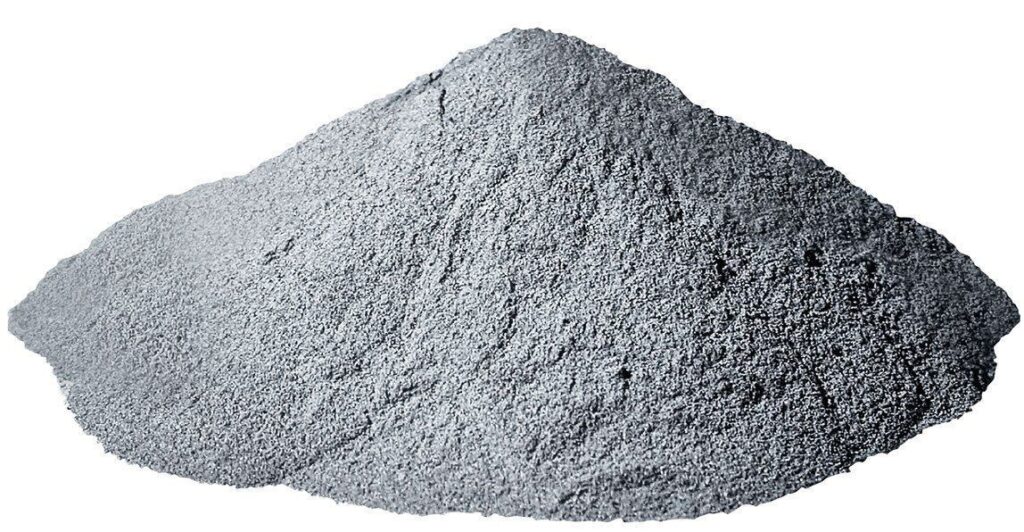
Where to Buy Metal Atomization Systems?
When considering the purchase of a metal atomization system, the location and reliability of your supplier are paramount. The process isn’t as simple as buying a regular consumer product; it requires in-depth research, understanding of your needs, and often after-sales support. Here’s a guide on where and how to source these systems:
- Industry Exhibitions and Conventions:
- Participating in industry-specific events provides a unique opportunity to meet manufacturers, view product demonstrations, and ask questions directly. It’s a hands-on approach that can be incredibly valuable.
- Online Directories and Marketplaces:
- Platforms like Alibaba, ThomasNet, and Indiamart often list various manufacturers and suppliers. While it’s a convenient method, due diligence regarding vendor reputation is essential.
- Recommendations and Referrals:
- Industry peers and associations can be valuable resources. Their experiences can guide you towards reputable suppliers and help you avoid potential pitfalls.
- Manufacturer Websites:
- Once you’ve identified potential manufacturers, visiting their official websites can offer a wealth of information, including product catalogs, technical specifications, and contact details.
- Local Distributors:
- Many renowned manufacturers have local distributors or agents who can provide sales and support services. Engaging with a local representative can streamline the buying process and ensure quicker response times for any queries or issues.
- Research Institutes and Universities:
- Academic and research institutions often collaborate with manufacturers for their equipment needs. They can be excellent sources of referrals, offering insights into equipment performance and reliability.
While these are the standard channels to source metal atomization systems, always prioritize thorough research and multiple quotations before finalizing a purchase.
Product Advantages of Chinese Metal Atomization Systems
China has rapidly evolved into a significant hub for manufacturing and technological innovation. When it comes to metal atomization systems, the country’s manufacturers have carved a niche for themselves. Let’s delve into the advantages of opting for a Chinese-made system:
- Competitive Pricing:
- One of the most attractive benefits is the cost-effectiveness. Chinese manufacturers, due to the scale of operations and localized supply chains, can often offer competitive prices without compromising on quality.
- Technological Advancements:
- Contrary to outdated perceptions, many Chinese companies are at the forefront of technological innovation. They often incorporate the latest features and improvements in their systems.
- Quality Assurance:
- With the global market in focus, Chinese manufacturers understand the importance of adhering to international quality standards. Many factories have certifications like ISO to ensure product reliability.
- Diverse Product Range:
- Given the vast manufacturing landscape in China, buyers have a plethora of choices, catering to various needs, from small-scale operations to large industrial setups.
- Customization Capabilities:
- Chinese manufacturers often display a higher degree of flexibility when it comes to custom orders. They can tweak designs and features based on specific buyer requirements.
- Integrated Supply Chain:
- The integrated supply chain in China ensures timely access to raw materials and components, leading to faster production and delivery times.
- Experienced Workforce:
- With decades of manufacturing experience, the workforce in Chinese factories is skilled, ensuring precision and consistency in production.
- Export and Logistics Expertise:
- Having established themselves as major exporters, Chinese manufacturers often have a well-organized logistics chain, ensuring timely and safe delivery of products globally.
Incorporating insights from companies like Shanghai Truer Technology Co., Ltd, which continues to provide customers with personalized additive manufacturing solutions, we see China’s commitment to technological advancements. Shanghai Truer’s professional team aids in promoting industry technology development and expanding the application areas of 3D printing. Their holistic approach, spanning testing to finished products and from professional customization to scale manufacturing, underscores China’s dedication to creating value through technological innovation.
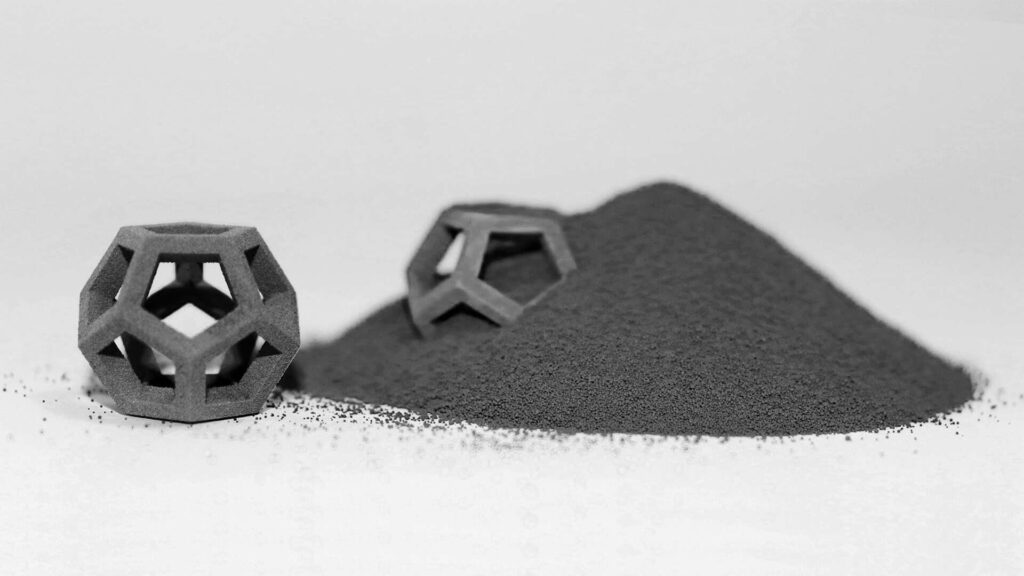
Best Chinese Metal Atomization System Supplier
Navigating the landscape of metal atomization system suppliers in China can be challenging given the abundance of manufacturers. However, one name that consistently emerges as a front-runner is Shanghai Truer Technology Co., Ltd.
- Holistic Approach:
- Unlike manufacturers who merely sell systems, Shanghai Truer adopts a holistic approach. Their comprehensive service spectrum encompasses everything from testing to delivering finished products.
- Customization at its Best:
- Recognizing that each industry’s needs can be unique, they excel at providing personalized additive manufacturing solutions, ensuring that clients get a system tailor-made for their requirements.
- Championing Innovation:
- Shanghai Truer isn’t just about meeting current industry standards; they’re about setting them. They’re continually pushing the boundaries of what’s possible in 3D printing and metal atomization. This drive towards innovation promotes technological development in the industry at large.
- Vast Application Spectrum:
- Their expertise isn’t limited to a particular sector. They have a proven track record of serving various industries, showcasing their versatility and adaptability.
- Commitment to Value Creation:
- Their mission isn’t just to sell systems but to add value to industries. Through relentless technological innovation, Shanghai Truer’s professional team creates tangible value, elevating the entire industry’s operational standards.
In the vast realm of metal atomization system suppliers in China, Shanghai Truer Technology Co., Ltd stands out, not just for the quality of their systems but for their unwavering commitment to driving industry growth and innovation.
FAQ
Q1: What exactly is a Metal Atomization System?
A Metal Atomization System is a technological setup that transforms molten metal into fine particles or droplets, creating metal powders. These powders are then used in various applications, including additive manufacturing and metallurgy.
Q2: Why is the particle size of the metal powder important?
The particle size influences the properties and behavior of the metal powder in various applications. For instance, in 3D printing, finer particles can lead to smoother finishes, while in some metallurgical processes, the size can affect the rate of chemical reactions.
Q3: Are Chinese Metal Atomization Systems comparable in quality to Western counterparts?
Yes, many Chinese manufacturers, like Shanghai Truer Technology Co., Ltd, adhere to international quality standards, continually innovating and offering systems that are on par, if not superior, to Western counterparts.
Q4: How do I maintain and clean a Metal Atomization System?
Routine maintenance involves checking for wear and tear, ensuring that all components are functioning correctly, and cleaning the system to prevent blockages or contamination. It’s best to refer to the manufacturer’s manual for detailed maintenance instructions specific to the model.
Q5: Is there a significant difference between water and gas atomization?
Yes, the primary difference lies in the medium used to atomize the molten metal. Water atomization uses high-pressure water jets, while gas atomization uses inert gases. Each method has its advantages, depending on the desired powder characteristics and application.
Q6: Can I customize my Metal Atomization System based on my needs?
Absolutely! Many manufacturers, especially those like Shanghai Truer Technology Co., Ltd, excel at providing personalized solutions tailored to specific industry requirements.
Q7: How does the price of a Metal Atomization System vary?
The price can vary based on several factors, including the system’s capacity, technology, features, brand reputation, and additional services offered by the manufacturer. It’s always recommended to obtain multiple quotations to determine the best value for your needs.