Have you ever marveled at the intricate gears of a high-performance bike or the robust strength of a construction crane? The secret behind many such marvels of modern engineering lies in a tiny, unassuming hero: low alloy steel powder. This innovative material is revolutionizing the way we manufacture complex parts, offering a potent blend of strength, versatility, and precision.
But what exactly is low alloy steel powder, and how does it translate into real-world applications? Buckle up, because we’re about to delve into the fascinating world of this transformative material.
Low Alloy Steel Powder: A Compositional Powerhouse
At its core, low alloy steel powder is a metal powder derived from steel with a carefully controlled composition. Unlike traditional steel, which contains minimal additional elements besides iron and carbon, low alloy steel powder incorporates small quantities of other metals like chromium, manganese, nickel, and molybdenum. These alloying elements, even in small amounts, play a crucial role in enhancing the steel’s properties, making it:
- Stronger: Alloying elements like chromium and manganese contribute to a more robust internal structure, leading to increased strength and resistance to deformation. Imagine steel as a tangled web of iron atoms. Alloying elements act like reinforcements, weaving themselves into this web and creating a more resilient structure.
- More hardenable: Certain elements, like molybdenum, improve the steel’s ability to harden during heat treatment processes. Think of hardening like tempering a blade. Molybdenum helps the steel “hold its edge” for longer, offering superior wear resistance.
- More versatile: The specific combination of alloying elements can be tailored to achieve desired properties. Need a steel that’s both strong and weldable? Nickel can help strike that balance. It’s like having a toolbox filled with different alloying elements, each offering unique benefits for specific applications.
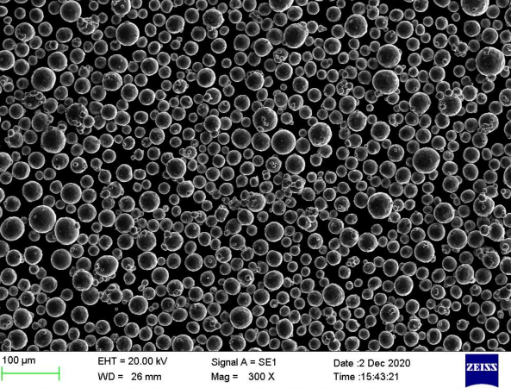
Here’s a table outlining the types, composition, properties, and characteristics of various low alloy steel powders:
Type of Low Alloy Steel Powder | Composition (wt%) | Key Properties | Characteristics |
---|---|---|---|
17-4PH | Fe (Bal.), Cr (17), Ni (4), Cu (4) | High strength, good corrosion resistance, excellent machinability | Widely used in aerospace and medical applications |
4140 | Fe (Bal.), Cr (1), Mo (0.25), Mn (0.80), C (0.40) | High strength, good hardenability, excellent toughness | Popular choice for gears, shafts, and other structural components |
316L | Fe (Bal.), Cr (16-18), Ni (10-14), Mo (2-3) | Excellent corrosion resistance, good weldability | Ideal for applications requiring high resistance to chemicals and saltwater, such as marine components and medical implants |
AISI 42CrMo4 | Fe (Bal.), Cr (1.00), Mo (0.20), Mn (0.70), C (0.42) | High strength, good toughness, excellent fatigue resistance | Used extensively in the automotive industry for parts like crankshafts and connecting rods |
20MnCr5 | Fe (Bal.), Mn (1.30), Cr (0.60), C (0.20) | High strength, good ductility, excellent wear resistance | A cost-effective option for automotive prototyping and general-purpose components |
CM24 | Fe (Bal.), Cr (2.5), Mo (0.4), Ni (0.5) | High strength, good creep resistance at elevated temperatures | Used in power generation and oil & gas industries for components operating under high stress and heat |
GLTech AM300 | Fe (Bal.), Ni (2), Cr (0.5), Mo (0.5) | Good strength, high ductility, excellent toughness | A versatile option for a wide range of applications, known for its good balance of properties |
Hoeganaes DM20 | Fe (Bal.), Ni (2), Cr (0.5), Mo (0.5) | Similar properties to GLTech AM300 | Another popular choice offering a good balance of strength, ductility, and toughness |
Carpenter AM 301 | Fe (Bal.), Ni (1.8), Cr (0.5), Mo (0.3) | High strength, good fatigue resistance | A premium option for demanding applications requiring superior performance |
Extrude Hone AM304L | Fe (Bal.), Ni (8-12), Cr (18-20), Mo (2-3) |
Low Alloy Steel Powder: A Manufacturing Marvel
The magic of low alloy steel powder lies not just in its composition, but also in the way it revolutionizes manufacturing. Traditional methods like machining or casting often involve significant material waste and limitations in creating complex geometries. Here’s where low additive manufacturing (AM), also known as 3D printing, steps in as a game-changer.
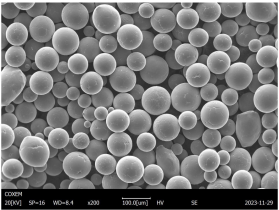
Low alloy steel powder shines in AM for several reasons:
- Near-net shape manufacturing: AM builds parts layer by layer using the powder, allowing for the creation of intricate shapes with minimal material waste. Imagine building a complex gear with internal channels – a near-impossible feat with traditional methods, but easily achievable with AM and low alloy steel powder.
- Design freedom: AM breaks free from the constraints of traditional manufacturing, allowing engineers to design complex geometries that were previously impossible. Think of lightweight structures with internal lattices for strength or parts with intricate cooling channels for improved performance.
- Mass customization: AM enables the production of customized parts in small batches, making it ideal for prototyping, low-volume production runs, or even creating personalized medical implants.
Here’s a table showcasing some of the applications of low alloy steel powder across various industries:
Industry | Application | Specific Low Alloy Steel Powder | Advantages |
---|---|---|---|
Aerospace | Turbine blades, landing gear components, lightweight structural parts | 17-4PH, CM24 | High strength-to-weight ratio, excellent mechanical properties at elevated temperatures |
Automotive | Gears, crankshafts, connecting rods, brake components | AISI 42CrMo4, 20MnCr5 | High strength, good fatigue resistance, wear resistance |
Medical | Dental implants, surgical instruments, prosthetics | 316L | Excellent corrosion resistance, biocompatibility |
Oil & Gas | Downhole tools, valves, pressure vessels | CM24 | High strength, creep resistance at high temperatures |
Tooling | Molds, dies, punches | GLTech AM300, Hoeganaes DM20 | Good balance of strength, ductility, and toughness for tooling applications |
Consumer Goods | Sporting goods components, bicycle parts, firearms components | Various depending on application | Design freedom, lightweighting capabilities |
It’s important to note that selecting the right low alloy steel powder is crucial for optimizing performance in a specific application. Factors like desired strength, corrosion resistance, and printability all play a role. Here’s a table outlining some of the key considerations when choosing a low alloy steel powder:
Factor | Description | Example |
---|---|---|
Strength | The ability of the material to withstand stress without breaking | AISI 42CrMo4 is a good choice for high-strength applications like crankshafts. |
Hardness | The material’s resistance to permanent indentation | Adding molybdenum to a steel powder can improve its hardenability. |
Toughness | The material’s ability to absorb energy before fracturing | GLTech AM300 offers a good balance of strength and toughness for various applications. |
Corrosion resistance | The material’s ability to resist rust and degradation | 316L is ideal for applications requiring high resistance to chemicals and saltwater. |
Printability | How well the powder flows and fuses during the AM process | Powders with a spherical shape and consistent particle size generally offer better printability. |
Several reputable suppliers offer a wide range of low alloy steel powders, with prices varying depending on the specific composition and particle size. Here’s a table listing some prominent suppliers for your reference (note that pricing information may change and needs to be obtained directly from the supplier):
Supplier | Website | Products |
---|---|---|
Höganäs AB | https://www.hoganas.com/en/ | A broad range of low alloy steel powders for AM |
Carpenter Additive Manufacturing | https://www.carpentertechnology.com/additive-manufacturing | Premium low alloy steel powders for demanding applications |
Extrude Hone Corporation | https://www.extrudehone.com/ | Low alloy steel powders for various AM applications |
AP Powder Company | https://www.allpowderpaints.com/ | Metal powders for AM, including low alloy steel grades |
Pros and Cons of Low Alloy Steel Powder in AM
Like any material, low alloy steel powder in AM has its own set of advantages and limitations:
Pros:
- High strength-to-weight ratio: Low alloy steel powder can achieve excellent strength while maintaining a relatively low weight, making it ideal for applications like aerospace components where weight reduction is critical. Imagine an airplane wing – it needs to be incredibly strong to handle the stress of flight, but also lightweight for optimal fuel efficiency. Low alloy steel powder in AM helps strike this delicate balance.
- Design freedom: As mentioned earlier, AM breaks free from traditional manufacturing constraints. With low alloy steel powder, engineers can design complex geometries that were previously impossible. This opens doors for innovation in everything from lightweight structures with internal lattices for strength to parts with intricate cooling channels for improved heat dissipation in engines.
- Material efficiency: AM with low alloy steel powder minimizes material waste compared to traditional methods like machining. Think of carving a complex gear out of a solid block of steel – a significant amount of material ends up as scrap. AM builds parts layer by layer, using only the necessary amount of powder, leading to a more sustainable and cost-effective approach.
- Mass customization: AM allows for the production of customized parts in small batches. This makes low alloy steel powder ideal for prototyping, creating specialized tools and molds, or even manufacturing personalized medical implants that perfectly match a patient’s anatomy.
Cons:
- Cost: While AM technology is constantly evolving and becoming more affordable, low alloy steel powder AM can still be more expensive than traditional manufacturing for high-volume production runs. This is due to factors like the cost of the powder itself, the AM machines, and the overall process.
- Surface roughness: Parts printed with AM can have a slightly rougher surface finish compared to traditionally machined components. However, post-processing techniques like polishing or machining can be used to achieve a smoother surface if needed.
- Limited material selection: While the range of available low alloy steel powders for AM is growing, it’s still not as vast as the options available for traditional steel production. This can limit applications in specific industries where unique material properties might be required.
- Process control: The success of AM with low alloy steel powder relies heavily on proper process control parameters. Factors like laser power, scan speed, and powder bed temperature all play a crucial role in achieving the desired mechanical properties in the final part.
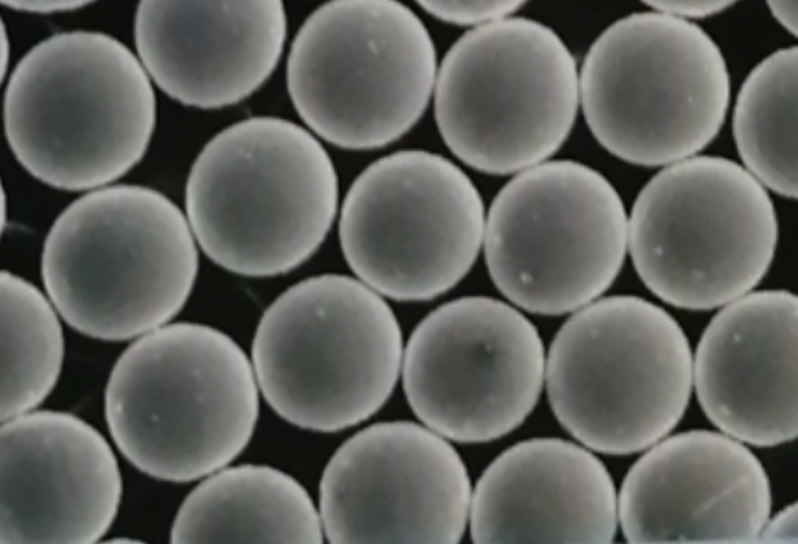
FAQ
Here are some frequently asked questions (FAQ) regarding low alloy steel powder:
Q: What are the different types of low alloy steel powder available for AM?
A: There’s a wide range of low alloy steel powders available, each with a specific composition tailored for different properties. Some common types include 17-4PH for high strength and corrosion resistance, 4140 for good hardenability, and 316L for excellent corrosion resistance.
Q: What are the advantages of using low alloy steel powder over traditional steel in AM?
A: Low alloy steel powder offers several advantages, including near-net shape manufacturing with minimal waste, design freedom for complex geometries, and mass customization capabilities for small batch production.
Q: What are some of the limitations of using low alloy steel powder in AM?
A: Some limitations include potentially higher costs compared to high-volume traditional manufacturing, slightly rougher surface finishes, and a limited selection of materials compared to traditional steel production.
Q: How strong are parts made with low alloy steel powder?
A: Low alloy steel powder can achieve very high strength levels, depending on the specific composition and processing parameters.
Q: What industries are using low alloy steel powder in AM?
A: Low alloy steel powder finds applications in various industries, including aerospace, automotive, medical, oil & gas, tooling, and even consumer goods.
In conclusion, low alloy steel powder is a revolutionary material that’s transforming the landscape of additive manufacturing. Its unique combination of strength, versatility, and design freedom opens doors for innovation across various industries. As AM technology continues to evolve and costs become more competitive, we can expect to see even wider adoption of low alloy steel powder, shaping the future of manufacturing with its potential for complex, high-performance parts.