Introduction
Inconel 625 powder is a highly sought-after material in various industries due to its exceptional properties and versatile applications. This article delves into the world of Inconel 625 powder, exploring its characteristics, manufacturing process, advantages, applications, and limitations. Whether you are involved in aerospace, chemical processing, oil and gas, or marine engineering, understanding the benefits and considerations of using Inconel 625 powder can greatly impact your projects’ success.
What is Inconel 625 Powder?
Inconel 625 powder is a nickel-based superalloy renowned for its outstanding resistance to corrosion, high temperatures, and oxidation. It is composed of a precise blend of nickel, chromium, molybdenum, and other alloying elements, resulting in a material with remarkable mechanical and chemical properties. The powder form of Inconel 625 offers unique advantages in manufacturing processes like additive manufacturing (3D printing), where complex geometries and intricate designs can be achieved.
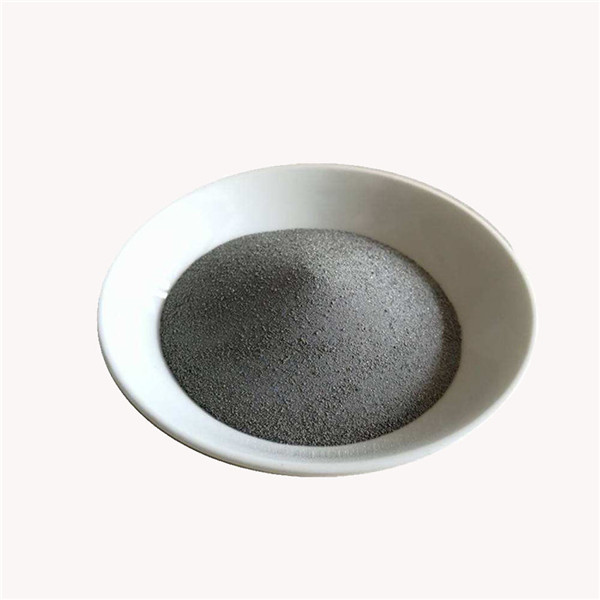
Properties of Inconel 625 Powder
Corrosion Resistance
One of the most notable characteristics of Inconel 625 powder is its exceptional resistance to corrosion. It exhibits superb performance in various corrosive environments, including seawater, acids, and alkalis. This property makes it a popular choice for applications involving exposure to harsh chemicals or corrosive substances.
High Temperature Strength
Inconel 625 powder maintains its strength and integrity even at elevated temperatures. It can withstand extreme heat conditions without significant deformation or loss of mechanical properties. This attribute is crucial in industries such as aerospace, where components must endure extreme temperatures during operation.
Oxidation Resistance
The alloying elements in Inconel 625 powder contribute to its remarkable oxidation resistance. This property enables the material to resist oxidation and scaling, even at high temperatures. As a result, it is commonly employed in environments where oxidation poses a significant risk, such as gas turbines and heat exchangers.
Applications of Inconel 625 Powder
Aerospace Industry
Inconel 625 powder finds extensive utilization in the aerospace industry, particularly in the manufacturing of aircraft engine components. Its excellent high temperature and corrosion resistance properties make it suitable for turbine blades, combustors, and exhaust systems. The powder form facilitates the production of intricate and lightweight components with reduced lead times.
Chemical Processing
In chemical processing plants, Inconel 625 powder is highly valued for its resistance to a wide range of corrosive chemicals. It is used in equipment such as reactors, valves, and pipes, where exposure to aggressive substances is common. The material’s reliability and longevity contribute to enhanced safety and reduced maintenance costs.
Oil and Gas Industry
The oil and gas industry extensively employs Inconel 625 powder due to its ability to withstand harsh offshore and onshore environments. It is utilized in equipment such as downhole components, wellhead valves, and piping systems. The material’s resistance to chloride-induced stress corrosion cracking and pitting make it an ideal choice for these applications.
Marine Engineering
Inconel 625 powder is well-suited for marine engineering applications due to its excellent resistance to seawater corrosion and biofouling. It is utilized in components such as propellers, shafts, and valves. The material’s high strength and durability ensure reliable performance in challenging marine conditions.
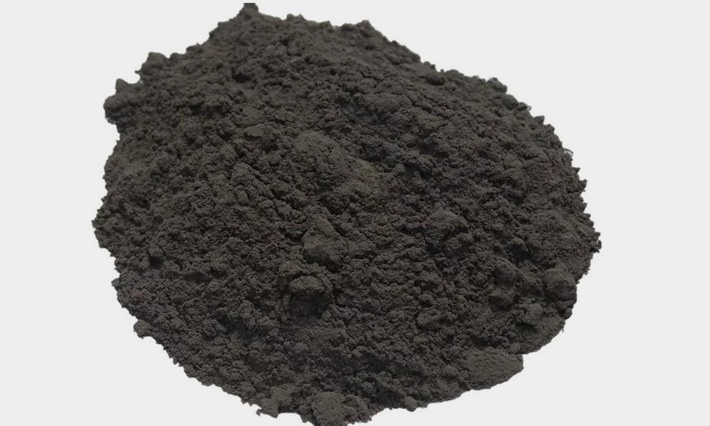
Manufacturing Process of Inconel 625 Powder
The manufacturing process of Inconel 625 powder typically involves atomization, where molten Inconel 625 alloy is rapidly cooled to form fine powder particles. This atomized powder can then undergo further processing techniques such as sieving, blending, and compacting to achieve the desired particle size distribution and enhance flowability. The resulting powder is then ready for use in various manufacturing methods, including additive manufacturing, powder metallurgy, and thermal spray coatings.
Advantages of Using Inconel 625 Powder
Superior Strength and Durability
Inconel 625 powder offers exceptional strength and durability, allowing it to withstand demanding operating conditions. Its high tensile strength and resistance to fatigue make it suitable for critical applications where reliability is paramount.
Versatility
The versatility of Inconel 625 powder lies in its ability to be processed using different manufacturing techniques. Whether it is 3D printing, powder metallurgy, or thermal spraying, this material adapts well to various production methods, enabling the creation of complex and customized components.
Cost-Effectiveness
While the initial cost of Inconel 625 powder may be higher compared to other materials, its long-term cost-effectiveness becomes evident. The material’s excellent corrosion and oxidation resistance minimize maintenance requirements and prolong the service life of equipment, ultimately reducing operational costs.
Challenges and Limitations
Although Inconel 625 powder boasts numerous advantages, there are some challenges and limitations to consider. The high hardness of the material can pose difficulties during machining operations, requiring appropriate tooling and techniques. Additionally, the cost of Inconel 625 powder can be a limiting factor for certain applications with budget constraints. It is essential to evaluate these factors when considering the use of Inconel 625 powder in specific projects.

Conclusion
Inconel 625 powder is a remarkable material with superior corrosion resistance, high temperature strength, and oxidation resistance. Its versatility and excellent mechanical properties make it highly sought-after in industries such as aerospace, chemical processing, oil and gas, and marine engineering. By understanding the properties, applications, manufacturing process, and advantages of Inconel 625 powder, engineers and designers can make informed decisions for their projects, achieving enhanced performance and reliability.
FAQs
Is Inconel 625 powder suitable for high-temperature applications? Yes, Inconel 625 powder exhibits excellent high-temperature strength and can withstand extreme heat conditions without significant deformation or loss of mechanical properties.
What industries commonly use Inconel 625 powder? Inconel 625 powder finds applications in industries such as aerospace, chemical processing, oil and gas, and marine engineering.
Can Inconel 625 powder resist corrosion? Yes, Inconel 625 powder is highly resistant to corrosion, making it suitable for applications in corrosive environments such as seawater and acidic substances.
What is the manufacturing process of Inconel 625 powder? Inconel 625 powder is typically manufactured through atomization, where molten Inconel 625 alloy is rapidly cooled to form fine powder particles.
What are the challenges associated with using Inconel 625 powder? Challenges of using Inconel 625 powder include difficulties during machining due to its high hardness and the higher cost compared to other materials.