High-entropy alloys (HEAs) have taken the scientific world by storm. Imagine a material concocted by throwing not just a couple, but a whole cocktail of different elements together in just the right proportions. The result? A new breed of metallic marvels boasting exceptional properties like high strength, excellent wear resistance, and impressive resistance to scorching temperatures. But how do we get these wonder materials into a usable form? Buckle up, because we’re diving deep into the world of HEA powder preparation!
The Powder Playbook: Unveiling Various Techniques
Just like baking a delicious cake requires the right ingredients and methods, crafting HEA powders involves a strategic selection of techniques. Here, we’ll explore the most prominent contenders in the HEA powder preparation arena:
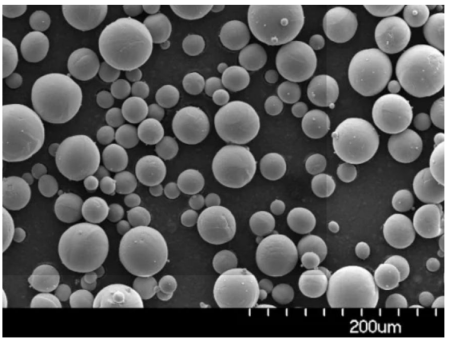
High-Entropy Alloy (HEA) Powder Mechanical Alloying Method
Imagine a high-energy mosh pit for metal elements. That’s essentially the essence of mechanical alloying. In this method, elemental powders are tossed together in a high-energy ball mill, a chamber filled with grinding balls. The relentless collisions and friction between the balls and the powder particles lead to a breakdown and re-welding phenomenon. Over time, this intense mixing fosters the intimate blending of the elements on an atomic level, eventually resulting in HEA powder.
Advantages:
- Versatility: This method can handle a wide range of elemental combinations.
- Scalability: Mechanical alloying can be readily scaled up for larger production volumes.
- Cost-Effectiveness: Compared to other techniques, mechanical alloying can be a more economical option.
Disadvantages:
- Contamination Risk: The grinding media can introduce impurities into the final powder.
- Particle Size Limitations: Achieving very fine powder sizes might be challenging.
- Process Control Complexity: Optimizing the milling parameters for specific HEA compositions can be intricate.
Imagine this: Picture a vigorous dance where metal elements are constantly bumping and fusing together. That’s the essence of mechanical alloying, gradually forging a new material with remarkable properties.
Gas/Water Atomization Method
This technique takes a molten HEA ingot, created by melting the elemental mixture, and transforms it into a fine powder using the power of either gas or water. In the gas atomization method, the molten metal is forced through a high-pressure nozzle, breaking it into tiny droplets that solidify rapidly in a stream of inert gas. Water atomization works similarly, but with a high-velocity water jet replacing the gas.
Advantages:
- Fine Powder Production: This method excels at producing very fine and spherical HEA powders, ideal for additive manufacturing techniques like 3D printing.
- Rapid Solidification: The quick cooling rates associated with atomization methods can lead to unique microstructures in the HEA powder, potentially enhancing its properties.
Disadvantages:
- High-Cost Investment: Setting up and operating gas/water atomization equipment requires significant capital expenditure.
- Process Complexity: Precise control over the atomization parameters is crucial for achieving the desired powder characteristics.
Think of it like this: Imagine a fiery waterfall of molten HEA disintegrating into a cloud of microscopic droplets that solidify mid-air. That’s the magic of gas/water atomization, crafting a powder perfect for building intricate 3D structures.
Chemical Reduction Method
This method involves a carefully orchestrated chemical reaction. Here, metallic oxides (compounds containing metal and oxygen) are used as precursors for the desired elements. These oxides are then reduced using suitable reducing agents, like hydrogen gas, to remove the oxygen and liberate the pure metal elements. The resulting metal powders are then blended and subjected to further processing (like mechanical alloying) to achieve the final HEA powder.
Advantages:
- High Purity Potential: This method offers the potential to achieve very high purity HEA powders, as unwanted impurities from the starting materials can be minimized.
- Tailored Elemental Ratios: Precise control over the starting oxide precursors allows for the creation of HEA powders with exact elemental ratios.
Disadvantages:
- Multi-Step Process: Chemical reduction involves multiple steps, making it a more complex and time-consuming approach compared to other methods.
- Cost Considerations: Depending on the specific reducing agents and processing requirements, this method can be expensive.
Envision this: Imagine a chemical ballet where oxygen is meticulously removed from metal oxides, leaving behind the pure elements ready to be combined into a powerful HEA powder.
Carbon Thermal Shock Method
This method utilizes the dramatic effects of rapid temperature changes. A mixture of graphite (carbon) and elemental powders is subjected to a sudden and intense heat pulse, often
exceeding 3000°C. This extreme heat triggers a reaction between the carbon and the metal elements, forming short-lived metal carbides. Following this heat pulse, the mixture is rapidly quenched (cooled) using water. This abrupt quenching shatters the metal carbides, liberating the desired HEA elements in the form of a fine powder.
Advantages:
- Rapid Processing: The carbon thermal shock method boasts very fast processing times, making it an attractive option for high-volume production.
- Non-Equilibrium Phases: The rapid heating and quenching can lead to the formation of non-equilibrium phases in the HEA powder, potentially offering unique properties not achievable with other methods.
Disadvantages:
- Limited Scalability: Scaling up the carbon thermal shock method for large-scale production can be challenging.
- Process Control Challenges: Precise control over the heating and quenching steps is essential for achieving the desired HEA powder characteristics.
Imagine this: Picture a scene of intense heat followed by a shocking quench. That’s the essence of the carbon thermal shock method, a rapid technique for creating HEA powders with potentially unique properties.
Choosing the Right HEA Powder Preparation Method
So, with this arsenal of techniques at your disposal, how do you pick the most suitable one for your HEA needs? It all boils down to a few key factors:
- Desired Powder Properties: Are you aiming for very fine powders for 3D printing (gas/water atomization) or a more economical option (mechanical alloying)?
- Material Composition: Certain methods might be better suited for specific HEA compositions due to factors like reactivity or processing limitations.
- Production Scale: If you require large quantities of HEA powder, scalability becomes a crucial consideration (mechanical alloying vs. gas/water atomization).
- Cost Constraints: Balancing the desired powder properties with budget limitations is essential.
The Final Frontier: A Glimpse into the Future of HEA Powder Preparation
The world of HEA powder preparation is constantly evolving. Researchers are exploring novel techniques like:
- Electrochemical methods: These methods utilize electricity to drive the reduction of metal oxides and subsequent formation of HEA powders.
- Laser melting techniques: High-powered lasers can be used to melt and rapidly solidify HEA mixtures, potentially creating unique powder morphologies (shapes).
As these techniques mature, they offer exciting possibilities for even more tailored and high-performance HEA powders, pushing the boundaries of what’s possible with this revolutionary class of materials.
FAQs
Question | Answer |
---|---|
Q: What are the typical sizes of HEA powders? | A: HEA powder sizes can vary significantly depending on the chosen preparation method. Gas/water atomization techniques often produce very fine powders, typically less than 50 microns in diameter. These powders are ideal for applications like 3D printing due to their excellent flowability and packing characteristics. Conversely, mechanical alloying might result in coarser powders, ranging up to several hundred microns. These coarser powders might be more suitable for applications where precise powder size isn’t as critical. |
Q: Can HEA powders be directly used in 3D printing? | A: Absolutely! HEA powders produced using gas/water atomization are particularly well-suited for 3D printing techniques like laser sintering or electron beam melting. This is because the gas/water atomization process yields fine and spherical HEA powders, which offer excellent flowability and packing density, essential properties for successful 3D printing. |
Q: Are there any safety considerations when handling HEA powders? | A: Yes, handling HEA powders requires following proper safety protocols similar to any metal powder. These powders can pose inhalation hazards. It’s crucial to wear appropriate personal protective equipment (PPE) like respirators whenever handling HEA powders. Additionally, working in well-ventilated areas is essential to minimize dust exposure. |
Q: Which HEA powder preparation method is the cheapest? | A: Generally, mechanical alloying is considered the most cost-effective method for HEA powder preparation. However, the cost can vary depending on factors like the specific HEA composition, required powder quantity, and processing parameters. |
Q: Which HEA powder preparation method offers the fastest processing times? | A: The carbon thermal shock method boasts the fastest processing times among the techniques discussed. This makes it an attractive option for high-volume production scenarios. However, achieving the desired HEA powder characteristics with this method can be challenging due to the need for precise control over the rapid heating and quenching steps. |
Q: Can I use a combination of HEA powder preparation methods? | A: In some cases, a combination of methods might be employed to achieve the desired HEA powder characteristics. For instance, mechanical alloying could be used initially to achieve a good elemental blend, followed by gas/water atomization to obtain the final, fine powder suitable for 3D printing. |
Q: How do I choose the right HEA powder preparation method for my needs? | A: Selecting the optimal HEA powder preparation method depends on several factors. Consider the desired powder properties (size, morphology), the specific HEA composition, the required production scale, and budgetary constraints. Consulting with experts in the field of HEA powder preparation can be highly beneficial in making an informed decision. |