Introduction
Molybdenum alloys powders are a group of materials that have gained significant attention in various industries due to their exceptional properties and versatile applications. These alloys, when processed into powder form, open up a world of possibilities across aerospace, medical, and manufacturing sectors. In this article, we’ll delve into the world of molybdenum alloy powders, exploring their types, properties, production methods, applications, and future prospects.
What are molybdenum alloys powder?
Molybdenum alloys powders are composite materials that combine molybdenum, a refractory metal known for its high melting point and exceptional strength, with other elements to enhance specific properties. These alloys are carefully engineered to achieve a balance between strength, thermal resistance, and other desired characteristics, making them highly suitable for demanding applications.
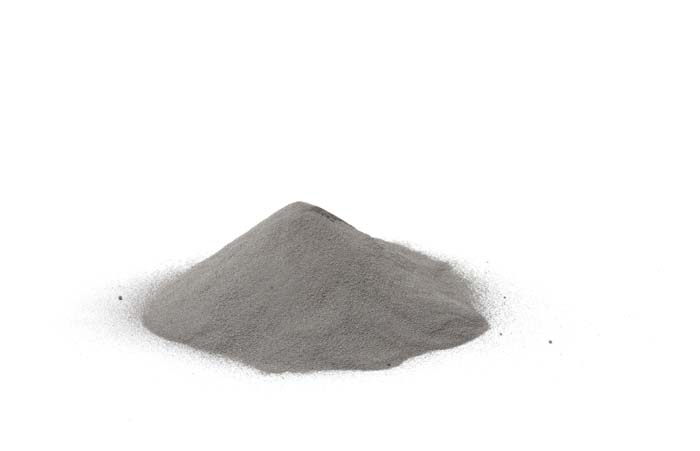
Types of Molybdenum Alloys
Molybdenum-Tungsten Alloys
One of the prominent types of molybdenum alloys is molybdenum-tungsten. This alloy’s addition of tungsten enhances its high-temperature strength and stability, making it indispensable in industries that operate under extreme thermal conditions.
Molybdenum-Chromium Alloys
Molybdenum-chromium alloys exhibit remarkable corrosion resistance, particularly in aggressive environments involving acids and alkalis. These alloys find their place in chemical processing and marine applications.
Molybdenum-Nickel Alloys
Molybdenum-nickel alloys offer a unique combination of properties, including improved ductility and fracture toughness. These alloys are utilized in aerospace and electronics industries where these attributes are essential.
Properties and Benefits of Molybdenum Alloys
High-Temperature Strength
One of the standout features of molybdenum alloys is their ability to retain strength at high temperatures. This property makes them valuable in aerospace propulsion systems and power generation technologies.
Corrosion Resistance
Molybdenum alloys’ corrosion resistance is a significant advantage, especially in aggressive chemical environments. This property expands their usefulness in chemical processing and oil refining.
Electrical and Thermal Conductivity
In addition to their mechanical properties, certain molybdenum alloys exhibit excellent electrical and thermal conductivity, making them suitable for electronic components and heat sinks.
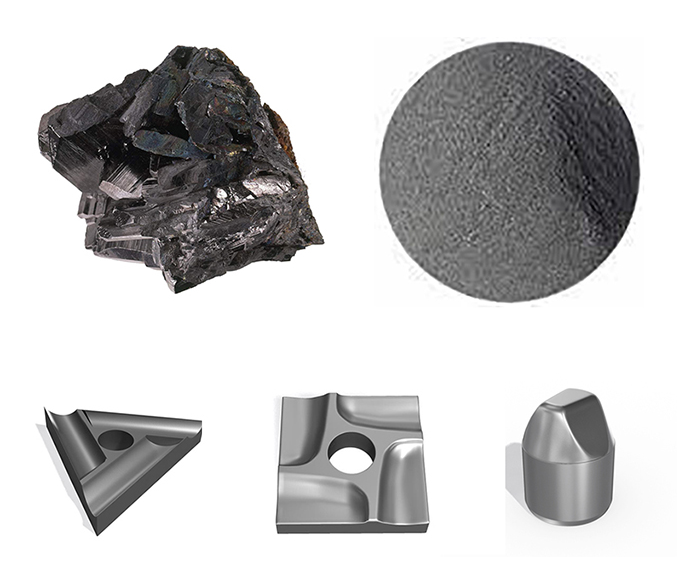
Applications of Molybdenum Alloy Powders
Aerospace Industry
Molybdenum alloy powders play a pivotal role in aerospace applications, where their combination of high-temperature strength and lightweight properties contributes to engine components and structural parts.
Medical Devices
The medical field benefits from molybdenum alloy powders for manufacturing implants and instruments due to their biocompatibility and corrosion resistance.
Manufacturing and Industrial Processes
In manufacturing, molybdenum alloy powders find use in additive manufacturing (3D printing) and metal injection molding, producing intricate and durable components.
Production and Processing of Molybdenum Alloy Powders
Mechanical Alloying
Mechanical alloying involves the blending and milling of molybdenum and other alloying elements to create uniform powder particles with desired properties.
Hydriding-Dehydriding Process
The hydriding-dehydriding process leverages hydrogen to produce molybdenum alloy powders with controlled particle size and morphology.
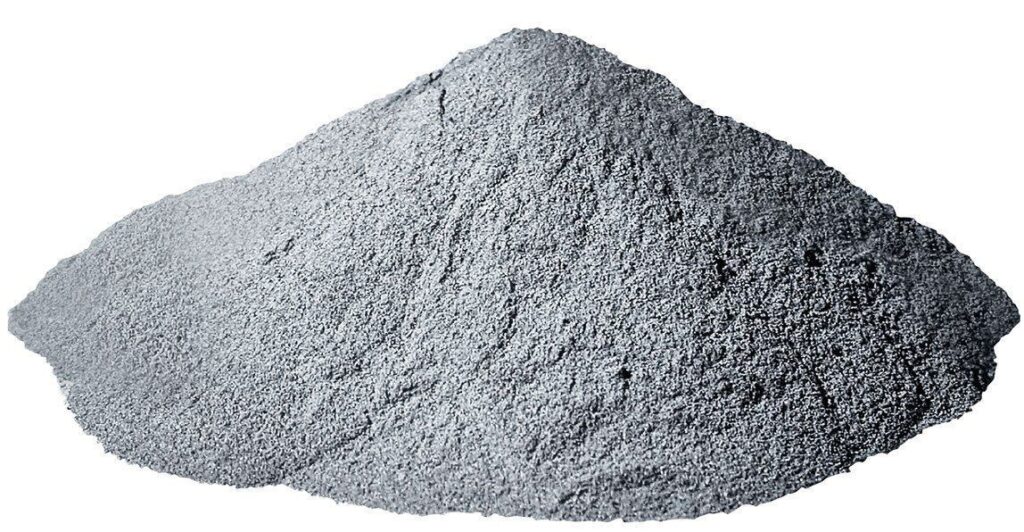
Factors Influencing the Quality of Molybdenum Alloy Powders
Particle Size Distribution
The particle size distribution of molybdenum alloy powders greatly affects their usability in different applications, necessitating precise control during production.
Purity and Impurity Control
Maintaining high purity levels while controlling impurities is critical for ensuring the desired mechanical and chemical properties of molybdenum alloy powders.
Challenges and Future Trends
Recycling and Sustainability
Efforts towards recycling molybdenum alloys and reducing the environmental impact of their production are becoming increasingly important in a sustainable future.
Advancements in Alloy Design
Continued research in alloy design and processing techniques holds the potential for creating innovative molybdenum alloys tailored to specific applications.
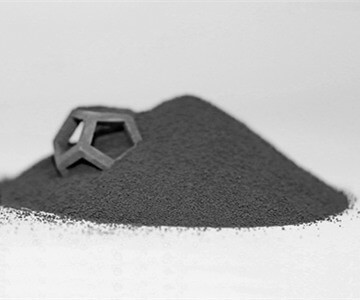
Conclusion
Molybdenum alloy powders stand as a testament to the remarkable synergy between materials science and engineering. Their exceptional properties and adaptability have secured their place in critical industries, offering solutions to challenges in aerospace, medicine, and manufacturing. As we explore new frontiers of material design, these alloys are poised to play an ever more significant role in shaping our technological landscape.
FA Qs
1. What makes molybdenum alloys unique in the realm of materials?
Molybdenum alloys stand out due to their exceptional high-temperature strength, corrosion resistance, and electrical conductivity, making them ideal for diverse applications.
2. How are molybdenum-tungsten alloys different from molybdenum-chromium alloys?
Molybdenum-tungsten alloys excel in high-temperature environments, while molybdenum-chromium alloys are prized for their corrosion resistance in harsh chemical settings.
3. What are some cutting-edge applications of molybdenum alloy powders?
Molybdenum alloy powders are being used in cutting-edge fields like additive manufacturing, where intricate parts are created layer by layer, and in advanced medical implants.
4. What role does particle size play in molybdenum alloy powders’ performance?
Particle size greatly influences the behavior of molybdenum alloy powders. Smaller particles offer improved sintering properties, enhanced surface area, and better mixing capabilities, making them suitable for various processing techniques.
5. How can molybdenum alloys contribute to sustainable practices?
Molybdenum alloys can contribute to sustainability through efficient recycling practices and reduced environmental impact in production. Their durability and resistance to degradation make them suitable for long-lasting applications, minimizing the need for frequent replacements.