Introduction to Metal Powder Atomisation
Metal Powder Atomisation is a cutting-edge process that transforms molten metal into finely divided spherical powders. Since its inception, the technique has witnessed numerous advancements, aligning with the evolving needs of industries.
Types of Metal Powder Atomisation
The world of atomisation isn’t a one-size-fits-all. Depending on the requirements, different types of atomisation techniques come into play.
- Water Atomisation: This process involves the use of high-pressure water jets to break molten metal into tiny droplets.
- Gas Atomisation: Probably the most widespread, here, inert gases like argon or nitrogen are used to disintegrate the molten metal.
- Centrifugal Atomisation: A high-speed rotating disk or other shapes help in producing fine metal powders.
Process of Atomisation
Imagine melting chocolate and turning it into sprinkles. Sounds fun, right? Similarly, atomisation of metal involves three main steps:
- Melting the Metal: It’s all about turning a solid metal into its molten form.
- Generating Fine Droplets: Using one of the techniques mentioned above, the molten metal is fragmented.
- Solidifying Droplets: These droplets cool down and solidify to become metal powders.
Advantages of Metal Powder Atomisation
- Uniform Particle Size: One of the standout benefits! The powders produced have a consistent size, enhancing their usability.
- Purity of Metal Powders: With minimal contamination, industries get a pure, high-quality product.
- Wide Range of Applications: From healthcare to aerospace, these powders are everywhere!
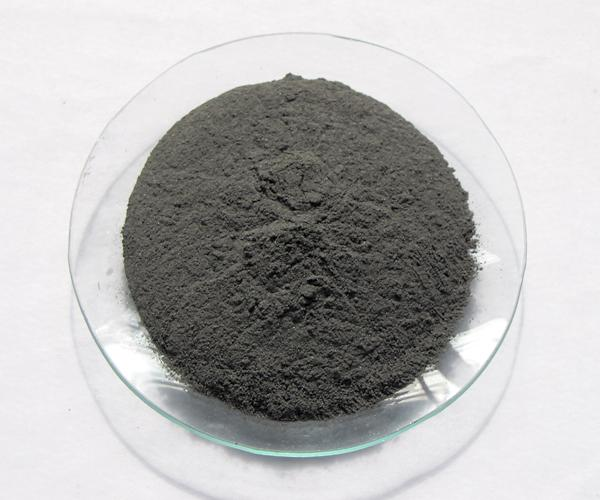
Applications of Metal Powders Produced by Atomisation
- Additive Manufacturing (3D Printing): One of the most significant applications of atomized metal powders is in additive manufacturing, or 3D printing. These powders are used as feedstock for metal 3D printers to create complex and customized parts with high precision and desired mechanical properties.
- Powder Metallurgy: Atomized metal powders are a fundamental component of powder metallurgy, where they are used to create sintered parts through processes like pressing and sintering. These parts are used in automotive, aerospace, medical devices, and more.
- Surface Coatings: Atomized metal powders are used to create coatings on various substrates through techniques like thermal spraying. These coatings enhance wear resistance, corrosion resistance, thermal conductivity, and more.
- Metal Injection Molding (MIM): MIM involves mixing atomized metal powders with a polymer binder to create a feedstock that is then molded and sintered to produce complex-shaped metal components with high dimensional accuracy.
- Catalysis: Metal powders are used as catalysts in various chemical reactions due to their high surface area and reactivity. They find applications in the chemical, petrochemical, and environmental industries.
- Electronics: Atomized metal powders are used in the production of electronic components, such as conductive inks for printed electronics, as well as in the manufacturing of capacitors and other electronic devices.
- Medical Devices: Some medical devices, such as orthopedic implants and dental prosthetics, are made from atomized metal powders due to their biocompatibility and ability to be tailored to specific medical needs.
- Aerospace and Automotive Industries: Atomized metal powders are used to produce lightweight and strong components for aerospace and automotive applications, including engine parts, structural components, and lightweight panels.
- Jewelry and Art: Atomized metal powders are used by artists and jewelers to create intricate designs and sculptures due to their malleability and ability to be fused together through techniques like welding and brazing.
- Energy Storage and Conversion: Metal powders are used in the production of batteries, fuel cells, and other energy storage and conversion devices due to their electrical conductivity and catalytic properties.
- Magnets and Magnetic Materials: Atomized metal powders are used in the production of magnetic materials, including permanent magnets used in various applications such as electronics and transportation.
- Abrasives and Cutting Tools: Atomized metal powders are used in the manufacturing of abrasives and cutting tools, providing enhanced wear resistance and cutting performance.
Current Trends and Innovations in Atomisation
With technology leaping forward, the atomisation process isn’t far behind.
- Advanced Atomisation Techniques: Scientists are experimenting with newer methods for better efficiency.
- Integration with Modern Technology: IoT and AI are making the process smarter and more automated.
Challenges and Limitations
Like all processes, atomisation has its own set of hurdles.
- Process Limitations: Some metals might not be suitable for all atomisation techniques.
- Economic Factors: The cost can sometimes be a barrier for smaller industries.
Environmental Impacts
Being environmentally friendly is the need of the hour. And guess what? Atomisation is stepping up!
- Waste Management: Innovative ways to recycle and reuse by-products.
- Sustainable Practices: Using resources judiciously to minimize wastage.
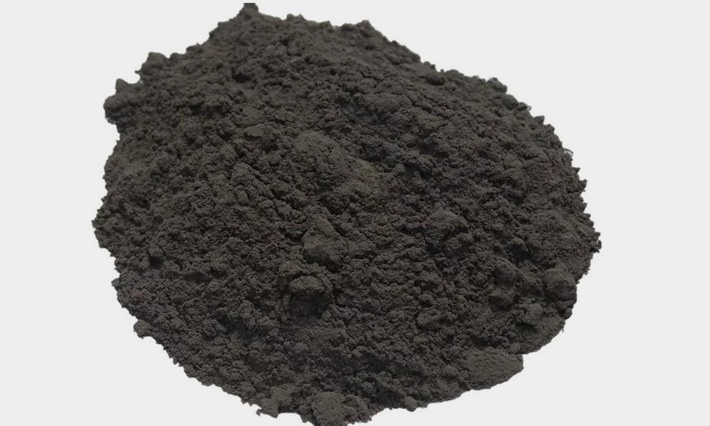
Future of Metal Powder Atomisation
- Advanced Materials: Researchers might focus on atomizing novel alloy compositions and exotic materials that offer enhanced mechanical properties, corrosion resistance, or thermal conductivity. These materials could find applications in aerospace, automotive, medical, and energy industries.
- Nanoparticle Production: Atomization techniques could be refined to produce metal nanoparticles with controlled sizes and shapes. These nanoparticles have unique properties and can find applications in areas like catalysis, electronics, and biomedicine.
- Customized Particle Sizes: The ability to control and customize the size distribution of metal powder particles could become more precise. This would allow manufacturers to tailor materials for specific additive manufacturing processes, resulting in improved part quality and efficiency.
- Improved Powder Flowability: Powder flowability is crucial for consistent and reliable additive manufacturing. Future atomization processes could produce powders with optimized flow characteristics, reducing the need for post-processing steps.
- Reduced Oxygen and Contaminant Levels: Contaminants like oxygen can affect the properties of metal powders. Advanced atomization methods could result in powders with lower levels of impurities, leading to higher-quality end products.
- Hybrid Atomization Techniques: Combining different atomization methods could lead to powders with enhanced properties. For instance, hybrid methods that incorporate both gas and water atomization might allow for better control over particle morphology and size distribution.
- In-Situ Alloying: Atomization could be used to create custom alloy powders in real-time by mixing different molten metals during the atomization process. This could enable rapid material development and prototyping.
- Energy Efficiency: Future advancements might focus on making atomization processes more energy-efficient by optimizing the use of gases, reducing heat losses, and recycling energy within the system.
- AI and Data-Driven Optimization: Artificial intelligence and data analytics could be employed to optimize atomization processes, predict powder properties, and adjust process parameters in real time for improved efficiency and powder quality.
- Sustainability: Future developments could also focus on making atomization processes more environmentally friendly by reducing waste generation, optimizing resource usage, and exploring alternative cooling mediums.
Conclusion
Metal Powder Atomisation has revolutionized the way industries function, offering them unparalleled quality and efficiency. As technology and research advance, the atomisation process promises even more exciting developments in the future.
FAQs
- What metals can be atomised?
- Almost all metals, including titanium, copper, steel, and alloys, can be atomised.
- How does atomisation contribute to sustainability?
- By reducing wastage and promoting recycling of by-products.
- Is the atomised powder ready to use immediately after production?
- Generally, yes. However, it might need some post-processing depending on the application.
- Why is particle size uniformity so crucial?
- It ensures consistent behavior during subsequent processes like sintering or melting.
- Can atomisation replace traditional metal production methods?
- Not entirely. While it’s a powerful method, traditional methods still have their unique benefits.