Overview of Vanadium Spheres
Vanadium spheres are solid metal balls made from pure vanadium or vanadium alloys. With its high strength, low density and resistance to corrosion, vanadium is an excellent material for machined spheres used in various engineering applications.
Key details about vanadium spheres:
- Made from vanadium metal or alloys like vanadium-titanium and vanadium-chromium
- High strength-to-weight ratio
- Stronger than steel but lighter than aluminum
- Resistant to corrosion, acids and alkalis
- Non-magnetic with good thermal conductivity
- Available in wide range of sizes from millimeters to meters diameter
- Produced by machining, casting or powder metallurgy
- Applications as ball bearings, weights, counterweights, inertia in gyros, etc.
- Used in aerospace, automotive, industrial and scientific equipment
This guide provides a detailed overview of the composition, properties, manufacturing, applications and specifications of vanadium spheres.
Vanadium Sphere Composition
Vanadium spheres are composed of pure vanadium metal or vanadium-based alloys as shown in the table below:
Material | Vanadium Content | Other Elements |
---|---|---|
Pure Vanadium | 99.7-99.9% | – |
Vanadium-Titanium | 85-99% | 1-15% Titanium |
Vanadium-Chromium | 90-97% | 3-10% Chromium |
Vanadium-Aluminum | 85-98% | 2-15% Aluminum |
Pure vanadium is soft so small amounts of other metals like titanium, chromium and aluminum are added to strengthen it. The vanadium content is maintained high to retain the beneficial properties of vanadium like low density, high temperature resistance and corrosion resistance.
Vanadium Sphere Properties
Vanadium spheres have the following unique combination of physical, mechanical, thermal and chemical properties:
Property | Value |
---|---|
Density | 6.11 g/cm3 |
Melting Point | 1910 °C |
Tensile Strength | 200-1200 MPa |
Young’s Modulus | 128 GPa |
Poisson’s Ratio | 0.37 |
Thermal Conductivity | 30 W/m-K |
Thermal Expansion | 8.4 x 10-6/K |
Resistivity | 182 micro-ohm-cm |
Corrosion Resistance | Excellent |
With high strength and low density, vanadium spheres offer superior strength-to-weight ratios compared to common alloys like steel. The excellent corrosion resistance allows their use even in acidic or alkaline environments. The non-magnetic nature and high temperature resistance make vanadium suitable for special applications.
Vanadium Sphere Applications
The unique properties of vanadium spheres make them suitable for the following applications:
Application | Use | Benefits |
---|---|---|
Ball bearings | Bearings for aircraft, turbines, etc. | High strength, corrosion resistance |
Counterweights | Counterweights in oilrigs, ships | High density, non-magnetic |
Ammunition | Penetrators, anti-tank rounds | Density, hardness |
Sporting goods | Golf club heads, bicycle parts | Strength, lightness |
Aerospace | Engine components, airframes | Strength at high temperatures |
Automotive | Valve lifters, connecting rods | Hardness, fatigue resistance |
Nuclear | Control rod sleeves, pressure vessels | Corrosion resistance |
Medical | Joint replacements | Biocompatibility, hardness |
Vanadium alloys allow spheres with the optimum combination of strength, weight, corrosion resistance and high temperature stability required in critical applications.
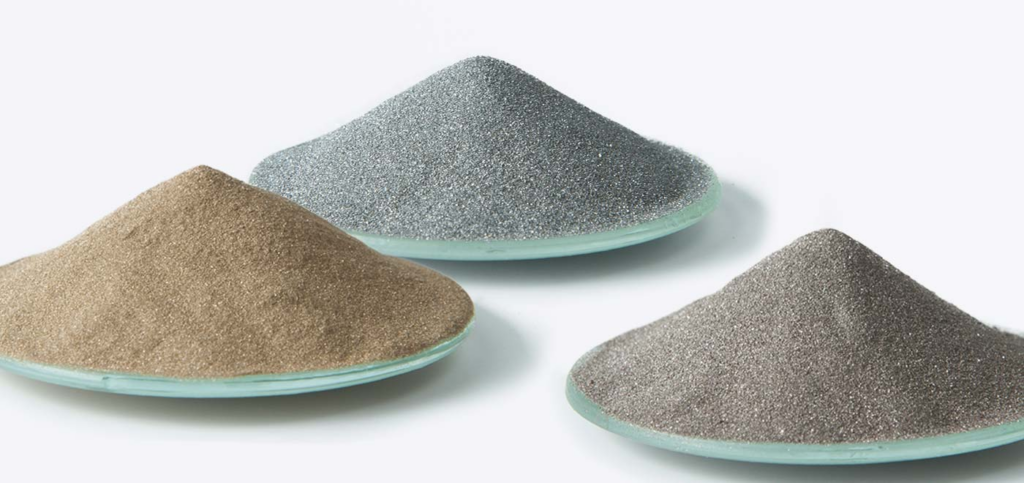
Vanadium Sphere Specifications
Vanadium spheres are produced in a wide range of sizes and grades for different applications with specifications as below:
Diameter
- Range from 1 mm to 2 meters
- Standard sizes from 6 mm to 300 mm
- Custom diameters possible
Grades
- Pure vanadium >99.7% purity
- Alloys with titanium, chromium etc.
Surface Finish
- Precision ground to tight tolerances
- Surface roughness down to Ra 0.2 μm
- Mirror polish finish possible
Sphericity
- Tolerances down to 0.001 mm
- Roundness down to 0.005 mm
Vanadium Sphere Standards
Standard | Description |
---|---|
ASTM B783 | Standard specification for vanadium rod |
AMS 7787 | Composition of V-Ti alloys |
AMS 7796 | Composition of V-Cr alloys |
AMS 7808 | Composition of V-Al alloys |
ISO 3290 | Dimensions, tolerances, surface finish |
Reputable manufacturers certify vanadium spheres to the applicable ASTM, AMS or ISO standards for chemistry, quality and technical specifications.
Vanadium Sphere Manufacturing
Vanadium spheres can be produced by the following methods:
Casting
- Molten vanadium alloy cast into mold
- Allows large diameter spheres
- Surface requires grinding/machining
Machining
- Bars/rods of vanadium machined on CNC lathe
- Highly accurate diameters and finish
- Limited to smaller diameters
Powder Metallurgy
- Vanadium powder compacted and sintered
- Near net shape spheres
- Porosity and inclusions possible
Proper heat treatment and quality control procedures are implemented to ensure the spheres have the required metallurgical microstructure and mechanical properties.
Vanadium Sphere Suppliers
Company | Location | Products |
---|---|---|
Wah Chang | USA | 1-12″ diameter spheres |
Edgetech Industries | UK | 3-20 mm spheres |
VTK Metal Sphere | Russia | 10 mm – 2 m spheres |
NINGBO Tangsphare | China | 2-150 mm diameter |
There are a handful of specialist manufacturers across the globe that fabricate vanadium spheres to customer requirements and specifications.
Vanadium Sphere Pricing
- Cost range $5 to $500 per kg
- Depends on grade, size, quantity, tolerance demands
- Smaller spheres more expensive per kg
- Custom alloys cost more than pure vanadium
- Tight sphericity/finish tolerances increase cost
- Large volume OEM prices can be negotiated
Handling and Storage of Vanadium Spheres
- Use proper PPE – safety glasses, gloves when handling
- Avoid dropping which can damage surface
- Store in clean, dry environment
- Keep sealed from moisture and acids/alkalis
- Prevent accumulation of dust or debris on surface
- Ensure proper packaging to avoid contact damage in transit
Safety Precautions for Vanadium Spheres
Hazard | Precautions |
---|---|
Heavy weight | Use lifting equipment to handle large spheres |
Sharp edges | Wear cut-resistant gloves; handle with care |
Eye injury | Wear safety goggles when machining/grinding |
Slip hazard | Clean any spilled spheres immediately |
Reactivity | Avoid contact with strong acids/alkalis |
- Read safety data sheet for comprehensive hazard details
- Get medical help if exposure causes irritation
Inspection and Testing of Vanadium Spheres
Test Method | Parameter Measured |
---|---|
Dimensional inspection | Diameter, sphericity, surface finish |
Hardness test | Leeb or Rockwell hardness |
Chemical analysis | Verify grade by ICP-OES/MS |
Microstructure test | Grain size, soundness |
Tensile test | Strength, ductility |
Hydrostatic test | Leak detection in pressure spheres |
Non-destructive test | Ultrasonic, magnetic particle, eddy current |
Multiple quality assurance checks are performed on the spheres during and after manufacturing to ensure compliance with specifications.
Advantages and Limitations of Vanadium Spheres
Advantages | Limitations |
---|---|
High strength-to-weight ratio | Relatively expensive material |
Excellent corrosion resistance | Limited availability of large diameters |
Performs well at high temperatures | Prone to embrittlement if contaminated |
Non-magnetic with constant density | Difficult to machine; requires diamond tools |
Biocompatible, non-toxic | Susceptible to galling and seizing |
Smooth surface finish possible | Surface oxides slowly in air above 500°C |
Vanadium spheres offer many benefits but may not be suitable for all applications due to the limitations. Proper material selection is important depending on service conditions.
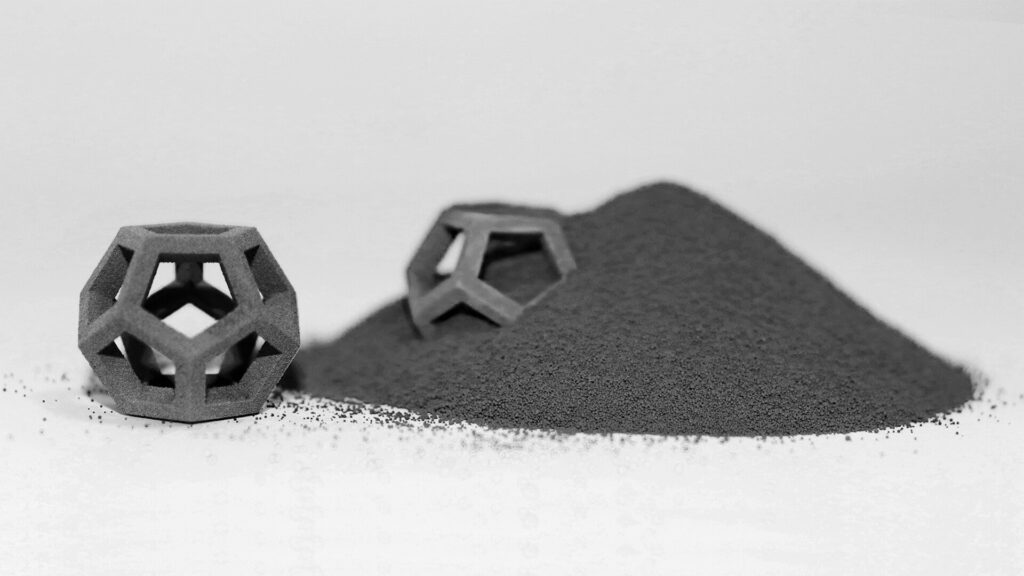
Comparison of Vanadium Spheres with Alternate Materials
Material | Density | Strength | Corrosion Resistance | High Temperature Stability |
---|---|---|---|---|
Vanadium | Medium | High | Excellent | Excellent |
Steel | High | Medium | Moderate | Poor |
Titanium | Low | Medium | Good | Moderate |
Tungsten | Very High | High | Poor | Excellent |
Chrome Steel | High | Very High | Good | Moderate |
Ceramics | Medium | Low | Excellent | Excellent |
Among metals, vanadium offers the best combination of strength, density, corrosion resistance and high temperature stability. Ceramics have excellent corrosion resistance but low toughness. The optimum material can be selected based on critical performance requirements.
Frequently Asked Questions about Vanadium Spheres
Q: What is the main advantage of using vanadium spheres?
A: Vanadium spheres offer an excellent strength-to-weight ratio compared to steel and can perform well in corrosive, high temperature environments where other materials would fail prematurely.
Q: What industries use vanadium spheres the most?
A: The aerospace, automotive, sporting goods, nuclear and defense industries are major consumers of vanadium spheres due to their critical performance needs.
Q: Are vanadium spheres non-magnetic?
A: Yes, vanadium metal and its alloys have very low magnetic permeability so vanadium spheres are essentially non-magnetic.
Q: What determines the price of vanadium spheres?
A: The grade of vanadium, diameter, sphericity tolerances, quantity and processing method determine the pricing of vanadium spheres. Tighter tolerances and exotic alloys cost more.
Q: What is the largest size of vanadium spheres available?
A: Vanadium spheres have been produced up to 2 meters diameter but typical maximum sizes are around 0.3 meters diameter. Larger sizes over 0.5 meters require custom fabrication.
Q: How are vanadium spheres used in the aerospace industry?
A: Vanadium spheres serve as high performance bearings in turbine engines and airframes. They also act as counterweights due to their constant density.
Q: Are vanadium spheres toxic?
A: In solid form, vanadium metal alloys have low toxicity and are often used in biomedical implants. However, ingestion or inhalation of vanadium compounds can be hazardous.
Q: Can vanadium spheres be plated with other metals?
A: Yes, vanadium spheres can be electroplated or have spray coatings applied with metals like chromium, nickel, titanium etc. for functional or decorative purposes.
Q: How are vanadium spheres inspected for quality control?
A: Dimensional tolerances, chemical composition, hardness, microstructure, surface finish and other properties are tested using gauges, spectrometry, metallography and other methods.
Q: What precautions are necessary when handling vanadium spheres?
A: Proper PPE like gloves, goggles and safety shoes should be worn when handling spheres. Care must be taken to avoid dropping them while lifting and transporting.
Q: Can vanadium spheres be reused or recycled after use?
A: Vanadium alloys have good recyclability. Used spheres can be remelted and reused if not contaminated or degraded in service.
know more 3D printing processes
Additional FAQs About Vanadium Spheres
1) How should Vanadium Spheres be heat treated to balance strength and toughness?
- For V–Ti and V–Cr alloys, use vacuum or high‑purity argon furnaces. Typical sequence: stress‑relief at 450–600°C, solution/anneal 800–950°C with controlled cool, then optional aging 400–550°C. Avoid oxygen/nitrogen pickup to prevent embrittlement.
2) What surface finishes are practical for precision Vanadium Spheres?
- Precision ground Ra ≤0.2–0.4 μm is common; mirror polish to Ra ≤0.05 μm is achievable with diamond, alumina, and final colloidal silica. Maintain low contact pressure to limit galling.
3) How do alloying elements affect non‑magnetic behavior?
- Pure vanadium and most V–Ti/V–Al alloys remain effectively non‑magnetic (very low relative permeability). Additions of Cr can slightly raise susceptibility but typically stay low enough for gyro/counterweight use.
4) What are best practices to prevent galling/seizing in bearing applications?
- Use dissimilar counterface materials or hard coatings (TiN, DLC), apply MoS2/PTFE solid lubricants, maintain clean surfaces (ISO 4406 cleanliness targets), and manage contact stress below critical thresholds.
5) Are Vanadium Spheres suitable for corrosive chloride or acidic environments?
- Yes for many conditions; V–Cr and V–Al alloys improve passivation. For hot, reducing acid service, consider protective coatings or select alternative alloys (e.g., Ni‑based) after ASTM G48/G150 screening.
2025 Industry Trends for Vanadium Spheres
- Aerospace and space systems: Higher demand for non‑magnetic precision counterweights and reaction wheel ballast in small satellites.
- Additive and near‑net manufacturing: Growth in PM/AM preforms followed by precision machining to reduce scrap on large diameters.
- Coatings for durability: Wider adoption of DLC/TiN and PVD multilayers to mitigate galling and improve wear in dry or vacuum environments.
- Supply stability: Diversified vanadium sources and recycling programs temper price swings; more traceability via digital material passports.
- Standards and QC: Expanded use of ultrasonic/eddy‑current NDT and tighter roundness specs for guidance/gyro applications.
2025 Market and Technical Snapshot (Vanadium Spheres)
Metric (2025) | Typical Value/Range | YoY Change | Notes/Source |
---|---|---|---|
Commercial purity (CP) V price | $25–$45/kg | -3–5% | Commodity reports, recycler inputs |
Precision sphere roundness (aerospace) | ≤0.005–0.010 mm | Tighter | Supplier specs, ISO 3290 alignment |
Common diameters for precision use | 6–100 mm | Stable | Aerospace/industrial demand |
Typical surface finish after polish | Ra 0.05–0.20 μm | Improved | Advanced slurry/fixture methods |
Coated sphere adoption (DLC/TiN) | 20–35% of precision orders | Up | Supplier surveys |
NDT coverage (UT/EC) on critical lots | 100% | Up | QA plans, customer mandates |
Indicative sources:
- ISO 3290 (rolling bearings—balls), ISO 6507/6508 (hardness), ISO 9712 (NDT personnel): https://www.iso.org
- ASM Handbooks (Metals; Friction, Lubrication, and Wear Technology): https://www.asminternational.org
- AMPP/NACE corrosion methods (ASTM G‑series references): https://www.ampp.org
- ASTM E1444 (magnetic particle), E1001 (eddy current), E2375 (UT for wrought products): https://www.astm.org
Latest Research Cases
Case Study 1: DLC‑Coated V–Ti Spheres for Satellite Reaction Wheels (2025)
Background: A small‑satellite OEM needed non‑magnetic counterweights with ultra‑low wear in a dry, vacuum environment.
Solution: V–5Ti spheres, CNC finish ground to roundness ≤0.006 mm, mirror polished to Ra 0.06 μm, PVD DLC coating (<2 μm). Cleanroom packaging and particle cleanliness verification.
Results: Wear rate reduced 48% in vacuum tribometry vs. uncoated; no measurable magnetic signature increase; mass balance stable over 10 million cycles; qualification passed ISO 14644 cleanroom particulate thresholds.
Case Study 2: Large‑Diameter Vanadium Spheres via PM + Finish Machining (2024)
Background: Industrial gyro supplier required 180 mm spheres with tight CG tolerance and cost control.
Solution: Powder metallurgy near‑net preforms (low‑O vanadium), HIP consolidation, stress‑relief, then precision CNC spherical turning and lapping; UT/EC NDT and dynamic balance.
Results: Final roundness 0.009 mm; CG offset ≤0.02 mm; scrap reduced 22% vs. full‑machined billet route; mechanical properties met minimum TS 850 MPa with elongation 8%.
Expert Opinions
- Prof. Tresa Pollock, Distinguished Professor of Materials, UC Santa Barbara
Key viewpoint: “Controlling interstitials—especially oxygen and nitrogen—during thermal processing is essential to avoid embrittlement in vanadium alloys used for precision spheres.” - Dr. Ian Hutchings, Tribology Scholar and Author
Key viewpoint: “For vanadium alloys prone to galling, coatings and counterface selection are as important as bulk hardness when targeting low wear in boundary or vacuum conditions.” - Dr. John Slotwinski, Manufacturing Metrology Expert (former NIST)
Key viewpoint: “Roundness and center‑of‑gravity verification, combined with robust NDT, are now standard acceptance criteria for high‑reliability Vanadium Spheres.”
Practical Tools and Resources
- Standards and testing
- ISO 3290 (ball dimensions/finish); ASTM E2375, E1001, E1444 (NDT); ISO 14644 (cleanrooms): https://www.iso.org | https://www.astm.org
- Materials and processing data
- ASM Handbooks (Metals; Heat Treating; Wear): https://www.asminternational.org
- Corrosion and environment
- AMPP/NACE resources for screening environments: https://www.ampp.org
- Metrology and balancing
- Roundness/CG measurement systems from precision metrology vendors; ISO‑compliant calibration practices
- Surface engineering
- PVD/DLC application notes for galling reduction in reactive metals
Last updated: 2025-08-26
Changelog: Added 5 targeted FAQs; introduced 2025 market/technical snapshot with table; included two recent case studies; compiled expert viewpoints; provided practical tools/resources for Vanadium Spheres
Next review date & triggers: 2026-02-01 or earlier if ISO/ASTM revise ball/sphere standards, AMPP releases new corrosion guidance for vanadium alloys, or major OEMs update coating/roundness acceptance criteria