Cobalt-based alloy powders are like the superheroes of the metal world, boasting incredible strength, resilience, and resistance to extreme temperatures. But just like the Avengers have different members with unique skills, various grades of cobalt-based alloy powders exist, each tailored for specific applications. Buckle up, because we’re about to embark on a journey into this fascinating realm of metallic marvels!
Factors to Consider When Selecting Cobalt-Based Alloy Powder
Choosing the right cobalt-based alloy powder is akin to picking the perfect tool for the job. Here are some key factors to consider:
- Application: What will the final product be used for? Is it a jet engine component that needs to withstand scorching temperatures, or a medical implant requiring biocompatibility? Different applications demand specific properties from the powder.
- Chemical Composition: Cobalt is the hero, but it doesn’t work alone. Common alloying elements include chromium, molybdenum, tungsten, and nickel. Each element imparts unique characteristics. Chromium enhances wear resistance, while molybdenum strengthens the material at high temperatures. Understanding the interplay of these elements is crucial.
- Particle Size and Morphology: Imagine building a sandcastle. Finer particles create a smoother, denser structure. Similarly, the size and shape (spherical or irregular) of the powder particles influence the flowability, packing density, and final properties of the finished product.
- Manufacturing Process: Are you using additive manufacturing (3D printing) or thermal spraying? Different processes have varying powder size and flowability requirements.
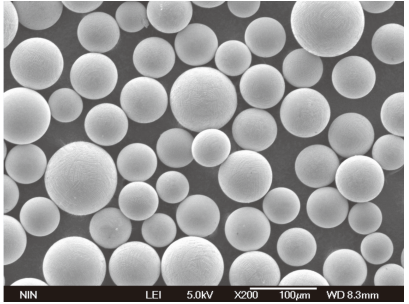
Preparation Methods of Cobalt-Based Alloy Powder
These metallic marvels aren’t born, they’re crafted! Here’s a peek into the two main methods for creating cobalt-based alloy powders:
- Gas Atomization: Picture molten metal being poured through a sieve under a high-pressure gas stream. The metal breaks into tiny droplets that solidify mid-air, forming spherical powder particles. This method yields consistent size and good flowability, making it ideal for additive manufacturing.
- Water Atomization: Similar to gas atomization, but instead of gas, a water jet disrupts the molten metal stream. This process produces a wider range of particle sizes and shapes, often used for thermal spraying applications.
Each method has its pros and cons. Gas atomization offers better control over particle size and morphology, but comes at a higher cost. Water atomization is more economical but yields less uniform particles.
The Applications of Cobalt-Based Alloy Powder
Cobalt-based alloy powders aren’t just sitting on a shelf waiting for admiration. They’re utilized in a diverse range of demanding applications:
- Aerospace: Jet engine components like turbine blades and combustors face extreme heat and pressure. Cobalt-based alloy powders, with their exceptional high-temperature strength and oxidation resistance, are the perfect recipe for these critical parts.
- Medical Implants: Imagine a hip replacement that’s not only strong but also biocompatible with your body. Cobalt-chromium-molybdenum (CoCrMo) alloy powders are a popular choice for such implants, offering a winning combination of strength, corrosion resistance, and biocompatibility.
- Cutting Tools: Need a drill bit that can chew through tough materials? Cobalt-based alloy powders are used to create drill bits, milling cutters, and other cutting tools that boast exceptional wear resistance and long-lasting sharpness.
- Energy Production: Gas turbines used in power generation require components that can withstand high temperatures and corrosive environments. Cobalt-based alloy powders come to the rescue, ensuring efficient and reliable energy production.
These are just a few examples. From dental tools to oil drilling equipment, cobalt-based alloy powders are revolutionizing various industries with their unique blend of properties.
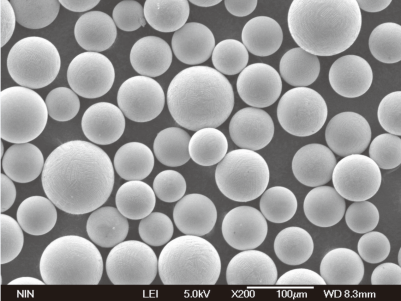
Common Grades of Cobalt-Based Alloy Powder
Now, let’s meet some of the most popular grades of cobalt-based alloy powders, each with its own set of strengths and weaknesses:
- CoCrMo (Cobalt-Chromium-Molybdenum): This is a true all-rounder, offering excellent wear resistance, high-temperature strength, and good corrosion resistance. It’s widely used in aerospace, medical implants, and cutting tools.
- CoCrW (Cobalt-Chromium-Tungsten): This grade prioritizes wear resistance above all else. Its high tungsten content makes it ideal for applications where extreme abrasion is a concern, like mining equipment and wear plates.
- Haynes® Alloys (e.g., Haynes 188, Haynes 25): These proprietary alloys are known for their exceptional high-temperature strength and oxidation resistance. They’re the go-to choice for jet engine components and other applications that experience extreme heat.
- Stellite® Alloys (e.g., Stellite 6B): Champions of wear resistance, Stellite alloys boast a high cobalt content combined with chromium and tungsten. They excel in applications like valves, pump components, and bearings that constantly battle friction and abrasion.
- Invar® Alloy: This unique grade possesses a remarkably low coefficient of thermal expansion. In simpler terms, it barely changes size with temperature fluctuations. This makes Invar® invaluable for precision instruments, electronics components, and applications where dimensional stability is critical.
Choosing Your Cobalt Champion:
Selecting the right grade requires careful consideration of the desired properties. Here’s a breakdown to help you navigate the hero’s gallery:
Grade | Strengths | Weaknesses | Typical Applications |
---|---|---|---|
CoCrMo | All-rounder: good wear resistance, high-temperature strength, corrosion resistance | Not the absolute best in any single category | Aerospace, medical implants, cutting tools |
CoCrW | Exceptional wear resistance | Lower high-temperature strength compared to some grades | Mining equipment, wear plates |
Haynes® Alloys | Unbeatable high-temperature strength and oxidation resistance | Often more expensive than other grades | Jet engine components, applications experiencing extreme heat |
Stellite® Alloys | Unequaled wear resistance | May not be ideal for high-temperature applications requiring maximum strength | Valves, pump components, bearings |
Invar® Alloy | Ultra-low coefficient of thermal expansion | Lower wear resistance and high-temperature strength compared to some grades | Precision instruments, electronics components, applications requiring dimensional stability |
Remember, this is just a glimpse into the diverse world of cobalt-based alloy powders. New grades are constantly being developed to meet the ever-evolving needs of different industries.
Beyond the Basics: A Deeper Dive into Specific Grades
Let’s delve a little deeper into some of the most popular grades:
- CoCrMo: This versatile workhorse comes in various sub-grades with slightly different compositions, tailored for specific applications. For instance, a higher molybdenum content might be preferred for medical implants due to its enhanced biocompatibility.
- Haynes® Alloys: These proprietary alloys are like the secret recipes of the cobalt world. Their exact compositions are closely guarded secrets, but their exceptional performance is no mystery. Haynes 188 is a popular choice for turbine discs in jet engines due to its phenomenal resistance to creep (deformation under stress at high temperatures). Haynes 25 shines in applications involving extreme heat and harsh environments, like parts in chemical processing plants.
- The Future of Cobalt Powders: Researchers are constantly innovating, developing new grades with even better properties. For example, there’s a growing focus on creating cobalt-based alloy powders that are not only strong but also lightweight. This could revolutionize industries like aerospace, where every gram saved translates to improved fuel efficiency. Additionally, biocompatible cobalt-based alloy powders are being explored for a wider range of medical implants, offering patients potentially longer-lasting and more comfortable options.
A Word on Cost: Cobalt-based alloy powders are not created equal, and their price reflects this. Factors like the complexity of the manufacturing process, the specific alloying elements used, and the demand for the grade all influence the cost. Generally, grades with exceptional high-temperature strength or wear resistance tend to be more expensive.
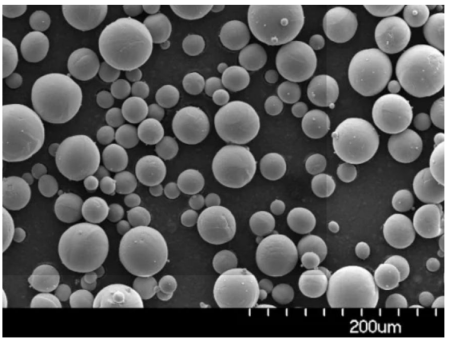
FAQ
Q: What are the advantages of using cobalt-based alloy powders compared to traditional manufacturing methods?
A: Several advantages come into play:
- Complex Geometries: Additive manufacturing using cobalt-based alloy powders allows for the creation of intricate shapes that would be difficult or impossible to produce with traditional techniques like machining.
- Lightweighting: Certain grades of cobalt-based alloy powders offer a good balance of strength and weight, enabling the development of lighter components for applications like aerospace.
- Material Efficiency: Powder-based additive manufacturing minimizes material waste compared to traditional methods that involve cutting away excess material.
Q: Are there any environmental concerns associated with cobalt-based alloy powders?
A: Cobalt mining can have environmental and social impacts. However, the recycling of cobalt scrap and the development of more sustainable mining practices are ongoing areas of focus. Additionally, powder-based additive manufacturing can help reduce waste compared to traditional techniques.
Q: What’s the future outlook for cobalt-based alloy powders?
A: The future looks bright! With continuous advancements in powder production techniques and alloy development, we can expect even more innovative grades with exceptional properties. Additionally, the growing adoption of additive manufacturing will likely drive increased demand for cobalt-based alloy powders.