powder atomization have revolutionized various industries, offering unique properties that traditional manufacturing methods cannot replicate.
Aerospace and Aviation
In the aerospace sector, atomized powders are utilized to produce lightweight yet high-strength components for aircraft and spacecraft. The fine particle size and controlled microstructures contribute to improved mechanical properties, making these powders ideal for critical applications like turbine blades and structural components.
Additive Manufacturing
powder atomization have significantly impacted the field of additive manufacturing, also known as 3D printing. These powders are specifically engineered for various printing processes, allowing the creation of intricate and complex designs with superior material properties. From aerospace to healthcare, additive manufacturing benefits from atomized powders’ ability to produce customized parts with exceptional precision.
Medical Devices
The medical industry benefits from atomized powders in the production of implants and medical devices. Materials such as titanium alloys and biocompatible ceramics are atomized to create powders that can be shaped into implants matching the patient’s anatomy. This process ensures better integration with surrounding tissues and reduces the risk of rejection.
Automotive Industry
Atomized powders find applications in the automotive sector, where they contribute to lightweighting and enhanced fuel efficiency. These powders are used to manufacture parts like pistons, connecting rods, and gears, providing better performance and durability while reducing overall weight.
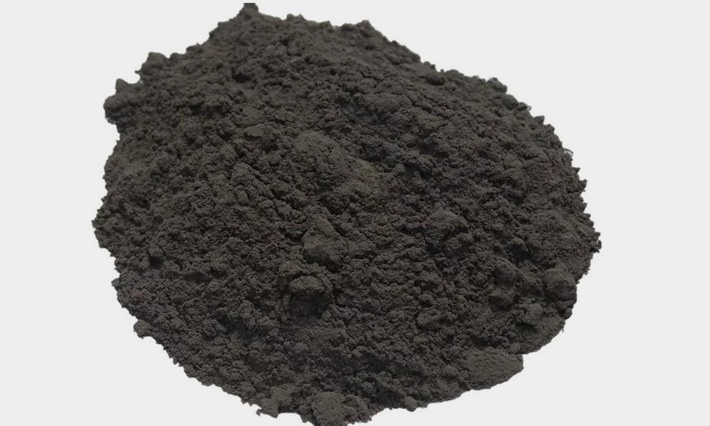
Challenges in Powder Atomization
While powder atomization offers numerous advantages, it also comes with its fair share of challenges that researchers and manufacturers must address.
Contamination Concerns
Contaminants from the environment or the atomization process itself can affect the quality of the powders. Ensuring a clean and controlled environment is crucial to prevent unwanted impurities in the final product.
Particle Size Distribution
Achieving a consistent and desired particle size distribution can be challenging. Variations in particle size can lead to inconsistencies in material properties and performance.
Energy Consumption
Atomization processes often require high-energy inputs, primarily due to the need to melt the material and generate the necessary forces for disintegration. Researchers are actively exploring energy-efficient alternatives to reduce the environmental impact.
Innovations in Atomization Technology
In recent years, significant innovations have emerged in the field of atomization technology, aiming to address challenges and push the boundaries of what’s possible.
Custom Alloy Development
Researchers are working on developing new alloys tailored to specific atomization techniques. These alloys are designed to solidify quickly during atomization, resulting in unique microstructures and improved properties.
Nanostructured Powders
Advancements in atomization technology have enabled the production of nanostructured powders with enhanced properties. These powders find applications in fields like electronics and advanced materials.
Sustainable Atomization Methods
Efforts are being made to develop more environmentally friendly atomization methods. This includes utilizing renewable energy sources and optimizing process parameters to reduce energy consumption.
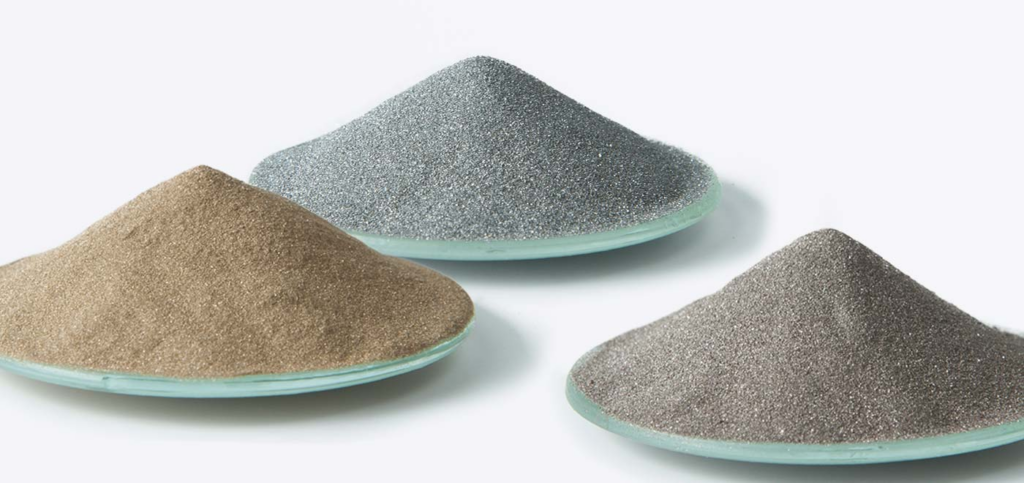
Future Trends in Powder Atomization
The evolution of powder atomization continues to shape the future of materials science and manufacturing.
Industry 4.0 Integration
The integration of Industry 4.0 principles, such as automation, data exchange, and advanced analytics, will lead to more precise control over the atomization process. This will result in even more tailored powders for specific applications.
Eco-Friendly Atomization Techniques
As sustainability becomes increasingly important, researchers are focusing on developing atomization techniques with minimal environmental impact. This includes reducing energy consumption, minimizing waste, and using greener processing methods.
Precision Powder Production
Future trends point toward achieving even greater precision in particle size control and composition. This will open up opportunities for applications requiring ultra-fine powders with precise characteristics.
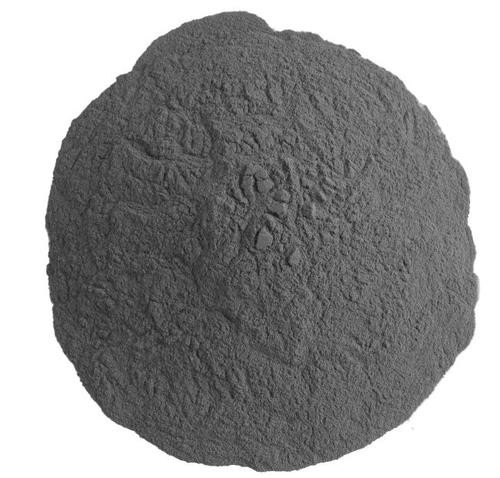
Conclusion
Powder atomization is a cornerstone of modern manufacturing, enabling the production of advanced materials with tailored properties. From aerospace to healthcare, the applications of atomized powders are diverse and continually expanding. As technology advances, challenges are being met with innovative solutions, paving the way for a more sustainable and precise atomization process that will shape the industries of tomorrow.
FAQs on Powder Atomization
- What is powder atomization? Powder atomization is the process of breaking down molten materials into fine particles or powders, often used in manufacturing various products.
- What are the benefits of atomized powders in additive manufacturing? Atomized powders provide precise control over material properties, allowing additive manufacturing to create intricate designs with superior performance.
- What industries benefit most from atomization technology? Industries such as aerospace, automotive, medical devices, and additive manufacturing benefit significantly from atomized powders.
- What challenges does powder atomization face? Challenges include maintaining consistent particle size distribution, addressing contamination concerns, and reducing energy consumption.
- How is the atomization process evolving for the future? The future of atomization involves Industry 4.0 integration, eco-friendly techniques, and enhanced precision in powder production to meet specific requirements.