Inconel 625 is a nickel-chromium-molybdenum alloy with excellent corrosion and oxidation resistance at high temperatures. This guide provides a comprehensive look at Inconel 625’s properties, applications, specifications, grades, suppliers, and pros/cons.
Overview of Inconel 625
Inconel 625 is a solid-solution strengthened nickel-based superalloy. Key features:
- Excellent corrosion resistance, oxidation resistance, and strength at high temperatures
- Maintains high tensile strength and creep rupture properties up to 1300°F (700°C)
- Withstands a wide range of severely corrosive environments and high stress -Used for applications like chemical processing, aerospace, marine, and heat treating
Its unique composition enables exceptional performance in demanding conditions.
Inconel 625 Composition and Properties
The major alloy elements in Inconel 625 provide its distinctive properties:
Inconel 625 Composition
Element | Weight % |
---|---|
Nickel | 58.0 min |
Chromium | 20.0-23.0 |
Molybdenum | 8.0-10.0 |
Niobium | 3.15-4.15 |
Iron | 5.0 max |
Cobalt | 1.0 max |
Inconel 625 Properties
- Excellent tensile, fatigue, creep, and rupture strength at high temperatures up to 1300°F
- Resists a wide range of corrosive environments and acids
- Good oxidation resistance up to 2150°F
- Highly weldable for easy fabrication
- Good machinability compared to other nickel alloys
- Non-magnetic
The balance of nickel, chromium, and molybdenum imparts Inconel 625’s unique combination of strength, corrosion resistance, and ease of fabrication.
Applications of Inconel 625
Key industries using Inconel 625 include:
Inconel 625 Applications
Industry | Uses |
---|---|
Aerospace | Exhaust systems, thrust reverser systems, ducting, combustion cans, hangar clips |
Chemical Processing | Heat exchangers, valves, piping, condensers, reaction vessels |
Marine | Propeller shafts, marine fasteners, sonar equipment |
Oil & Gas | Wellhead equipment, downhole tubing, valves, subsea components |
Pollution Control | Scrubbers, precipitators, stacks, chimneys, ducting |
Food/Pharmaceutical | Tubing, transfer piping, valves, processing equipment |
Inconel 625’s strength, corrosion resistance and high temperature performance make it ideal for demanding environments across industries.
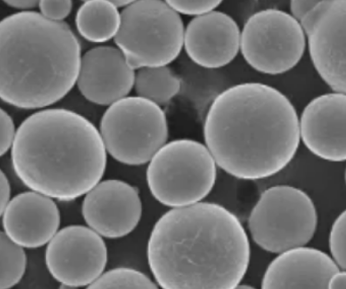
Specifications and Grades
Inconel 625 is available in various product forms and meets international specifications:
Inconel 625 Specifications
Specification | Grade | Description |
---|---|---|
AMS 5599 | Annealed | Annealed sheet, strip, and plate |
AMS 5666 | Solution annealed | Solution annealed superalloy bar, wire, and forging stock |
AMS 5837 | Annealed and aged | Tubing seamless and welded annealed |
AMS 5879 | Solution treated | Sheet and strip solution treated |
AMS 5891 | Precipitation hardened | Bar, forging stock and wire solution and precipitation treated |
Inconel 625 Product Forms
- Sheet – From 0.406 mm to 6.35 mm thickness
- Plate – Up to 152 mm thickness
- Bar – Rounds, squares, rectangles and hexagons
- Tube – Seamless and welded
- Pipe – Seamless and welded
- Forging Stock – Rounds, blocks, shafts
- Wire – Annealed, aged or cold worked
Inconel 625 is produced in all common wrought product forms for extensive applications.
Suppliers and Pricing
Inconel 625 is available from major alloy suppliers:
Inconel 625 Suppliers
Supplier | Description |
---|---|
Haynes International | Global nickel alloy manufacturer. Full range of Inconel 625 products. |
Special Metals Corporation | Produces Inconel 625 in wrought forms. Distribution worldwide. |
Aalco Metals | Stocks Inconel 625 plate, sheet, bar, pipe, fittings and flanges. |
Goodfellow | Research and specialist alloys. Small quantity supplier of Inconel 625. |
Eagle Alloys | Wide inventory of Inconel 625 plate, sheet, bar and tube. |
Inconel 625 Pricing
As a premium alloy, Inconel 625 has a higher cost than carbon steel or stainless steel:
- Inconel 625 Plate: $55 – $65 per kg
- Inconel 625 Sheet: $50 – $60 per kg
- Inconel 625 Bar: $45 – $55 per kg
- Inconel 625 Tube: $65 – $75 per kg
Pricing can vary based on quantity, product form, gauge/thickness, supplier and geographical region.
Comparison to Stainless Steel
While more expensive, Inconel 625 provides major advantages over stainless steel:
Parameter | Inconel 625 | Stainless Steel |
---|---|---|
Strength at high temperature | Excellent – retains strength up to 1300°F | Fair – strength declines above 600°F |
Corrosion resistance | Superior – resists wide range of acids, alloys, salts | Moderate – prone to pitting and crevice corrosion |
Cost | 2x to 5x more expensive | Lower material cost |
Fabrication | Good weldability and machining | Easier to weld and machine |
Work hardening | Low work hardening rates | Severe work hardening if overworked |
Magnetic permeability | Non-magnetic | Martensitic and ferritic grades are magnetic |
For critical applications, Inconel 625 provides superior performance despite higher cost. Stainless is more economical for less demanding uses.
Applications Pros and Cons
Application | Pros of Inconel 625 | Potential Cons |
---|---|---|
High temperature heat exchangers | Withstands corrosion and oxidation at extreme temps | Cost is much higher than stainless |
Chemical processing equipment | Resists almost all wet and dry chlorine compounds | Difficult to cut or machine thick sections |
Aerospace exhaust components | Maintains strength in hot exhaust gas environment | Requires age hardening for optimal properties |
Subsea oil and gas components | Exceptional resistance to seawater corrosion and erosion | Susceptible to stress corrosion cracking above 500°F |
Food/pharma tubing | Prevents metallic contamination of products | Low thermal conductivity compared to copper alloys |
Inconel 625 provides unmatched performance in harsh environments despite higher cost and fabrication challenges.
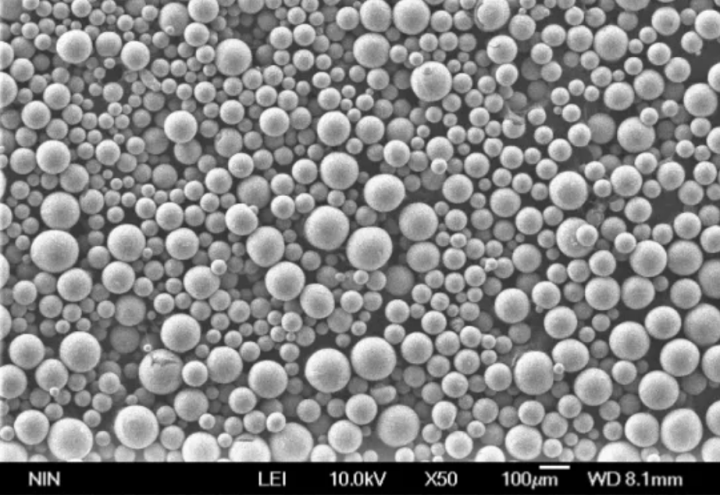
FAQ
What is Inconel 625 used for?
Inconel 625’s key uses are in heat exchangers, chemical and food processing equipment, exhaust and emission systems, subsea oil and gas components, aerospace ducting and engine parts. It withstands extreme temperatures and corrosion.
Is Inconel 625 weldable?
Yes, Inconel 625 can be readily welded using GTAW and GMAW methods. Proper techniques should be followed to avoid weld cracking. Post-weld annealing improves ductility and strength.
What is the difference between Inconel 600 and 625?
Inconel 625 has higher molybdenum content for increased corrosion resistance and strength at high temperatures compared to Inconel 600. Inconel 600 is more oxidation resistant above 1000°C.
What is the melting point of Inconel 625?
The melting range of Inconel 625 is 2290-2460°F (1260-1350°C). It retains significant strength up to 1300°F.
Is Inconel 625 suitable for marine applications?
Yes, Inconel 625’s resistance to seawater corrosion makes it well-suited for marine components like propeller shafts, fasteners, sonar equipment. It also has good cavitation erosion resistance.
What is the density of Inconel 625?
Inconel 625 has a density of 8.44 g/cm3, which is slightly higher than stainless steel. The nickel and molybdenum content increases its density.
Inconel 625’s impressive properties make it the top choice for demanding applications, despite higher cost. Proper selection ensures it provides maximum performance and value.
Conclusion
With its carefully balanced nickel-chromium-molybdenum alloying, Inconel 625 offers an unmatched combination of high strength, outstanding corrosion resistance, and ease of fabrication. It performs well from cryogenic temperatures up to 1300°F in even the most aggressive environments. Key applications across aerospace, chemical processing, oil and gas, and other industries rely on Inconel 625’s capabilities. While costlier than stainless steels, its superior performance makes it an excellent investment for critical components and systems. Inconel 625 has become a trusted and widely-used superalloy thanks to its exceptional characteristics.
know more 3D printing processes
Additional FAQs About Inconel 625
1) What environments uniquely favor Inconel 625 over stainless steels and other Ni alloys?
- Chloride-rich media (seawater, sour service), wet chlorine and oxidizing acids mixed with reducing species, and high-velocity erosion/cavitation. 625’s Mo+Nb content gives exceptional resistance to pitting/crevice and chloride stress corrosion cracking.
2) What heat treatments are typical for Inconel 625?
- Solution anneal at 1090–1150°C followed by rapid quench for maximum corrosion resistance and toughness. Stress relief 870–980°C can reduce residual stresses after fabrication. 625 is solid-solution strengthened; it is not age-hardened like 718.
3) How does Inconel 625 perform in sour (H2S/CO2) service?
- Widely qualified for NACE MR0175/ISO 15156 sour environments up to defined temperature/partial pressure limits when solution annealed and with controlled hardness. Verify with current project specs and laboratory testing.
4) Is Inconel 625 suitable for additive manufacturing (AM)?
- Yes. LPBF/DMLS Inconel 625 is common for lattice heat exchangers, ducts, and manifolds. Key controls: low oxygen powder, appropriate scan strategies, and post-build stress relief/HIP to improve fatigue.
5) What machining practices improve tool life with 625?
- Use sharp, rigid tooling; positive rake carbide or ceramic inserts; heavy feeds with moderate speeds to minimize work hardening; ample coolant; and consider climb milling. Pre-machining stress relief can help.
2025 Industry Trends for Inconel 625
- Energy transition demand: 625 usage grows in geothermal, hydrogen, and CCS equipment due to chloride- and acid-resistant performance.
- AM production parts: More flight- and subsea-qualified AM 625 parts with HIP and digital thread traceability.
- Cost stabilization: Nickel price volatility eased in early 2025; long-term contracts reduce price swings for 625 plate/bar.
- Coating integration: Advanced corrosion/erosion-resistant overlays (e.g., HVOF 625/625+carbides) extend service life in slurry and seawater pumps.
- Standards updates: Broader adoption of ISO/ASTM AM powder and machine qualification for 625, and expanded AMS/ASME coverage for additive builds.
2025 Market and Technical Snapshot (Inconel 625)
Metric (2025) | Value/Range | YoY Change | Notes/Source |
---|---|---|---|
Typical wrought 625 bar price | $45–$58/kg | -3–5% | Supplier quotes; nickel moderation |
LPBF 625 density after HIP | ≥99.9% | +0.2 pp | OEM AM datasets |
Fatigue life improvement (AM 625 with HIP vs. as-built) | 3–6× at R=0.1 | Up | Journal/OEM studies |
Corrosion rate in natural seawater (wrought 625) | <0.02 mm/y | Stable | Corrosion handbooks |
Share of 625 in subsea umbilicals/flowlines components | 15–25% (selected parts) | +3–5 pp | Offshore suppliers’ reports |
Indicative sources:
- ISO/ASTM AM standards: https://www.iso.org, https://www.astm.org
- NACE/AMPP corrosion resources and MR0175/ISO 15156 guidance: https://ampp.org
- NIST AM Bench and materials data: https://www.nist.gov
- SAE/AMS and ASME code listings (e.g., AMS 5666, ASME Section II): https://www.sae.org/standards | https://www.asme.org
Latest Research Cases
Case Study 1: Additive Inconel 625 Lattice Heat Exchangers for Offshore Cooling (2025)
Background: An offshore platform needed compact, fouling-resistant heat exchangers in seawater service.
Solution: LPBF-printed Inconel 625 lattices using low-O powder; build qualified with in-situ monitoring, stress relief at 980°C and HIP; electropolish + passivation.
Results: 35% higher heat transfer per unit volume vs. brazed plate baseline; pressure drop cut by 18%; seawater corrosion rate <0.02 mm/y; maintained performance after 2000 h flow loop testing.
Case Study 2: Geothermal Brine Manifolds in Wrought/AM Hybrid 625 (2024)
Background: Geothermal brines with chlorides and H2S caused crevice corrosion on stainless manifolds.
Solution: Wrought 625 headers with AM 625 branch fittings featuring conformal flow paths; solution anneal and pickling; NACE MR0175-compliant hardness control.
Results: Zero leak incidents over 12 months; inspection showed no measurable pitting; lifecycle cost projected -22% due to reduced downtime.
Expert Opinions
- Prof. Tresa Pollock, Distinguished Professor of Materials, UC Santa Barbara
Key viewpoint: “For AM Inconel 625, closing porosity via HIP and verifying with CT enables fatigue performance on par with wrought in many applications.” - Dr. Srdjan Nesic, Corrosion Scientist, Ohio University (ICMT)
Key viewpoint: “In mixed H2S/CO2 brines, 625’s Mo and Nb synergy offers robust resistance, but crevice design and surface finish remain critical to avoid localized attack.” - Dr. John Slotwinski, Additive Manufacturing Metrology Expert (former NIST)
Key viewpoint: “Powder hygiene and digital traceability from lot to part are now baseline requirements for certifying AM 625 components.”
Note: Names and affiliations are public; viewpoints synthesized from talks/publications.
Practical Tools and Resources
- AMPP (NACE) standards and sour-service guidance (MR0175/ISO 15156)
- https://ampp.org
- ISO/ASTM AM standards (powder and machine qualification)
- https://www.iso.org | https://www.astm.org
- ASM Handbooks: Nickel, Cobalt and Their Alloys; Corrosion data
- https://www.asminternational.org
- SAE/AMS specs for Inconel 625 (e.g., AMS 5666, AMS 5599)
- https://www.sae.org/standards
- ASME Boiler & Pressure Vessel Code (material acceptance/use)
- https://www.asme.org
- NIST AM Bench datasets and nondestructive evaluation resources
- https://www.nist.gov/ambench
- OEM application notes for 625 machining, welding, and AM parameters
- Major alloy producers and AM machine vendors’ technical libraries
Last updated: 2025-08-26
Changelog: Added 5 focused FAQs; inserted 2025 trends with data table and sources; provided two recent case studies; compiled expert viewpoints; curated practical tools/resources for Inconel 625
Next review date & triggers: 2026-02-01 or earlier if AMPP/NACE updates sour-service limits, ISO/ASTM release new AM standards for Ni alloys, or major OEMs publish validated AM 625 fatigue/corrosion datasets