With the advantages of low density, high specific strength and good corrosion resistance, aluminium alloy powders have become a major material in aerospace, machinery and construction, especially in the aerospace sector, due to the need for light weight.
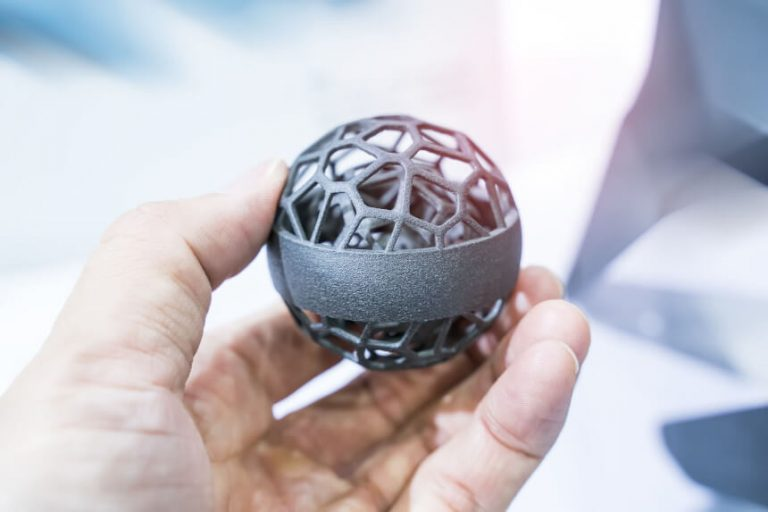
Aluminium Alloy Powders: ALSi10Mg
AlSi10Mg alloy powder is a material that is widely used in 3D printing, it has the advantages of good flowability, good gas tightness, low shrinkage and has good casting properties.
Al-Si alloy is a widely used casting aluminium alloy, according to the amount of Si content in the alloy, the Al-Si series alloys can be divided into eutectic silicon aluminium alloy, peri-eutectic silicon aluminium alloy and sub-eutectic silicon aluminium alloy.In Al-Si alloy, Si as the main alloying element can improve the alloy Al-Si alloys have good corrosion resistance, medium machinability, medium strength and hardness, but low plasticity.
AlSi10Mg has good fluidity, good gas tightness, low shrinkage, low thermal cracking tendency, good casting properties and is one of the most widely used alloys for casting aluminium alloys.
SLM is an additive manufacturing technology, in which titanium alloy, stainless steel, nickel-based high-temperature alloy and other metal powder materials have been more mature about the application of SLM technology, while there are considerable challenges in the application of SLM technology because aluminium alloy powder is more difficult to shape compared with other metals.
Aluminium alloy powders are light and poorly flowable, so there is a problem with the difficulty of spreading the powder in the application of SLM technology. At the same time, aluminium alloy powders are highly reflective of the laser and have a high thermal conductivity, so higher laser energy is required during processing. The laser is prone to vapourisation and oxidation when applied to the aluminium alloy surface, and is prone to spheroidisation during SLM forming, resulting in poor forming quality.
AlSi10Mg aluminium alloy is a sub-eutectic casting aluminium alloy with a relatively small solidification interval and better flowability than other aluminium alloys. Due to the high Si content, it can improve the absorption of laser light and make its forming relatively easy, therefore the development of AlSi10Mg in the field of SLM technology is more mature compared to the development of other aluminium alloy powders.
The fabrication of AlSi10Mg using SLM technology is widely used to improve its strength and toughness due to the microstructure refinement and melt pool-induced fine structure caused by the rapid cooling of laser fabrication. Further investigations such as the combination of properties require a detailed study of how the process conditions control the microstructure and fine view, and in turn, the mechanical properties, particularly fracture toughness, require particular attention.
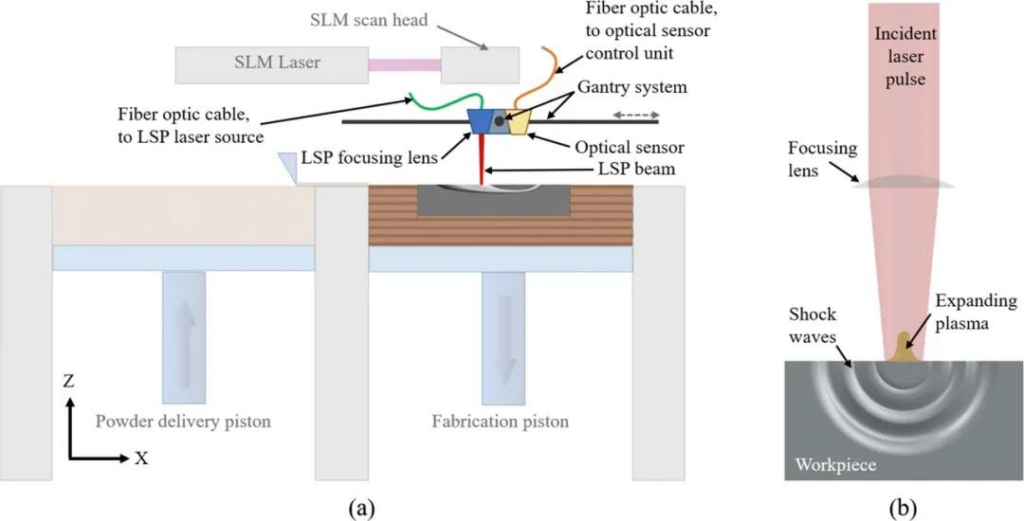
As selective laser melting (SLM) is a new type of laser rapid forming process. The application of SLM process to form single-piece, small batch aerospace aluminium alloy products has advantages over traditional processes in terms of improving material utilisation, achieving complex structure manufacturing and shortening manufacturing cycle time. However, the preparation of high performance aluminium alloy powder materials is one of the main difficulties in order to obtain SLM parts with excellent performance. Therefore, regarding the preparation of AlSi10Mg powder, at present, the main methods used for aluminium alloy powder materials are inert gas atomisation (AA method) and crucible-free electrode induction melting gas atomisation (EIGA method), which have the shortcomings of low sphericity, poor fluidity (-325 mesh powder basically does not have fluidity) and low loose packing density. The PREP method produces powders with high sphericity, good flowability and loose packing density up to 60% of the dense material, which can effectively solve the technical bottleneck of aerosolised powders.
These are some notes on AlSi10Mg powder as an aluminium alloy in SLM technology for forming. More research on powder making and experiments are also needed on how the aluminium alloy powder can achieve the most ideal forming quality.