Introduction
The world of manufacturing is constantly evolving, and one of the most significant advancements in recent times has been the advent of additive manufacturing, popularly known as 3D printing. This revolutionary technique allows the creation of intricate and complex shapes with unprecedented precision. Among the myriad of materials used in additive manufacturing, tungsten stands out due to its exceptional properties and applications. In this article, we will explore the fascinating world of additive manufacturing with tungsten and how it is transforming various industries.
What is additive manufacturing tungsten?
Additive manufacturing, also known as 3D printing, is a process that builds three-dimensional objects layer by layer from a digital model. Unlike traditional subtractive methods that involve cutting or drilling material from a solid block, additive manufacturing allows for the precise addition of material, resulting in minimal waste and maximum design flexibility.
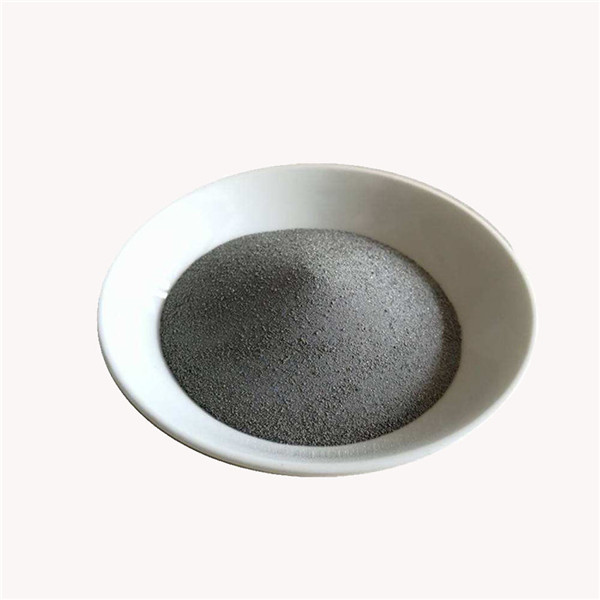
Understanding Tungsten in Additive Manufacturing
What is Tungsten?
Tungsten, symbolized by W on the periodic table, is a remarkable metal known for its exceptional hardness and high melting point. It is often referred to as “heavy metal” due to its density, which is comparable to gold. additive manufacturing tungsten finds applications in various industries, ranging from aerospace and defense to electronics and medical.
Properties of Tungsten
Tungsten boasts an array of properties that make it ideal for additive manufacturing. These properties include its high melting point, excellent thermal conductivity, low coefficient of thermal expansion, and outstanding mechanical strength.
Tungsten in Traditional Manufacturing
Before we delve into additive manufacturing with tungsten, it is essential to understand how this metal has been used in traditional manufacturing processes. Tungsten has a rich history of applications in the production of electrical wires, filaments, and various alloys, such as steel and superalloys.
Additive Manufacturing Techniques Using Tungsten
Powder Bed Fusion (PBF)
One of the most popular additive manufacturing techniques using tungsten is Powder Bed Fusion. This process involves spreading a thin layer of tungsten powder and selectively melting it using a high-energy laser or electron beam. The process is repeated layer by layer, creating a solid, dense, and intricate tungsten component.
Directed Energy Deposition (DED)
Directed Energy Deposition is another additive manufacturing method that incorporates tungsten. In this technique, a focused energy source, such as a laser or electron beam, is used to melt tungsten wire or powder, which is precisely deposited onto a substrate to build the desired object.
Binder Jetting
Binder Jetting is a unique additive manufacturing process where layers of tungsten powder are selectively bound together using a binding agent. The unbound powder is removed, and the bound layers are sintered to create the final part.
Material Extrusion
Material Extrusion, commonly known as Fused Deposition Modeling (FDM), is a technique where a continuous strand of tungsten-filled thermoplastic is extruded and deposited layer by layer to form the desired shape.
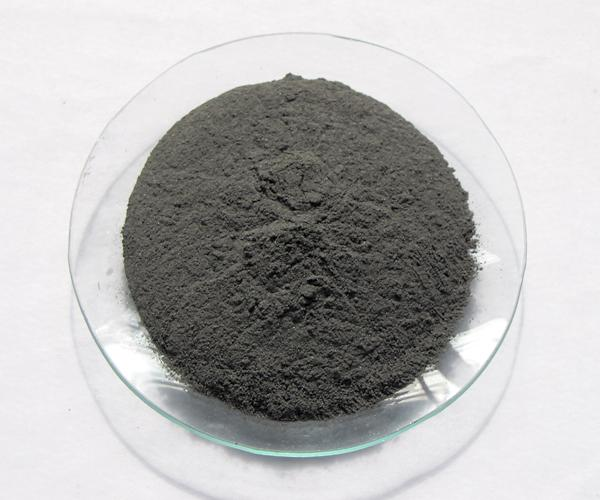
Applications of Additive Manufacturing with Tungsten
Aerospace Industry
Tungsten’s remarkable properties, such as high strength and density, make it a valuable material in the aerospace industry. Additive manufacturing allows for the creation of lightweight, yet robust components used in aircraft and spacecraft.
Medical Sector
In the medical field, additive manufacturing with tungsten has opened new doors for creating patient-specific implants, surgical instruments, and dental prosthetics, providing better treatment options and improved patient outcomes.
Energy and Power Generation
Tungsten plays a crucial role in the energy and power generation sectors, where components like turbine blades, heat exchangers, and nuclear reactor parts benefit from the precision and efficiency of additive manufacturing.
Advantages of Additive Manufacturing with Tungsten
Complex Geometries
Additive manufacturing allows for the fabrication of intricate and complex geometries that are challenging or impossible to achieve using traditional manufacturing methods.
Material Efficiency
With additive manufacturing, tungsten and other materials are used more efficiently, as the process builds the final part layer by layer, minimizing wastage.
Customization and Prototyping
The flexibility of additive manufacturing enables rapid prototyping and customization, facilitating faster product development and iteration.
Reduced Waste and Environmental Impact
As a sustainable manufacturing process, additive manufacturing produces less waste, reduces energy consumption, and has a lower environmental impact compared to conventional methods.
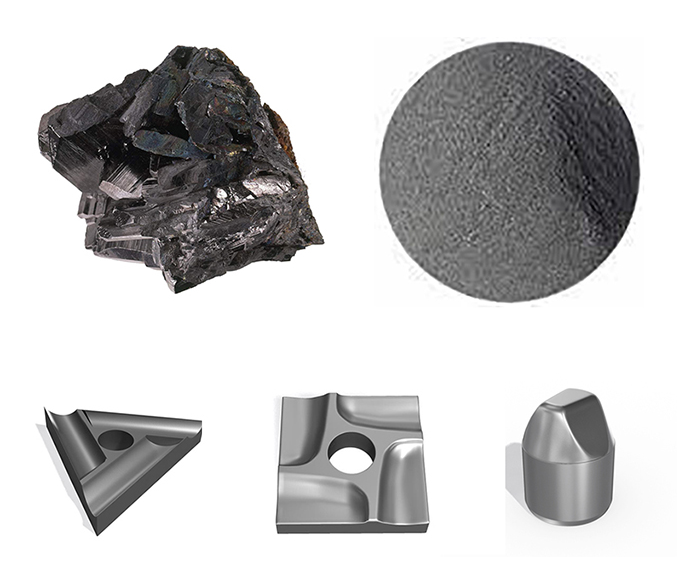
Challenges and Limitations of Additive Manufacturing with Tungsten
High Melting Point and Thermal Conductivity
Tungsten’s high melting point and thermal conductivity pose challenges during the additive manufacturing process, demanding specialized equipment and precise temperature control.
Powder Handling and Safety Concerns
Tungsten powder can be hazardous if not handled with care, necessitating strict safety measures and specialized equipment for handling and processing.
Surface Finish and Post-Processing
Achieving a smooth surface finish on tungsten parts can be challenging, often requiring additional post-processing steps to meet the desired specifications.
Current Research and Innovations in Additive Manufacturing with Tungsten
The field of additive manufacturing with tungsten is continuously evolving, with ongoing research focused on enhancing the process, exploring new applications, and developing advanced materials.
Future Prospects of Additive Manufacturing with Tungsten
As additive manufacturing technology matures and becomes more accessible, the adoption of tungsten in various industries is expected to increase, leading to further innovation and optimization of the process.
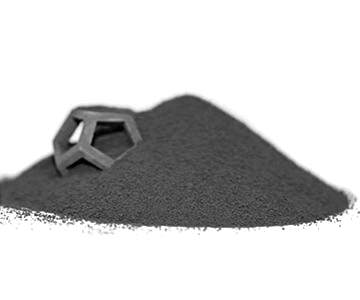
Conclusion
Additive manufacturing with tungsten has emerged as a groundbreaking technology, revolutionizing the way metal components are fabricated. Its unique properties, combined with the versatility of additive manufacturing, have unlocked numerous possibilities in industries like aerospace, healthcare, and energy generation. The ability to create complex geometries, reduce material waste, and customize parts has made additive manufacturing with tungsten a game-changer in modern manufacturing.
FAQs
Q1: What makes tungsten an ideal material for additive manufacturing?
Tungsten’s exceptional properties, such as high melting point, thermal conductivity, and mechanical strength, make it an ideal material for additive manufacturing. It allows the creation of robust and intricate parts with precision.
Q2: How does additive manufacturing with tungsten reduce material waste?
Additive manufacturing builds parts layer by layer, only using the necessary amount of material. This reduces material waste significantly compared to traditional manufacturing methods.
Q3: Is additive manufacturing with tungsten safe for handling and processing?
Tungsten powder can be hazardous if not handled properly. Proper safety measures and specialized equipment are essential to ensure safe handling and processing during additive manufacturing.
Q4: What are some of the challenges in additive manufacturing with tungsten?
Challenges include managing the high melting point and thermal conductivity of tungsten, achieving smooth surface finishes, and ensuring safety during powder handling.
Q5: What industries benefit the most from additive manufacturing with tungsten?
Aerospace, medical, and energy sectors are among the industries that benefit the most from additive manufacturing with tungsten, thanks to its unique properties and versatility.
know more 3D printing processes
Additional FAQs About additive manufacturing tungsten
1) Which AM processes work best for tungsten and why?
- Electron Beam Melting (EBM) and Directed Energy Deposition (DED—laser/e-beam) are most mature because high preheat and vacuum/inert conditions mitigate cracking, evaporation, and oxidation. Binder Jetting + sinter/HIP is promising for large or complex shapes with lower thermal stress.
2) What powder specifications are recommended for tungsten in PBF?
- Spherical powder, PSD 15–45 µm (fine feature) or 20–63 µm (general), sphericity ≥0.93, satellites ≤5%, and oxygen ≤0.05–0.15 wt% depending on application. Low hollow fraction verified by CT improves density and reduces spatter.
3) How do you control cracking and residual stress in tungsten AM?
- Use high build preheat (EBM often 800–1000°C equivalent), reduce scan speed/adjust hatch spacing, apply contour-first strategies, and perform stress-relief or HIP post-processing. For laser PBF, consider elevated plate heating and tailored scan vectors.
4) Can tungsten be alloyed or blended to improve printability?
- Yes. W‑Ni‑Fe (heavy alloy), W‑Cu (cermet), W‑Re, and W‑Ta systems improve toughness or thermal properties and ease processing. Binder Jetting and DED also enable graded W‑Cu or W‑Mo structures for thermal management.
5) What are the leading applications of additive manufacturing tungsten today?
- Radiation shielding and collimators, high‑temperature rocket nozzle throats/inserts, plasma‑facing components, X‑ray anodes, hot‑zone tooling, and wear/erosion resistant or high thermal load components in energy and semiconductor equipment.
2025 Industry Trends for additive manufacturing tungsten
- Process windows mature: More validated EBM/DED parameters for pure W and W‑based alloys reduce cracking and porosity.
- Binder Jetting scale-up: Larger near‑net W and W‑Cu components with optimized debind/sinter/HIP cycles enter production.
- Data-rich CoAs: CT‑based hollow fraction and image‑based satellite counts added to tungsten powder certificates.
- Thermal management parts: Growth in W‑Cu graded heat spreaders for power electronics and semiconductor tools.
- Sustainability: Increased powder recycling with oxygen/hydrogen trending; regional atomization reduces lead times.
2025 Market and Technical Snapshot (additive manufacturing tungsten)
Metric (2025) | Typical Value/Range | YoY Change | Notes/Source |
---|---|---|---|
AM‑grade spherical W powder price | $120–$250/kg (99.9%); W‑Cu/W‑Ni‑Fe: $90–$180/kg | −2–5% | Supplier quotes; alloy/PSD dependent |
Recommended PSD (PBF / DED / BJ) | 15–45 or 20–63 µm / 53–150 µm / 20–80 µm | Stable | OEM/application guidance |
Typical oxygen in AM‑grade W | 0.05–0.15 wt% | Down | Improved atomization/inert handling |
Achievable relative density (EBM W) | 99.5–99.9% post‑HIP | +0.1–0.2 pp | OEM/academic datasets |
Binder Jet + sinter W density | 97.5–99.2% (HIP optional) | Up | Optimized sinter/HIP cycles |
Validated powder reuse cycles | 4–7 with QC | Stable | O/H trending + sieving programs |
Indicative sources:
- ISO/ASTM 52907 (Metal powders) and 52908 (Process qualification): https://www.iso.org | https://www.astm.org
- NIST AM Bench and powder metrology: https://www.nist.gov
- ASM Handbooks (Additive Manufacturing; Refractory Metals & Alloys): https://www.asminternational.org
Latest Research Cases
Case Study 1: EBM‑Processed Tungsten Collimators for Radiation Therapy (2025)
Background: A medical device OEM needed complex, high‑density collimators with internal channels unachievable by machining.
Solution: EBM with high preheat; spherical W powder (20–63 µm, sphericity 0.95, O 0.08 wt%). Post‑HIP and precision machining of interfaces.
Results: Relative density 99.7%; dimensional accuracy within ±80 µm; measured attenuation improved 12% over brazed assemblies; part count reduced from 8 to 1, cutting lead time by 35%.
Case Study 2: Binder Jet + HIP W‑Cu Heat Sinks for Power Electronics (2024)
Background: An EV inverter supplier sought near‑net W‑Cu heat spreaders with embedded cooling features.
Solution: Binder Jetting a bimodal PSD blend; solvent debind + H2 sinter; infiltration and HIP to target 70W‑30Cu; surface finishing of channels.
Results: Final density 99.0–99.3%; through‑plane thermal conductivity 210–230 W/m·K; flatness improved 40% vs. machined baseline; cost per part −18%.
Expert Opinions
- Dr. Zhigang Zak Fang, Professor of Metallurgical Engineering, University of Utah
Key viewpoint: “High‑temperature processing and impurity control are pivotal—oxygen management and optimized sinter/HIP cycles are the difference between brittle and robust tungsten AM parts.” - Prof. Tresa Pollock, Distinguished Professor of Materials, UC Santa Barbara
Key viewpoint: “In refractory metals like tungsten, vacuum/temperature control and powder morphology strongly dictate defect populations and fatigue/thermal shock performance.” - Dr. John Slotwinski, Additive Manufacturing Metrology Expert (former NIST)
Key viewpoint: “Lot‑to‑lot PSD, sphericity, and O/H trending in CoAs accelerate qualification for additive manufacturing tungsten more than incremental scan tweaks.”
Note: Viewpoints synthesized from public literature and talks; affiliations are publicly known.
Practical Tools and Resources
- Standards and guidance
- ISO/ASTM 52907 (powders), 52908 (process/machine qualification): https://www.iso.org | https://www.astm.org
- Metrology and safety
- NIST powder characterization; LECO O/H analyzers; industrial CT for hollow/satellite quantification: https://www.nist.gov
- NFPA 484 (Combustible metal powders safety): https://www.nfpa.org
- Technical data and handbooks
- ASM Digital Library (Refractory metals, AM processing): https://www.asminternational.org
- Process/QC checklist
- Powder QC: PSD, sphericity, satellites, O/H; Build: preheat control, scan strategy; Post: HIP/stress‑relief, NDE (CT), thermal/mechanical validation
Last updated: 2025-08-26
Changelog: Added 5 targeted FAQs; introduced 2025 market/technical snapshot table with indicative sources; provided two tungsten AM case studies; compiled expert viewpoints; listed practical tools/resources for additive manufacturing tungsten
Next review date & triggers: 2026-02-01 or earlier if ISO/ASTM update refractory metal AM standards, major OEMs release new W/W‑Cu material cards, or NIST/ASM publish datasets on impurity–defect–performance links for tungsten AM