Introduction
In the ever-evolving landscape of manufacturing, additive manufacturing, also known as 3D printing, has emerged as a groundbreaking technology. Among the various 3D printing techniques, Selective Laser Melting (SLM) stands out as one of the most promising and versatile methods. This article explores the world of additive manufacturing SLM, shedding light on its history, applications, materials used, challenges, and future possibilities.
What is Additive Manufacturing SLM?
Additive Manufacturing SLM is a revolutionary process that enables the creation of complex three-dimensional objects by selectively fusing fine layers of materials. Unlike traditional subtractive methods, where material is removed to achieve the desired shape, additive manufacturing SLM builds objects layer by layer, using a high-power laser to melt and fuse the powdered material. This process offers unprecedented design flexibility and has found applications across various industries.
History and Evolution of SLM
The concept of additive manufacturing dates back to the 1980s, but it was not until the 1990s that SLM gained traction as a viable method. Over the years, advancements in laser technology, materials, and software have propelled SLM to new heights, making it commercially accessible and cost-effective. As industries began to recognize its potential, research and development efforts intensified, leading to significant improvements in machine capabilities and material options.
How Does Additive Manufacturing SLM Work?
The SLM process starts with creating a 3D digital model using Computer-Aided Design (CAD) software. This virtual model is then sliced into thin horizontal layers, serving as the blueprint for the physical object. The SLM machine preheats the build platform and spreads a thin layer of metal powder evenly. The focused laser beam selectively melts and fuses the powder according to the cross-section of the model. Once a layer is complete, the build platform moves down, and a new layer of powder is applied, repeating the process until the entire object is formed.
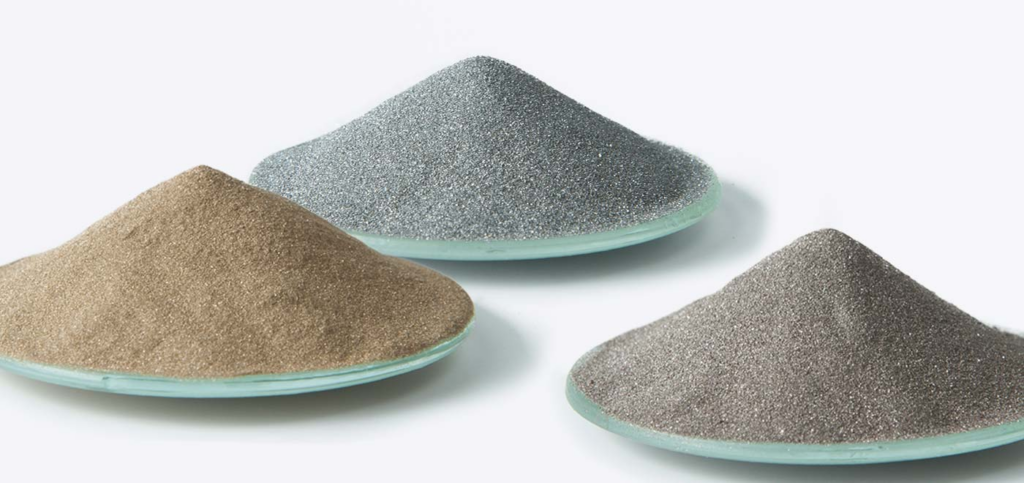
Benefits of Additive Manufacturing SLM
Cost-Effective Production
Additive manufacturing SLM eliminates the need for costly tooling, which is common in traditional manufacturing. This feature is especially beneficial for small-scale production runs, where investing in molds or dies can be economically unviable. As a result, companies can bring products to market faster and at lower costs.
Design Freedom and Complexity
The layer-by-layer approach of SLM allows for unprecedented design freedom. Manufacturers can create complex geometries and intricate details that would be impossible or extremely challenging to achieve through conventional methods. This opens up new opportunities for innovation and optimization in product design.
Reduced Material Waste
Traditional manufacturing often generates a substantial amount of material waste due to subtractive processes. In contrast, SLM is an additive process, minimizing material waste as it only uses the exact amount of material required to build the object. This efficiency is environmentally friendly and cost-effective.
Rapid Prototyping and Time-to-Market
SLM’s ability to quickly produce prototypes significantly accelerates the product development cycle. Iterative design improvements can be made rapidly, reducing time-to-market and enabling companies to stay ahead in highly competitive industries.
Applications of Additive Manufacturing SLM
The versatility of SLM has led to its adoption across various sectors. Some of the prominent applications include:
Aerospace Industry
The aerospace sector has been an early adopter of additive manufacturing SLM. It allows for lightweight yet robust components, reducing the overall weight of aircraft and enhancing fuel efficiency. Moreover, custom and complex parts can be produced with ease, supporting mission-critical applications.
Medical and Healthcare Sector
In the medical field, SLM has revolutionized the production of patient-specific implants and prosthetics. Customized medical devices can be created to perfectly fit the anatomy of individual patients, resulting in better treatment outcomes and enhanced patient comfort.
Automotive Industry
The automotive industry utilizes SLM for rapid prototyping, functional end-use parts, and performance optimization. Additive manufacturing enables car manufacturers to create intricate designs, leading to lighter and more efficient vehicles.
Jewelry and Fashion
SLM has disrupted the jewelry industry by enabling intricate and personalized designs that were previously unattainable. It allows designers to push the boundaries of creativity and produce unique pieces for their customers.
Tooling and Industrial Manufacturing
In the manufacturing sector, SLM is employed to create complex tooling and molds, streamlining production processes and reducing lead times. It also supports the repair and replacement of critical parts in industrial machinery.
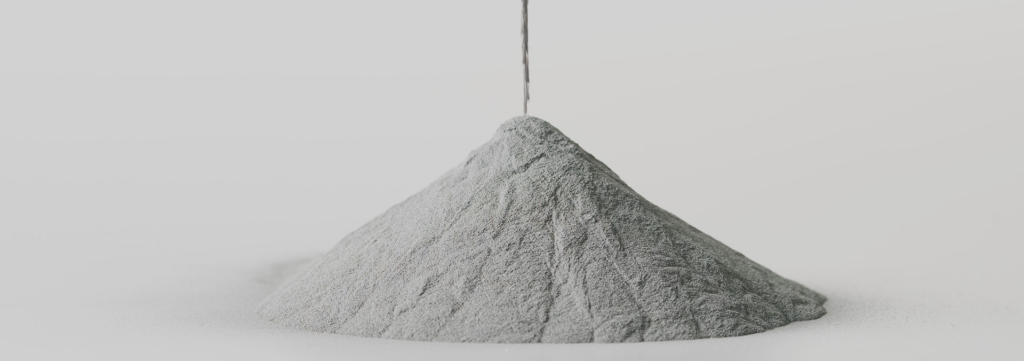
Materials Used in SLM
SLM is compatible with a wide range of materials, including metals, polymers, and ceramics. Some of the commonly used materials are:
Metals
Various metals, such as titanium, aluminum, stainless steel, and nickel alloys, can be used in SLM. Each metal offers specific properties, making them suitable for different applications in industries like aerospace, medical, and automotive.
Polymers
Polymer-based SLM is commonly used in the production of prototypes, consumer goods, and medical devices. Polyamide (nylon), polyetheretherketone (PEEK), and polylactic acid (PLA) are examples of polymers used in SLM.
Ceramics
Ceramic materials are employed in applications requiring high-temperature resistance, biocompatibility, and electrical insulation. Ceramic SLM finds applications in the medical and electronics industries.
Challenges and Limitations of SLM
Despite its remarkable capabilities, additive manufacturing SLM faces certain challenges and limitations that must be addressed:
Surface Finish and Post-Processing
The surface finish of SLM parts may not always meet the desired standards, requiring additional post-processing steps like polishing or machining. These additional steps can increase production time and costs.
Quality and Consistency
Achieving consistent quality in SLM parts can be challenging due to factors like thermal stress, distortion, and porosity. Manufacturers must carefully control process parameters to ensure reliable and manufacturers must carefully control process parameters to ensure reliable and repeatable results. Quality control measures are essential to identify defects and ensure the integrity of the final product.
Size and Scale Constraints
The build size of SLM machines is limited, which can be a constraint for producing large-scale components. Upscaling the technology without sacrificing quality remains an ongoing challenge in the field.
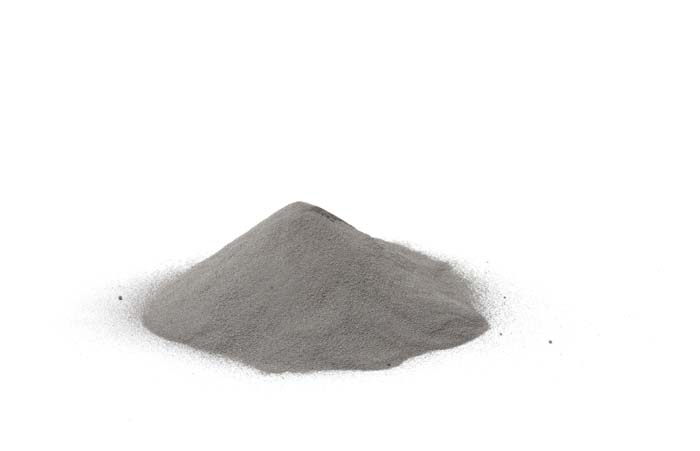
Future Trends in Additive Manufacturing SLM
As technology continues to advance, several exciting trends are shaping the future of additive manufacturing SLM:
- Improved Materials: Researchers are actively working on developing new and improved materials with enhanced properties and performance, expanding the scope of applications for SLM.
- Multi-Material Printing: Advancements in multi-material printing are on the horizon, enabling the creation of hybrid structures with varying properties, further boosting design possibilities.
- In-Situ Monitoring: Real-time monitoring during the printing process is being explored to enhance process control and ensure better quality outcomes.
- Automation and Integration: Efforts are being made to integrate SLM with other manufacturing processes and automate post-processing steps to streamline production.
- Reduced Costs: As technology matures and becomes more widespread, the overall cost of SLM machines and materials is expected to decrease, making the technology more accessible to a broader range of industries.
The Role of SLM in Sustainable Manufacturing
Sustainable manufacturing practices are gaining prominence as industries strive to reduce their environmental impact. Additive manufacturing SLM aligns with these goals in several ways:
- Material Efficiency: SLM’s additive nature minimizes material waste, reducing the consumption of raw materials and energy.
- Lightweighting: By producing lightweight yet strong components, SLM contributes to fuel efficiency in transportation and reduces overall energy consumption.
- Local Production: On-demand manufacturing with SLM can reduce the need for long-distance transportation of goods, thereby lowering carbon emissions.
- Circular Economy: SLM enables the use of recycled materials and supports a circular economy model, reducing reliance on virgin resources.
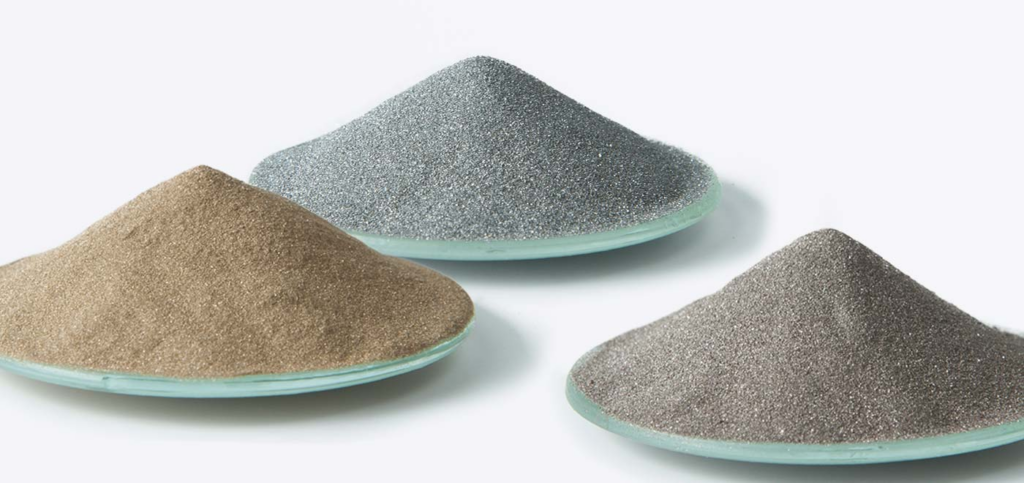
Conclusion
Additive manufacturing SLM has emerged as a transformative technology in the manufacturing landscape, unlocking new possibilities for design, efficiency, and sustainability. Its applications span across various industries, from aerospace and healthcare to automotive and fashion. As research and development continue to push the boundaries, SLM is poised to revolutionize how we produce and consume goods. However, challenges related to surface finish, quality control, and scalability must be overcome for widespread adoption. With advancements on the horizon and a commitment to sustainable practices, the future of additive manufacturing SLM looks promising.
FAQs
- Is additive manufacturing SLM the same as 3D printing?Yes, additive manufacturing SLM is a specific form of 3D printing. It utilizes a high-power laser to selectively fuse powdered material, layer by layer, to create complex three-dimensional objects.
- What industries benefit the most from SLM?Additive manufacturing SLM finds applications in industries like aerospace, medical, automotive, jewelry, and industrial manufacturing, among others.
- Can SLM be used for mass production?While SLM is excellent for producing low-volume and highly customized parts, mass production may still require further advancements in speed and scalability.
- What materials can be used in SLM?SLM is compatible with various materials, including metals (e.g., titanium, aluminum), polymers (e.g., nylon, PEEK), and ceramics.
- What are the environmental benefits of SLM?SLM reduces material waste, supports lightweight design for fuel efficiency, and promotes local production, contributing to more sustainable manufacturing practices.
Remember, additive manufacturing SLM is an ever-evolving technology, and its potential is only limited by our imagination. As more industries and innovators embrace SLM’s capabilities, we can expect to witness even more groundbreaking applications and advancements in the future.