1. Introduction
In recent years, additive manufacturing has revolutionized the manufacturing industry by enabling the production of complex and customized parts. One of the most promising techniques within this field is Selective Laser Melting (SLM) 3D printing. This article explores the world of SLM 3D printing, how it works, its advantages, applications, challenges, and future trends.
2. What is SLM 3D Printing?
SLM 3D printing, also known as laser powder bed fusion, is an additive manufacturing process that utilizes a high-powered laser to selectively melt and fuse metallic powders layer by layer. The process starts with a 3D digital model, which is sliced into thin cross-sectional layers. These layers are then sequentially melted and solidified, forming a three-dimensional object. SLM 3D printing primarily utilizes metal powders such as stainless steel, titanium, aluminum, and nickel alloys.
3. How Does SLM 3D Printing Work?
The SLM 3D printing process begins with the preparation of the build platform. A thin layer of metal powder is evenly spread over the platform, and the laser is directed to selectively melt the powder according to the digital design. The melted powder solidifies, forming a solid layer. The build platform is then lowered, and a new layer of powder is spread on top. This process is repeated until the entire object is printed.
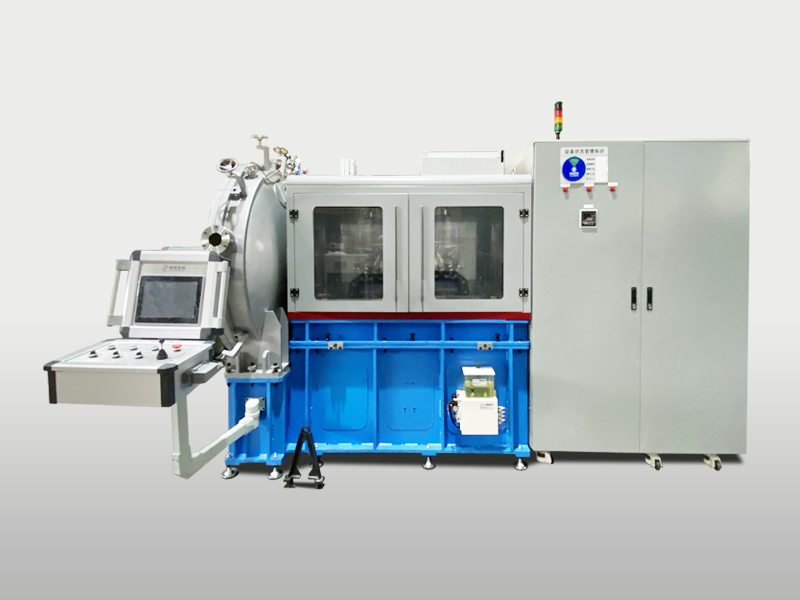
4. Advantages of SLM 3D Printing
4.1 Complex Geometries
One of the major advantages of SLM 3D printing is its ability to create highly complex geometries that are otherwise difficult or impossible to manufacture using traditional methods. The layer-by-layer approach allows for the creation of intricate internal structures, hollow parts, and organic shapes, opening up new design possibilities.
4.2 Material Versatility
SLM 3D printings supports a wide range of metallic materials, including alloys with specific mechanical properties. This versatility makes it suitable for various industries, from aerospace to medical and automotive. Different materials can be utilized within a single print job, enabling the production of multi-material and graded structures.
4.3 Rapid Prototyping
SLM 3D printing allows for the quick and cost-effective production of prototypes. Traditional manufacturing methods often involve time-consuming and expensive tooling processes. With SLM 3D printing, designers can rapidly iterate and test their designs, accelerating the product development cycle.
4.4 Cost Efficiency
While the initial investment in SLM 3D printings equipment can be significant, it offers long-term cost advantages. The additive nature of the process minimizes material waste, and the ability to consolidate complex parts reduces assembly requirements. Additionally, SLM 3D printings eliminates the need for specialized tooling and molds, saving both time and money.
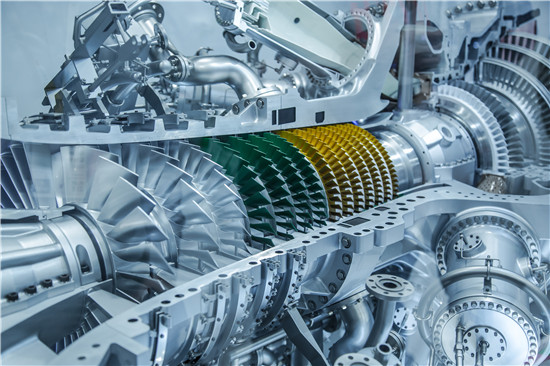
5. Applications of SLM 3D Printing
5.1 Aerospace Industry
The aerospace industry has been at the forefront of adopting SLM 3D printing technology. The ability to create lightweight yet robust parts with complex internal structures is highly beneficial in aerospace applications. Components such as turbine blades, fuel nozzles, and brackets can be produced using SLM 3D printing, leading to weight reduction, improved fuel efficiency, and enhanced performance of aircraft.
5.2 Medical Field
SLM 3D printings has also found extensive applications in the medical field. Customized implants, prosthetics, and surgical instruments can be produced with high precision and tailored to individual patient needs. This technology enables the development of patient-specific solutions, improving treatment outcomes and patient satisfaction. Furthermore, it allows for the creation of porous structures that promote better integration with natural tissues.
5.3 Automotive Sector
The automotive industry benefits from SLM 3D printing in various ways. It enables the production of lightweight and complex components, contributing to fuel efficiency and vehicle performance. Additionally, SLM 3D printing enables the rapid prototyping of car parts, facilitating the design and testing of new models. This technology also plays a role in the production of custom-made components for specialized vehicles and racing cars.
5.4 Jewelry Design
SLM 3D printings has revolutionized the jewelry industry by providing new avenues for design and customization. Intricate and intricate designs can be created with high precision, allowing jewelers to bring their artistic visions to life. Moreover, SLM 3D printing enables the production of complex and lightweight jewelry pieces that are comfortable to wear and visually stunning.
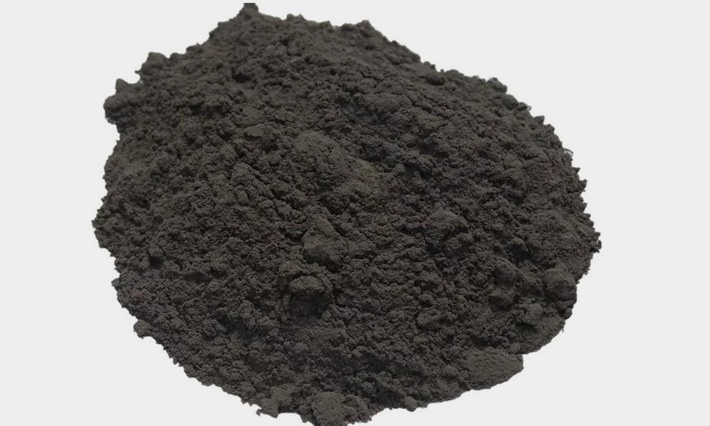
6. Challenges in SLM 3D Printing
While SLM 3D printings offers numerous advantages, it also presents some challenges that need to be addressed:
6.1 Post-Processing
After the completion of the printing process, post-processing steps are required to remove support structures, improve surface finish, and achieve desired mechanical properties. This post-processing can be time-consuming and labor-intensive, adding to the overall production time and cost.
6.2 Material Limitations
Although SLM 3D printings supports a wide range of metallic materials, certain materials may pose challenges due to their properties. For instance, materials with high thermal conductivity or low melting points can be difficult to process effectively. Advancements in material development and process optimization are necessary to expand the range of materials suitable for SLM 3D printing.
6.3 Build Failures
SLM 3D printing is not immune to build failures, which can occur due to issues such as powder contamination, inadequate laser power, or insufficient heat distribution. These failures can result in wasted time, material, and resources. Continual process monitoring and optimization are crucial to minimize build failures and improve overall productivity.
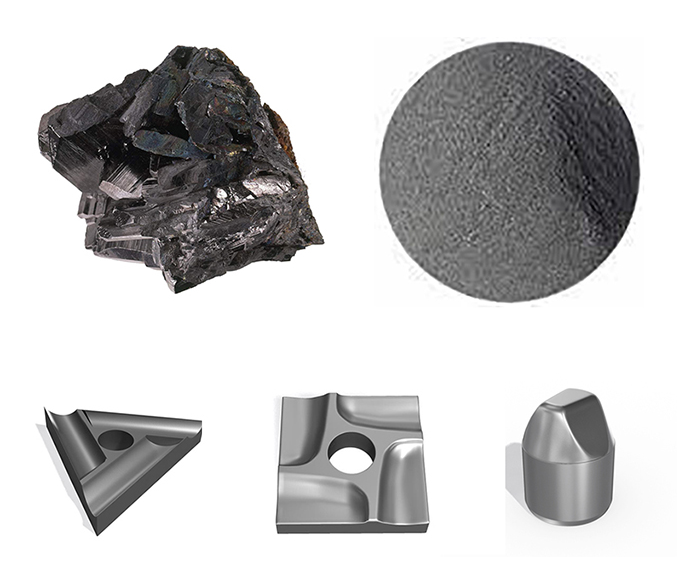
7. Future Trends in SLM 3D Printing
The field of SLM 3D printings is evolving rapidly, and several trends are shaping its future:
7.1 Improved Materials
Ongoing research focuses on developing new alloys and composite materials specifically designed for SLM 3D printing. These materials aim to offer enhanced mechanical properties, better heat resistance, and improved biocompatibility. The availability of a broader range of materials will further expand the applications of SLM 3D printings.
7.2 Enhanced Speed and Precision
Efforts are being made to increase the printing speed and improve the accuracy and resolution of SLM 3D printing systems. Advancements in laser technology, scanning techniques, and process optimization will enable faster production times and finer details, making SLM 3D printing even more versatile and efficient.
7.3 Integration of AI and Machine Learning
The integration of artificial intelligence (AI) and machine learning (ML) algorithms is set to revolutionize SLM 3D printing. These technologies can optimize the printing process, predict and prevent build failures, and automate post-processing tasks. AI and ML will play a vital role in improving the overall efficiency, productivity, and quality control in SLM 3D printing.
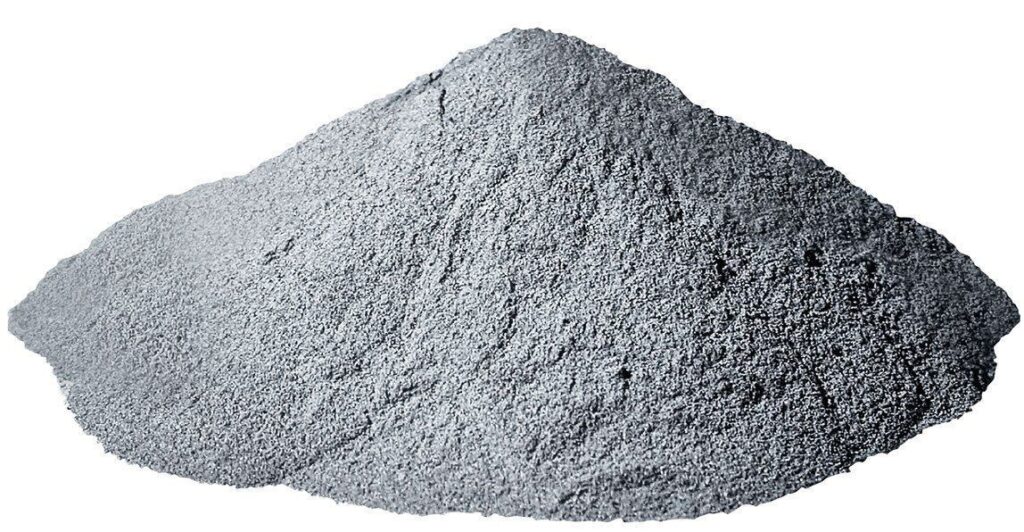
8. Conclusion
SLM 3D printing has emerged as a powerful additive manufacturing technique with numerous advantages and applications across industries. Its ability to produce complex geometries, utilize a variety of materials, and enable rapid prototyping has revolutionized the manufacturing landscape. Despite some challenges, ongoing advancements in materials, process optimization, and post-processing techniques are paving the way for a promising future in SLM 3D printing. As technology continues to evolve and integrate with AI and ML, we can expect even greater advancements and innovations in this exciting field.
FAQs
1. Can SLM 3D printing be used with non-metallic materials?
Currently, SLM 3D printings primarily focuses on metallic materials. However, there are other additive manufacturing techniques, such as selective laser sintering (SLS), that can handle non-metallic materials like polymers and ceramics.
2. Is SLM 3D printing cost-effective for small-scale production?
SLM 3D printings is particularly beneficial for small-scale production, as it eliminates the need for expensive tooling and molds. It allows for cost-efficient production of customized and low-volume parts, making it a viable option for small-scale manufacturing.
3. Can SLM 3D printing achieve high surface quality?
While SLM 3D printings can achieve good surface quality, post-processing steps are often required to improve the final finish. Techniques such as polishing, machining, and surface treatments can be employed to achieve the desired surface quality.
4. Are there any size limitations in SLM 3D printing?
SLM 3D printing systems come with different build volumes, which determine the maximum size of the printed objects. However, large-scale objects may require additional considerations, such as support structures and build time optimization.
5. What are the environmental implications of SLM 3D printings?
SLM 3D printing has the potential to reduce material waste compared to traditional manufacturing processes. However, it is important to consider the energy consumption of the equipment and the proper disposal of metal powders and waste materials. Efforts are being made to improve sustainability aspects and minimize the environmental impact of SLM 3D printing.