1. Introduction
In recent years, the field of additive manufacturing has witnessed significant advancements, revolutionizing the way we produce complex components. One material that has gained considerable attention in this domain is titanium. With its exceptional properties and growing demand across various industries, titanium additive manufacturing has emerged as a game-changer. This article explores the concept of titanium additive manufacturing, its benefits, applications, challenges, and future prospects.
2. What is Titanium Additive Manufacturing?
Titanium additive manufacturing, also known as titanium 3D printing, refers to the process of fabricating objects layer by layer using titanium alloys. Unlike traditional manufacturing techniques, which involve subtractive methods like cutting and molding, additive manufacturing builds the desired object from the ground up, resulting in intricate and highly customizable designs.
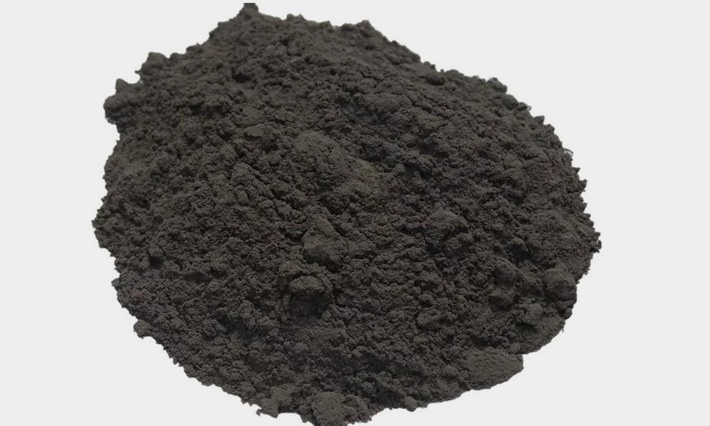
3. Benefits of Titanium Additive Manufacturing
3.1 Enhanced Design Flexibility
Titanium additive manufacturing offers unparalleled design freedom, allowing engineers and designers to create complex geometries that were previously impossible or cost-prohibitive. This technology eliminates many of the constraints associated with traditional manufacturing processes, empowering innovators to unleash their creativity and push the boundaries of design.
3.2 Lightweight and Strong Structures
Titanium is renowned for its exceptional strength-to-weight ratio, making it an ideal material for industries where weight reduction is crucial. By leveraging additive manufacturing, engineers can optimize component designs, creating lightweight structures without compromising strength or durability. This benefit has significant implications for industries such as aerospace, automotive, and sports equipment manufacturing.
3.3 Cost-Effectiveness
While the initial setup costs for titanium additive manufacturing can be substantial, it offers long-term cost advantages. Traditional manufacturing methods often involve extensive tooling and machining, leading to higher production costs, especially for complex parts. Additive manufacturing reduces these expenses by eliminating the need for specialized tooling, reducing waste, and enabling efficient use of materials.
3.4 Reduced Waste and Environmental Impact
Traditional manufacturing processes often generate significant amounts of waste due to material removal and excess inventory. Titanium additive manufacturing minimizes waste by using only the necessary amount of material for each build, resulting in substantial material savings. Additionally, this technology can facilitate the recycling and reusability of titanium powders, further reducing the environmental footprint associated with manufacturing processes.
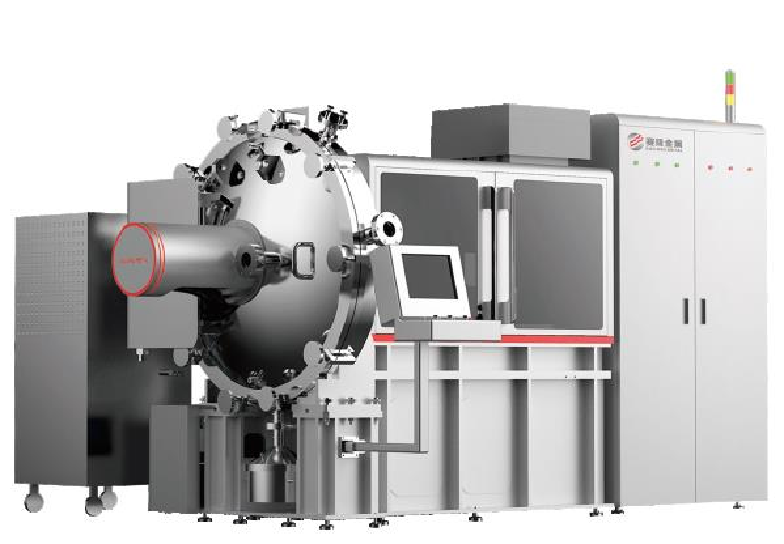
4. Applications of Titanium Additive Manufacturing
4.1 Aerospace Industry
The aerospace industry has embraced titanium additive manufacturing for the production of critical components, such as turbine blades, brackets, and structural parts. The lightweight nature, high strength, and heat resistance of titanium make it an ideal choice for aerospace applications. Additive manufacturing allows for the creation of complex geometries and internal lattice structures, enhancing component performance while reducing weight.
4.2 Medical and Dental Implants
Titanium has long been used in the medical field due to its biocompatibility and corrosion resistance. Additive manufacturing enables the production of patient-specific implants with intricate designs, ensuring a better fit and enhanced functionality. From orthopedic implants to dental prosthetics, titanium additive manufacturing has revolutionized the medical industry, improving patient outcomes and reducing surgery time.
4.3 Automotive Industry
The automotive sector is increasingly turning to titanium additive manufacturing for lightweighting vehicles and improving fuel efficiency. Additively manufactured titanium parts can be found in engine components, exhaust systems, suspension parts, and even entire chassis structures. By reducing weight and optimizing designs, automakers can enhance performance and reduce emissions.
4.4 Industrial and Tooling Applications
Titanium additive manufacturing is gaining traction in various industrial applications, including tooling, jigs, and fixtures. By leveraging the design flexibility of additive manufacturing, complex tooling structures can be created to meet specific manufacturing needs. This technology allows for rapid prototyping, customization, and optimization of tooling systems, improving overall manufacturing efficiency.
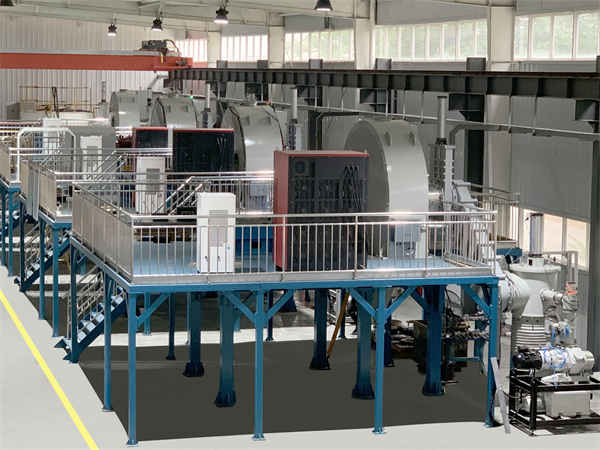
5. Challenges and Limitations of Titanium Additive Manufacturing
5.1 Material Properties and Quality Control
Ensuring consistent material properties and quality control in titanium additive manufacturing can be challenging. Variations in powder quality, process parameters, and post-processing techniques can impact the final part’s mechanical properties. Robust quality control measures and material characterization are necessary to mitigate these challenges and ensure reliable and repeatable production.
5.2 Production Speed and Scale
While additive manufacturing offers unique design possibilities, production speed remains a limitation, especially for large and complex parts. Building intricate structures layer by layer is a time-consuming process, making it less suitable for mass production. However, advancements in printing technologies and process optimization are gradually addressing these limitations, enabling faster production speeds and larger-scale applications.
5.3 Post-Processing and Finishing
Additively manufactured titanium parts often require post-processing steps, such as heat treatment, surface finishing, and machining, to achieve the desired specifications and aesthetics. These additional steps add complexity, time, and cost to the manufacturing process. Streamlining post-processing techniques and developing in-situ finishing capabilities are ongoing areas of research to overcome these challenges.
5.4 Regulatory and Certification Requirements
Certain industries, such as aerospace and medical, have stringent regulatory and certification requirements. The adoption of titanium additive manufacturing in these industries necessitates thorough testing, validation, and compliance with established standards. Meeting these requirements is essential to ensure the safety and reliability of additively manufactured titanium components.
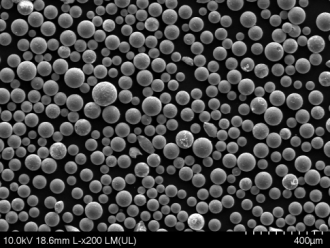
6. Future Outlook and Innovations in Titanium Additive Manufacturing
The future of titanium additive manufacturing holds immense potential for advancements and innovation. Researchers and industry experts are continuously exploring new materials, process optimization techniques, and design methodologies to overcome the current limitations. Additionally, advancements in multi-material printing, in-situ monitoring, and automation are expected to further enhance the capabilities of titanium additive manufacturing, opening up new possibilities in various industries.
7. Conclusion
Titanium additive manufacturing has revolutionized the manufacturing landscape, offering numerous benefits across industries. From enhanced design flexibility and lightweight structures to cost savings and reduced waste, the advantages of this technology are substantial. Despite the challenges associated with material properties, production speed, and post-processing, ongoing research and innovation are driving the field forward. As titanium additive manufacturing continues to evolve, we can expect further breakthroughs, expanding its applications and unlocking new horizons.
FAQs
Q1. Is titanium additive manufacturing expensive? While the initial setup costs can be high, titanium additive manufacturing offers long-term cost advantages through reduced waste, efficient material utilization, and elimination of specialized tooling.
Q2. Can titanium additive manufacturing produce large-scale parts? Additive manufacturing of large-scale titanium parts is challenging due to production speed and build volume limitations. However, advancements in printing technologies are gradually enabling larger-scale applications.
Q3. Are additively manufactured titanium parts as strong as traditionally manufactured parts? Yes, additively manufactured titanium parts can exhibit comparable strength to traditionally manufactured parts. However, material properties and quality control measures play a crucial role in ensuring consistent mechanical properties.
Q4. What industries benefit from titanium additive manufacturing? Titanium additive manufacturing finds applications in industries such as aerospace, medical and dental, automotive, and industrial tooling, among others.
Q5. Is titanium additive manufacturing environmentally friendly? Yes, titanium additive manufacturing reduces waste by using only the necessary amount of material and enables recycling of titanium powders, resulting in a reduced environmental impact compared to traditional manufacturing methods.