Overview of 3D Printing Metal Powder
3D printing metal powder, also known as metal additive manufacturing (AM), is a transformative technology that allows complex metal parts to be created directly from digital designs. Unlike traditional subtractive manufacturing that cuts away material, 3D printing builds up parts layer-by-layer using metal powder as the raw material.
Some key features of 3D printing metal powder include:
Technology | Description |
---|---|
Powder Bed Fusion | A laser or electron beam fuses regions of a powder bed to create parts layer-by-layer |
Directed Energy Deposition | A focused heat source melts metal powder or wire as it is deposited to build up parts |
Binder Jetting | A liquid bonding agent selectively joins metal powder particles in each layer |
Compared to traditional manufacturing, 3D printing metal enables:
- More design freedom for complex, organic shapes
- Customized parts on-demand without specialized tooling
- Reduced waste from subtractive methods
- Consolidated assemblies printed as one part
- Lighter weight from topology optimization
As the technology matures, metal 3D printing is transitioning from prototyping to production across industries like aerospace, automotive, medical, and energy.
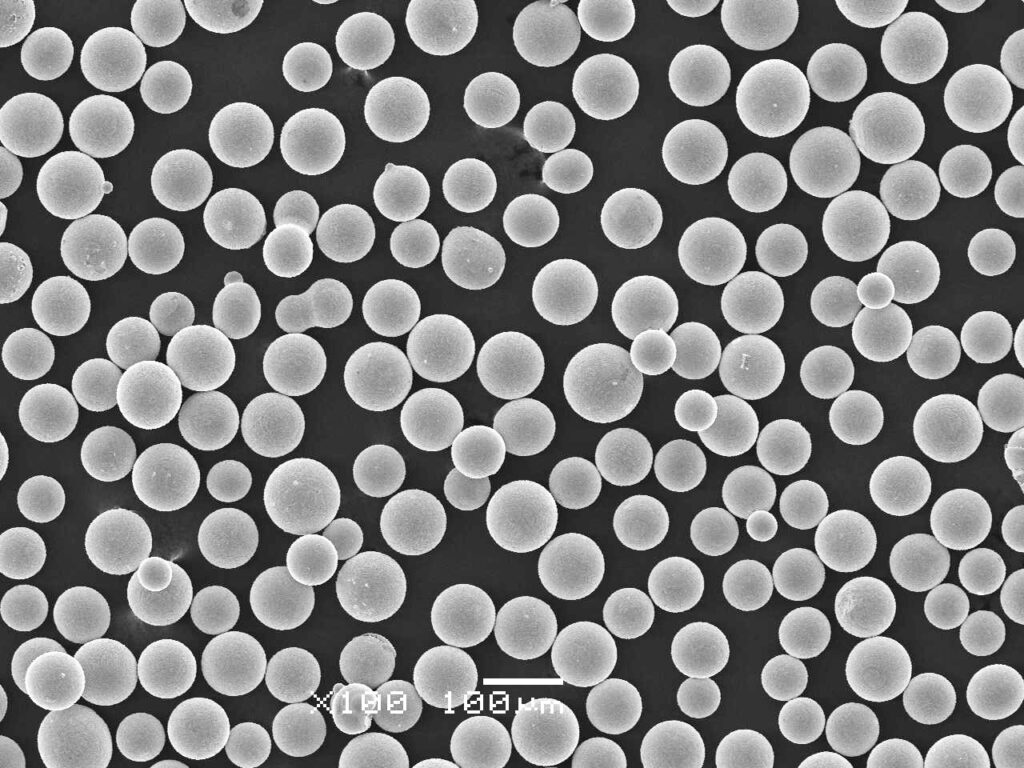
Applications of 3D Printing Metal Powder
3D printing with metal powder has a diverse range of applications across industries. Some of the main uses include:
Industry | Applications |
---|---|
Aerospace | Engine parts, airframe components, turbomachinery |
Automotive | Lightweighting components, custom tooling, performance parts |
Medical | Dental copings, implants, surgical instruments |
Industrial | End-use production parts, conformal cooling, tooling |
The technology is ideal for low-volume production of complex, high-value metal parts with custom geometries. Key advantages over traditional manufacturing include:
- Parts consolidation – Many assembled components can be printed as one consolidated part
- Mass customization – Personalized metal parts can be made on-demand
- Rapid prototyping – Designs can be quickly iterated and validated
- Reduced waste – Only metal powder required for each part is used
- Lightweighting – Organic geometries with lattices and thin walls reduce weight
As the quality and repeatability of printed metal parts improves, 3D printing is transitioning from prototyping to end-use production applications.
Metal Powders for 3D Printing
A wide range of metals can be used for powder bed fusion and directed energy deposition 3D printing. Common alloys include:
Alloy | Characteristics | Applications |
---|---|---|
Stainless steel | Corrosion resistance, high strength | Aerospace, automotive, industrial |
Aluminum | Lightweight, strong, machinable | Aerospace, automotive |
Titanium | Biocompatible, high strength-to-weight | Aerospace, medical |
Cobalt Chrome | Wear resistance, biocompatibility | Medical, dental |
Nickel Alloys | Heat resistance, corrosion resistance | Aerospace, energy |
The powder is spherical in shape, ranging from 10-100 microns in diameter. Key powder characteristics include:
- Particle size distribution – Affects packing density, surface finish
- Morphology – Spherical particles with smooth surfaces fuse best
- Flowability – Ensures uniform layers and material delivery
- Apparent density – Higher density improves mechanical properties
- Reuse – Powder can be collected and reused to reduce material costs
Most metals require an inert printing environment to prevent oxidation. The build chamber is flooded with argon or nitrogen gas during printing.
Metal 3D Printer Specifications
3D printers for metal powder are industrial systems designed for 24/7 operation. Typical specifications include:
Parameter | Typical Range |
---|---|
Build volume | 100-500 mm x 100-500 mm x 100-500 mm |
Layer thickness | 20-100 microns |
Laser power | 100-500 W |
Scanning speed | Up to 10 m/s |
Beam diameter | 50-100 microns |
Inert gas | Argon, nitrogen |
Powder handling | Closed-loop recycling systems |
Other accessories like powder recovery systems and post-processing equipment may be required for a complete workflow. The system requirements vary based on the metal alloys printed and end-use applications.
Metal 3D Printing Standards and Design
To ensure high quality printed parts, metal 3D printing has several key design standards:
Standard | Description |
---|---|
STL File Format | Standard file format for representing 3D model geometries |
Wall Thickness | Minimum wall thickness of ~0.3-0.5 mm to avoid failures |
Supported Angles | Overhangs require angles over 30-45° to be supported |
Escape Holes | Needed to remove excess powder from internal channels |
Surface Finish | As-printed surface is rough, post-processing improves finish |
Designers should account for factors like residual stresses, anisotropic material properties, and powder removal to create successful metal printed parts. Simulation software helps validate designs digitally before printing.
Suppliers of Metal 3D Printing Systems
Major suppliers of industrial metal 3D printing equipment include:
Company | Models | Cost Range |
---|---|---|
EOS | FORMIGA, EOS M series | $100,000 – $1,000,000+ |
3D Systems | ProX, DMP series | $100,000 – $1,000,000+ |
GE Additive | Concept Laser M2, X Line | $400,000 – $1,500,000+ |
Trumpf | TruPrint 1000, 5000, 7000 series | $500,000 – $1,500,000+ |
SLM Solutions | SLM 500, SLM 800 | $400,000 – $1,500,000+ |
The systems range from small, entry-level metal printers to large-format, industrial machines. Costs vary based on build volume, materials, and productivity. Additional expenses include installation, training, maintenance contracts, and powder materials.
Choosing a Metal 3D Printing Supplier
When selecting an industrial metal 3D printing system, key factors to consider include:
Factor | Description |
---|---|
Build volume | Match to expected part sizes, allowances for support structures |
Materials | Range of metals and alloys supported |
Productivity | Build rate, utilization, total cost of operations |
Powder handling | Closed-loop, recycling capabilities |
Software | Capabilities for support, simulation, optimization |
Post-processing | Automated vs. manual removal of supports, surface finishing |
Training | Installation support, operator training, maintenance procedures |
Service | Maintenance contracts, response time, reliability |
Pilot builds, site visits, and customer references help validate printer performance for intended applications. Total cost of ownership models factor in all expenses over a system’s lifetime.
Metal 3D Printing Compared to Traditional Manufacturing
3D printing metal parts has advantages and limitations compared to conventional manufacturing processes like CNC machining, casting, and metal injection molding:
3D Printing Metal | Traditional Manufacturing | |
---|---|---|
Cost per part | High at low volumes, decreases with higher volumes | Lower at high volumes, high initial tooling costs |
Part complexity | No added costs for complex geometries | Increased costs for complex CNC programs or molds |
Build rate | Slower, depends on part size and printer | Typically faster build rates |
Materials | Limited material options, isotropic properties | Broader material selection, often anisotropic |
Post-processing | Support removal, machining, finishing often required | May require some finishing steps |
Scalability | Smaller build volumes limit scaling | Mass production with no volume limitations |
Design freedom | Unlimited geometric complexity | Design restrictions based on process limitations |
The ideal production scenario often uses both 3D printing and traditional manufacturing synergistically based on application requirements.
Post-Processing Methods for Metal Printed Parts
After printing, 3D metal parts typically require post-processing to achieve the desired finish and tolerances:
Method | Description |
---|---|
Support removal | Chemically dissolving or mechanically removing support structures |
Stress relieving | Heat treating to relieve residual stresses from printing |
Hot isostatic pressing | Applies heat and pressure to densify parts |
Surface finishing | Machining, grinding, polishing, blasting to improve surface finish |
Plating | Electroplating for corrosion protection or improved wear resistance |
Automated support removal, CNC machining, and surface finishing systems tailored for 3D printed metal parts help streamline post-processing. These steps are essential for meeting the requirements of final part applications.
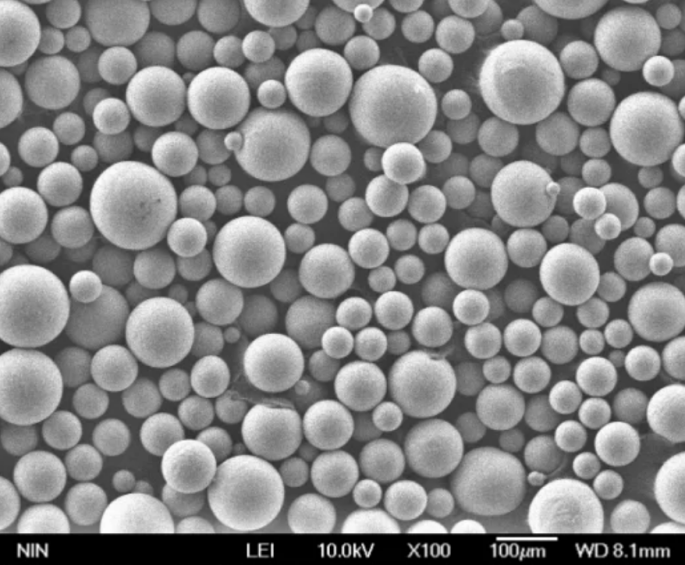
Operating and Maintaining a Metal 3D Printer
To sustain robust production with metal additive manufacturing, proper operation and preventative maintenance is crucial:
Activity | Description |
---|---|
Loading powder | Carefully measure and refill powder hoppers using PPE |
Levelling build plate | Ensure build plate is level prior to prints for uniform layers |
Monitoring prints | Check for errors like powder spatter, smoking or distorted parts |
Parameter optimization | Tune settings like laser power, speed, hatch spacing for better density |
Changing filters | Replace gas and particle filters based on usage intervals |
Cleaning and testing | Regularly clear dust and debris, test laser power metering |
Replacing worn parts | Change recoater blades, wipers, seals when worn |
Staff training and preventative maintenance contracts help maximize printer uptime and utilization for production applications.
FAQ
Question | Answer |
---|---|
How accurate is metal 3D printing? | Dimension accuracy is around ±0.1-0.2% with ±50 micron precision on features. Post-processing improves tolerance further. |
What surface finish can be achieved? | As-printed surface is quite rough at 5-15 microns Ra. Machining and polishing can achieve under 1 micron Ra finish. |
What metals can be 3D printed? | Common alloys are stainless steel, aluminum, titanium, nickel alloys, cobalt-chrome. New alloys are continually being introduced. |
How porous are metal printed parts? | Density reaches over 99% for most metals with proper parameters. Hot isostatic pressing further densifies parts. |
What support structures are required? | Support lattices are printed where needed and removed after printing. Strategic design minimizes their use. |
What post-processing is required? | Support removal, stress relieving, surface finishing, and inspection are commonly needed steps. |
know more 3D printing processes
Additional FAQs on 3D Printing Metal Powder
1) How do I select the right metal powder for my application?
Match alloy to service needs: stainless steel for corrosion/strength, aluminum for lightweight thermal parts, titanium for high strength-to-weight and biocompatibility, nickel alloys for heat/corrosion, and CoCr for wear/medical. Then refine by particle size distribution (PSD), sphericity, and interstitial limits required by your process.
2) What powder specifications matter most for LPBF quality?
Spherical morphology, PSD D10–D90 ≈ 15–45 μm (material dependent), low O/N/H, high flowability (Hall/Carney), consistent apparent/tap density, and minimal satellites/contamination. Conform to ISO/ASTM 52907 where possible.
3) How many reuse cycles are safe for 3D printing metal powder?
It’s application- and alloy-dependent. Establish a reuse plan with blend-back ratios (e.g., 20–50% recycled), sieving after each build, O/N/H checks, PSD monitoring, and mechanical coupon verification. Retire powder when specs drift or defect rates rise.
4) What are typical as-printed tolerances and surface finishes?
LPBF often achieves ±0.1–0.3 mm plus ±0.1% of feature size; as-built Ra ~6–20 μm. Post-processing (machining, blasting, electropolish) can reach Ra <0.8 μm and tighter tolerances.
5) How do in-situ monitoring tools help production?
Coaxial cameras and melt pool sensors detect lack-of-fusion, spatter, or contour defects in real time. Correlating these signals to CT and mechanical outcomes supports part acceptance, reducing inspection burden on stable geometries.
2025 Industry Trends in 3D Printing Metal Powder
- Multi-laser LPBF normalization: 8–12 laser platforms and smarter tiling improve throughput 20–40% across steels, Ti, and Ni alloys.
- Copper- and aluminum-ready systems: Blue/green lasers and scan strategies expand use of high-reflectivity metals for electronics cooling and e-mobility.
- Binder jetting maturity: Sinter/HIP playbooks deliver 95–99% density in steels, Inconel, and copper for larger, cost-sensitive parts.
- Powder governance: Material passports track powder genealogy; inline O2/moisture monitoring and automated sieving standardize quality.
- Sustainability: Higher recycled content, argon recirculation, and EPDs gain traction in aerospace/medical supply chains.
2025 Metric (Metal AM) | Typical Range/Value | Why it matters | Source |
---|---|---|---|
LPBF relative density (common alloys; with HIP) | 99.5–99.9% | Aerospace/medical-grade integrity | Peer-reviewed AM studies; OEM notes |
Build rate (12‑laser LPBF, 40 μm layers) | 35–70 cm³/h per system | Cost per part reduction | OEM application notes |
Binder‑jetted final density (steel/Ni/Cu after sinter/HIP) | 95–99% | Larger parts at lower cost | Vendor case data |
Typical LPBF PSD | D10–D90 ≈ 15–45 μm | Stable recoating and melt pool | ISO/ASTM 52907 |
Powder oxygen spec (Ti-64 ELI) | ≤0.13 wt% O | Ductility/biocompatibility | ASTM F136/F3001 |
Indicative AM‑grade powder price | ~$20–$500/kg (alloy/route dependent) | Budgeting and sourcing | Market trackers/suppliers |
Authoritative references and further reading:
- ISO/ASTM 52907 (AM feedstock), 52910 (DFAM), 52931 (LPBF metals): https://www.astm.org and https://www.iso.org
- NIST AM Bench and datasets: https://www.nist.gov
- ASM Handbook (Powder Metallurgy; Materials Systems): https://www.asminternational.org
- NFPA 484 (combustible metals safety): https://www.nfpa.org
Latest Research Cases
Case Study 1: Multi‑Laser LPBF Lattice Heat Exchanger in Stainless Steel (2025)
Background: An industrial OEM needed a compact, corrosion‑resistant heat exchanger with reduced build time.
Solution: Printed 316L on a 12‑laser LPBF system with coordinated tiling, in‑situ melt pool monitoring, and automated sieving/powder genealogy. Post‑HIP and surface passivation.
Results: 27% cycle time reduction, >99.8% density post‑HIP, pressure drop lowered 15% vs. baseline, and a 35% reduction in CT inspection volume after correlation study.
Case Study 2: Binder‑Jetted Copper EMI Shielding Enclosures (2024)
Background: An avionics supplier required high‑conductivity enclosures with lower cost than LPBF.
Solution: Binder jetting spherical copper powder (fine PSD), hydrogen sinter and selective HIP; nickel flash on contact pads.
Results: 97–98% density, shielding effectiveness improved by 9–12 dB (10 MHz–1 GHz) vs. machined aluminum, and 30% lead‑time reduction.
Expert Opinions
- Prof. John Hart, Professor of Mechanical Engineering, MIT
Key viewpoint: “In‑situ sensing combined with material passports is enabling statistically defensible acceptance for serial metal AM.” - Dr. Laura Schmidt, Head of Additive Manufacturing, Fraunhofer IAPT
Key viewpoint: “Process windows for copper and nickel superalloys have widened with wavelength‑optimized lasers and advanced scan strategies, broadening production applications.” - Dr. Brent Stucker, AM standards contributor and industry executive
Key viewpoint: “Hybrid workflows—AM preforms plus HIP/forging—deliver wrought‑like properties while preserving AM’s design freedom.”
Citations for expert profiles:
- MIT: https://meche.mit.edu
- Fraunhofer IAPT: https://www.iapt.fraunhofer.de
- ASTM AM Center of Excellence: https://amcoe.org
Practical Tools and Resources
- Standards and safety
- ISO/ASTM 52907, 52910, 52931; NFPA 484
- Powder characterization and QC
- LECO O/N/H analyzers: https://www.leco.com
- Laser diffraction PSD (e.g., Malvern), SEM imaging at accredited labs
- CT scanning best practices (ASTM E1441)
- Design and simulation
- Ansys Additive/Mechanical; Simufact Additive; nTopology for lattices/conformal cooling
- Market and data
- Senvol Database (machines/materials): https://senvol.com/database
- USGS Mineral Commodity Summaries: https://pubs.usgs.gov/periodicals/mcs
- NIST AM Bench datasets: https://www.nist.gov
Last updated: 2025-08-21
Changelog: Added 5 targeted FAQs, a 2025 trends table with metrics and sources, two recent case studies, expert viewpoints with credible affiliations, and a curated tools/resources list for 3D Printing Metal Powder.
Next review date & triggers: 2026-02-01 or earlier if ISO/ASTM standards update, major OEMs release new multi‑laser parameter sets or copper-capable platforms, or powder pricing/availability shifts >10% QoQ.