Introduction
In the realm of modern manufacturing and engineering, the demand for high-quality metal powders has surged due to the rapid growth of industries like aerospace, automotive, and electronics. Metal powder atomization has emerged as a groundbreaking technique to produce finely divided, spherical metal particles with exceptional properties. This article delves into the world of metal powder atomization, exploring its process, advantages, applications, challenges, and future possibilities.
What is Metal Powder Atomization?
Metal powder atomization is a powder production process that converts molten metal into fine droplets, which rapidly solidify into spherical particles. The resulting metal powders exhibit consistent particle size distribution and enhanced properties, making them ideal for various industrial applications.
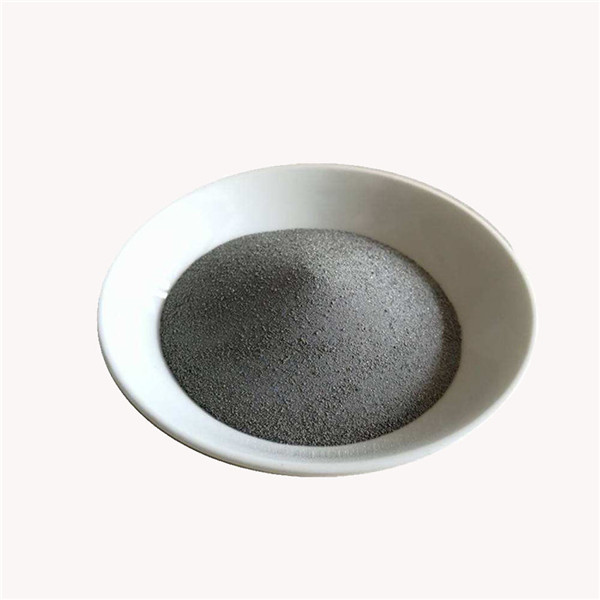
The Atomization Process
Gas Atomization
Gas atomization is one of the most prevalent methods, wherein high-pressure gas is utilized to break up the molten metal stream into fine droplets. The gas can be nitrogen, argon, or even hydrogen, depending on the metal’s reactivity.
Water Atomization
Water atomization involves using high-pressure water jets to fragment the molten metal into droplets. This method is particularly suitable for producing non-reactive metals and alloys.
Plasma Atomization
Plasma atomization employs a high-temperature plasma arc to vaporize the metal, followed by rapid cooling and solidification to form powdered particles. This technique is well-suited for refractory metals and complex alloys.
Advantages of Metal Powder Atomization
Controlled Particle Size Distribution
Metal powder atomization allows precise control over particle size distribution, resulting in uniform powder that enhances the material’s performance in various applications.
Enhanced Powder Purity
The atomization process reduces the presence of impurities in metal powders, leading to higher purity levels, a crucial aspect in industries where material integrity is paramount.
Improved Powder Flowability
The spherical morphology achieved through atomization ensures excellent flowability of metal powders, making them easy to handle and process during production.
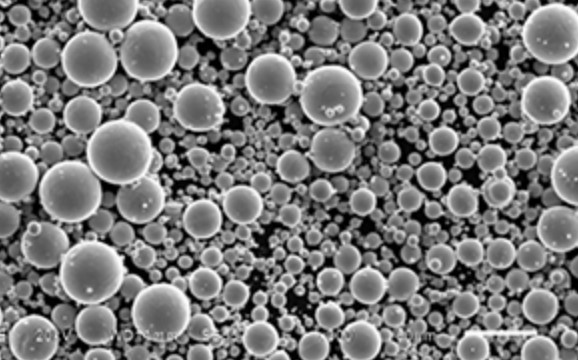
Applications of Metal Powder Atomization
Additive Manufacturing
The advent of metal 3D printing has revolutionized manufacturing, and metal powder atomization plays a pivotal role in providing the high-quality powders needed for additive manufacturing processes.
Powder Metallurgy
Powder metallurgy techniques, such as pressing and sintering, utilize atomized metal powders to create complex parts with excellent mechanical properties.
Thermal Spray Coatings
Metal powders produced through atomization are widely used in thermal spray coatings for corrosion protection, wear resistance, and thermal barriers.
Brazing and Sintering
The unique properties of atomized metal powders are exploited in brazing and sintering applications to achieve strong, durable joints in various assemblies.
Metal Injection Molding (MIM)
MIM, a process akin to plastic injection molding, utilizes atomized metal powders to fabricate intricate metal components for the medical, automotive, and consumer goods sectors.
Types of Metals Used in Atomization
Ferrous Metals
Ferrous metals, including iron, steel, and stainless steel, are commonly atomized to produce powders used in a wide range of industries, from automotive components to construction materials.
Non-Ferrous Metals
Non-ferrous metals, such as aluminum, copper, and titanium, are also frequently atomized, catering to industries like aerospace, electronics, and defense.
Reactive Metals
Reactive metals like zirconium, tantalum, and magnesium are more challenging to atomize due to their high reactivity. However, advancements in atomization techniques have made it possible to produce powders from these materials for specialized applications.
Factors Affecting Atomization
Metal Composition
The choice of metal or alloy significantly impacts the atomization process, with varying reactivity, melting points, and viscosity affecting droplet formation.
Atomization Gas/Water/Plasma Selection
Selecting the appropriate atomization medium is crucial to achieve the desired particle characteristics, as different media influence the cooling rate and solidification of droplets.
Atomization Chamber Design
The design of the atomization chamber plays a vital role in ensuring efficient droplet breakup and cooling, affecting the final powder’s quality and yield.
Atomization Pressure and Temperature
Controlling atomization pressure and temperature enables precise tuning of particle size, morphology, and properties, making it a critical aspect of the process.
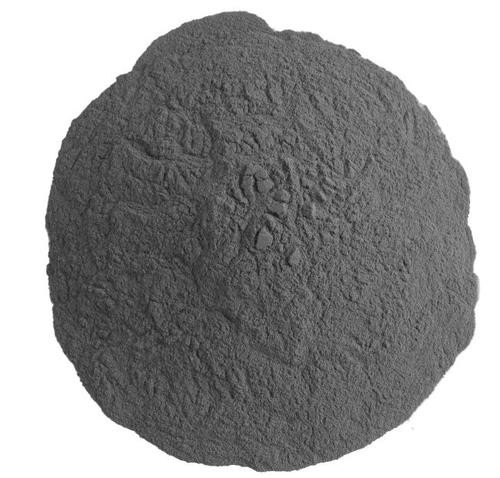
Challenges in Metal Powder Atomization
Oxidation and Contamination
During atomization, exposure to reactive gases or moisture can lead to unwanted oxidation and contamination of the metal powders, affecting their performance.
Particle Agglomeration
Agglomeration, the clumping of particles, can occur during atomization, hindering powder flowability and dispersion in various applications.
Cost and Energy Consumption
Metal powder atomization can be energy-intensive and costly, making it essential to explore energy-efficient methods and cost-effective production routes.
Innovations and Future Prospects
Alloy Development
Advancements in alloy development, tailored specifically for atomization processes, will lead to novel materials with superior properties and broader applications.
Nanoparticle Production
Research in producing nanoparticles through atomization will open up new possibilities in fields like catalysis, electronics, and biomedicine.
Hybrid Atomization Techniques
Combining different atomization methods or integrating atomization with other processes may yield hybrid techniques that enhance powder properties and process efficiency.
Environmental Considerations
Waste Management
Efficient waste management strategies need to be implemented to minimize the environmental impact of atomization, especially for reactive or hazardous metals.
Energy Efficiency
Continued efforts to improve energy efficiency in atomization processes will contribute to sustainable manufacturing practices and reduced carbon footprints.
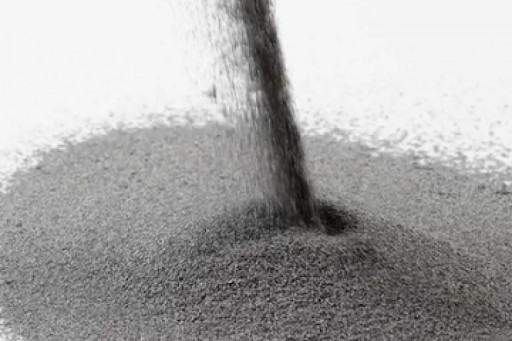
Conclusion
Metal powder atomization has revolutionized the production of metal powders, unlocking a myriad of possibilities in industries spanning from aerospace to medical. The ability to control particle size distribution, enhance powder purity, and improve flowability has propelled the adoption of atomized powders across diverse applications. As technology advances, addressing challenges and exploring innovations, metal powder atomization will continue to play a pivotal role in shaping the future of materials engineering and manufacturing.
FAQs
What is the primary application of metal powder atomization?
Metal powder atomization finds primary application in industries like additive manufacturing, powder metallurgy, and thermal spray coatings.
Can metal powder atomization be used for large-scale production?
Yes, metal powder atomization can be scaled up for large-scale production, catering to the demands of various industries.
What metals are commonly atomized for 3D printing?
Materials like titanium, aluminum, and stainless steel are commonly atomized for 3D printing using metal powder bed fusion techniques.
Is metal powder atomization a sustainable process?
While it can be energy-intensive, efforts are being made to improve the energy efficiency and sustainability of metal powder atomization processes.
How does metal powder atomization compare to other powder production methods?
Metal powder atomization offers distinct advantages in producing spherical powders with controlled properties, setting it apart from traditional powder production methods like mechanical crushing and milling.
know more 3D printing processes
Additional FAQs About Metal Powder Atomization
1) Which atomization route is best for additive manufacturing powders and why?
- Inert gas atomization and vacuum gas atomization (including EIGA/PREP) are preferred because they yield highly spherical particles with tight PSD, low oxygen/nitrogen, and fewer satellites/hollows—key for PBF/DED flowability and density.
2) How do process parameters influence particle size distribution (PSD)?
- Higher gas-to-metal ratio and superheat reduce median size (D50) and narrow PSD; nozzle geometry and chamber pressure affect breakup mode and satellite formation; quench rate impacts surface roughness and hollows.
3) Can water‑atomized powders be used for AM?
- Viable for binder jetting followed by sinter/HIP, but generally unsuitable for PBF without extensive conditioning due to irregular shape and higher oxide. They are widely used in MIM and PM components.
4) What are “satellites” and “hollow particles,” and why do they matter?
- Satellites are small particles welded onto larger ones; hollows are shells formed by gas entrapment. Both degrade flowability, packing, and can seed defects in AM parts. Image analysis and CT quantify and help control them.
5) How do suppliers minimize oxidation and contamination during atomization?
- Use high‑purity feedstock, inert/vacuum atmospheres, low O2/H2O dew points, closed‑loop argon recirculation, clean refractories, and rapid, controlled cooling; post‑processing includes sieving, de‑dusting, and air elutriation.
2025 Industry Trends for Metal Powder Atomization
- Quality transparency: CoAs increasingly include sphericity/satellite % (image analysis) and CT‑measured hollow fraction alongside O/N/H and PSD.
- Energy efficiency: Argon recirculation, higher thermal recovery from off‑gas, and optimized gas-to-metal ratios trim operating costs 5–12%.
- Regional capacity: New atomizers in NA/EU/APAC reduce lead times and logistics risk; greater onshore supply for aerospace/medical alloys.
- Binder jet surge: Engineered bimodal PSDs for steels and Cu alloys enable 97–99.5% sintered density, with HIP for critical parts.
- Advanced monitoring: Real‑time melt superheat control, off‑gas spectroscopy, and machine vision for plume diagnostics reduce satellite formation.
2025 Market and Technical Snapshot (Metal Powder Atomization)
Metric (2025) | Typical Value/Range | YoY Change | Notes/Source |
---|---|---|---|
Gas‑atomized 316L price | $10–$18/kg | −2–5% | Supplier indices, distributor quotes |
Gas‑atomized Ti‑6Al‑4V price | $150–$280/kg | −3–7% | Alloy/PSD dependent |
Common AM PSD cuts (PBF) | 15–45 µm, 20–63 µm | Stable | OEM guidance |
Sphericity (image analysis) | ≥0.93–0.98 | Slightly up | Supplier CoAs |
Satellite fraction (image) | ≤3–6% | Down | Process tuning, plume control |
CT hollow particle fraction | 0.5–1.5% | Down | PREP/EIGA/VGA adoption |
Validated AM powder reuse | 5–10 cycles | Up | O/N/H trending + sieving programs |
Argon recirculation savings | 15–30% Ar use reduction | Up | Energy/LCA initiatives |
Indicative sources:
- ISO/ASTM 52907 (Metal powders), 52908 (AM process qualification): https://www.iso.org | https://www.astm.org
- MPIF standards and buyer guides: https://www.mpif.org
- NIST AM Bench and powder metrology: https://www.nist.gov
- ASM Handbooks (Powder Metallurgy; Additive Manufacturing): https://www.asminternational.org
- NFPA 484 (Combustible metal dusts): https://www.nfpa.org
Latest Research Cases
Case Study 1: Closed‑Loop Gas‑to‑Metal Ratio Reduces Satellites in 316L (2025)
Background: A European atomizer faced high satellite content causing PBF recoater stops at customers.
Solution: Implemented real‑time plume imaging, closed‑loop gas‑to‑metal ratio, and tighter melt superheat control; added post‑classification air elutriation.
Results: Satellite fraction fell from 8.0% to 3.0% (image analysis); Hall flow improved 14%; AM relative density improved from 99.4% to 99.8%; customer stoppages reduced 40%.
Case Study 2: Vacuum Gas Atomization with CT Screening for Ti‑6Al‑4V (2024)
Background: An aerospace OEM required lower hollow fraction to tighten fatigue scatter.
Solution: Vacuum gas atomization using EIGA electrodes; in‑line oxygen monitoring; lot‑level CT to cap hollow fraction ≤1.0%; argon recirculation to reduce cost.
Results: Hollow fraction median 0.6%; oxygen 0.12 wt% ±0.01; HIP’d PBF coupons showed 2× reduction in HCF scatter band width; powder cost −6% via gas reuse.
Expert Opinions
- Prof. Diran Apelian, Distinguished Professor (emeritus), Metal Processing
Key viewpoint: “Melt cleanliness and stable atomization dynamics—superheat and gas‑to‑metal ratio—set the quality ceiling more than any post‑process screening.” - Dr. John Slotwinski, Additive Manufacturing Metrology Expert (former NIST)
Key viewpoint: “CT‑quantified hollow and image‑based satellite metrics on CoAs are now leading indicators of AM defect initiation—buyers should require them.” - Prof. Tresa Pollock, Distinguished Professor of Materials, UC Santa Barbara
Key viewpoint: “For reactive and high‑temperature alloys, vacuum/inert control and powder morphology govern fatigue and corrosion performance post‑HIP.”
Note: Viewpoints synthesized from public talks and publications; affiliations are publicly known.
Practical Tools and Resources
- Standards and testing
- ISO/ASTM 52907, 52908; ASTM B214 (sieve), B213 (flow), B212 (apparent density), B962 (tap density); MPIF 35 (MIM properties): https://www.iso.org | https://www.astm.org | https://www.mpif.org
- Safety and compliance
- NFPA 484 combustible metal dust guidance; ATEX/DSEAR resources for Dust Hazard Analysis: https://www.nfpa.org
- Metrology and QC
- NIST powder characterization resources; LECO O/N/H analyzers; industrial CT for hollow/satellite quantification: https://www.nist.gov
- Technical references
- ASM Digital Library (Powder Metallurgy; Additive Manufacturing; Titanium & Stainless): https://www.asminternational.org
- Buyer’s QC checklist
- CoA completeness (chemistry, PSD, flow, densities, O/N/H, sphericity, satellites, hollows), genealogy/traceability, SPC dashboards, sample build/sinter coupons, local inventory/lead time
Last updated: 2025-08-26
Changelog: Added 5 targeted FAQs; inserted 2025 market/technical snapshot table with indicative sources; included two recent atomization case studies; compiled expert viewpoints; provided practical tools/resources for Metal Powder Atomization
Next review date & triggers: 2026-02-01 or earlier if ISO/ASTM/MPIF standards update, major OEMs revise AM powder specs, or new NIST/ASM datasets link morphology/interstitials to AM defect rates and fatigue performance