Introduction
Additive manufacturing, also known as 3D printing, has transformed various industries by enabling the production of complex and customized components. One technology at the forefront of this revolution is the Electron Beam Melting (EBM) furnace. In this article, we will delve into the working principle, advantages, applications, limitations, and future trends of Electron Beam Melting furnaces.
What is an Electron Beam Melting Furnace?
An Electron Beam Melting furnace is a type of additive manufacturing equipment that utilizes an electron beam to selectively melt and fuse metal powders to create complex three-dimensional (3D) structures. The process takes place in a high-vacuum environment, ensuring precise control over the melting and solidification of the metal powders.
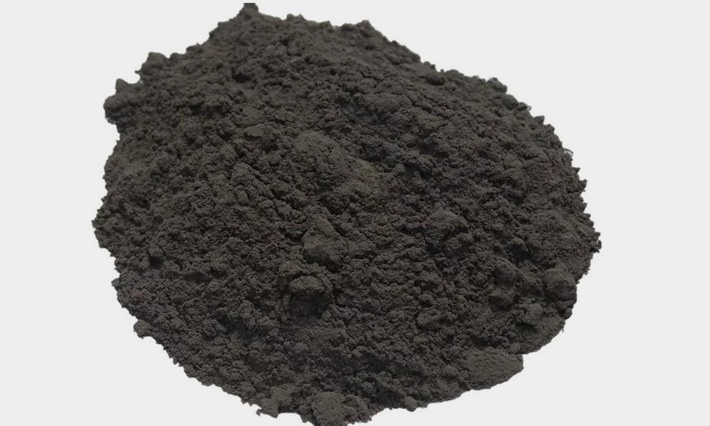
Working Principle of an Electron Beam Melting Furnace
Electron Beam Generation
The Electron Beam Melting process begins with the generation of a high-energy electron beam. A powerful electron gun emits a focused beam that scans across the metal powder bed.
Powder Bed Preparation
Before the melting process, a thin layer of metal powder is evenly distributed over the build platform. The powder bed serves as the raw material for the additive manufacturing process.
Powder Melting Process
As the electron beam scans over the powder bed, it selectively melts and fuses the metal particles. The energy from the beam causes the particles to reach their melting point, creating a solid, fully dense layer.
Layer-by-Layer Building
Once a layer is melted and solidified, the build platform moves down, and a new layer of powder is spread on top. This layer-by-layer approach is repeated until the desired 3D structure is achieved.
Advantages of Electron Beam Melting Furnaces
Complex Geometry Capability
One of the major advantages of Electron Beam Melting furnaces is their ability to produce complex geometric shapes that are difficult or impossible to manufacture using traditional methods. The layer-by-layer nature of the process allows for intricate internal structures and undercuts without the need for additional support structures.
High Material Utilization
EBM furnaces have high material utilization rates. As the powder bed is selectively melted, the surrounding untouched powder acts as support, minimizing waste and reducing material costs.
Reduced Post-Processing Requirements
The near-net-shape capabilities of Electron Beam Melting reduce the need for extensive post-processing. The parts manufactured require minimal machining or finishing, saving time and resources in the production process.
Enhanced Material Properties
The controlled melting and solidification process in EBM furnaces result in improved material properties. The fine microstructure and absence of porosity contribute to enhanced mechanical properties, such as strength and fatigue resistance.
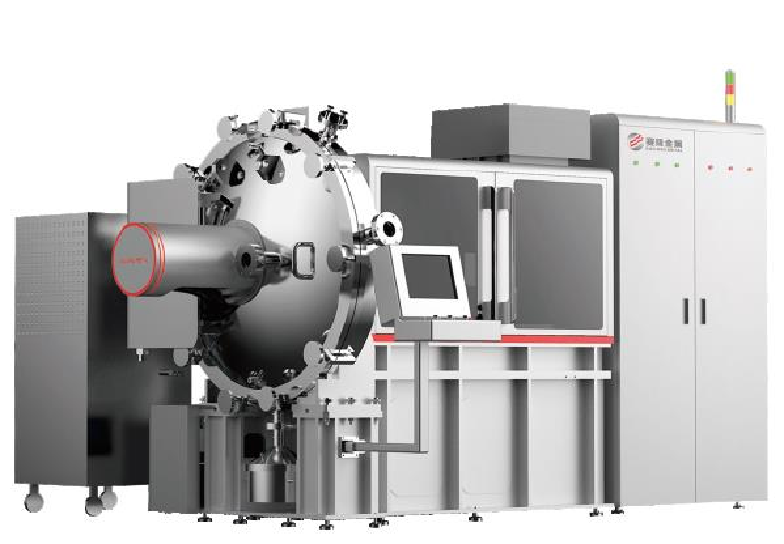
Applications of Electron Beam Melting Technology
Aerospace Industry
The aerospace industry has embraced Electron Beam Melting technology for the production of lightweight, complex components such as turbine blades and fuel nozzles. The ability to create intricate internal cooling channels enhances the performance of these critical parts.
Medical Field
In the medical field, EBM furnaces are used to manufacture patient-specific implants, dental frameworks, and orthopedic devices. The customization capabilities enable the production of implants tailored to individual patients, leading to better treatment outcomes.
Automotive Sector
The automotive sector benefits from Electron Beam Melting in the production of lightweight parts, reducing vehicle weight and improving fuel efficiency. Components like engine brackets, intake manifolds, and suspension parts can be optimized for strength and weight reduction.
Tool and Die Manufacturing
Electron Beam Melting is also employed in tool and die manufacturing. The process allows the production of highly complex molds, dies, and inserts with intricate cooling channels, reducing cycle times and improving part quality.
Limitations and Challenges
Build Volume and Speed
One limitation of Electron Beam Melting is the build volume and speed. The size of the build chamber limits the maximum dimensions of the parts that can be produced, while the layer-by-layer approach can be time-consuming for larger structures.
Cost Considerations
The initial investment and operational costs of Electron Beam Melting technology can be substantial. The equipment, maintenance, and skilled operator requirements contribute to the overall expenses associated with this manufacturing method.
Material Selection and Availability
Not all materials can be processed using Electron Beam Melting. The availability of suitable metal powders and the ability to achieve the desired material properties can be a challenge for certain applications.
Surface Finish and Accuracy
EBM-fabricated parts often exhibit a rough surface finish, requiring additional post-processing if a smoother surface is desired. Additionally, achieving high dimensional accuracy can be challenging due to factors such as thermal stresses and warping.
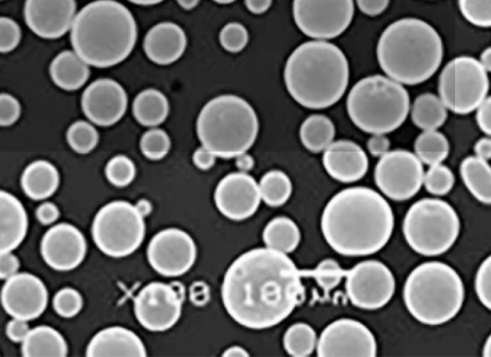
Future Trends and Developments
Increased Use of Hybrid Processes
Hybrid manufacturing processes that combine Electron Beam Melting with other techniques, such as machining or laser deposition, are emerging. These hybrid processes offer the advantages of EBM while addressing some of its limitations, such as improved surface finish and reduced build time.
Advancements in In-Situ Monitoring
Developments in in-situ monitoring systems allow real-time observation of the melting process, enabling better control and optimization of the manufacturing parameters. This enhances process reliability and reduces the risk of defects.
Improved Material Selection
Ongoing research aims to expand the range of materials that can be processed using Electron Beam Melting. Advances in alloy development and powder production techniques will enable the fabrication of a wider range of functional materials.
Scaling Up of Electron Beam Melting
Efforts are being made to scale up Electron Beam Melting technology for industrial production. Increasing the build volume and speed, as well as optimizing the process for high-volume manufacturing, will make EBM more accessible to various industries and enable mass production of complex parts with shorter lead times.
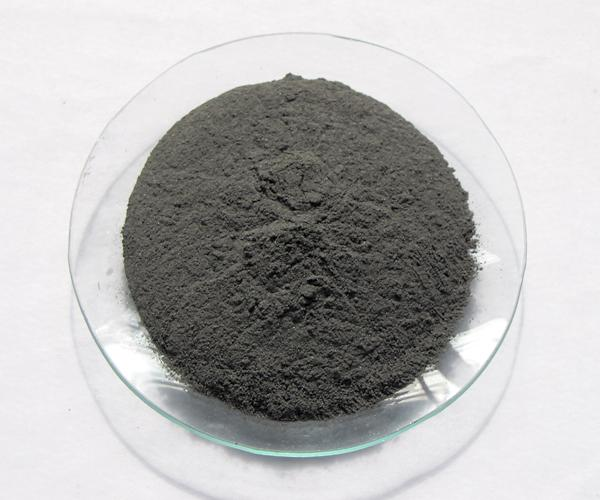
Conclusion
Electron Beam Melting furnaces have revolutionized the field of additive manufacturing by offering unique capabilities and advantages. The ability to produce complex geometries, high material utilization, reduced post-processing requirements, and enhanced material properties make EBM a valuable technology in industries such as aerospace, medical, automotive, and tool and die manufacturing.
However, challenges such as build volume and speed limitations, cost considerations, material selection, and surface finish accuracy need to be addressed for wider adoption. Future trends indicate the integration of hybrid processes, advancements in in-situ monitoring, improved material selection, and scaling up of Electron Beam Melting technology.
As the technology continues to evolve, Electron Beam Melting furnaces are expected to play a significant role in shaping the future of additive manufacturing, enabling the production of highly customized, complex, and functional parts with improved efficiency and performance.
FAQs
1. Can Electron Beam Melting be used with different types of metals?
Yes, Electron Beam Melting can be used with a wide range of metal powders, including titanium alloys, stainless steels, nickel-based superalloys, and more. However, the availability and suitability of specific materials may vary.
2. Are there any size limitations for parts produced using Electron Beam Melting?
Yes, the build volume of Electron Beam Melting machines sets limitations on the maximum size of parts that can be manufactured. However, advancements in technology are continuously pushing the boundaries of size capabilities.
3. How does Electron Beam Melting compare to other additive manufacturing technologies?
Electron Beam Melting offers unique advantages such as the ability to produce complex geometries, high material utilization, and enhanced material properties. However, it also has limitations in terms of build volume, surface finish, and speed compared to other technologies like selective laser melting (SLM) or fused deposition modeling (FDM).
4. Are Electron Beam Melting furnaces suitable for high-volume production?
While Electron Beam Melting has the potential for high-volume production, it currently faces challenges in terms of build speed and cost considerations. Ongoing research and development efforts aim to address these challenges and make EBM more viable for industrial-scale manufacturing.
5. Can Electron Beam Melting be used for applications outside of manufacturing?
While Electron Beam Melting is primarily used in manufacturing industries, its applications are not limited to just that. The technology has the potential to be utilized in fields such as architecture, art, and jewelry design, where complex and customized structures are desired.
Remember, the key to success in Electron Beam Melting lies in understanding the technology’s capabilities, harnessing its advantages, and continuously pushing the boundaries of innovation to overcome its limitations.