We all know that there are few typical technologies to preparation the spherical metallic powder, they are Gas Automization (GA), Plasma Rotating Electrode Process(prep),Plasma Atomization(PA), Plasma Spheroidization (PS).
4 best spherical metallic powder preparation techniques:
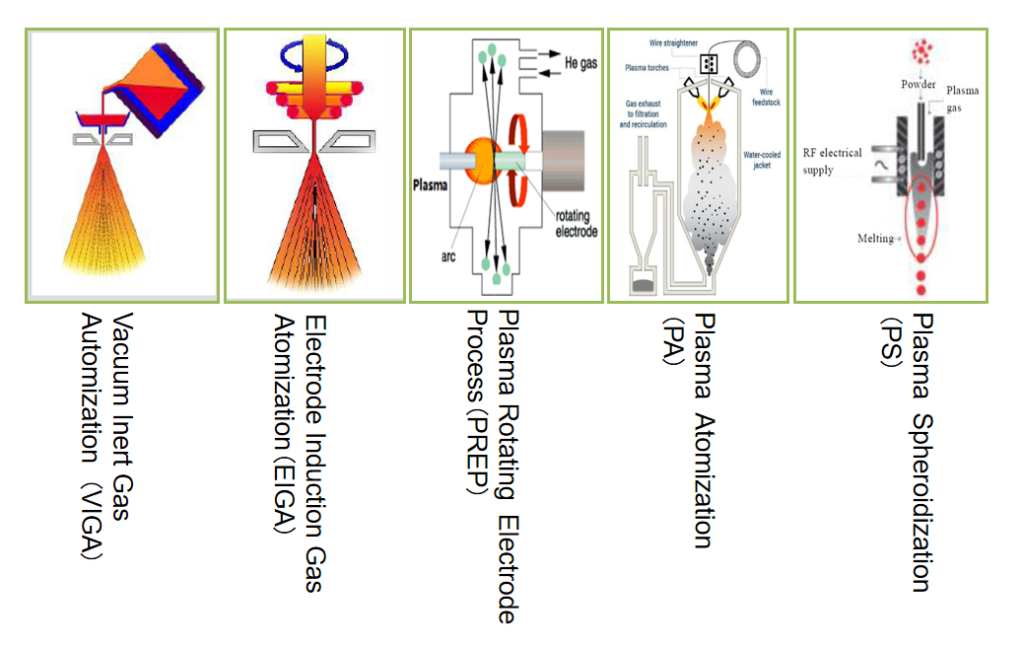
Gas Automization(GA)
Aerosolised powder production is the use of high speed airflow to break up liquid metal streams into small droplets, which are then rapidly condensed to produce a shaped powder.
Aerosolisation has become the most important method for the preparation of fine spherical metal and alloy powders, and according to statistics, the production of metal powders by atomisation has reached 80% of the world’s total powder production. There are many different types of metal powders that can be industrially produced by atomisation, including almost all common metal and alloy systems, except for refractory metals such as tungsten and molybdenum and very reactive metals.
This method produces metal powders with fine particle size (<150μm), good sphericity, high purity, low oxygen content, fast forming speed and low environmental pollution, and is the mainstream method for the preparation of metal powders for powder metallurgy, metal injection moulding and metal additive manufacturing.
Plasma Atomization(PA)
Plasma Atomization (PA) is the process of feeding metal raw materials (generally wire) at a certain rate through a special feeding mechanism. The raw materials are rapidly dispersed into ultra-fine droplets or aerosols by focused plasma jets generated by multiple symmetrically mounted plasma torches at the top of the furnace, and heat exchange with inert gases for cooling during the deposition process, resulting in a near spherical powder.
Using plasma atomisation technology, titanium alloy powders with small particle size, high purity and good flowability can be obtained. In contrast to conventional powder making techniques, plasma atomisation does not use the commonly used water or gaseous media streams to crush the liquid stream, but rather a hot plasma, which avoids the problem of poor sphericity of the molten droplets due to rapid cooling. In addition, this method does not require the use of conventional ceramic crucibles and is suitable for the powdering of all metallic materials that can be melted, especially highly reactive metallic materials containing titanium that cause contamination of the crucible.
Plasma Rotating Electrode Process(PREP)
The plasma rotating electrode atomisation method is one of the more ideal ways to prepare highly pure and dense spherical powder materials. The mechanism can be simply described as follows: the plasma beam is the heat source, the metal or alloy is the self-consuming electrode, the electrode ends are melted into a liquid film by the coaxial plasma, and the spherical powder is obtained under the action of its own high-speed centrifugal force and surface tension.
Plasma rotary atomisation powder making characteristics: (1) powder particle size distribution narrow, particle size more controllable, high sphericity gas atomisation method prepared alloy powder particle size is mainly concentrated in the range of 0-150μm; plasma rotary electrode atomisation method prepared alloy powder particle size is mainly concentrated in 20-200μm.(2) powder basically does not exist hollow powder, satellite powder (3) powder ceramic inclusions less, higher cleanliness (4 ) powder oxygen increment less without alloy melting process; no high-speed inert airflow to break the liquid stream; aerosolized powder oxygen increment in more than 100ppm, plasma rotary atomization powder oxygen increment can be controlled in less than 50ppm. The advantages of plasma rotary atomization powder manufacturing technology in additive manufacturing 1) powder solid, the printing process will not exist in the hollow ball brought about by air gaps, involvement and precipitation pores, cracks and other defects; 2) powder particle size, narrow particle size distribution, printing process less/no spherification, agglomeration phenomenon, higher surface finish, and the consistency and uniformity of printing can be fully guaranteed.
Plasma Spheroidization (PS)
The plasma spheroidisation technique uses the high temperature characteristics of the plasma to rapidly heat and melt irregularly shaped powder particles fed into the plasma, which rapidly solidify under the combined effect of surface tension and extremely high temperature gradients to form spherical powders. Plasma has the advantages of high temperature (~104 K), large plasma torch volume, high energy density, no electrode contamination, fast heat transfer and cooling, etc. It is a good way to produce high quality spherical powders with uniform components, high sphericity and good flowability, especially in the preparation of rare refractory metals, oxides, nitrides, carbides and other spherical powders.
The above is a brief introduction to the principles and characteristics of several types of 3D printing powder making equipment. In summary, atomised powder making technology, especially VIGA and EIGA, is currently the most used powder making technology, but it is still limited by the purity and sphericity of the powder compared to several other technologies.
When PREP, PA and PS technologies are compared, PA has more satellite powder, PS is limited by the raw material, and PREP has a relatively low fines yield compared to the other two.
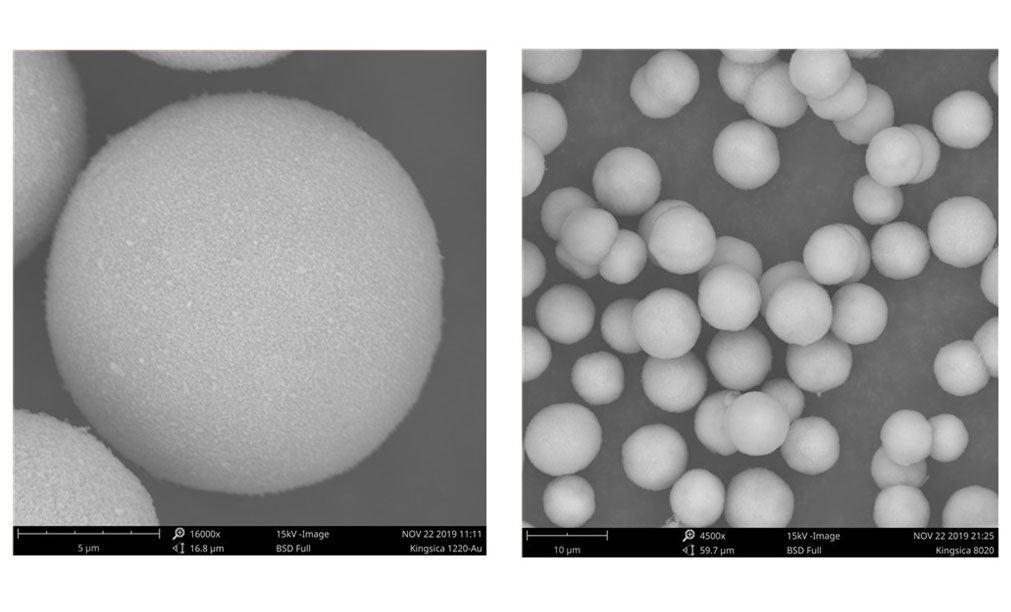