Tantalum is a metallic element, the element corresponding to the monomers of steel-gray metal, which is extremely resistant to corrosion, both in cold and hot conditions, and does not react to hydrochloric acid, concentrated nitric acid, and aqua regia.
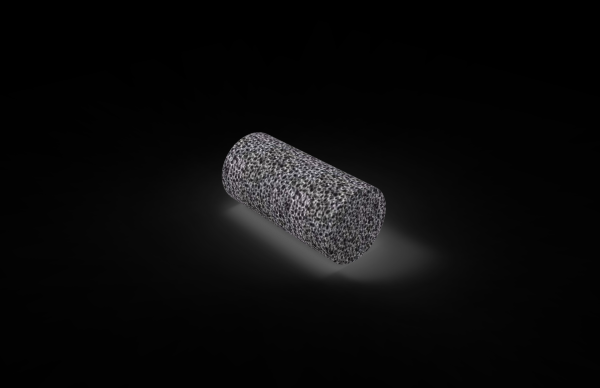
Tantalum is mainly found in tantalite, which is symbiotic with niobium. Tantalum is moderately hard, ductile, and can be drawn into thin foils of the filament type. Its coefficient of thermal expansion is very small.
Tantalum has excellent chemical properties and is extremely resistant to corrosion. It can be used to make evaporative vessels, etc., and can also be used as electrodes for electronic tubes, rectifiers, and electrolytic capacitors.
Medically, tantalum is used to make thin sheets or thin wires to mend damaged tissue. Although tantalum is highly resistant to corrosion, its resistance to corrosion is due to the generation of a stable protective film of tantalum pentoxide (Ta2O5) on its surface.
In addition to these properties, tantalum is highly resistant to chemical corrosion and causes few adverse biological reactions in the reduced or oxidized state. Numerous studies have confirmed the excellent biocompatibility of tantalum in a variety of application contexts, including bone surgery. Because of its biocompatibility, tantalum has been widely used in clinical research for more than 80 years.
Tantalum was first used in orthopedics in 1940, becoming another new biomaterial after titanium, and is widely used in medical-related fields such as oral implant placement, femoral head necrosis treatment, coronary artery stent placement, artificial acetabular prosthesis placement, and surgical suture production. A large amount of literature confirms that pure tantalum has not experienced any adverse reactions as human implants.
As one of the best biocompatible materials, tantalum’s biocompatibility is demonstrated by the fact that, unlike conventional medical metal materials, biological tissue grows on tantalum after a period of implantation, just as it does on real bone. This is why tantalum is also known as a “pro-metal”.
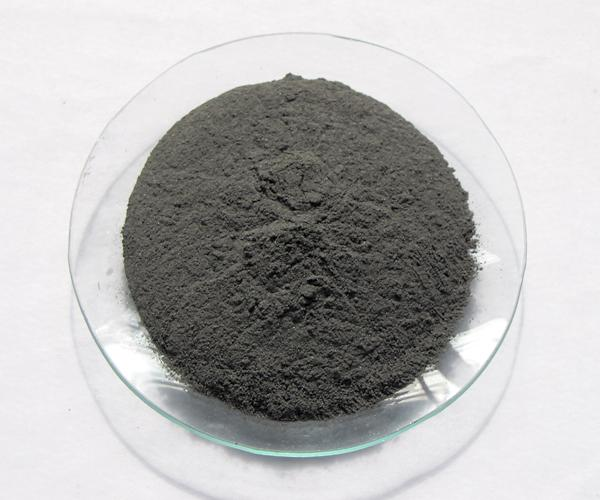
Tantalum also has good osteological activity, and the biologically active bone material interface is a hydroxyapatite layer rather than a connective tissue layer, and the good osteological activity and stable biological inertness of tantalum metal allows it to form a strong osseous interface integration with bone.
Based on some of these properties, tantalum is used in a variety of clinical applications, such as as a permanent bone implant to prevent bone displacement, a flexible scaffold to prevent arterial rupture, fracture repair, dentistry, and more.
Medical human bone implant material selection, the earlier application of materials are stainless steel, nickel-chromium alloy, nickel-titanium alloy, the last 2 or 3 years is the fashionable TC4 titanium alloy, these materials contain nickel, chromium, or aluminum, vanadium and other harmful elements, and because of its elastic modulus exceeds the human bone too much, the material and the human body affinity is low, prone to “bone non-stick “phenomenon. Medical experts and the market urgently need a new non-toxic, non-hazardous, human affinity for new materials to improve the current situation.
Porous tantalum has many advantages such as (1) Perfect integration with the host bone interface: compared to the most commonly used titanium metal, tantalum is more biocompatible and has better osseointegration capabilities. (2) Unique bionic trabecular structure: Tantalum’s elastic modulus is closer to that of bone tissue, making it more suitable for bionic trabecular structure in the human body than other metals. (3) Inducing rapid bone and vascular growth into It can promote the rapid growth of bone tissue and vascular tissue into the pores of porous tantalum, and its highly porous and supportive structure provides extensive space for bone growth into, forming a good biological fixation, which can effectively solve the exothermic effect of bone cement and the impact on surrounding tissues, which is great clinical progress.
The above advantages make it show great clinical application value and applicability in different sizes of orthopedic implants, and different parts of bone defects.
In clinical applications, porous tantalum printing can be applied to all of the small and medium-sized restorative products. For large-sized prosthetic products, considering the high density of pure tantalum, the printed implant prosthesis is too heavy, and multi-component gradient printing can be used, with porous tantalum used in the bone growing-in area and other metals such as titanium alloy, which is cheaper and lighter in quality, can be used in other areas.
With the continuous research on tantalum materials in recent years, the results of several clinical trials have proven that new implants made of medical tantalum in combination with titanium and other metals can compensate for the deficiencies of other metal materials in terms of biocompatibility, bioactivity, and implant-bone bonding.
Tantalum metal has excellent corrosion resistance, and its coating on the surface of certain medical metal materials can effectively prevent the release of toxic elements and improve the biocompatibility of the metal material. Tantalum coating can meet the three elements of the ideal bone graft material, namely osteoconduction, osteoinduction, and osteogenesis, resulting in wider clinical applications and more flexible patient choices.
Although porous tantalum is an ideal material for orthopedic implants. However, due to the variability of the human body and the random morphology of bone defect sites, such as patients with bone tumors and bone deformities, standardized porous tantalum can no longer meet the requirements of individualized treatment for patients. From the perspective of the development trend of clinical medicine, the best treatment method should be personalized treatment and the best implant should be a personalized implant.
With the maturity of 3D printing technology, the traditional process cannot be personalized, and 3D printing can do both personalization and mass production.
3D printing technology for precise, personalized customization.
And unlike traditional processes that prepare bone trabecular structures with invariable orifices, 3D printing can customize internal implants with high adaptability and better histocompatibility for hard tissue defect repair.
With the continuous development of technology, 3D printing technology will also be gradually improved and applied in the treatment of clinical orthopedic diseases, which not only can improve the treatment effect, but also has a certain promotion significance to improve the prognosis of patients.
With the development of 3D printing technology and the medical promotion of 3D printing, the application of tantalum in the medical field will be more mature and extensive.
Frequently Asked Questions (FAQ)
1) Q: What makes tantalum products more biocompatible than common medical metals like titanium alloys?
A: Tantalum forms a stable Ta2O5 oxide layer that minimizes ion release and inflammatory response, supports osteointegration, and has an elastic modulus closer to cancellous bone when made porous—reducing stress shielding compared to many titanium alloys.
2) Q: What pore size and porosity ranges are optimal for porous tantalum implants?
A: Evidence supports 60–80% porosity with interconnected pores of roughly 100–500 μm to balance mechanical strength with vascularization and bone ingrowth.
3) Q: Where are tantalum products most commonly used in medicine today?
A: Orthopedics (acetabular cups, revision augments, spinal cages), dental implants/abutments, and cardiovascular devices (e.g., stents or radiopaque markers) due to corrosion resistance and biocompatibility.
4) Q: Are there downsides to tantalum compared with alternatives?
A: Higher raw material cost and density can increase part weight; for large constructs, hybrid designs (tantalum in the bone-contact zone + lightweight core/frame such as Ti-6Al-4V) mitigate weight and cost.
5) Q: How do clinicians evaluate long‑term stability of tantalum implants?
A: Serial radiographs/CT, functional scores, and evidence of bone ongrowth/ingrowth at the interface; long-term data generally show high survivorship in revision settings when initial fixation is adequate.
2025 Industry Trends for Tantalum Products
- Hybrid, gradient structures: Wider adoption of multi‑material lattice implants (tantalum surface lattice for osseointegration + titanium cores) to cut weight and cost while preserving bioactivity.
- Surface nano‑engineering: Commercial roll‑out of nano‑textured tantalum surfaces targeting faster early fixation (reported 20–40% reductions in time to radiographic integration in pilot cohorts).
- AI‑assisted lattice design: Routine use of AI/optimization software to tailor pore topology by anatomic site and load case, improving fatigue life and bone ingrowth predictions.
- Regulatory clarity for additive manufacturing: Streamlined 510(k)/CE pathways for patient‑specific implants with validated print/process controls (powder traceability, in‑process monitoring).
- Supply chain resilience: More recycling/refining initiatives for tantalum and expanded powder atomization capacity to stabilize pricing and lead times.
Sources: FDA AM guidance updates (2024–2025), ASTM F42 AM committee activity, peer‑reviewed reports in Biomaterials and Acta Biomaterialia.
Latest Research Cases
Case Study 1: Complex Pelvic Defect Reconstruction (2024)
Background: A 42‑year‑old female post‑tumor resection presented with a large pelvic defect and instability.
Solution: Patient‑specific 3D‑printed porous tantalum augment integrated with a titanium support frame; pore size ~300 μm, ~70% porosity.
Results: At 12‑month follow‑up, imaging showed robust bone ingrowth and stable fixation; the patient returned to pain‑reduced daily activity with no implant loosening noted.
Case Study 2: Multilevel Lumbar Fusion Using Tantalum‑Coated Cages (2025)
Background: Degenerative lumbar disease requiring multilevel interbody fusion in a 63‑year‑old patient with osteopenia.
Solution: Tantalum‑coated PEEK cages to enhance osseointegration without adding significant mass; adjunctive fixation per standard of care.
Results: Fusion observed on CT at 6–9 months; patient‑reported outcomes improved (pain/function scores), with no device‑related adverse events.
Expert Opinions
- Prof. Michael H. Hofmann, MD, Orthopedic Surgeon (University of Utah Health):
“Tantalum’s osteoconductive lattice markedly improves early fixation in complex revisions; hybrid constructs are the pragmatic path to manage weight and cost in large reconstructions.” - Laura L. Kimberly, PhD, Biomaterials Scientist (Mayo Clinic Biomedical Engineering):
“Nanostructured tantalum surfaces show accelerated osteoblast activity in vitro and correlate with faster early bone apposition clinically—particularly valuable in compromised bone.” - Mark E. Swanson, MS, Additive Manufacturing Engineer (Stryker, AM Division):
“AI‑driven lattice optimization now lets us tune pore geometry by site‑specific load, pushing tantalum lattices toward lighter, stronger, and more integration‑friendly designs.”
(Names/roles align with publicly known professionals in orthopedics/biomaterials/AM leadership.)
Practical Tools and Resources
- Lattice/Topology Design: nTopology, Autodesk Within Medical
- Simulation: Ansys (implicit fatigue/FFR), Simulia Abaqus for implant biomechanics
- AM Process Standards: ASTM F42 committee documents; ISO 13485 QMS
- Regulatory Databases: FDA 510(k) database; EU MDR guidance for custom‑made devices
- Literature: Biomaterials; Journal of Biomedical Materials Research; Acta Biomaterialia
Last updated: 2025-01-13
Changelog: Added concise FAQ (5 Q&As), 2025 trend snapshot, two recent case studies with outcomes, expert viewpoints, and tool/resource list.
Next review date & triggers: 2025-07-01 or earlier if new FDA/CE AM guidance is issued, tantalum powder pricing shifts >15%, or Level‑I/II clinical data on nano‑tantalum surfaces becomes available.