High temperature alloy powders are powders commonly used for 3D printing. High temperature alloys have good oxidation resistance, corrosion resistance, excellent tensile, endurance, fatigue properties and long-term tissue stability and were developed to meet the requirements of modern aerospace technology in a variety of high temperature use conditions.
Common high temperature alloy powders include Hastelloy X, IN625, IN718, etc. We will then highlight the properties of these high temperature alloy powders and their applications in 3D printing.
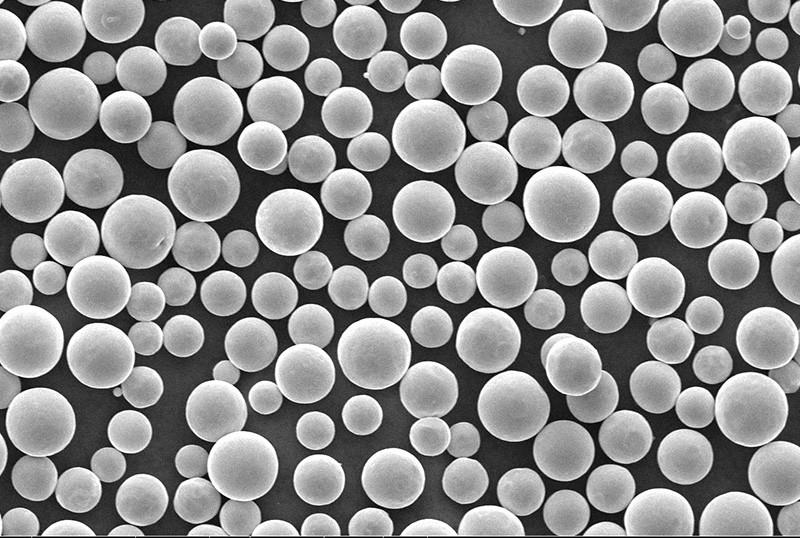
Hastelloy X Powder
Hastelloy X powder (GH3536) is a solution-reinforced deformable high temperature alloy powders with moderate endurance and creep strength below 900°C and good oxidation and corrosion resistance. It is suitable for the manufacture of components such as aero-engine combustion chambers for long-term use below 900°C.
Hastelloy X powder has high strength, good ductility, excellent high temperature oxidation resistance and high creep strength up to 850°C. It is therefore commonly used in turbine engine components, aero engines, aerospace engine hot end components, etc.
In625 Powder
IN625 powder (GH3625) is a solid solution strengthened deformed high temperature alloy powder with a maximum operating temperature of 950°C. It has good tensile strength and fatigue resistance, and good processing and welding process performance. It is widely used in the manufacture of aero-engine parts, aerospace structural components, etc.
6IN625 has high strength; good ductility; excellent creep fracture strength up to 700 °C; and excellent corrosion resistance, so it is widely used in aircraft engine components; energy applications; turbine components; etc.
Chemical Composition
元素 Element 实测值 Tested
Ni Bal.
Cr 20.00-23.00
Mo 8.0-10.0
Nb 3.15-4.15
Fe ≤5.0
Co ≤1.0
Ti ≤0.40
Si ≤0.50
Mn ≤0.50
Al ≤0.40
Cu ≤0.07
C ≤0.10
P ≤0.015
IN718 Powder
IN718 powder (GH4169) is a precipitation hardening deformation high temperature alloy powders, can be used at 650 ℃ for a long time, short time use temperature can reach 800 ℃, the alloy at 650 ℃ It has good fatigue resistance, oxidation resistance and organisational stability. It is suitable for the production of aerospace and industrial turbine discs, rings, blades, cassettes and other structures. The alloy is suitable for the production of aerospace and industrial turbine discs, rings, blades, magazines and other structures.
IN718 has high strength; good ductility; excellent mechanical properties up to 700 °C; and excellent oxidation resistance, so it is widely used in aircraft engine components; rocket components; and energy in high temperature environments.
Chemical Composition
元素 Element | 实测值 Tested |
Fe | Bal. |
Ni | 50.00-55.00 |
Cr | 17.00-21.00 |
Nb | 4.75-5.50 |
Mo | 2.80-3.30 |
Ti | 0.65-1.15 |
Al | 0.20-0.80 |
Cu | ≤0.30 |
C | ≤0.08 |
Si | ≤0.35 |
Mn | ≤0.35 |
Mg | ≤0.01 |
B | ≤0.006 |
Co | ≤1.00 |
P | ≤0.015 |
S | ≤0.015 |
IN939 Powder
IN939 powder is not a common type of high-temperature alloy powder; it is a nickel-based high-temperature alloy with γ′ precipitation phase as the main strengthening phase. temperature alloy with a high chromium content and excellent resistance to hot corrosion and high temperature oxidation resistance.
Widely used in the manufacture of blades, fuel nozzles, retaining rings, diffusers and other structural components for gas turbines, IN939 is one of the most corrosion resistant nickel-based high temperature alloys in high temperature oxidising and sulphide atmospheres. However, due to the high cost of the material, the difficulty of deposition and forming, and the difficulty of processing, there has been little discussion at home and abroad about IN939.
However, due to the high cost of the material, the difficulty of deposition and forming, and the difficulty of processing, the research and application of IN939 nickel-based high-temperature alloy at home and abroad is relatively small, and the existing ones mainly focus on the organization of IN939 blade material in service properties and the study of the heat-affected zone liquid cracks in the welding repair process The elimination of the heat-affected zone crack, has not yet involved such as coating preparation, defect repair and other areas.
High Temperature Alloy Powders
The above is a brief list of several commonly used and one very useful high temperature alloy powders.
High temperature alloys have been developed to meet the requirements of modern aerospace technology under various high temperature use conditions due to their good oxidation resistance, corrosion resistance, excellent tensile, endurance, fatigue properties and long-term organisational stability and have shown a strong vitality in the field of advanced aerospace engines.
With the development of aerospace, high temperature alloy powders will be more often used in aerospace, energy and other fields.