In recent years, the aerospace industry has witnessed remarkable advancements in manufacturing technology. One such technology that has revolutionized the industry is 3D printing, also known as additive manufacturing. 3D printing has opened up a whole new realm of possibilities, enabling the production of complex and intricate designs that were once deemed impossible. In particular, the use of metal powders in 3D printing has garnered significant attention due to its wide range of applications and benefits. This article will explore the various applications of 3D printing metal powder in the aerospace industry.
Introduction to 3D Printing in Aerospace
3D printing, or additive manufacturing, is a process that builds objects layer by layer using a computer-controlled machine. It has gained prominence in the aerospace industry due to its ability to create intricate parts with high precision and complexity. Traditionally, manufacturing aerospace components involved subtractive processes like milling, cutting, and drilling. However, 3D printing offers several advantages that make it an attractive option for aerospace applications.
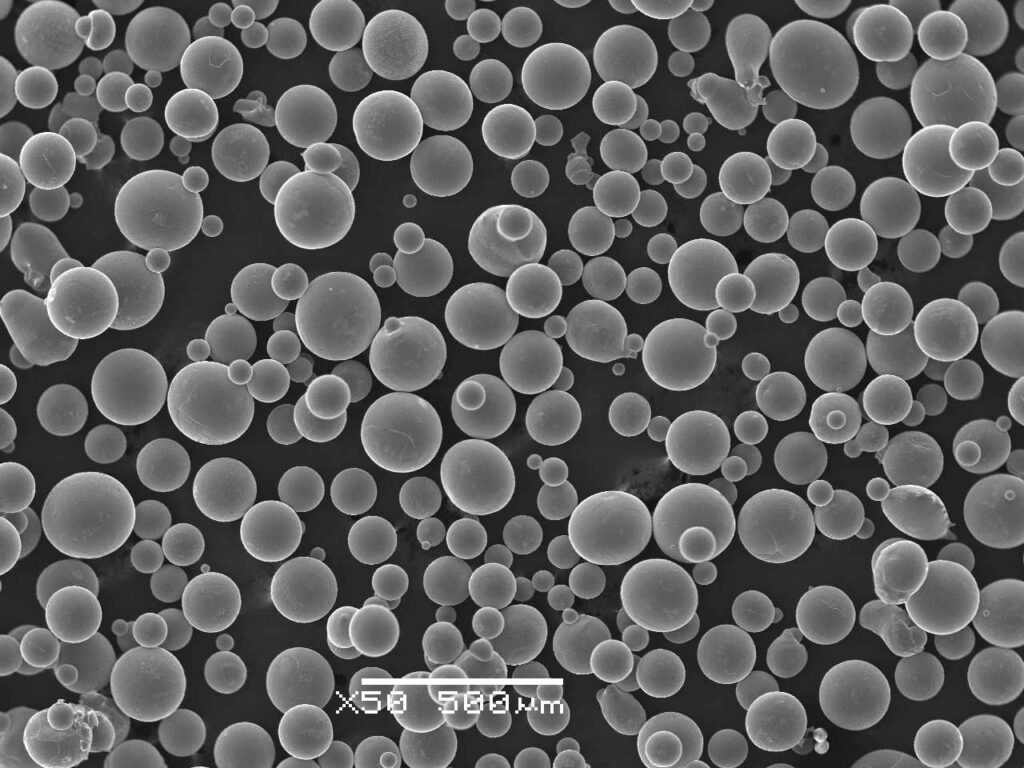
Advantages of 3D Printing with Metal Powders
3D printing with metal powders brings numerous advantages to the aerospace industry. Firstly, it allows for the production of lightweight components with complex geometries that were previously difficult or impossible to manufacture using traditional methods. This weight reduction leads to fuel efficiency and increased payload capacity, both crucial factors for the aerospace industry. Additionally, 3D printing offers reduced material waste, as it only uses the required amount of metal powder, minimizing costs and environmental impact.
Furthermore, the ability to print on-demand parts brings significant benefits in terms of supply chain management. Spare parts can be produced when needed, eliminating the need for extensive inventory storage and reducing downtime. This advantage is particularly valuable for the aerospace industry, where maintenance, repair, and replacement of components are critical for operational efficiency.
Applications of 3D Printed Metal Parts in Aerospace
Engine Components
One of the most vital applications of 3D printed metal parts in the aerospace industry is in the production of engine components. 3D printing allows for the creation of intricate cooling channels and optimized geometries, enhancing the performance and efficiency of engines. Turbine blades, fuel nozzles, and combustion chambers are among the engine components that can benefit from 3D printing.
Lightweight Structures
Weight reduction is a key consideration in aerospace design, as it directly impacts fuel consumption and overall performance. 3D printing enables the creation of lightweight structures by using optimized lattice designs and internal cavities, resulting in parts that are both strong and lightweight. This advantage is particularly relevant for applications such as airframe components, where weight savings are highly desirable.
Heat Exchangers
Heat exchangers play a crucial role in the aerospace industry, facilitating the transfer of heat between fluids. 3D printing allows for the production of complex heat exchanger designs with enhanced heat transfer efficiency. By using metal powders, it becomes possible to create intricate geometries that maximize the surface area for heat exchange, leading to improved performance.
Tooling and Fixtures
3D printing metal powders also finds applications in the creation of tooling and fixtures used in aerospace manufacturing processes. Custom jigs, fixtures, and molds can be produced quickly and cost-effectively, streamlining production and assembly processes. The ability to create complex shapes with precision enhances the accuracy and repeatability of manufacturing operations.
Satellite Components
Satellites require lightweight and robust components to withstand the harsh conditions of space. 3D printing metal powders provides a viable solution for the production of satellite components such as antenna supports, brackets, and structural elements. The ability to create intricate designs and optimize weight ensures efficient use of resources and improved satellite performance.
Challenges and Limitations of 3D Printing Metal Powders
While 3D printing with metal powders offers numerous advantages, there are challenges and limitations that need to be addressed. One major challenge is the high cost of equipment and materials associated with metal 3D printing. Additionally, the process of printing with metal powders requires careful control of parameters such as temperature, gas atmosphere, and powder quality to ensure optimal results. Furthermore, post-processing steps like heat treatment and finishing are often necessary to achieve the desired mechanical properties, adding complexity to the overall manufacturing process.
Future Prospects and Innovations
As technology continues to evolve, the future of 3D printing metal powders in the aerospace industry looks promising. Researchers and engineers are continuously working on improving the quality, speed, and scalability of metal 3D printing. Advancements in material science and process optimization will enable the production of even more advanced components, pushing the boundaries of what is achievable in aerospace manufacturing.
Conclusion
In conclusion, 3D printing with metal powders has revolutionized the aerospace industry by providing innovative solutions for complex part manufacturing. The applications of 3D printed metal parts in aerospace span engine components, lightweight structures, heat exchangers, tooling and fixtures, and satellite components. Despite challenges and limitations, the future prospects for 3D printing metal powders in aerospace are promising, as ongoing research and development continue to push the boundaries of additive manufacturing technology.
FAQs (Frequently Asked Questions)
- Q: What is 3D printing?
- A: 3D printing, also known as additive manufacturing, is a process that builds objects layer by layer using a computer-controlled machine.
- Q: How does 3D printing benefit the aerospace industry?
- A: 3D printing offers advantages such as lightweight part production, reduced material waste, on-demand spare parts, and enhanced supply chain management.
- Q: What are some applications of 3D printing with metal powders in aerospace?
- A: Applications include engine components, lightweight structures, heat exchangers, tooling and fixtures, and satellite components.
- Q: What are the challenges of 3D printing metal powders?
- A: Challenges include the high cost of equipment and materials, precise process control, and the need for post-processing steps for optimal results.
- Q: What does the future hold for 3D printing metal powders in aerospace?
- A: Ongoing research and development will lead to advancements in quality, speed, and scalability, opening up new possibilities in aerospace manufacturing.