3D printing technology is a revolutionary manufacturing technology that overturns traditional manufacturing methods. It is a revolutionary manufacturing technology¨, also known as “additive manufacturing“. This article focuses on several aspects of 3D printing materials and research into the development of 3D printing materials and technologies.
Principles of 3D Printing
The basic principles of 3D printing are: digital layering Lamination. Physical lamination, where a digital model of the object to be printed is first created and The digital layering is carried out to obtain a two-dimensional processing path or track for each layer. Then, a suitable material is selected and the corresponding process is applied to each layer. Then, a suitable material and corresponding process is selected, and the printed object is printed layer by layer, driven by the above-mentioned layer-by-layer, two-dimensional digital path. The final object is produced cumulatively.
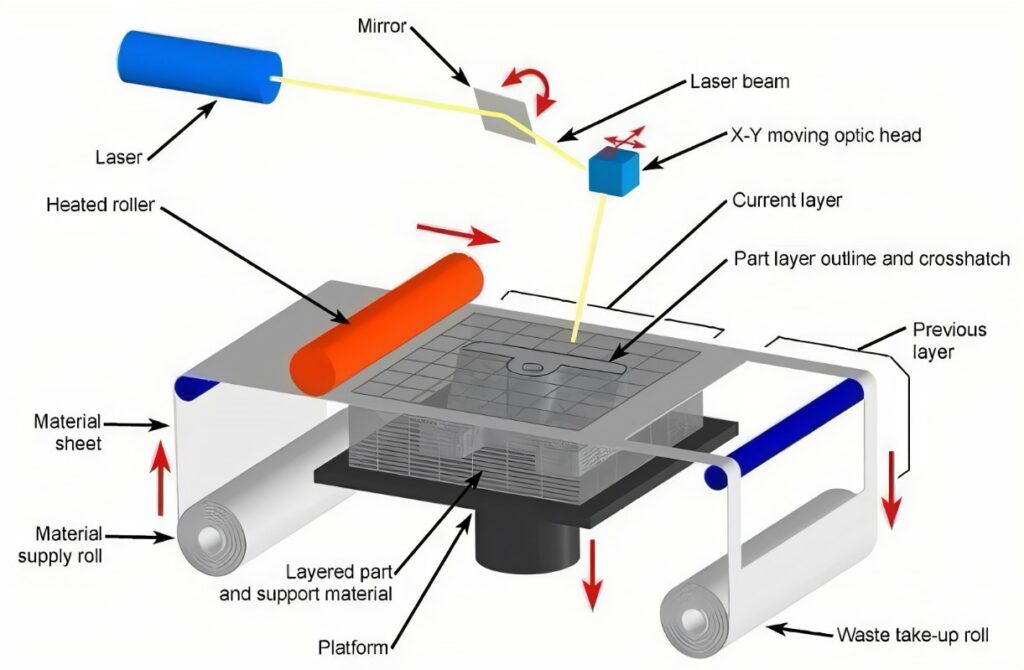
With its high processing flexibility and fast market response, 3D printing technology is well established in the fields of industrial modelling, packaging, manufacturing, architecture, art, medicine, aviation, aerospace and film.
Currently, there are nearly 20 different process systems in the field of 3D printing, of which the six most typical and mature processes are Stereo Lithigraphy Apparatus (SLA), Laminated ObjectManufacturing (LOM), Fused Deposition Modeling, FDM, Selective Laser Sintering, SLS, Selective Laser Melting, SLM), and Three Dimensional Printing and Gluing, 3DP.
Although the principles of these six 3D printing processes are the same, their respective characteristics and specific applications differ due to the different printing materials used. Printing materials are currently a hot topic of research in 3D printing. and is a bottleneck in the further development and application of 3D printing processes. The paper also highlights that printing materials are a bottleneck in the further development and application of 3D printing processes.
3D Printing Technologies and Materials
SLA
The SLA process was patented in the USA by Charles Hull in 1984 and commercialised by 3D Systems, and is now recognised as one of the most well researched and earliest used 3D printing methods in the world.
The materials currently available for this process are mainly light sensitive liquid resins, i.e. photosensitive resins. This type of photosensitive resin material mainly includes zwitterion, reactive diluent and initiator.
LOM
Michael Feygin introduced the LOM process in 1984, which is generally more suitable than SLA for making large parts, especially for the automotive industry, and is now used more often by Chinese 3D printing in the industrial sector.
The printing material in the LOM process involves three aspects, namely the thin layer material, the binder and the coating process. The thin layer material can be divided into paper, plastic film, metal foil, etc., currently mostly inexpensive paper; and the binder is generally a hot melt adhesive. The selection of the paper material, the configuration of the hot melt adhesive and the coating process are all based on ensuring the quality of the final prototype part, while taking into account the cost.
FDM
The FDM process is most widely used with the FDM manufacturing system developed by the US company Stratasys.
The materials currently available for this process are mainly low melting point materials that are easy to melt. The general process is that the filamentary material is fed through the feed rollers to the The general process is that the filamentary material is heated in the cavity of the nozzle by a feed roll.
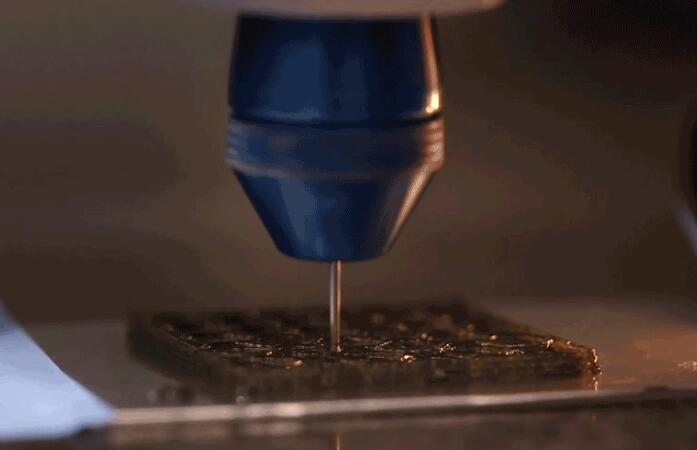
SLS
The SLS process, also known as the Selected Area Laser Sintering process, was developed by Dechard at the University of Texas at Orting in 1989. Based on this material, the Direct Metal Laser Sintering, DMLS process system was also introduced in the same category as the SLS process.
In terms of form, the materials used in the SLS process are various types of powder, such as nylon powder, nylon-coated glass powder, polycarbonate powder, polyamide powder, wax powder, metal powder (often subject to re-sintering and coppering after printing), fine sand coated with thermosetting resin, wax-coated ceramic powder and wax-coated metal
In terms of materials, the SLS process is not only capable of forming low melting point materials such as paraffin and plastics, but can also directly form metals including stainless steel, and even high melting point materials such as ceramics. The SLS process is not only capable of forming low melting point materials such as paraffin and plastics, but also metals including stainless steel and even high melting point materials such as ceramics. The ability to print high strength, high hardness parts or components from metal or ceramic materials is one of the reasons why the SLS process is gaining ground in the industry. This is the main reason why the SLS process is gaining so much attention and has the most promising applications in the industry. The main reason why the SLS process has gained so much attention and has the most promising applications.
SLM
In response to the above disadvantages of the SLS process, the Fraunholfer Institute in Germany In 1995, the Fraunholfer Institute proposed the SLM technology, which also uses the discrete stack-plus principle. This process not only has the advantages of SLS, but also has a high density of formed metal and good mechanical properties. The process not only has the advantages of SLS, but also has a high density of formed metal and good mechanical properties. It has brought about a revolution in the manufacture of complex metal parts.
The SLM material range includes iron-based alloys, nickel-based alloys, aluminium alloys and titanium alloys.
Iron-based alloys have an important role in engineering and therefore the study of iron SLM forming of Fe-based powders has been the most widely and intensively studied.
3DP
3DP technology and equipment was developed by the Massachusetts Institute of Technology (MIT) in the USA, using mostly powdered materials such as ceramic, metal and plastic powders, which are sprayed through a nozzle with an adhesive to “print” the cross-section of the part onto the material.
These powders are sprayed with a nozzle that “prints” the section of the part onto the material powder. The printing process is similar to colour printing on paper, and can be achieved by setting up a three-color binder and nozzle system for colourful three-dimensional printing. The 3D printing of ceramic artefacts has already found many applications. This process is one of the most promising 3D printing processes after SLA, LOM, SLS and FDM, as it is increasingly being used to construct biological tissue engineering structures¨”.
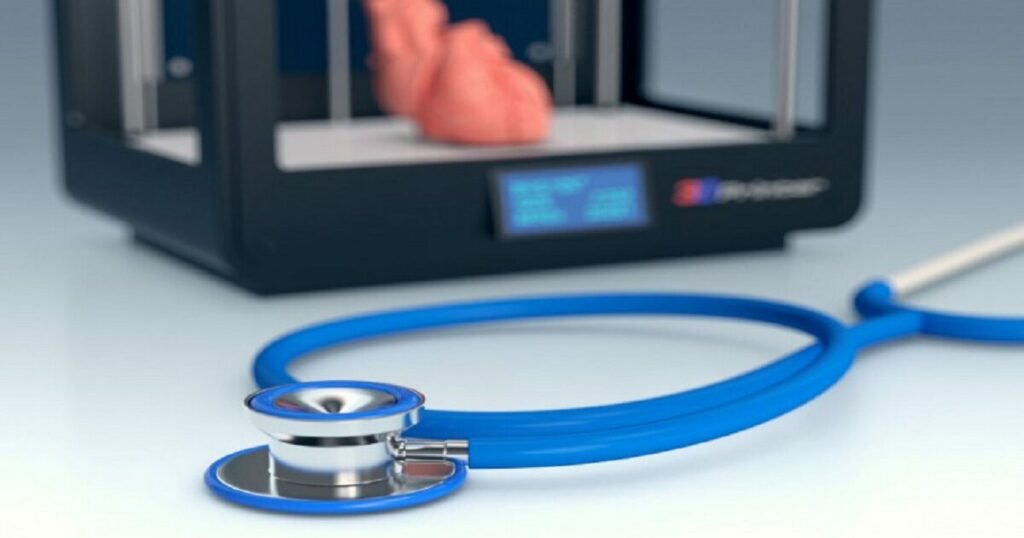
Currently, six 3D printing processes are used within the 3D printing field The printing materials that are widely used in the system contain four main types in terms of form. liquid photosensitive resin materials, thin materials (paper, plastic film), low melting point filament and powder materials; in terms of composition, they cover almost all types of materials currently used in production The composition covers almost all types of materials used in production, including plastics, resins, waxes and other polymers, metals and alloys, ceramics, etc. Metals and alloys, ceramics, etc.
From the characteristics of 3D printing, combined with various application requirements, the development of new printing materials, especially nano-materials, non-homogeneous materials, composite materials that are difficult to produce by other methods, direct printing to produce highly dense metal parts of alloy materials, functional gradient materials, biological materials, etc. will be the development direction of 3D printing materials to continuously improve the quality; in addition, to promote the serialization of 3D printing materials, standardization, In addition, to promote the serialization, standardization, green and environmental protection of 3D printing materials, and with the concept of “3D printing +”, to continuously expand the The in-depth integration of 3D printing technology with traditional manufacturing industries will The development direction for the continuous expansion of the production of 3D printing materials.