Welcome to the ultimate guide on plasma gas atomizers! If you’re here, you’re likely keen to dive deep into the fascinating world of plasma gas atomization, where science meets cutting-edge technology to produce fine metal powders used in a myriad of industries. This article will take you through every aspect of plasma gas atomizers, from their composition and characteristics to their applications and specifications. Buckle up for an engaging journey filled with analogies, metaphors, and an informal tone that makes complex topics easy to understand.
Overview of Plasma Gas Atomizers
Plasma gas atomization is a technique used to produce fine metal powders. Imagine a machine that can transform a solid metal into a mist of tiny droplets, which then solidify into powder particles. That’s essentially what a plasma gas atomizer does. It uses a high-energy plasma torch to melt the metal, which is then atomized into droplets by a stream of gas. These droplets cool down rapidly, forming fine, spherical metal powders.
This method is popular in industries that require high-quality metal powders, such as additive manufacturing (3D printing), aerospace, and biomedical engineering. The metal powders produced are prized for their uniform size, high purity, and excellent flowability.
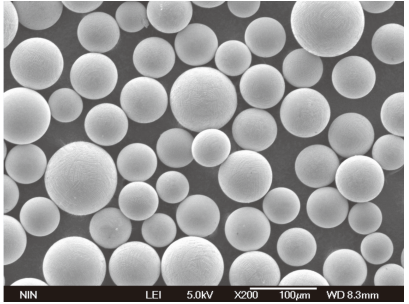
Types of Metal Powders Produced
Here’s a list of specific metal powder models produced by plasma gas atomizers, each with its unique properties and applications:
Metal Powder Model | Composition | Properties | Applications |
---|---|---|---|
Ti-6Al-4V | Titanium alloy | High strength, corrosion resistance | Aerospace, biomedical implants |
Inconel 718 | Nickel-chromium alloy | High temperature, oxidation resistance | Turbine blades, aerospace |
316L Stainless Steel | Iron, chromium, nickel | Corrosion resistance, biocompatibility | Medical devices, marine applications |
AlSi10Mg | Aluminum-silicon-magnesium alloy | Lightweight, high thermal conductivity | Automotive, aerospace |
CoCrMo | Cobalt-chromium-molybdenum alloy | Wear resistance, high strength | Dental implants, orthopedic devices |
NiCoCrAlY | Nickel-cobalt-chromium-aluminum-yttrium | Thermal stability, oxidation resistance | Thermal barrier coatings |
CuSn10 | Copper-tin alloy | High electrical conductivity, wear resistance | Electrical components, bearings |
FeNiCo | Iron-nickel-cobalt alloy | Magnetic properties | Electronics, magnetic applications |
Ti-48Al-2Cr-2Nb | Titanium-aluminum-chromium-niobium alloy | High temperature, lightweight | Aerospace, automotive |
Al7075 | Aluminum-zinc-magnesium-copper alloy | High strength-to-weight ratio | Aerospace, sporting goods |
Composition of Plasma Gas Atomizer Metal Powders
The composition of metal powders produced by plasma gas atomizers can vary widely depending on the specific alloy and its intended application. For instance, Ti-6Al-4V, a popular titanium alloy, consists of titanium, aluminum, and vanadium, providing an excellent balance of strength, weight, and corrosion resistance. On the other hand, Inconel 718, a nickel-chromium alloy, is renowned for its ability to withstand high temperatures and resist oxidation.
Detailed Composition Table
Metal Powder Model | Elemental Composition |
---|---|
Ti-6Al-4V | Ti (90%), Al (6%), V (4%) |
Inconel 718 | Ni (50-55%), Cr (17-21%), Fe (balance), Nb (4.75-5.5%), Mo (2.8-3.3%) |
316L Stainless Steel | Fe (balance), Cr (16-18%), Ni (10-14%), Mo (2-3%) |
AlSi10Mg | Al (balance), Si (9-11%), Mg (0.2-0.45%) |
CoCrMo | Co (balance), Cr (26-30%), Mo (5-7%) |
NiCoCrAlY | Ni (balance), Co (17-23%), Cr (12-19%), Al (5-11%), Y (0.2-0.6%) |
CuSn10 | Cu (balance), Sn (9-11%) |
FeNiCo | Fe (balance), Ni (29-30%), Co (10-20%) |
Ti-48Al-2Cr-2Nb | Ti (balance), Al (48%), Cr (2%), Nb (2%) |
Al7075 | Al (balance), Zn (5.1-6.1%), Mg (2.1-2.9%), Cu (1.2-2.0%) |
Characteristics of Plasma Gas Atomizer Metal Powders
When it comes to the characteristics of these metal powders, several factors come into play, including particle size distribution, morphology, purity, and flowability. Let’s break these down:
- Particle Size Distribution: Plasma gas atomization typically produces metal powders with a uniform particle size distribution, which is crucial for applications like 3D printing where consistency is key.
- Morphology: The particles produced are generally spherical, contributing to better flowability and packing density, essential for processes like powder bed fusion in additive manufacturing.
- Purity: The high-energy plasma environment ensures that the metal powders are highly pure, with minimal contamination from other elements or oxides.
- Flowability: Spherical particles flow more easily than irregularly shaped ones, making these powders ideal for applications where precise control of the material is needed.
Properties Table
Property | Description |
---|---|
Particle Size | Typically ranges from 10 to 100 microns |
Shape | Mostly spherical |
Purity | >99% |
Flowability | Excellent |
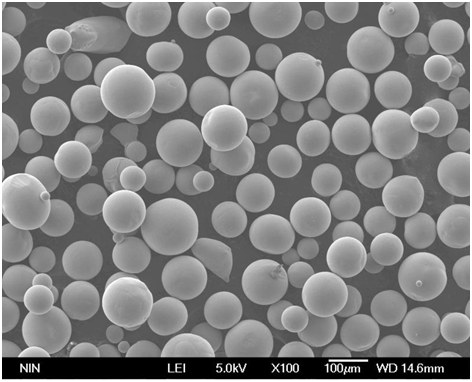
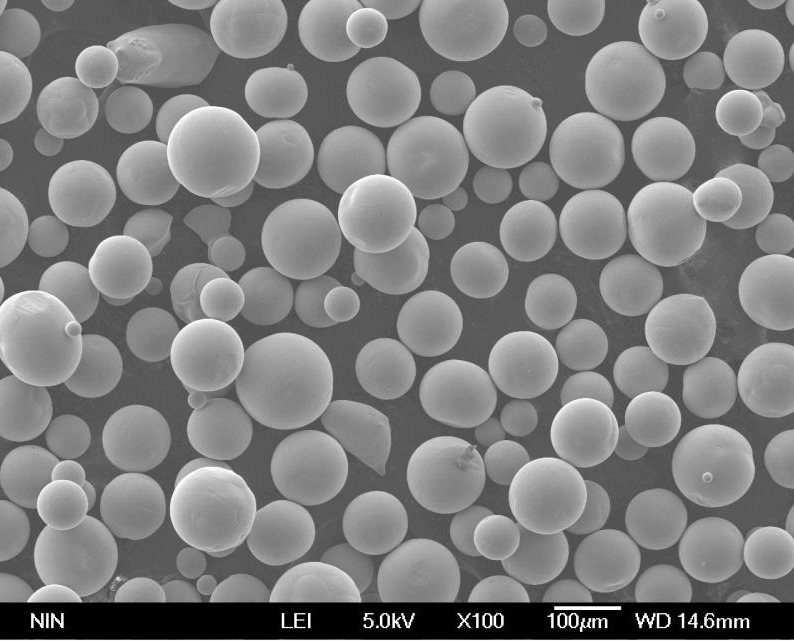
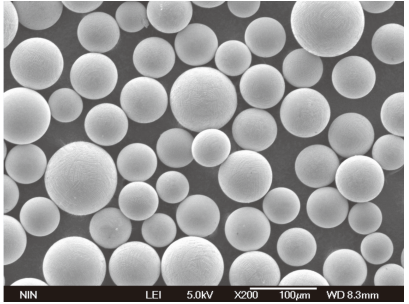
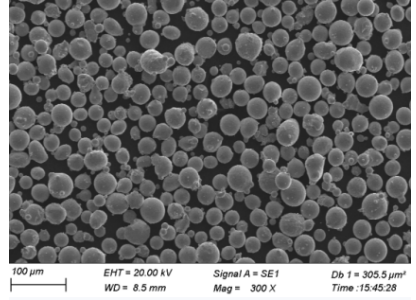

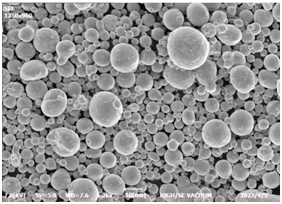
Applications of Plasma Gas Atomizer Metal Powders
The metal powders produced by plasma gas atomizers find applications across a wide range of industries. Here are some of the key applications:
Applications Table
Industry | Application | Metal Powder Models |
---|---|---|
Aerospace | Turbine blades, structural components | Inconel 718, Ti-6Al-4V |
Biomedical | Implants, dental prosthetics | CoCrMo, Ti-6Al-4V |
Automotive | Engine components, lightweight structures | AlSi10Mg, Ti-48Al-2Cr-2Nb |
Electronics | Magnetic materials, conductive components | FeNiCo, CuSn10 |
Additive Manufacturing | 3D printing of prototypes and parts | All models |
Specifications, Sizes, Grades, and Standards
When selecting metal powders for specific applications, it’s crucial to consider their specifications, sizes, grades, and standards. These factors ensure that the powders meet the necessary requirements for performance and safety.
Specifications Table
Metal Powder Model | Size Range | Grade | Standard |
---|---|---|---|
Ti-6Al-4V | 15-45 microns | Grade 5 | ASTM F2924 |
Inconel 718 | 20-63 microns | UNS N07718 | AMS 5662 |
316L Stainless Steel | 15-45 microns | Grade 316L | ASTM F138 |
AlSi10Mg | 20-60 microns | Grade A | ISO 3522 |
CoCrMo | 10-50 microns | ASTM F75 | ASTM F75 |
NiCoCrAlY | 10-80 microns | Custom grades | ISO 15156-3 |
CuSn10 | 15-63 microns | CW453K | EN 1982 |
FeNiCo | 20-100 microns | Custom grades | IEC 60404-8-6 |
Ti-48Al-2Cr-2Nb | 20-45 microns | Custom grades | AMS 4822 |
Al7075 | 15-63 microns | Grade 7075 | ASTM B211 |
Suppliers and Pricing Details
When it comes to sourcing metal powders, numerous suppliers offer a range of products. Pricing can vary significantly based on the material, quantity, and quality.
Suppliers and Pricing Table
Supplier | Metal Powder Model | Price (per kg) |
---|---|---|
AP&C | Ti-6Al-4V | $300 – $400 |
Praxair Surface Technologies | Inconel 718 | $200 – $350 |
Sandvik | 316L Stainless Steel | $100 – $200 |
LPW Technology | AlSi10Mg | $80 – $150 |
Carpenter Additive | CoCrMo | $250 – $400 |
HC Starck | NiCoCrAlY | $300 – $500 |
Höganäs | CuSn10 | $50 – $100 |
Kennametal | FeNiCo | $150 – $250 |
ATI Powder Metals | Ti-48Al-2Cr-2Nb | $400 – $600 |
Valimet | Al7075 | $100 – $200 |
Pros and Cons of Plasma Gas Atomizer Metal Powders
Understanding the advantages and limitations of plasma gas atomizer metal powders can help you make informed decisions.
Comparison Table
Aspect | Advantages | Limitations |
---|---|---|
Particle Size | Uniform distribution | Can be limited in size range |
Shape | Spherical particles | Higher cost of production |
Purity | High purity levels | Requires stringent control |
Flowability | Excellent flow characteristics | Can be affected by humidity |
Applications | Wide range of applications | Some metals are expensive |
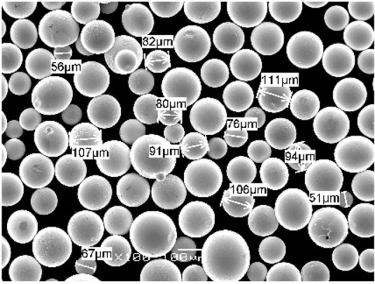
FAQ
Question | Answer |
---|---|
What is plasma gas atomization? | Plasma gas atomization is a process that uses a plasma torch to melt metal and atomize it into fine droplets, which solidify into spherical powders. |
Why are spherical metal powders preferred? | Spherical powders have better flowability and packing density, which are crucial for processes like additive manufacturing. |
What are some common applications of these metal powders? | They are used in aerospace, biomedical implants, automotive components, and electronics. |
How does the particle size affect the application? | Smaller, uniform particles provide better precision and consistency in manufacturing processes. |
What factors influence the cost of metal powders? | Material type, production method, purity, and supplier can all affect the price. |
Are there any environmental concerns with plasma gas atomization? | The process is relatively clean, but energy consumption and raw material sourcing can have environmental impacts. |
How do I choose the right metal powder for my application? | Consider the material properties, application requirements, and cost. Consulting with suppliers can also provide guidance. |
Can I customize the composition of metal powders? | Yes, many suppliers offer custom compositions to meet specific needs. |
What are the main advantages of plasma gas atomization compared to other methods? | Higher purity, spherical particles, and uniform size distribution are key advantages. |
Where can I buy these metal powders? | Numerous suppliers like AP&C, Praxair, and Sandvik offer a wide range of metal powders. |
Conclusion
In conclusion, plasma gas atomizers play a crucial role in producing high-quality metal powders used in various advanced manufacturing processes. Whether you’re in aerospace, biomedical, automotive, or electronics, understanding the composition, characteristics, and applications of these powders can significantly impact your project’s success. With this comprehensive guide, you’re now equipped with the knowledge to navigate the world of plasma gas atomizers with confidence. Happy manufacturing!