Overview of Refractory Metal Powders
When you think of materials that can withstand extreme conditions, refractory metals are the unsung heroes of the periodic table. These metals are used in a myriad of high-temperature applications, ranging from aerospace to industrial manufacturing. But what exactly are refractory metal powders, and why are they so critical in advanced technologies?
Refractory metal powders are finely divided particles of metals that have exceptionally high melting points and are highly resistant to wear, corrosion, and deformation. The most common refractory metals include tungsten, molybdenum, tantalum, niobium, and rhenium. These powders are used in the manufacturing of components that need to perform under extreme conditions, such as in jet engines, nuclear reactors, and even space exploration.
The importance of refractory metal powders cannot be overstated. Their unique properties allow them to be used in environments where other materials would fail. Whether you’re an engineer, a scientist, or just someone with a keen interest in advanced materials, understanding these powders’ properties, applications, and various types is crucial.
This article dives deep into the world of refractory metal powders, exploring everything from their composition to their applications, and even providing a detailed comparison of different types. Let’s embark on this technical journey together.
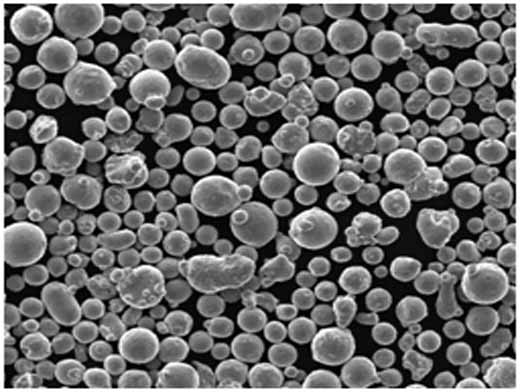
Types and Composition of Refractory Metal Powders
Refractory metal powders come in various types, each with its unique composition and properties. Below is a detailed look at some of the most commonly used refractory metal powders:
Metal Powder | Composition | Melting Point | Density | Key Characteristics |
---|---|---|---|---|
Tungsten (W) | Pure tungsten | 3,422°C | 19.25 g/cm³ | Highest melting point, excellent high-temperature strength, and conductivity. |
Molybdenum (Mo) | Pure molybdenum | 2,623°C | 10.22 g/cm³ | Good thermal conductivity, corrosion resistance, and low thermal expansion. |
Tantalum (Ta) | Pure tantalum | 3,017°C | 16.69 g/cm³ | High ductility, excellent corrosion resistance, and biocompatibility. |
Niobium (Nb) | Pure niobium | 2,468°C | 8.57 g/cm³ | High melting point, excellent corrosion resistance, and superconducting properties. |
Rhenium (Re) | Pure rhenium | 3,185°C | 21.02 g/cm³ | Extremely high melting point, good wear resistance, and catalytic properties. |
Chromium (Cr) | Pure chromium | 1,907°C | 7.19 g/cm³ | High hardness, corrosion resistance, and reflective properties. |
Hafnium (Hf) | Pure hafnium | 2,233°C | 13.31 g/cm³ | Excellent corrosion resistance, high melting point, and neutron-absorbing properties. |
Zirconium (Zr) | Pure zirconium | 1,855°C | 6.52 g/cm³ | High resistance to corrosion, low neutron-capture cross-section, and good ductility. |
Iridium (Ir) | Pure iridium | 2,446°C | 22.56 g/cm³ | Extremely high density, excellent corrosion resistance, and high melting point. |
Osmium (Os) | Pure osmium | 3,033°C | 22.59 g/cm³ | Highest density, high hardness, and excellent wear resistance. |
Characteristics of Refractory Metal Powders
So, what makes refractory metal powders so special? It’s all in the characteristics. These powders boast properties that are not only unique but also essential for high-stress applications. Let’s break down these characteristics:
- High Melting Points: The most notable characteristic of refractory metals is their incredibly high melting points, often exceeding 2,000°C. Tungsten, for example, has the highest melting point of any metal at 3,422°C. This property makes these metals indispensable in applications where extreme heat is a factor, such as in rocket nozzles and furnace components.
- High Density: Refractory metals like tungsten and rhenium are known for their high densities. This makes them ideal for applications requiring materials that can absorb significant amounts of kinetic energy, such as in armor-piercing ammunition.
- Corrosion Resistance: Many refractory metals, particularly tantalum and niobium, exhibit excellent resistance to corrosion, even in harsh chemical environments. This makes them ideal for use in chemical processing equipment and medical implants.
- Wear Resistance: The high hardness of refractory metals like chromium and osmium provides excellent wear resistance, making them suitable for cutting tools, wear-resistant coatings, and high-durability components.
- Thermal and Electrical Conductivity: Despite their high melting points, many refractory metals also possess good thermal and electrical conductivity. This is particularly true for tungsten and molybdenum, making them useful in electrical contacts and heating elements.
- Ductility and Machinability: While some refractory metals are known for their hardness, others, like tantalum, are highly ductile, which means they can be drawn into thin wires without breaking. This ductility is crucial in applications like electronics and aerospace engineering.
Applications of Refractory Metal Powders
Given their unique properties, it’s no surprise that refractory metal powders find their way into a wide array of applications. Here’s a look at where these materials are commonly used:
Application | Refractory Metal Powder Used | Purpose |
---|---|---|
Aerospace Components | Tungsten, Molybdenum | High-temperature resistance in rocket engines, heat shields, and turbine blades. |
Nuclear Reactors | Zirconium, Hafnium | Neutron absorption, corrosion resistance, and structural components in reactors. |
Medical Implants | Tantalum, Niobium | Biocompatibility and corrosion resistance in implants and prosthetics. |
Electronics | Tungsten, Tantalum | Use in capacitors, resistors, and other electronic components due to conductivity and stability. |
Cutting Tools | Tungsten, Chromium | Wear resistance and durability in cutting, drilling, and mining tools. |
Chemical Processing Equipment | Tantalum, Molybdenum | Corrosion resistance in acid and chemical handling equipment. |
Defense and Ammunition | Tungsten, Osmium | High-density materials for armor-piercing ammunition and penetrators. |
Catalysts in Chemical Reactions | Rhenium, Iridium | Catalytic properties in chemical reactions, such as in refining and synthesis processes. |
Superconductors | Niobium | Superconducting properties in magnets, MRI machines, and particle accelerators. |
Jewelry and Watches | Tungsten, Platinum | High durability, corrosion resistance, and aesthetic appeal in luxury items. |
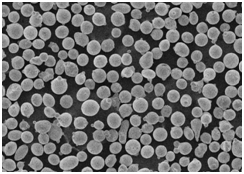
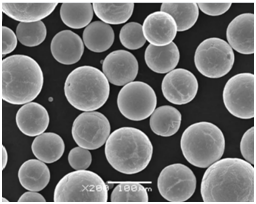
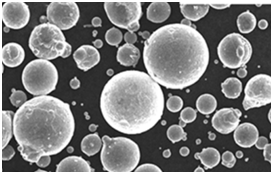
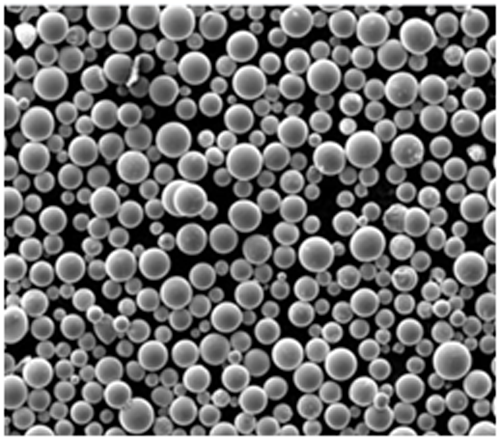
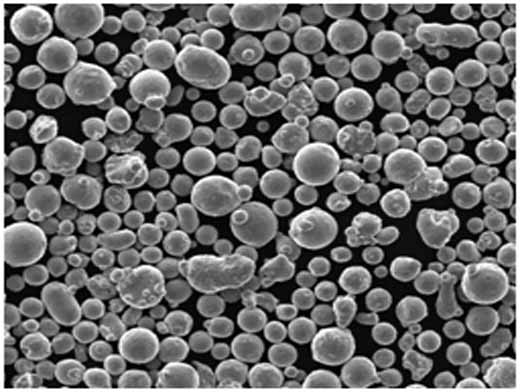
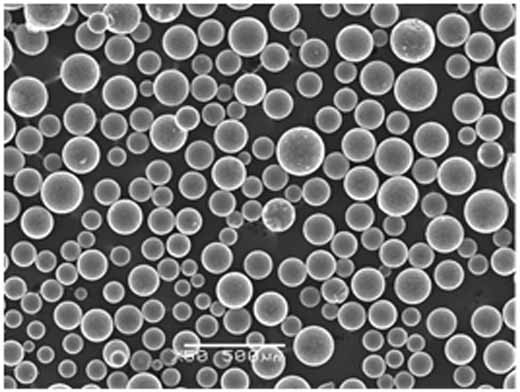
Specifications, Sizes, Grades, and Standards
When dealing with refractory metal powders, it’s important to understand the specifications, sizes, grades, and standards that govern their use. These parameters ensure that the right material is used for the right application, and that performance is consistent and reliable.
Refractory Metal | Particle Size | Grade | Standard | Typical Application |
---|---|---|---|---|
Tungsten | 0.5 – 10 µm | W1, W2, W3 | ASTM B777 | High-temperature components, electrical contacts. |
Molybdenum | 1 – 15 µm | Mo1, Mo2 | ASTM B386 | Heating elements, thermal spray coatings. |
Tantalum | 0.5 – 5 µm | Ta1, Ta2 | ASTM B521 | Medical implants, chemical processing equipment. |
Niobium | 1 – 20 µm | Nb1, Nb2 | ASTM B392 | Superconductors, nuclear reactors. |
Rhenium | 0.1 – 5 µm | Re1, Re2 | ASTM F1760 | Catalysts, high-temperature thermocouples. |
Chromium | 1 – 50 µm | Cr1, Cr2 | ASTM B835 | Wear-resistant coatings, alloy production. |
Hafnium | 0.2 – 10 µm | Hf1, Hf2 | ASTM B776 | Nuclear reactors, aerospace components. |
Zirconium | 1 – 25 µm | Zr1, Zr2 | ASTM B551 | Chemical processing, nuclear reactors. |
Iridium | 0.1 – 10 µm | Ir1, Ir2 | ASTM B785 | Electrical contacts, spark plugs. |
Osmium | 0.5 – 5 µm | Os1, Os2 | Custom specifications | Wear-resistant coatings, alloy production. |
Suppliers and Pricing Details
Finding the right supplier for refractory metal powders is crucial, as the quality and consistency of the powder can significantly impact your application. Pricing can vary based on factors like purity, particle size, and supply chain dynamics.
Supplier | Refractory Metals Offered | Average Price (per kg) | Region | Specialty |
---|---|---|---|---|
H.C. Starck | Tungsten, Molybdenum, Tantalum, Niobium | $500 – $2,000 | Global | High purity powders, customized particle sizes, consistent quality. |
Global Tungsten & Powders | Tungsten, Rhenium, Tantalum | $600 – $2,500 | North America, Europe | High-performance powders for aerospace, defense, and industrial applications. |
ATI | Tungsten, Hafnium, Zirconium | $450 – $1,800 | United States | Reliable supply for critical industries, wide range of refractory metals. |
Plansee | Molybdenum, Tungsten, Niobium | $400 – $1,500 | Europe, Asia | Specializes in high-temperature applications, custom alloy production. |
Rhenium Alloys, Inc. | Rhenium, Molybdenum-Rhenium Alloys | $2,000 – $10,000 | United States | Niche markets, customized alloys, high-performance materials. |
Zhuzhou Cemented Carbide Group | Tungsten, Chromium, Tantalum | $300 – $1,200 | China | Large-scale production, competitive pricing, reliable quality. |
Treibacher Industrie AG | Tungsten, Tantalum, Niobium | $500 – $2,000 | Europe, North America | High purity materials, custom solutions, strong R&D support. |
CBMM | Niobium | $800 – $3,000 | Global | Leading producer of niobium, strong focus on quality and innovation. |
JSC Chepetsky | Zirconium, Hafnium | $600 – $2,200 | Russia, Europe | Specializes in nuclear-grade materials, high-purity powders. |
American Elements | All refractory metals | $400 – $10,000 | Global | Wide range of products, small to large quantities, focus on innovation. |
Advantages and Limitations of Refractory Metal Powders
While refractory metal powders offer incredible benefits, they also come with certain limitations. Here’s a comparison of their pros and cons:
Advantage | Limitation |
---|---|
High-Temperature Resistance: Refractory metals can withstand extreme temperatures, making them ideal for high-stress applications like aerospace and nuclear reactors. | Cost: These metals are often expensive due to their rarity and the complexity of extraction and processing. |
Corrosion Resistance: Metals like tantalum and niobium are highly resistant to corrosion, making them suitable for chemical processing and medical applications. | Machining Difficulty: Some refractory metals are difficult to machine due to their hardness and brittleness. |
High Density: The high density of metals like tungsten and osmium makes them suitable for applications requiring weight and kinetic energy absorption, such as in defense and aerospace. | Availability: Certain refractory metals, like rhenium and iridium, are rare and have limited availability, which can lead to supply chain challenges. |
Wear Resistance: Refractory metals like chromium offer excellent wear resistance, which is crucial for cutting tools and wear-resistant coatings. | Oxidation: Some refractory metals, particularly molybdenum and tungsten, are prone to oxidation at high temperatures unless protected by coatings or in inert environments. |
Ductility: Metals like tantalum are highly ductile, allowing them to be formed into complex shapes without cracking, which is essential for electronic components and medical devices. | Toxicity: Some refractory metals and their compounds can be toxic, requiring careful handling and disposal. |
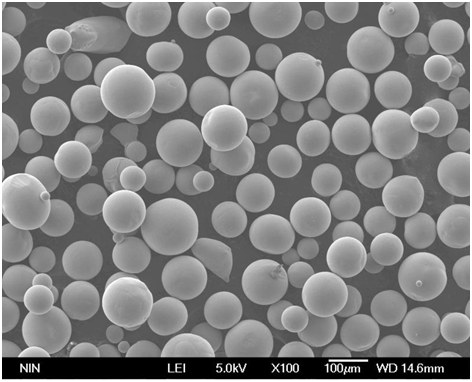
FAQs
Question | Answer |
---|---|
What are refractory metal powders? | Refractory metal powders are fine particles of metals with high melting points, used in applications requiring extreme heat and wear resistance. |
Why are refractory metals expensive? | These metals are often rare and difficult to extract and process, which drives up their cost. |
What is the hardest refractory metal? | Tungsten is considered the hardest refractory metal, with a Mohs hardness of 7.5. |
Can refractory metals be machined? | Yes, but some are difficult to machine due to their hardness and brittleness, requiring specialized tools and techniques. |
Are refractory metals safe to use? | Generally, yes, but some can be toxic or hazardous in certain forms, requiring proper handling and safety precautions. |
Which refractory metal has the highest melting point? | Tungsten has the highest melting point of any metal, at 3,422°C. |
How are refractory metal powders made? | They are typically produced through processes like hydrogen reduction, carbothermal reduction, or electrolysis. |
What industries use refractory metal powders? | Industries like aerospace, defense, electronics, medical, nuclear, and chemical processing heavily use these powders. |
Can refractory metals resist corrosion? | Yes, metals like tantalum and niobium are highly resistant to corrosion, even in aggressive chemical environments. |
Why are refractory metals important in nuclear reactors? | Their high melting points and resistance to radiation damage make them essential for components in nuclear reactors. |