Overview of Electron Beam Additive Manufacturing (EBAM)
Imagine being able to build complex metal parts layer by layer with incredible precision and minimal waste. Sounds like something out of a sci-fi movie, right? Well, welcome to the world of Electron Beam Additive Manufacturing (EBAM). This cutting-edge technology uses an electron beam to melt metal powder or wire, creating 3D objects with intricate details and robust properties.
EBAM stands out in the additive manufacturing landscape for its ability to produce high-quality, high-strength components, particularly for aerospace, automotive, and medical applications. Let’s dive into the specifics of how EBAM works, the types of metal powders used, their properties, and why this technology is revolutionizing manufacturing.
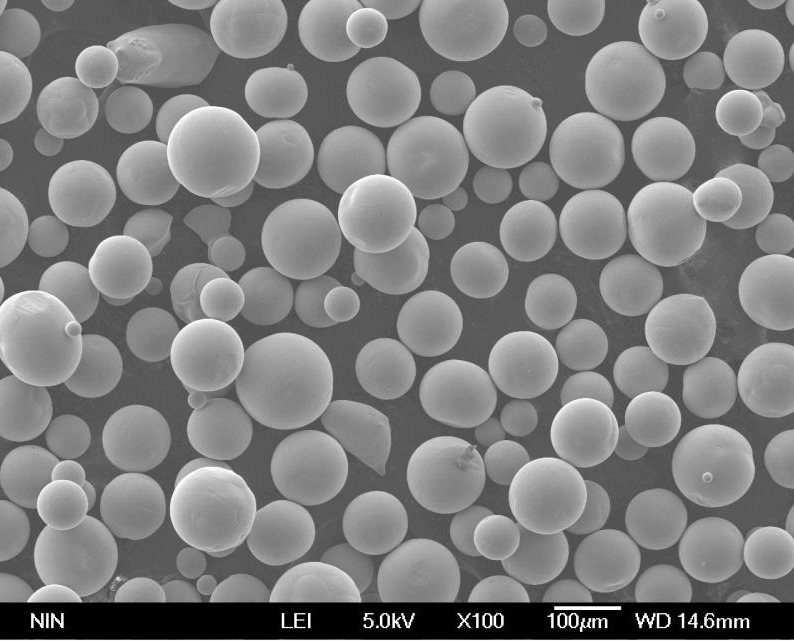
Types of Metal Powders for EBAM
Metal Powder | Composition | Properties | Characteristics |
---|---|---|---|
Titanium (Ti-6Al-4V) | Ti, Al, V | High strength, corrosion-resistant | Lightweight, biocompatible |
Inconel 718 | Ni, Cr, Fe, Nb, Mo | High temperature resistance, durability | Ideal for aerospace and turbines |
Stainless Steel (316L) | Fe, Cr, Ni, Mo | Corrosion resistance, high strength | Common in medical and food industries |
Aluminum (AlSi10Mg) | Al, Si, Mg | Lightweight, good thermal properties | Used in automotive and aerospace |
Cobalt-Chrome (CoCr) | Co, Cr, Mo | Wear-resistant, high strength | Popular in medical implants |
Tool Steel (H13) | Fe, Cr, Mo, V | High toughness, wear resistance | Used in tooling and molds |
Nickel Alloy (Hastelloy X) | Ni, Cr, Fe, Mo | Oxidation and corrosion-resistant | Used in chemical and aerospace industries |
Copper (Cu) | Cu | Excellent conductivity, ductility | Used in electrical and thermal applications |
Titanium (CP-Ti) | Ti | High strength-to-weight ratio, corrosion-resistant | Used in aerospace and medical |
Maraging Steel (18Ni300) | Fe, Ni, Co, Mo | High strength, toughness | Used in aerospace and tooling |
Composition of Electron Beam Additive Manufacturing (EBAM)
The magic of EBAM lies in its materials and their composition. The most common materials used are metal powders or wires, each chosen for specific properties that suit various industrial applications. Let’s break down some of the most popular metal powders used in EBAM:
- Titanium (Ti-6Al-4V): A blend of titanium, aluminum, and vanadium, this alloy offers high strength, lightweight properties, and excellent corrosion resistance. It’s particularly favored in aerospace and medical implants due to its biocompatibility.
- Inconel 718: Comprising nickel, chromium, iron, niobium, and molybdenum, Inconel 718 is known for its high-temperature resistance and durability, making it perfect for turbine engines and other aerospace applications.
- Stainless Steel (316L): This iron-based alloy, with chromium, nickel, and molybdenum, is celebrated for its corrosion resistance and high strength, making it ideal for medical devices and food industry equipment.
- Aluminum (AlSi10Mg): With a composition of aluminum, silicon, and magnesium, this alloy is lightweight and boasts good thermal properties, making it a favorite in the automotive and aerospace sectors.
- Cobalt-Chrome (CoCr): An alloy of cobalt, chromium, and molybdenum, CoCr is wear-resistant and high-strength, commonly used in medical implants.
- Tool Steel (H13): This steel alloy contains iron, chromium, molybdenum, and vanadium, known for its high toughness and wear resistance, used in making molds and tooling.
- Nickel Alloy (Hastelloy X): Comprising nickel, chromium, iron, and molybdenum, this alloy is oxidation and corrosion-resistant, used extensively in chemical processing and aerospace industries.
- Copper (Cu): Pure copper is known for its excellent electrical and thermal conductivity, used in various electrical and heat exchange applications.
- Titanium (CP-Ti): Commercially pure titanium offers a high strength-to-weight ratio and excellent corrosion resistance, suitable for aerospace and medical applications.
- Maraging Steel (18Ni300): This steel alloy, consisting of iron, nickel, cobalt, and molybdenum, provides high strength and toughness, ideal for aerospace and tooling applications.
Characteristics of Electron Beam Additive Manufacturing (EBAM)
EBAM is not just about melting metal; it’s about precision, efficiency, and quality. Here’s a detailed look at the characteristics that make EBAM stand out:
- Precision: EBAM can produce intricate designs with tight tolerances, essential for high-performance components in aerospace and medical fields.
- Efficiency: By using an electron beam, EBAM can quickly melt metal powders or wires, significantly speeding up the manufacturing process compared to traditional methods.
- Versatility: EBAM is compatible with a wide range of metals and alloys, from lightweight aluminum to super-strong titanium and heat-resistant Inconel.
- Strength and Durability: Parts produced with EBAM exhibit excellent mechanical properties, often surpassing those made by conventional manufacturing techniques.
- Minimal Waste: EBAM is an additive process, meaning it builds parts layer by layer, using only the material needed, which minimizes waste and reduces costs.
- Scalability: Whether it’s producing a single prototype or large-scale manufacturing, EBAM offers scalability to meet various production needs.
- Customization: EBAM allows for easy customization of parts, making it ideal for creating bespoke components tailored to specific requirements.
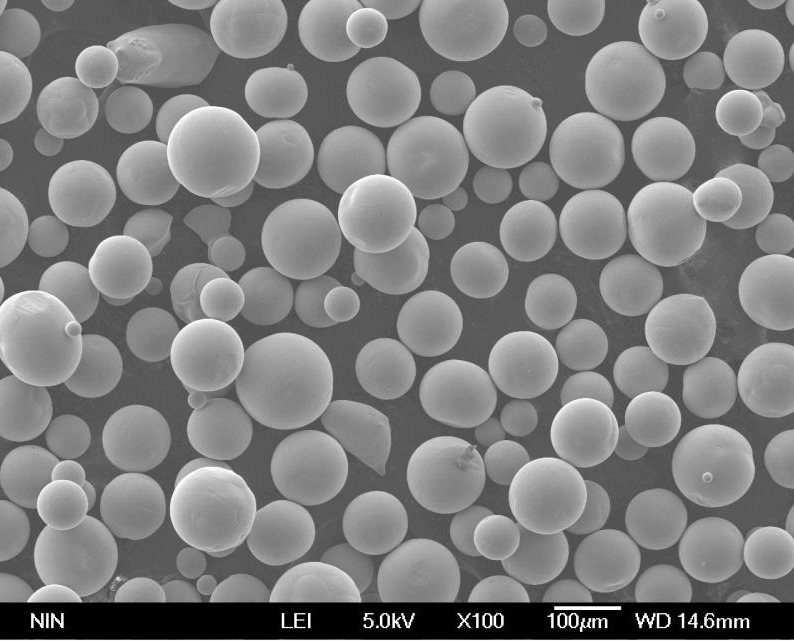
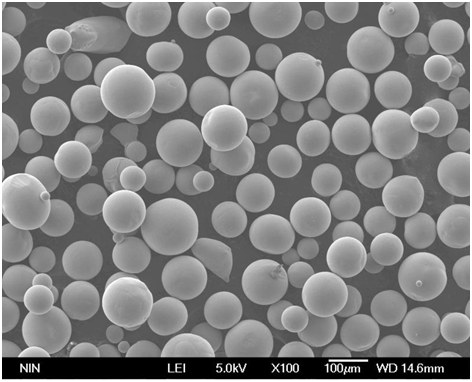

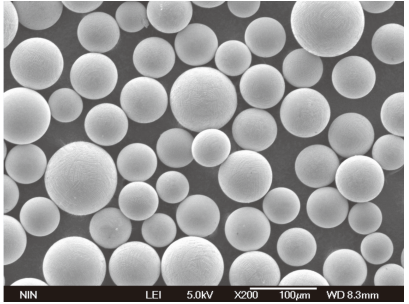
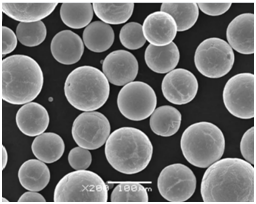
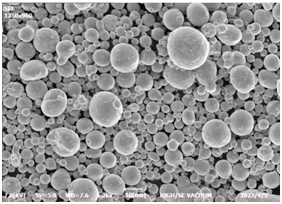
Advantages of Electron Beam Additive Manufacturing (EBAM)
Why should you consider EBAM for your manufacturing needs? Here are some compelling reasons:
- Design Flexibility: EBAM allows for complex geometries that are often impossible with traditional manufacturing methods. Think of intricate lattice structures or internal channels that enhance functionality without adding weight.
- Material Efficiency: Since EBAM uses only the required amount of material, it drastically reduces waste, making it a more sustainable option compared to subtractive manufacturing processes.
- Cost-Effective Prototyping: With EBAM, creating prototypes becomes faster and cheaper, enabling quicker iteration and innovation without the high costs of tooling and molds.
- Enhanced Mechanical Properties: Parts produced by EBAM often exhibit superior mechanical properties due to the fine microstructure achieved through the rapid cooling process.
- High Deposition Rates: EBAM can achieve high deposition rates, translating to faster production times, which is crucial for industries requiring rapid turnaround.
- Reduced Lead Times: By eliminating the need for extensive tooling and allowing for rapid production, EBAM significantly reduces lead times, helping companies bring products to market faster.
Applications of Electron Beam Additive Manufacturing (EBAM)
EBAM’s versatility and precision open up a wide range of applications across various industries. Let’s explore some key areas where EBAM is making a significant impact:
Industry | Application | Benefits |
---|---|---|
Aerospace | Engine components, structural parts | Lightweight, high strength, design flexibility |
Automotive | Custom parts, lightweight components | Reduced weight, increased performance |
Medical | Implants, prosthetics, surgical instruments | Biocompatibility, customization |
Energy | Turbine blades, heat exchangers | High temperature resistance, efficiency |
Tooling | Molds, dies, custom tools | Durability, precision, reduced lead times |
Electronics | Heat sinks, conductive parts | Excellent thermal and electrical conductivity |
Defense | Weapon components, lightweight armor | Strength, durability, lightweight properties |
Specifications, Sizes, Grades, Standards for EBAM Materials
When it comes to EBAM, understanding the specifications, sizes, grades, and standards of materials is crucial for ensuring the desired performance and quality. Here’s a comprehensive table to guide you:
Material | Specifications | Sizes | Grades | Standards |
---|---|---|---|---|
Titanium (Ti-6Al-4V) | ASTM B348, AMS 4928 | 10-45 µm | Grade 5 | ASTM F2924, AMS 4998 |
Inconel 718 | ASTM B637, AMS 5662 | 15-53 µm | – | AMS 5663, ASTM F3055 |
Stainless Steel (316L) | ASTM A276, AMS 5653 | 15-45 µm | – | ASTM F138, ASTM F799 |
Aluminum (AlSi10Mg) | DIN EN 1706 | 20-63 µm | – | ISO 3522 |
Cobalt-Chrome (CoCr) | ASTM F75, ISO 5832-4 | 15-45 µm | – | ASTM F1537 |
Tool Steel (H13) | ASTM A681, AMS 6487 | 15-53 µm | – | ASTM A681 |
Nickel Alloy (Hastelloy X) | ASTM B435, AMS 5754 | 15-45 µm | – | AMS 5536, ASTM B619 |
Copper (Cu) | ASTM B170, ASTM B224 | 15-45 µm | ASTM F68 | |
Titanium (CP-Ti) | ASTM B348, ASTM F67 | 10-45 µm | Grade 1, Grade 2 | AMS 4900, ASTM F1580 |
Maraging Steel (18Ni300) | ASTM A538, AMS 6521 | 15-45 µm | AMS 6514, ASTM A538 |
Suppliers and Pricing Details for EBAM Materials
Finding the right supplier is crucial for ensuring the quality and consistency of EBAM materials. Here’s a list of some reputable suppliers along with pricing details:
Supplier | Material | Price (per kg) | Contact |
---|---|---|---|
Carpenter Technology | Titanium (Ti-6Al-4V) | $250 – $300 | www.carpentertechnology.com |
Sandvik | Inconel 718 | $400 – $450 | www.materials.sandvik |
Praxair Surface Technologies | Stainless Steel (316L) | $150 – $200 | www.praxairsurfacetechnologies.com |
LPW Technology | Aluminum (AlSi10Mg) | $100 – $150 | www.lpwtechnology.com |
Arcam AB | Cobalt-Chrome (CoCr) | $350 – $400 | www.arcam.com |
Höganäs | Tool Steel (H13) | $180 – $220 | www.hoganas.com |
Haynes International | Nickel Alloy (Hastelloy X) | $500 – $550 | www.haynesintl.com |
American Elements | Copper (Cu) | $50 – $100 | www.americanelements.com |
Titanium Processing Center | Titanium (CP-Ti) | $200 – $250 | www.titaniumprocessingcenter.com |
Renishaw | Maraging Steel (18Ni300) | $300 – $350 | www.renishaw.com |
Pros and Cons of Electron Beam Additive Manufacturing (EBAM)
Like any technology, EBAM comes with its set of advantages and limitations. Here’s a comparative look:
Advantages | Disadvantages |
---|---|
High precision and accuracy | High initial setup cost |
Reduced material waste | Requires specialized knowledge and training |
Ability to produce complex geometries | Limited material options compared to other methods |
Faster production times | High energy consumption |
Strong and durable end products | Limited build size |
Customization and flexibility | Post-processing often required |
High deposition rates | Surface finish may require additional work |
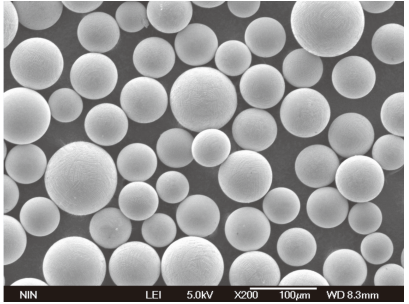
FAQ
Question | Answer |
---|---|
What is EBAM? | EBAM is a 3D printing process that uses an electron beam to melt metal powder or wire to build parts layer by layer. |
How does EBAM differ from other additive manufacturing methods? | EBAM uses an electron beam, offering high precision and the ability to work with high-temperature materials. |
What materials can be used in EBAM? | Common materials include titanium alloys, Inconel, stainless steel, aluminum alloys, and cobalt-chrome. |
What are the main applications of EBAM? | EBAM is used in aerospace, automotive, medical, energy, tooling, electronics, and defense industries. |
Is EBAM cost-effective? | While EBAM has high initial setup costs, it reduces material waste and production time, offering long-term cost savings. |
What are the limitations of EBAM? | EBAM requires specialized equipment and knowledge, has high energy consumption, and is limited by build size. |
How does EBAM ensure part quality? | EBAM provides high precision, but post-processing may be required for surface finishing and achieving desired properties. |
Can EBAM be used for mass production? | Yes, EBAM is scalable and can be used for both prototyping and mass production, depending on the application. |
What are the environmental benefits of EBAM? | EBAM produces minimal waste and uses materials efficiently, contributing to more sustainable manufacturing practices. |
How do I choose the right material for EBAM? | Material choice depends on the required properties and application. Consulting with suppliers and experts can help in making the right decision. |