Engines in high-stress applications endure extreme conditions, necessitating advanced materials capable of withstanding such rigorous demands. The development of these materials, particularly metal powders, is a critical factor in ensuring the durability and efficiency of engines in sectors like aerospace, automotive racing, and heavy machinery. This article dives into the specifics of high-stress engine applications, examining the key materials, their properties, uses, and the intricate details that make them suitable for such challenging environments.
Overview of High-Stress Engine Applications
High-stress engine applications refer to scenarios where engines operate under extreme conditions, such as high temperatures, pressures, and mechanical stresses. These conditions are common in industries like aerospace, automotive racing, and heavy machinery, where the reliability and performance of engines are paramount.
Key Aspects:
- Extreme Operating Conditions: High temperatures, pressures, and mechanical stresses.
- Material Requirements: High strength, temperature resistance, and durability.
- Industries: Aerospace, automotive racing, heavy machinery, and power generation.
The use of metal powders in these applications is critical. These materials are engineered to provide the necessary properties to withstand such extreme conditions, ensuring the longevity and reliability of the engines.
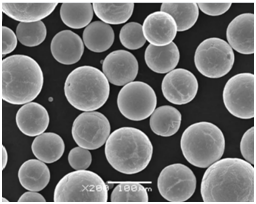
Types of Metal Powders for High-Stress Engine Applications
Metal powders used in high-stress engine applications are specifically engineered to meet the rigorous demands of these environments. Below are ten notable metal powder models, each with unique compositions and properties.
Metal Powder Model | Composition | Properties | Applications |
---|---|---|---|
Inconel 718 | Nickel-Chromium-Iron alloy | High strength, corrosion resistance, excellent weldability | Aerospace engines, gas turbines |
Hastelloy X | Nickel-Chromium-Iron-Molybdenum alloy | High-temperature strength, oxidation resistance | Jet engines, gas turbines |
Tungsten Carbide | Tungsten and Carbon | Extremely hard, high melting point, wear resistance | Cutting tools, wear-resistant parts |
Stellite 6 | Cobalt-Chromium alloy | High wear resistance, corrosion resistance | Valve seats, bushings |
Molybdenum TZM | Molybdenum-Titanium-Zirconium alloy | High strength at high temperatures, creep resistance | Rocket nozzles, furnace parts |
Maraging Steel | Iron-Nickel alloy | High tensile strength, toughness, easy to machine | Aerospace components, tooling |
Aluminum 7075 | Aluminum-Zinc-Magnesium-Copper alloy | High strength, good fatigue resistance | Aircraft structures, high-stress components |
Titanium Aluminide | Titanium and Aluminum | High strength-to-weight ratio, oxidation resistance | Turbine blades, aerospace components |
Nimonic 90 | Nickel-Chromium-Cobalt alloy | High creep resistance, excellent thermal properties | Turbine blades, hot section components |
Rene 41 | Nickel-Chromium alloy | High temperature strength, oxidation resistance | Gas turbines, aerospace engines |
Detailed Descriptions of Metal Powders
- Inconel 718: Known for its incredible tensile strength and resistance to extreme environments, Inconel 718 is a nickel-based superalloy that excels in both high-temperature and high-pressure conditions. Its excellent weldability makes it a preferred choice in aerospace applications.
- Hastelloy X: This alloy is renowned for its performance in high-temperature environments. It offers exceptional oxidation resistance and retains its strength even at elevated temperatures, making it ideal for jet engines and gas turbines.
- Tungsten Carbide: Combining tungsten and carbon, this material is one of the hardest known substances. It’s primarily used in applications requiring extreme wear resistance and the ability to withstand high temperatures, such as cutting tools and wear-resistant parts.
- Stellite 6: A cobalt-chromium alloy, Stellite 6 is used in applications where high wear resistance and corrosion resistance are crucial. It’s commonly found in valve seats, bushings, and other components exposed to harsh conditions.
- Molybdenum TZM: This alloy, containing titanium and zirconium, offers high strength at elevated temperatures and excellent creep resistance. It’s used in high-temperature environments like rocket nozzles and furnace parts.
- Maraging Steel: Known for its ultra-high tensile strength and toughness, maraging steel is a critical material in the aerospace industry. Its ability to be easily machined while maintaining strength makes it valuable for tooling and aerospace components.
- Aluminum 7075: This aluminum alloy is prized for its high strength and good fatigue resistance. It’s extensively used in aerospace structures and other high-stress applications where lightweight materials are beneficial.
- Titanium Aluminide: Offering a high strength-to-weight ratio and excellent oxidation resistance, titanium aluminide is a top choice for turbine blades and other aerospace components that operate under extreme conditions.
- Nimonic 90: This nickel-chromium-cobalt alloy provides high creep resistance and excellent thermal properties. It’s commonly used in turbine blades and other hot section components of engines.
- Rene 41: Known for its high-temperature strength and oxidation resistance, Rene 41 is used in gas turbines and aerospace engines. Its ability to maintain structural integrity under severe conditions makes it invaluable in these applications.
Properties and Characteristics of High-Stress Engine Materials
The materials used in high-stress engine applications need to exhibit specific properties to ensure they can perform under extreme conditions. The table below outlines the critical properties and characteristics of these materials.
Material | Strength | Temperature Resistance | Corrosion Resistance | Wear Resistance | Machinability |
---|---|---|---|---|---|
Inconel 718 | High | Up to 700°C | Excellent | Moderate | Good |
Hastelloy X | High | Up to 1200°C | Excellent | Moderate | Moderate |
Tungsten Carbide | Very High | Up to 1000°C | Good | Excellent | Poor |
Stellite 6 | High | Up to 980°C | Excellent | Excellent | Poor |
Molybdenum TZM | High | Up to 1400°C | Good | Good | Moderate |
Maraging Steel | Very High | Up to 480°C | Moderate | Good | Excellent |
Aluminum 7075 | High | Up to 120°C | Moderate | Good | Excellent |
Titanium Aluminide | High | Up to 800°C | Excellent | Good | Moderate |
Nimonic 90 | High | Up to 920°C | Excellent | Good | Moderate |
Rene 41 | Very High | Up to 980°C | Excellent | Good | Poor |
Characteristics of High-Stress Engine Materials
- Strength: Essential for withstanding mechanical stresses and loads without deformation.
- Temperature Resistance: Ability to retain properties and structural integrity at high temperatures.
- Corrosion Resistance: Crucial for materials exposed to harsh environments and corrosive substances.
- Wear Resistance: Important for components subjected to friction and abrasive conditions.
- Machinability: Affects the ease of manufacturing and shaping the material into the desired components.
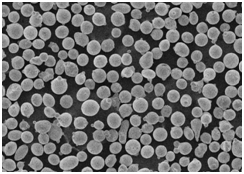
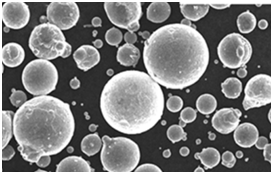

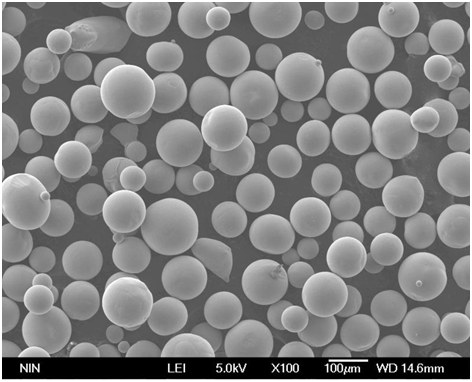
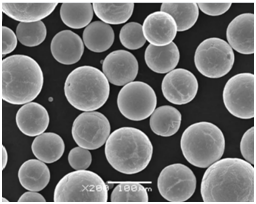
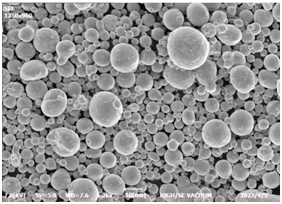
Applications of High-Stress Engine Materials
The unique properties of these metal powders make them suitable for various high-stress engine applications. The table below highlights some common applications.
Application | Materials Used | Reason for Use |
---|---|---|
Aerospace Engines | Inconel 718, Hastelloy X, Nimonic 90 | High strength, temperature resistance, corrosion resistance |
Gas Turbines | Inconel 718, Hastelloy X, Rene 41 | High temperature strength, oxidation resistance |
Rocket Nozzles | Molybdenum TZM, Tungsten Carbide | High temperature resistance, wear resistance |
Valve Seats | Stellite 6, Maraging Steel | Wear resistance, corrosion resistance |
Cutting Tools | Tungsten Carbide, Stellite 6 | Extreme hardness, wear resistance |
Aircraft Structures | Aluminum 7075, Titanium Aluminide | High strength-to-weight ratio, fatigue resistance |
Turbine Blades | Titanium Aluminide, Nimonic 90 | High strength, oxidation resistance |
Heavy Machinery | Maraging Steel, Aluminum 7075 | High tensile strength, good machinability |
Specifications, Sizes, Grades, and Standards
Different applications require materials that meet specific standards and grades to ensure quality and performance. Below is a table outlining the specifications and standards for some of these materials.
Material | Specification | Sizes Available | Grades | Standards |
---|---|---|---|---|
Inconel 718 | ASTM B637 | Rods, sheets, bars | 718 | ASTM, ASME, AMS |
Hastelloy X | ASTM B572 | Sheets, bars, forgings | X | ASTM, ASME, AMS |
Tungsten Carbide | ISO 9001:2015 | Powder, rods, sheets | WC, WC-Co | ISO, ASTM |
Stellite 6 | ASTM F75 | Bars, sheets, rods | 6 | ASTM, AMS |
Molybdenum TZM | ASTM B386 | Rods, sheets | TZM | ASTM, AMS |
Maraging Steel | ASTM A538 | Sheets, bars, rods | 18Ni (250, 300, 350) | ASTM, AMS, MIL-SPEC |
Aluminum 7075 | ASTM B209 | Sheets, plates, bars | 7075-T6, 7075-T651 | ASTM, AMS, QQ-A-250 |
Titanium Aluminide | ASTM B348 | Bars, rods | Ti-6Al-4V, Ti-6Al-2Sn-4Zr-6Mo | ASTM, AMS, MIL-T-9047 |
Nimonic 90 | BS HR1 | Bars, rods, sheets | 90 | BS, AMS, ASTM |
Rene 41 | ASTM B166 | Sheets, rods, bars | Rene 41 | ASTM, AMS |
Suppliers and Pricing Details
Finding reliable suppliers and understanding the pricing is crucial for industries relying on high-stress engine materials. Below is a table with supplier information and estimated pricing.
Material | Supplier | Price per kg (USD) | Location |
---|---|---|---|
Inconel 718 | Special Metals | $60 – $80 | USA |
Hastelloy X | Haynes International | $100 – $120 | USA |
Tungsten Carbide | Global Tungsten & Powders | $90 – $110 | USA |
Stellite 6 | Kennametal | $150 – $180 | USA |
Molybdenum TZM | H.C. Starck | $70 – $90 | Germany |
Maraging Steel | Carpenter Technology | $80 – $100 | USA |
Aluminum 7075 | Alcoa | $10 – $15 | USA |
Titanium Aluminide | ATI | $100 – $130 | USA |
Nimonic 90 | Special Metals | $80 – $100 | UK |
Rene 41 | Special Metals | $90 – $110 | USA |
Comparing Pros and Cons of High-Stress Engine Materials
Understanding the advantages and limitations of each material is crucial for making informed decisions. Below is a comparison of the pros and cons.
Material | Advantages | Limitations |
---|---|---|
Inconel 718 | High strength, excellent weldability | Expensive, difficult to machine |
Hastelloy X | High temperature and oxidation resistance | High cost, limited machinability |
Tungsten Carbide | Extreme hardness, wear resistance | Very brittle, challenging to fabricate |
Stellite 6 | Excellent wear and corrosion resistance | High cost, poor machinability |
Molybdenum TZM | High temperature strength, creep resistance | Expensive, limited ductility |
Maraging Steel | High tensile strength, easy to machine | Moderate corrosion resistance, high cost |
Aluminum 7075 | High strength-to-weight ratio, affordable | Lower temperature resistance |
Titanium Aluminide | High strength-to-weight ratio, oxidation resistance | Expensive, challenging to machine |
Nimonic 90 | High creep resistance, good thermal properties | Expensive, difficult to work with |
Rene 41 | High temperature strength, oxidation resistance | Expensive, poor machinability |
Advantages of High-Stress Engine Applications
The use of advanced metal powders in high-stress engine applications offers several advantages:
- Improved Performance: Materials like Inconel 718 and Hastelloy X enhance engine performance by maintaining strength and stability under extreme conditions.
- Enhanced Durability: The wear resistance of materials like Tungsten Carbide and Stellite 6 extends the lifespan of engine components, reducing maintenance costs.
- Weight Reduction: Alloys like Aluminum 7075 and Titanium Aluminide offer high strength-to-weight ratios, contributing to fuel efficiency and overall performance, especially in aerospace applications.
- Reliability: Using high-quality materials ensures reliability and safety in critical applications like aerospace and power generation.
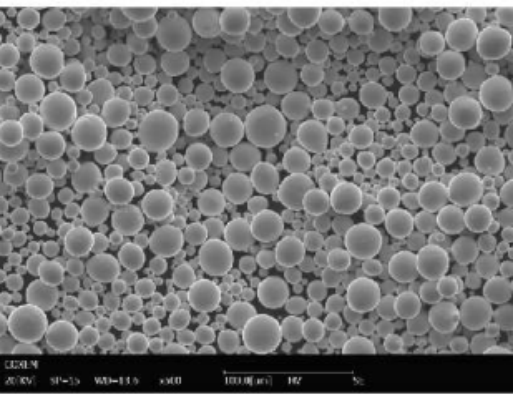
FAQs
What are high-stress engine applications?
High-stress engine applications involve operating conditions that include extreme temperatures, pressures, and mechanical stresses. These are common in industries like aerospace, automotive racing, and heavy machinery.
Why are metal powders used in these applications?
Metal powders are engineered to provide specific properties such as high strength, temperature resistance, and durability, making them ideal for extreme conditions.
What is the role of Inconel 718 in aerospace engines?
Inconel 718 offers high tensile strength, excellent weldability, and corrosion resistance, making it a top choice for aerospace engines.
How do materials like Tungsten Carbide withstand wear?
Tungsten Carbide is extremely hard and has a high melting point, providing excellent wear resistance even under extreme conditions.
Are there affordable high-stress engine materials?
Aluminum 7075 offers a good balance of high strength and affordability, making it suitable for various high-stress applications.