In today’s advanced manufacturing landscape, the production of high-quality metal powders is essential for various applications, from 3D printing to metallurgy. One of the most efficient and effective methods to produce these metal powders is through gas atomization. A gas atomizer machine is a critical piece of equipment in this process. This comprehensive guide will delve into the intricacies of gas atomizer machines, their types, compositions, properties, applications, and more.
Overview of Gas Atomizer Machines
A gas atomizer machine is designed to produce fine metal powders by breaking down molten metal into tiny droplets using a high-velocity gas stream. These droplets then solidify into fine particles, making them suitable for various industrial applications. This method is favored for its ability to produce powders with a uniform size distribution, high purity, and excellent sphericity.
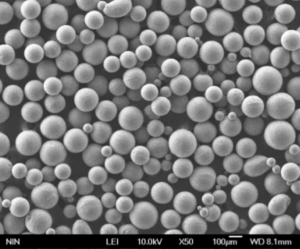
Types and Models of Gas Atomizer Machines
Specific Metal Powder Models
Here are some specific models of metal powders produced using gas atomizer machines, each with unique characteristics and applications:
- 316L Stainless Steel Powder: Known for its corrosion resistance and strength, widely used in medical and aerospace industries.
- 17-4 PH Stainless Steel Powder: Offers high strength and hardness, suitable for aerospace, chemical, and petrochemical industries.
- Titanium Alloy Powder (Ti-6Al-4V): Lightweight and strong, used in aerospace, medical implants, and automotive sectors.
- Inconel 718 Powder: Nickel-based superalloy powder, excellent for high-temperature applications in aerospace and energy sectors.
- Aluminum Alloy Powder (AlSi10Mg): Lightweight with good thermal properties, ideal for automotive and aerospace applications.
- Copper Powder: High thermal and electrical conductivity, used in electronics and heat exchangers.
- Cobalt-Chrome Alloy Powder: High wear and corrosion resistance, used in medical implants and dental applications.
- Tool Steel Powder (H13): High hardness and thermal resistance, used in tooling and molding industries.
- Nickel Alloy Powder (NiCrMo): High-temperature and corrosion resistance, suitable for turbine engines and chemical processing.
- Bronze Powder: Good machinability and wear resistance, used in bearings, bushings, and sculptures.
Composition and Characteristics of Gas Atomizer Machines
Composition of Gas Atomizer Machines
Gas atomizer machines are composed of several key components that work together to produce fine metal powders:
Component | Description |
---|---|
Crucible | Container where the metal is melted. |
Gas Nozzle | Directs high-velocity gas at the molten metal to atomize it. |
Atomization Chamber | Enclosed space where atomization occurs and particles solidify. |
Cyclone Separator | Separates powder from the gas stream. |
Powder Collector | Collects the fine metal powders after atomization. |
Control System | Manages the process parameters, ensuring consistent production quality. |
Characteristics of Gas Atomizer Machines
Gas atomizer machines possess several characteristics that make them suitable for producing high-quality metal powders:
Characteristic | Description |
---|---|
High Purity | Produces powders with minimal contamination. |
Uniform Size | Capable of producing powders with consistent particle size distribution. |
Sphericity | Produces spherical powders, which improve flowability and packing density. |
Scalability | Suitable for both small-scale and large-scale production. |
Versatility | Can atomize a wide range of metals and alloys. |
Efficiency | Efficient in terms of energy consumption and production speed. |
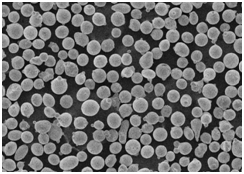
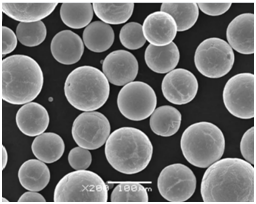
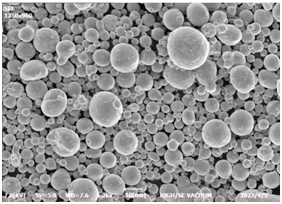
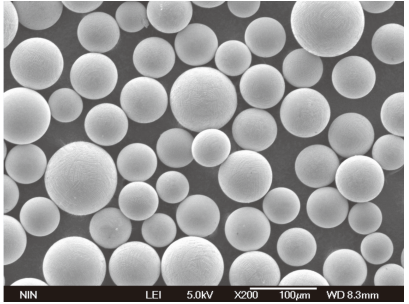
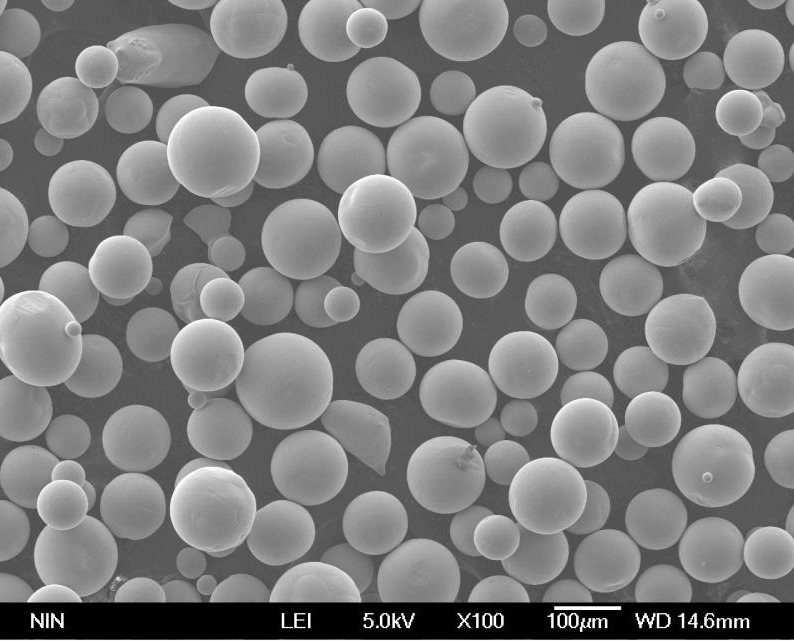
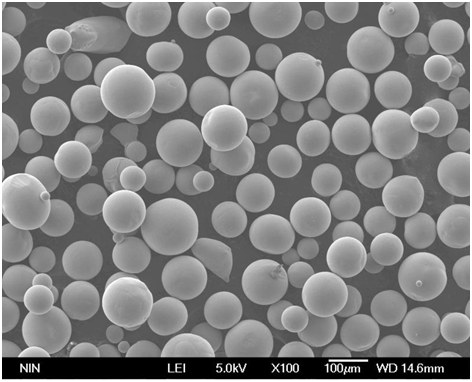
Applications of Gas Atomizer Machine Products
Metal powders produced using gas atomizer machines have a wide range of applications across various industries:
Application | Description |
---|---|
Additive Manufacturing | Used in 3D printing to create complex and precise components. |
Aerospace | Manufacturing high-performance parts that require high strength and lightweight characteristics. |
Medical Implants | Producing biocompatible materials for implants and prosthetics. |
Automotive | Creating components that require high strength and lightweight properties. |
Tooling | Manufacturing durable and high-strength tools and dies. |
Electronics | Producing conductive components for electrical applications. |
Energy Sector | Creating components that can withstand high temperatures and corrosive environments. |
Jewelry | Producing high-quality and intricate designs in precious metals. |
Specifications, Sizes, Grades, and Standards
When selecting a gas atomizer machine or the metal powders it produces, it’s essential to consider specifications, sizes, grades, and standards:
Parameter | Details |
---|---|
Particle Size | Typically ranges from 10 to 150 microns, depending on the application. |
Purity | High purity levels, often exceeding 99.9%. |
Grades | Various grades available depending on the alloy composition and intended use. |
Standards | Adheres to industry standards such as ASTM, ISO, and AMS. |
Production Volume | Capable of producing from a few kilograms to several tonnes per batch. |
Melting Capacity | Varies from small-scale 10 kg systems to large-scale 1000 kg systems. |
Suppliers and Pricing Details
Several suppliers provide gas atomizer machines and the corresponding metal powders, with prices varying based on specifications and quantities:
Supplier | Product | Price Range |
---|---|---|
LPW Technology | Metal powders for AM | $50 – $500 per kg |
Höganäs AB | High-quality metal powders | $100 – $600 per kg |
Sandvik Osprey | Various alloy powders | $150 – $700 per kg |
Carpenter Technology | Specialty alloy powders | $200 – $800 per kg |
GKN Additive | Metal powders for 3D printing | $120 – $650 per kg |
AP&C | Titanium and aluminum alloy powders | $250 – $900 per kg |
Praxair | High-performance metal powders | $180 – $750 per kg |
Erasteel | Tool steel and high-speed steel powders | $140 – $680 per kg |
Arcam AB | Metal powders for EBM systems | $220 – $850 per kg |
VBN Components | Custom alloy powders | $300 – $1000 per kg |
Comparing Pros and Cons
When choosing a gas atomizer machine or its metal powders, it’s essential to weigh the advantages and limitations:
Pros | Cons |
---|---|
High Purity | High Initial Cost |
Uniform Particle Size Distribution | Complex Maintenance Requirements |
Versatile Material Options | Requires Skilled Operators |
Scalability for Large Production Volumes | High Energy Consumption |
Improved Powder Flowability | Potential for Gas Contamination |
Efficient Production Process | Limited to Certain Metals and Alloys |
Composition of Gas Atomizer Machine Products
Detailed Composition of Common Powders
Powder Model | Primary Elements | Secondary Elements |
---|---|---|
316L Stainless Steel | Fe, Cr, Ni, Mo | Mn, Si, P, S |
17-4 PH Stainless Steel | Fe, Cr, Ni, Cu | C, Mn, Si, P, S, Nb |
Ti-6Al-4V | Ti, Al, V | O, N, C, H, Fe |
Inconel 718 | Ni, Cr, Fe, Nb, Mo, Ti, Al | C, Mn, Si, Cu |
AlSi10Mg | Al, Si, Mg | Fe, Cu, Mn, Zn |
Copper | Cu | Pb, Fe, Ni, Zn |
Cobalt-Chrome | Co, Cr | Mo, Ni, Fe, Si |
Tool Steel H13 | Fe, Cr, Mo, Si, V | C, Mn, P, S |
NiCrMo | Ni, Cr, Mo | Fe, C, Mn, Si, Cu |
Bronze | Cu, Sn | Zn, Pb, Ni |
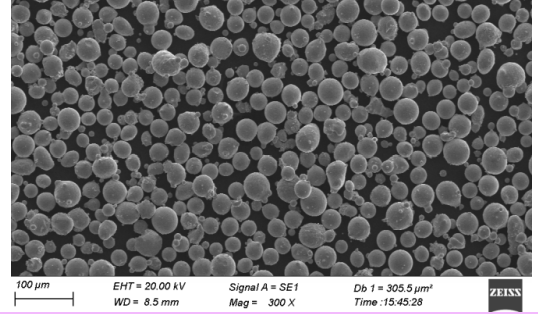
FAQ
Question | Answer |
---|---|
What is a gas atomizer machine? | A machine used to produce fine metal powders by atomizing molten metal using a high-velocity gas. |
What metals can be atomized? | Various metals including stainless steels, titanium, nickel alloys, aluminum, and more. |
What are the applications of metal powders? | Applications include 3D printing, aerospace, medical implants, automotive, tooling, and electronics. |
What are the benefits of gas atomized powders? | Benefits include high purity, uniform size, sphericity, and excellent flowability. |
What is the typical particle size of these powders? | Particle sizes typically range from 10 to 150 microns. |
Are there any limitations to gas atomization? | Limitations include high initial costs and the need for skilled operators. |
How do I choose the right gas atomizer machine? | Consider factors like production volume, metal type, and desired powder characteristics. |
Who are some leading suppliers of these machines? | Suppliers include LPW Technology, Höganäs AB, Sandvik Osprey, Carpenter Technology, and more. |
What are the key characteristics of gas atomized powders? | Key characteristics are high purity, uniform size, sphericity, and good flowability. |
How does gas atomization compare to other methods? | Gas atomization is often preferred for its ability to produce high-quality powders with consistent properties. |
In conclusion, gas atomizer machines are indispensable in modern manufacturing, enabling the production of high-quality metal powders for a wide range of applications. By understanding the various types, compositions, characteristics, and applications of these machines and powders, you can make informed decisions that best suit your needs.