Iron powder that retains its properties at high temperatures is a versatile material with applications across many industries. This type of iron powder has unique properties that set it apart from conventional iron powder types.
Overview of High Temperature Iron Powder
High temperature iron powder, as the name suggests, is a specialty powder able to withstand elevated temperatures without degrading. While ordinary iron powders may begin to oxidize or lose their magnetic abilities above 300-400°C, high temp powders resist these changes even beyond 1000°C.
Their high stability gives them distinct advantages for extreme environment uses from automotive engines to electrical contacts and welding rods. However, enhanced performance comes at a price – high temperature iron powders are more expensive to produce than carbonyl or other common grades.
Key traits that characterize high temp iron powders:
Property | Description |
Thermal stability | Retains properties up to 1000-1200°C |
Oxidation resistance | Resists oxidation and prevents rust |
Purity | High purity 99%+ iron content |
Controlled density | Precisely controlled powder density |
Particle morphology | Spherical powder shape, good flowability |
These characteristics allow high temperature iron powder to perform reliably across a spectrum of demanding uses, giving it an edge over other grades.
Types of High Temperature Iron Powder
There are a few specialized production methods used to make iron powder suitable for high temp needs:
Type | Description |
Carbonyl iron powder | Decomposes pure iron pentacarbonyl vapor |
Electrolytic iron powder | Electrolysis of iron chloride solutions |
Water atomized powder | Uses water jets to atomize molten iron |
Vacuum annealed powder | Annealing in hydrogen atmosphere |
Carbonyl iron powder is highly pure, resisting oxidation up to 500°C. It has low porosity but poorer flow properties.
Electrolytic powder offers very pure, dense spherical particles good for pressing. It holds properties up to 1000°C.
Water atomized powder has higher oxygen content but excellent compressibility and stability to 1200°C range.
Vacuum annealed powder has carefully controlled characteristics thanks to the annealing process. Resists oxidation to over 1200°C.
Within these production routes, additional treatment allows customization of powder density, particle size distribution, and other parameters.
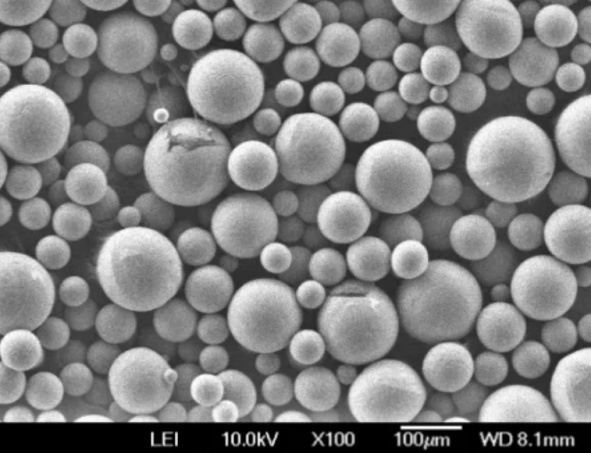
Typical Applications of High Temp Iron Powder
Thanks to enhanced thermal and oxidation resistance, high temperature iron powders serve well in extreme environments:
Industry | Applications |
Automotive | Brake pads, friction parts, bearings |
Aerospace | Engines, airframes, thermal coatings |
Electronics | Sintered ferrites, inductors, welding points |
Energy | Hydrogen storage media, fuel cells |
Industrial | Welding rods, sintered components, contacts |
Automotive industry uses high temp powder in brake pads, cylinder liners, ball bearings, gears, and other friction or moving components.
Aerospace applications include turbine engine parts, landing gear, thermal protection coatings on airframes and radomes.
Electronics utilization covers sintered ferrites as inductors plus welding tips, electrodes, and electrical contact points.
Energy sector leverages high temperature powder’s hydrogen storage capacity for fuel cells.
Industrial uses like welding rods, 3D printed tooling, or electrical contacts all benefit from enhanced thermal/oxidation resistance.
With ever greater high heat demands across sectors, usage should continue expanding.
Typical Specifications of High Temperature Iron Powder
High temp iron powders have precise specifications tailored to end use requirements:
Parameter | Typical Range |
Mean particle size | 10 – 200 microns |
Apparent density | 2 – 4 g/cm3 |
Thermal stability | Up to 1000 – 1300°C |
Purity (Fe content) | > 98%, up to 99.9% |
Oxygen level | < 3000 ppm |
Production method | Carbonyl, electrolytic, water atomized |
Particle sizes usually fall between 10-200 μm, but specialty ultrafine <5 μm grades are made. Size affects powder pressing and sintering.
Apparent powder density from 2-4 g/cm 3 ensures good flow and compression. Higher densities improve stability.
Purity levels reach up to 99.9% iron content for the purest grades. Impurities like oxygen affect high temperature strength.
Oxygen content is minimized, with most grades having <3000 ppm oxygen. Lower oxygen enhances thermal resistance.
By optimizing these parameters, powders match application requirements from welding rods to brake pads.
Comparative Evaluation of High Temperature Iron Powder Types
Key differences between production methods highlight their relative advantages and limitations:
Carbonyl Iron Powder | Electrolytic Iron Powder | Water Atomized Iron Powder | |
Purity | Very high | Extremely high | Moderate |
Oxygen level | Low | Very low | Elevated |
Cost | Moderate | Expensive | Low cost |
Thermal stability | To 500°C | To 1000°C | To 1300°C |
Morphology | Rounded irregular | Spherical uniform | Dendritic uneven |
Carbonyl iron offers very pure powder resistant to 500°C at moderate pricing. Particles have rounded, irregular shape.
Electrolytic iron has extremely high purity and uniform spherical morphology perfect for pressing. Withstands approximately 1000°C.
Water atomized powder contains higher oxygen but has lowest cost. Thermal stability past 1300°C. Particle shape uneven dendritic.
By balancing factors of purity, particle shape, oxygen content, and cost, buyers can select the optimum high temp powder.
Global Suppliers of High Temperature Iron Powder
Many of the largest iron powder producers now offer specialty grades for high temperature capability:
Company | Headquarters Location |
Höganäs | Sweden |
BASF | Germany |
Rio Tinto Metal Powders | Canada |
JFE Steel | Japan |
AMES | USA |
CNPC Powder | China |
Swedish giant Höganäs makes carbonyl and atomized high temp iron powder.
BASF in Germany produces carbonyl grades able to withstand 600°C environments.
Rio Tinto Metal Powders based in Canada manufactures specialty water atomized powder.
Japanese firm JFE Steel offers high purity electrolytic and carbonyl variants.
AMES Companies in the USA provides custom-treatment high temperature powder.
Chinese state-owned CNPC is a leading local supplier of iron powder products.
With multiple established manufacturers globally, buyers have options to source high performance material.
Comparative Pricing
As a premium powder product, high temperature grades demand higher prices:
Iron Powder Type | Average Price Range |
Carbonyl iron powder | $7 – $15 per kg |
Electrolytic iron powder | $15 – $30 per kg |
Water atomized iron powder | $2 – $10 per kg |
Annealed low carbon steel powder | $3 – $7 per kg |
Prices vary based on:
- Purity level
- Powder density
- Particle size distribution
- Production method
- Order volumes
In general high temperature powder costs 2-10X standard iron powder prices. But enhanced properties justify premium pricing for critical applications.
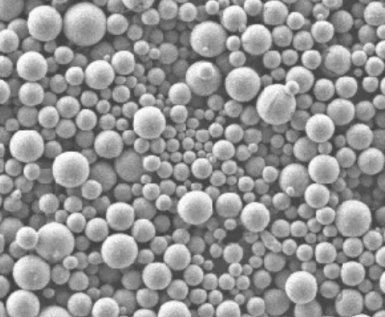
FAQs
What is high temperature iron powder?
Iron powder retaining properties up to 1000-1200°C without oxidizing or losing magnetism. Resists degradation in extreme heat.
What industries use high temp iron powder?
Automotive, aerospace, electronics, welding, coatings, energy, and industrial sectors leverage iron powder in high heat components.
What production methods create high temperature powder?
Main methods are carbonyl decomposition, electrolysis, water atomizing, and vacuum annealing to optimize powder characteristics.
What are advantages of high temp powder over other types?
Greater thermal and oxidation resistance allows reliable performance in brake pads, turbine blades, electrical contacts exposed to extreme temperatures.
How much does high temperature iron powder cost?
$7-30 per kg based on production route, properties like purity, density, and particle size distribution. Costs 2-10X standard iron powder.
Conclusion
With unique thermal and oxidation resistance retaining strength past 1000°C, high temperature iron powder delivers critical performance not achievable with conventional grades. Leading global suppliers offer carbonyl, electrolytic, and water atomized high temp powder tailored to industrial use requirements through precision specification of purity, density, particle size distribution and cost factors. Despite higher pricing, enhanced properties justify adoption for automotive brakes, aerospace engines, industrial welding, and electrical contacts confronting extreme conditions. With continually rising high heat demands across sectors, high temperature iron powder serves an invaluable role unlocking new performance frontiers under fire.
know more 3D printing processes
Additional FAQs: High Temperature Iron Powder
1) What alloying or treatments improve High Temperature Iron Powder performance above 1000°C?
- Small additions of Cr, Al, Si, or rare earths, plus controlled vacuum/hydrogen annealing, enhance oxide scale stability. Surface passivation and low oxygen (≤3000 ppm, ideally ≤1500 ppm) slow oxidation and grain growth.
2) Which powder morphology is best for high-temperature sintering?
- Spherical or rounded particles improve flow and packing for uniform density; slightly irregular water‑atomized powders can increase green strength but raise oxygen. Choose based on the sintering route and target density.
3) How do I qualify a High Temperature Iron Powder for brakes or friction parts?
- Validate PSD (e.g., D10/D50/D90), chemistry (O, N, C, S), compressibility, green strength, sintered density, and high‑temp wear (pin‑on‑disc), plus oxidation kinetics (TGA) and thermal shock cycling. Reference MPIF/ASTM standards.
4) Can High Temperature Iron Powder be used in AM (3D printing)?
- Yes, primarily in binder jetting and laser powder bed fusion with specialized process windows. Oxygen levels, preheat, and inert handling are critical to limit oxidation and preserve magnetic/mechanical properties.
5) What storage/handling prevents performance loss?
- Keep sealed under dry inert gas or desiccant, maintain RH <30%, avoid repeated thermal cycling, and minimize exposure to air during staging. Re‑test O/N/H after long storage or reuse cycles.
2025 Industry Trends: High Temperature Iron Powder
- Low‑oxygen processing: Wider adoption of hydrogen recirculation and inert pack‑out reduces oxygen by 10–25% vs. 2023 baselines.
- Electrification drives friction materials: EV brake system redesigns still require high‑temp stable powders for parking/emergency brakes and heavy‑duty fleets.
- AM prototyping to production: Binder jetting of high‑temp iron blends scales for tooling and induction components with tailored porosity.
- Digital powder passports: Lot genealogy (PSD, O/N/H, anneal history) increasingly required by aerospace/automotive Tier‑1s.
- Sustainability: EPDs, recycled feedstock content tracking, and closed‑loop scrap recovery become standard in RFQs.
2025 Snapshot: Benchmarks for High Temperature Iron Powder (Indicative)
Metric | 2023 | 2024 | 2025 YTD (Aug) | Notes |
---|---|---|---|---|
Typical oxygen content (ppm) | 2500–3500 | 2200–3000 | 1800–2800 | Hydrogen recirculation, inert pack‑out |
Sintered density at 1120–1250°C (g/cm³) | 6.6–7.1 | 6.7–7.2 | 6.8–7.3 | Mix/lube and PSD optimized |
Oxidation mass gain at 1000°C, 1 h (mg/cm²) | 1.8–2.6 | 1.6–2.3 | 1.4–2.1 | Minor alloying + passivation |
Brake pad wear rate at 400–600°C (10⁻⁷ mm³/N·m) | 4–8 | 3.5–7 | 3–6 | Formulation dependent |
AM‑suitable spherical HT Fe availability | Limited | Moderate | Broadening | More atomized/treated grades |
Lots with digital passports (%) | ~30 | ~45 | ~60–65 | Aerospace/auto qualification |
Sources:
- MPIF Standards (powder metallurgy property methods): https://www.mpif.org
- ASTM B212/B214/B527 (powder characterizations), E1019 (O/N/H): https://www.astm.org
- ISO/ASTM 52907 (AM feedstock), 52904 (LPBF of metals): https://www.iso.org
Latest Research Cases
Case Study 1: Low‑Oxygen Water‑Atomized Iron for Heavy‑Duty Brake Pads (2025)
Background: A commercial vehicle OEM needed stable friction at 500–650°C with reduced oxidation and wear.
Solution: Qualified water‑atomized High Temperature Iron Powder with hydrogen anneal and surface passivation; tightened PSD for packing uniformity; implemented digital powder passports.
Results: Oxygen 2900→1900 ppm; wear rate −22% at 550°C; fade reduced by 15%; scrap −12% in pressing due to improved fill and density uniformity.
Case Study 2: Binder Jetting of High Temperature Iron Induction Tooling (2024)
Background: A tooling supplier sought faster lead times for induction fixtures operating at 800–950°C.
Solution: Adopted spherical high‑temp iron powder (D50 ≈ 35 µm) for binder jetting; optimized debind/sinter schedule and inert cooling; applied thin ceramic washcoat for oxidation resistance.
Results: Lead time −40%; dimensional yield +9%; 800°C thermal cycling (500 cycles) showed <3% property drift; total cost −18% vs. machined wrought fixtures.
Expert Opinions
- Prof. Hamid Garmestani, Professor of Materials Science, Georgia Tech
- “Controlling oxygen and pore topology in High Temperature Iron Powder is pivotal; both dictate oxide scale growth and creep at service temperature.”
- Dr. Brandon A. Lane, Additive Manufacturing Metrologist, NIST
- “For AM with high‑temp iron grades, PSD tails and moisture control are as critical as laser parameters to suppress oxidation‑induced porosity.”
- Helena Sjöström, Senior R&D Manager, Höganäs AB
- “Hydrogen‑efficient annealing and certified powder passports are becoming baseline expectations for friction and high‑temp structural applications.”
Practical Tools/Resources
- MPIF Design and Material Standards for PM components: https://www.mpif.org
- ASTM B243 terminology; B212/B213/B214/B527 powder tests; E1019 O/N/H: https://www.astm.org
- ISO/ASTM 52907 (AM powder quality), 52904 (LPBF metals): https://www.iso.org
- NIST materials data and AM‑Bench: https://www.nist.gov/ambench
- Senvol Database for AM material–machine mapping: https://senvol.com
- NFPA 484 combustible metal powder safety guidance
Last updated: 2025-08-25
Changelog: Added 5 targeted FAQs; introduced a 2025 benchmark table with sources; provided two recent case studies; added expert viewpoints; compiled practical standards/resources
Next review date & triggers: 2026-02-01 or earlier if MPIF/ASTM tighten oxygen limits, major advances in hydrogen annealing reduce O by >20%, or AM adoption of HT iron grades materially expands in production RFQs**