Introduction
metal atomization technology is a process where metal is converted from liquid to powder form by disintegrating molten metal into very fine droplets using gas or water. The droplets rapidly solidify into powder particles in the size range of 5 – 500 μm. Atomization technology has enabled production of metal powders with precise particle size distribution, composition, and morphology. Metal powders find applications in manufacturing of components using powder metallurgy, thermal spraying, metal additive manufacturing, etc. This article provides an overview of various methods of atomization, characteristics of atomized powders, and applications across different industries.
Methods of metal atomization technology
There are two main techniques for atomization of metals:
Gas atomization
In gas atomization, molten metal stream is disintegrated by high velocity jets of gas, usually nitrogen or argon. Gas atomization apparatus consists of a melt delivery system, atomization chamber, and powder collection system. The melt delivery system is tundish or crucible with a nozzle at the bottom through which the molten metal flows out. Upon exiting the nozzle, the metal stream is impacted by high pressure gas jets arranged radially or parallel to the melt stream. The gas jets breakup the melt into fine droplets which solidify rapidly as they move down to the collection chamber.
Following are the key advantages of gas atomization:
- Fine powders with average size down to 20 μm can be produced. Particle size distribution is narrow.
- Gas atomized powders have rounded particle morphology ideal for sintering applications.
- Reactive metals like titanium, aluminum can be atomized since the process is carried out in inert atmosphere.
- Multiple gas jets allow large volumes of powders to be produced continuously.
However, gas atomization requires high capital investment and running costs are high due to large gas consumption.
Water atomization
In water atomization, the molten metal stream coming out of the nozzle is disintegrated by jets of water coming from above or from the sides. Water atomization does not require inert gas and is a simpler process. But the particle size range is 100 – 500 μm and powder particles have irregular morphology. Key applications are in powder coating of metal components.
Water atomized powders find limited applications in powder metallurgy since fine powders are not possible. However, water atomization is economical compared to gas atomization.
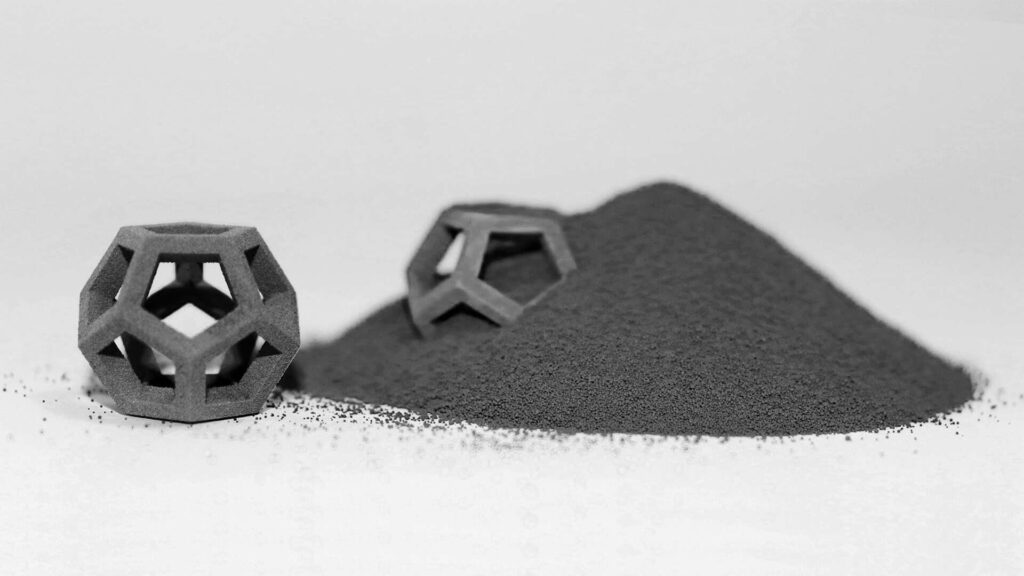
Characteristics of atomized powders
Properties of atomized metal powders depend on composition of the metal alloy as well as the atomization process parameters. By optimizing process parameters, powders with desired characteristics can be produced.
Particle size and shape
- Gas atomized powders have smaller particle size of 5 – 150 μm compared to water atomized powders (100 – 500 μm).
- Water atomized particles have irregular shapes while gas atomized powders have more spherical morphology.
- Particle size distribution is an important parameter. Narrow distribution is preferred for applications like metal additive manufacturing.
Purity
- Gas atomization done under controlled atmosphere results in retention of alloy chemistry in the powder.
- Water atomized powders can have contamination from oxygen absorption.
- Fine powders have large surface area and can readily oxidize when handled in air. Passivation treatments are used to prevent oxidation.
Density
- Rapid solidification during atomization results in refined microstructure. Powder particles have low porosity.
- Gas atomized powders have higher density than water atomized powders.
- Closed porosity in atomized powders improves compressibility during compaction.
Flowability
- Irregular particle shape and wide size distribution leads to poor flow in water atomized powders.
- Fine spherical powders produced by gas atomization have good flowability.
Cost
- Gas atomized powders are 10X more expensive than water atomized powders.
- Cost depends on composition i.e. reactive alloys like titanium are costlier.
- Finer is the powder, higher is the cost. Cost increases exponentially for very fine powders.
Applications of atomized metal powders
Unique characteristics of atomized powders have enabled their use across manufacturing industries.
Powder metallurgy
Atomized powders are compacted and sintered to produce precision components like bearings, gears, magnets etc. Important requirements are:
- Spherical shape and narrow size distribution for high density and uniform compaction
- Fine powders (<100 μm) for greater sintered density
- Low oxygen content to minimize porosity after sintering
Metal additive manufacturing
Also known as 3D printing, it is one of the fastest growing applications of atomized powders. Key material requirements:
- Spherical powder morphology for good flowability
- Particle size between 15-45 μm for precision and surface finish
- Narrow size distribution for uniform layer deposition and density
- Low oxygen content for superior mechanical properties
Titanium and nickel superalloys are common alloys used.
Thermal spray coatings
In thermal spray processes like plasma spray, flame spray etc, atomized powders are heated to melt and sprayed on the component surface. Coatings provide wear and corrosion resistance. Powder characteristics:
- Particle size range suitable for spray technique (10 – 100 μm)
- Low oxygen content for higher coating density and bond strength
- Cost is critical, so water atomized powders commonly used
Metal injection molding (MIM)
MIM combines advantages of plastic injection molding and powder metallurgy to produce small, complex metal parts. Feedstock preparation involves mixing fine metal powder with binder. Requirements:
- Particle size below 20 μm for homogeneous mixing with binder
- Spherical morphology for improved flow during molding
- Narrow size distribution
Advances in atomization technology
Continuous research has led to development of atomization techniques to produce powders with customized properties and new alloys. Some key trends are:
- Multiple gas nozzle configurations to produce finer atomized powders
- Use of close-coupled atomization for reactive alloys like titanium, aluminum
- Hybrid atomization combining gas and water atomization
- Controlled oxidation during water atomization for better powder properties
- Atomization using centrifugal atomization, ultrasonic atomization techniques
- Computer simulations of droplet solidification to optimize atomization process
Development of new lightweight and high strength alloys has also expanded the application areas of atomized powders.
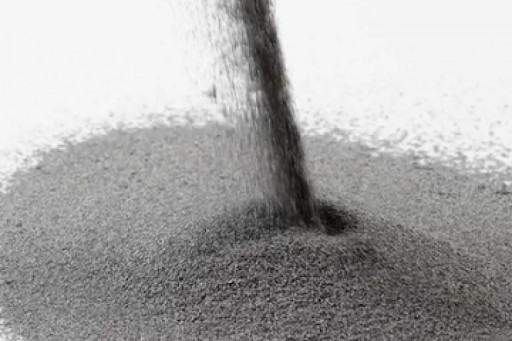
Conclusion
Metal atomization technology produces fine and precisely shaped metal powders suitable for advanced powder-based manufacturing processes. With the ability to control powder characteristics, atomized powders find increasing applications in high performance components across automotive, aerospace, biomedical, and other industries. Ongoing advances will enable manufacturing of tailored materials using atomized powders.
FAQs
What are the different methods used for metal atomization?
The two main methods are gas atomization and water atomization. In gas atomization, molten metal is disintegrated into fine droplets by high velocity jets of inert gas like nitrogen or argon. In water atomization, jets of water impact the molten metal stream coming out of the nozzle tip.
What kind of metals can be atomized?
Most alloys based on aluminum, copper, iron, nickel etc. can be readily atomized. Reactive alloys like titanium and magnesium can also be atomized using controlled atmosphere in gas atomization units. Some examples are aluminum alloys, stainless steels, nickel superalloys, titanium alloys.
What are the major applications of atomized metal powders?
Important applications are powder metallurgy parts manufacturing, metal additive manufacturing using 3D printing, thermal spray coatings, metal injection molding of small precise components, powder forging, production of metal flakes and pastes etc.
How does gas atomization produce finer powders compared to water atomization?
In gas atomization, the high velocity gas jets have sufficient momentum to disintegrate the metal stream into very fine droplets of around 5-50 microns. Also, the rapid cooling rate in gas atomization enables easier breakup into finer droplets. In water atomization, the water jet velocities are lower, resulting in coarser powder of 100 microns and above.
What is the typical cost difference between gas and water atomized powders?
Gas atomized powders are about 10 times more expensive than water atomized powders. This is because gas atomization requires very high capital investment in equipment and high operating costs due to gas consumption. Water atomization units in comparison are inexpensive to set up and operate.