1. Introduction
In the world of advanced materials, titanium has gained significant attention for its remarkable properties and diverse applications. One of the key forms in which titanium is utilized is as titanium powders. This article aims to explore titanium powders in detail, including their properties, production methods, applications, advantages, challenges, safety measures, and future trends.
2. What is Titanium Powder?
Titanium powders refers to the fine particles of titanium powders that are obtained through various manufacturing processes. It is a versatile material with exceptional strength, low density, corrosion resistance, and biocompatibility, making it highly sought after in numerous industries. The powder form of titanium enables its utilization in additive manufacturing, also known as 3D printing, and other applications where precise and intricate shapes are required.
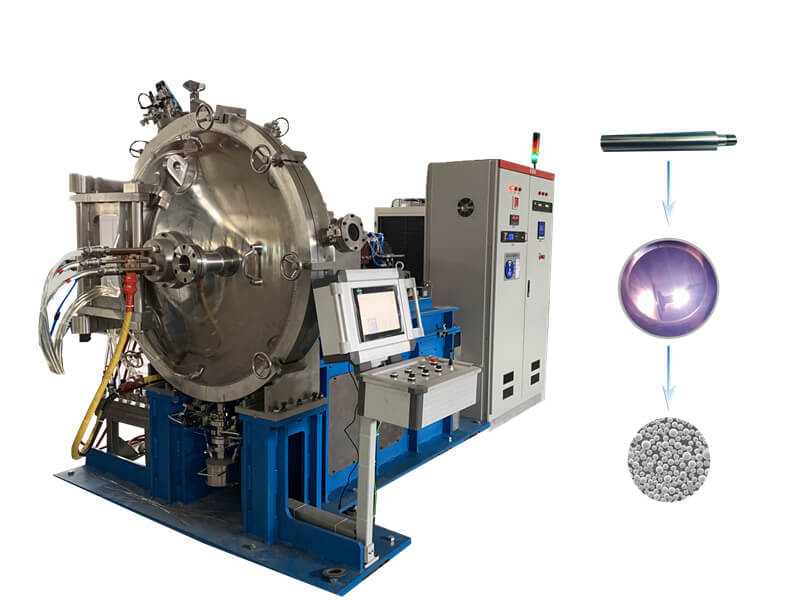
3. Properties of Titanium Powders
3.1 Particle Size and Shape
The particle size and shape of titanium powders play a crucial role in determining its properties and applications. Finer particles provide increased surface area, allowing for better reactivity and sintering capabilities. The shape of the powder particles can vary from spherical to irregular, impacting flowability, packing density, and processability.
3.2 Purity and Composition
The purity and composition of titanium powders are vital considerations, as they directly affect the material’s performance and reliability. High-purity powders ensure minimal impurities, which is especially critical in applications such as aerospace and biomedical fields. Different compositions, such as titanium alloys, offer tailored properties for specific requirements.
3.3 Surface Characteristics
The surface characteristics of titanium powders influence its interactions with surrounding environments. Factors like surface oxidation, contamination, and surface energy can affect powder flow, adhesion, and the quality of the final product. Proper surface treatment and handling techniques are essential to maintain the integrity of titanium powders.
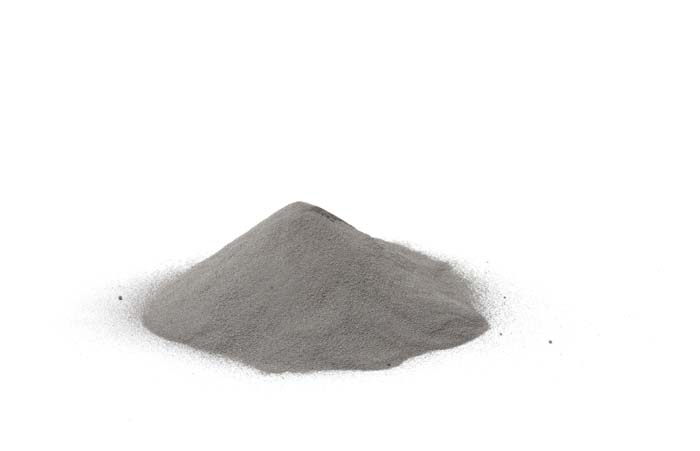
4. Production Methods of Titanium Powder
Several methods are employed to produce titanium powders, each with its own advantages and limitations. The following are some commonly used production methods:
4.1 Hydride-Dehydride (HDH) Process
The Hydride-Dehydride process involves the conversion of titanium sponge or scrap into a hydride form. This hydride is then subjected to a dehydrogenation process, resulting in the production of titanium powders. The HDH process offers good control over particle size, purity, and morphology.
4.2 Armstrong Process
The Armstrong process utilizes the reaction between titanium tetrachloride and magnesium to produce titanium powders. In this method, the titanium tetrachloride is reduced by magnesium in a high-temperature reactor, leading to the formation of titanium powders. The Armstrong process is known for its efficiency and ability to produce high-purity titanium powders.
4.3 Plasma Atomization
Plasma atomization involves the use of a plasma torch to melt a titanium feedstock. The molten titanium is then atomized into fine droplets using high-velocity gas. These droplets solidify into titanium powders upon contact with a cooling medium. Plasma atomization offers control over particle size distribution and the production of spherical particles.
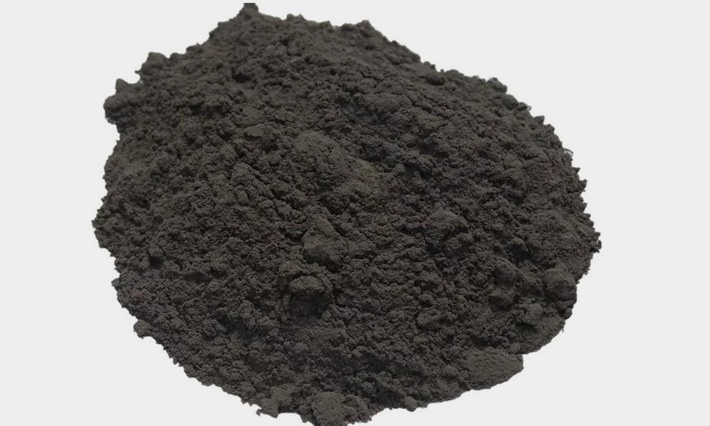
5. Applications of Titanium Powder
Titanium powders finds extensive applications across various industries due to its exceptional properties. Some notable applications include:
5.1 Additive Manufacturing
Titanium powders is widely used in additive manufacturing or 3D printing. Its high strength, lightweight nature, and corrosion resistance make it ideal for fabricating complex components in aerospace, automotive, and medical sectors. Additive manufacturing using titanium powder enables the production of intricate designs with excellent mechanical properties.
5.2 Aerospace and Defense
The aerospace and defense industries extensively utilize titanium powder. It is used in the production of aircraft components, missile systems, engine parts, and structural elements. Titanium’s high strength-to-weight ratio and resistance to extreme temperatures make it an ideal choice for these demanding applications.
5.3 Automotive Industry
In the automotive industry, titanium powders is employed for manufacturing lightweight components that contribute to fuel efficiency and improved performance. Titanium-based alloys find applications in exhaust systems, suspension components, and engine parts, offering durability and corrosion resistance.
5.4 Biomedical and Dental Implants
Titanium powders is highly valued in the medical field for its biocompatibility and corrosion resistance. It is widely used in the production of orthopedic implants, dental implants, and surgical instruments. The ability of titanium to integrate with living tissues makes it a preferred choice for these critical applications.
5.5 Sports Equipment
The sports industry utilizes titanium powders for the production of high-performance sports equipment. Titanium-based alloys are used in the manufacturing of bicycle frames, golf clubs, tennis rackets, and various other athletic gear. The lightweight nature and strength of titanium contribute to enhanced performance and durability.
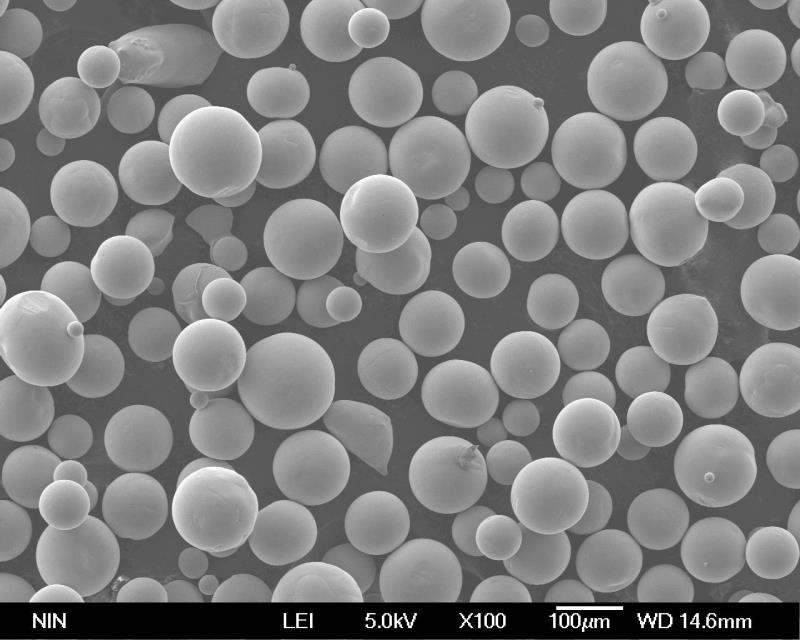
6. Advantages of Using Titanium Powder
Utilizing titanium powder offers several advantages in various applications:
- Exceptional Strength: Titanium powder provides excellent strength-to-weight ratio, ensuring lightweight yet robust components.
- Corrosion Resistance: Titanium exhibits remarkable corrosion resistance, making it suitable for applications in aggressive environments.
- Biocompatibility: Titanium powder is biocompatible, enabling its use in medical and dental implants without adverse reactions.
- Additive Manufacturing Flexibility: Titanium powder allows for intricate designs and complex geometries in additive manufacturing processes.
- Heat Resistance: Titanium exhibits high-temperature resistance, maintaining its structural integrity even in extreme conditions.
7. Challenges in Working with Titanium Powder
While titanium powders offers numerous benefits, certain challenges should be considered when working with this material:
7.1 Fire and Explosion Hazards
Titanium powders is highly reactive with oxygen, posing fire and explosion hazards if not handled properly. The fine particles can ignite in the presence of an ignition source, such as sparks or hot surfaces. Adequate precautions and safety measures are crucial to mitigate these risks.
7.2 Oxidation and Contamination
Titanium powders is susceptible to oxidation and contamination, which can affect its properties and performance. Exposure to moisture and airborne contaminants should be minimized during storage and handling to maintain the integrity of the powder.
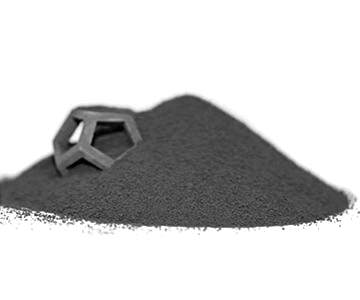
8. Safety Measures for Handling Titanium Powder
To ensure safe handling of titanium powders, the following safety measures should be implemented:
- Personal Protective Equipment (PPE): When working with titanium powders, individuals should wear appropriate PPE, including gloves, goggles, and protective clothing, to minimize the risk of exposure and potential skin irritation.
- Proper Storage and Handling: Titanium powders should be stored in tightly sealed containers in a dry and well-ventilated area. It should be kept away from sources of ignition, moisture, and reactive substances. Proper labeling and storage procedures should be followed to prevent accidents.
- Fire Prevention and Mitigation: Fire prevention measures, such as installing fire suppression systems and using fire-resistant materials, should be in place. In the event of a fire, appropriate fire extinguishing agents for metal fires, such as Class D extinguishers, should be available.
- Ventilation and Dust Control: Adequate ventilation systems should be installed to minimize the concentration of airborne titanium powders particles. Dust control measures, such as using dust collectors and wetting agents, should be implemented to reduce the risk of inhalation and fire hazards.
- Training and Education: Workers handling titanium powders should receive comprehensive training on its properties, handling techniques, and safety protocols. They should be aware of the potential hazards and the proper procedures to minimize risks.
9. Future Trends in Titanium Powder Applications
The utilization of titanium powders is expected to continue growing, driven by advancements in technology and expanding industrial sectors. Some future trends in titanium powder applications include:
- Customized Medical Implants: Titanium powder enables the production of customized medical implants tailored to an individual’s specific needs, promoting better patient outcomes and faster recovery.
- Increased Adoption in Automotive Industry: With a focus on lightweight materials and fuel efficiency, the automotive industry is likely to embrace titanium powder for the production of lightweight and durable components.
- Advancements in Additive Manufacturing: Ongoing research and development in additive manufacturing techniques using titanium powder will lead to improved process efficiency, higher printing speeds, and enhanced part quality.
- Integration in Renewable Energy Technologies: Titanium powder has the potential to play a significant role in renewable energy technologies, such as hydrogen production, due to its corrosion resistance and catalytic properties.
- Exploration of New Alloys and Composites: Researchers are continuously exploring new titanium alloys and composites, further expanding the range of applications and enhancing the material’s performance in specific industries.
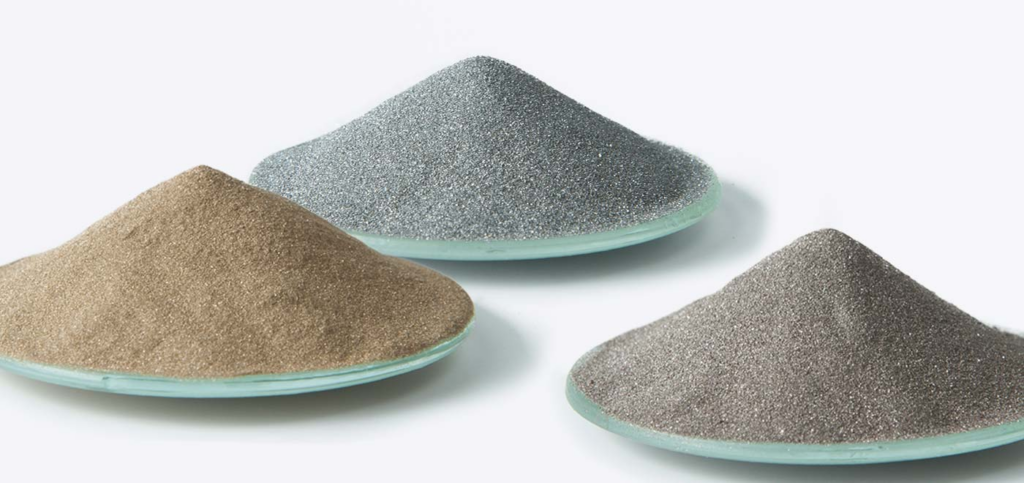
10. Conclusion
Titanium powder offers a myriad of possibilities across industries due to its exceptional properties, including strength, corrosion resistance, and biocompatibility. From additive manufacturing to aerospace, automotive, biomedical, and sports equipment, titanium powder finds applications in various sectors. However, careful handling, adherence to safety protocols, and awareness of potential hazards are essential when working with titanium powder. As technology advances, titanium powder is poised to play an even more significant role in shaping the future of materials and manufacturing.
FAQs
1. Is titanium powder expensive?
Titanium powder can be relatively expensive due to the complex and energy-intensive manufacturing processes involved. However, its unique properties and benefits justify the cost in many applications.
2. Can titanium powder be recycled?
Yes, titanium powder can be recycled and reused in the manufacturing process. Recycling helps reduce waste and minimize the environmental impact associated with titanium production.
3. Are there any health risks associated with titanium powder exposure?
When handled properly, titanium powder poses minimal health risks. However, inhalation of high concentrations of titanium powder particles may irritate the respiratory system. Following safety measures and using appropriate PPE mitigates such risks.
4. What are the advantages of using titanium powder in additive manufacturing?
Titanium powder enables the production of complex and lightweight components with excellent mechanical properties through additive manufacturing. It offers design freedom, reduced material waste, and the ability to fabricate intricate structures that would be challenging with traditional manufacturing methods.
5. Can titanium powder be combined with other materials?
Yes, titanium powder can be combined with other materials to form titanium alloys or composite materials. This allows for the enhancement of specific properties or the creation of tailored materials for specific applications.