1. Introduction
The world of 3D printing has revolutionized manufacturing across various industries, enabling the production of complex geometries and customized parts with unprecedented ease. Among the different materials used in 3D printing, metal powder holds a significant place. Metal powder for 3D printing allows the creation of robust and functional metal parts layer by layer, opening up a wide range of possibilities in engineering, aerospace, healthcare, and other sectors. In this article, we will explore the fascinating world of metal powder for 3D printing, its benefits, applications, types, techniques, and challenges associated with this cutting-edge technology.
2. What is Metal Powder for 3D Printing?
Metal powder for 3D printing refers to fine particles of metallic substances that are specifically designed and manufactured for use in additive manufacturing processes. These powders possess specific characteristics, such as particle size, flowability, and composition, which make them suitable for various 3D printing techniques. Metal powders for 3D printing are typically produced through processes like gas atomization, water atomization, or plasma atomization, ensuring high purity and consistent quality.
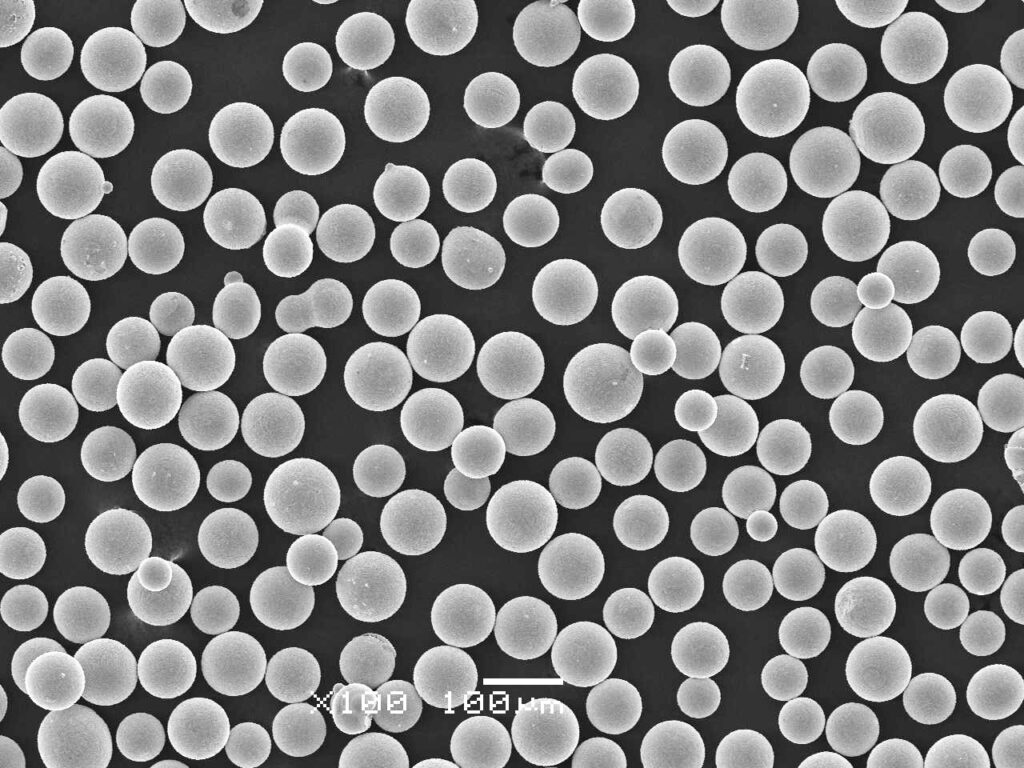
3. Benefits of Using Metal Powder for 3D Printing
Metal powder 3D printing offers several advantages over traditional manufacturing methods. Some key benefits include:
- Design Freedom: metal powder for 3d printing enables the production of highly complex and intricate designs that would be challenging or impossible to achieve with conventional methods. This allows engineers and designers to unleash their creativity and optimize part geometries for enhanced performance.
- Reduced Material Waste: Additive manufacturing with metal powder significantly reduces material waste compared to subtractive manufacturing processes. The ability to add material only where it is needed ensures efficient use of resources, making it a more sustainable option.
- Cost Efficiency: While metal powder 3D printing may have higher upfront costs, it often proves cost-effective in the long run. By eliminating the need for tooling and reducing assembly requirements, companies can save on production costs and achieve faster time-to-market.
- Customization and Personalization: metal powder for 3d printing allows for the production of highly customized and personalized parts. This is particularly beneficial in industries such as healthcare, where patient-specific implants and prosthetics can be created with precision.
- Lightweighting: metal powder for 3d printing enables the creation of lightweight structures without compromising strength and durability. By utilizing advanced lattice structures and optimized designs, components can be printed with internal voids or porous structures, resulting in reduced weight and improved material efficiency.
- Material Diversity: metal powder for 3d printing offers a wide range of materials to choose from, including titanium, aluminum, stainless steel, nickel alloys, and cobalt chrome, among others. This versatility allows engineers to select the most suitable material for their specific application requirements.
- Complex Functionality: metal powder for 3d printing enables the integration of complex functionalities into a single part. By printing intricate internal channels, cooling features, or internal supports, engineers can optimize the performance and functionality of the printed components.
4. Applications of Metal Powder 3D Printing
metal powder for 3d printing finds applications in various industries due to its unique capabilities. Some notable applications include:
- Aerospace: metal powder for 3d printing is widely used in the aerospace industry to produce lightweight components, such as turbine blades, fuel nozzles, and structural parts. The ability to create complex geometries and reduce weight contributes to improved fuel efficiency and performance.
- Medical and Dental: The healthcare sector benefits from metal powder for 3d printing for the production of patient-specific implants, surgical instruments, and dental prosthetics. The ability to create customized, biocompatible parts with excellent mechanical properties enhances patient outcomes.
- Automotive: metal powder for 3d printing plays a crucial role in automotive manufacturing, allowing the production of lightweight and high-performance parts. Engine components, exhaust manifolds, and suspension parts can be manufactured with improved strength-to-weight ratios.
- Tooling: Metal powder 3D printing is employed in the production of complex tooling and molds, enabling faster and cost-effective iterations. Conformal cooling channels and intricate mold geometries enhance productivity and quality in injection molding and die casting processes.
- Architecture: Architects and designers utilize metal powder for 3d printing to create intricate and visually stunning structures. The technology enables the fabrication of complex facades, decorative elements, and artistic installations with high precision.
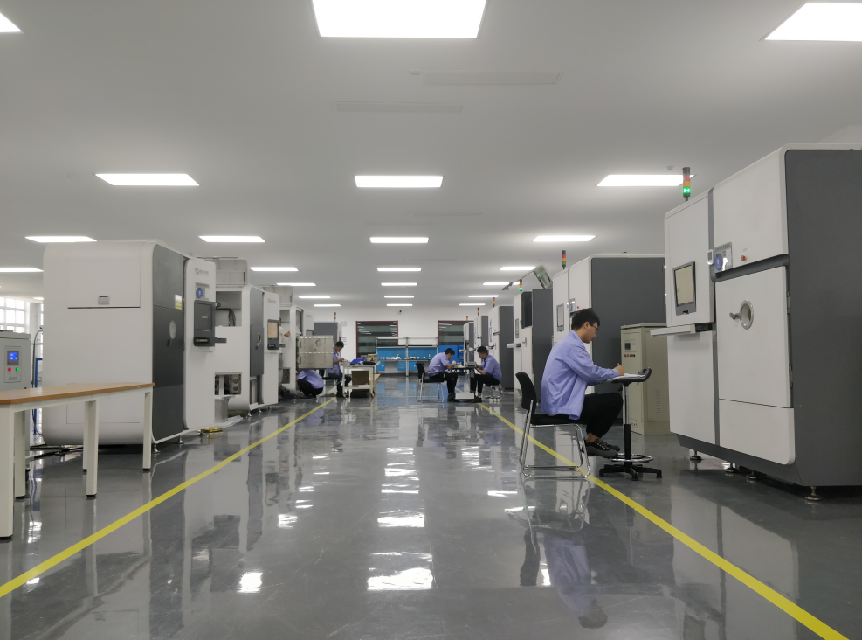
5. Types of Metal Powders Used in 3D Printing
Various metal powders are used in 3D printing, each with its specific properties and applications. Some commonly used metal powders include:
5.1 Titanium Powder
Titanium powder is renowned for its high strength, excellent corrosion resistance, and low weight. It finds applications in aerospace, medical, and automotive industries, where lightweight yet strong components are required.
5.2 Aluminum Powder
Aluminum powder is lightweight, cost-effective, and exhibits good thermal and electrical conductivity. It is used in industries such as aerospace, automotive, and consumer electronics for parts that require high strength and low weight.
5.3 Stainless Steel Powder
Stainless steel powder is widely utilized for its excellent mechanical properties, corrosion resistance, and versatility. It is employed in various industries, including automotive, medical, and consumer goods.
5.4 Nickel Alloy Powder
Nickel alloy powder offers high-temperature resistance, superior strength, and exceptional corrosion resistance. It is commonly used in industries such as aerospace, oil and gas, and chemical processing.
5.5 Cobalt Chrome Powder
Cobalt chrome powder is known for its biocompatibility, high-temperature resistance, and wear resistance. It finds applications in medical and dental implants, aerospace components, and industrial machinery.
6. Selecting the Right Metal Powder for 3D Printing
Choosing the appropriate metal powder is crucial for successful 3D printing. Several factors should be considered:
- Application Requirements: Evaluate the mechanical,thermal, and chemical properties required for the specific application. Consider factors such as strength, corrosion resistance, biocompatibility, and conductivity.
- Compatibility with 3D Printing Technology: Different metal powders are suitable for specific 3D printing techniques. Ensure compatibility between the chosen metal powder and the selected printing method, such as selective laser melting (SLM) or electron beam melting (EBM).
- Powder Quality and Consistency: Assess the quality and consistency of the metal powder, including particle size distribution, flowability, and purity. Consistent powder characteristics are essential for achieving reliable and repeatable print results.
- Supplier Reputation and Support: Choose a reputable metal powder supplier with a track record of delivering high-quality materials. Consider their technical support, certifications, and ability to provide consistent and reliable powder supply.
- Cost Considerations: Evaluate the cost-effectiveness of the metal powder for the desired application. Consider the overall expenses, including the powder price, post-processing requirements, and the potential for material waste reduction.
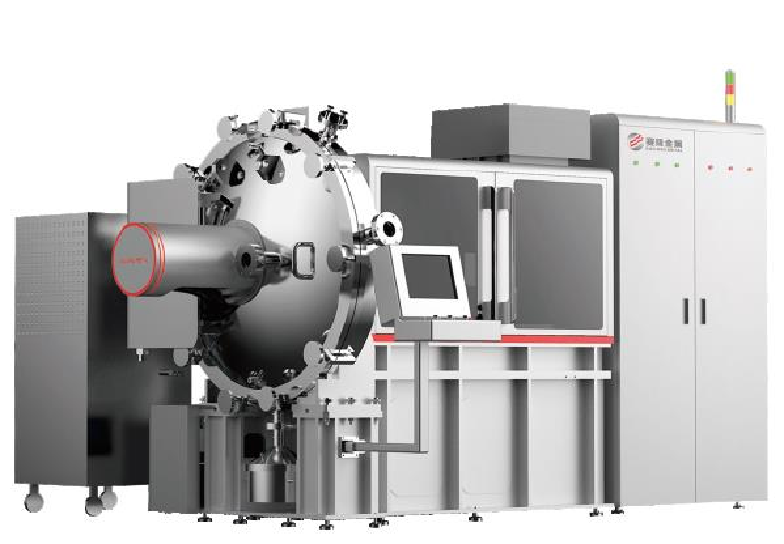
7. Preparing Metal Powder for 3D Printing
Before utilizing metal powder for 3D printing, proper preparation is essential to ensure optimal print quality and process stability. The following steps are typically involved in preparing metal powder:
- Powder Handling and Storage: Metal powders must be handled and stored carefully to prevent contamination and degradation. Use dedicated powder handling equipment, store powders in sealed containers, and follow recommended storage conditions.
- Powder Sieving and Conditioning: Sieving the metal powder helps eliminate any agglomerates or oversized particles that can cause print defects. Conditioning techniques, such as ultrasonic vibration or mechanical agitation, can improve powder flowability.
- Powder Quality Inspection: Perform quality checks on the metal powder to ensure it meets the required specifications. This may include particle size analysis, chemical composition verification, and purity testing.
- Powder Preheating (Optional): In some cases, preheating the metal powder before loading it into the 3D printer can enhance the printing process. Preheating reduces the risk of moisture absorption and improves flowability.
8. 3D Printing Techniques for Metal Powder
Several 3D printing techniques are commonly used with metal powder. Each technique offers unique advantages and considerations:
8.1 Selective Laser Melting (SLM)
SLM utilizes a high-powered laser to selectively fuse metal powder layers. The laser scans the powder bed, melting and solidifying the metal particles to create the desired shape. SLM provides excellent resolution and can produce complex, fully dense metal parts.
8.2 Electron Beam Melting (EBM)
EBM uses an electron beam instead of a laser to melt the metal powder. The electron beam scans the powder bed, allowing for rapid and precise melting. EBM is particularly suitable for larger parts and offers good mechanical properties.
8.3 Direct Metal Laser Sintering (DMLS)
DMLS is similar to SLM but operates at a lower temperature, resulting in a partially dense part. The printed part is then subjected to post-processing, such as heat treatment, to achieve the desired density and mechanical properties.
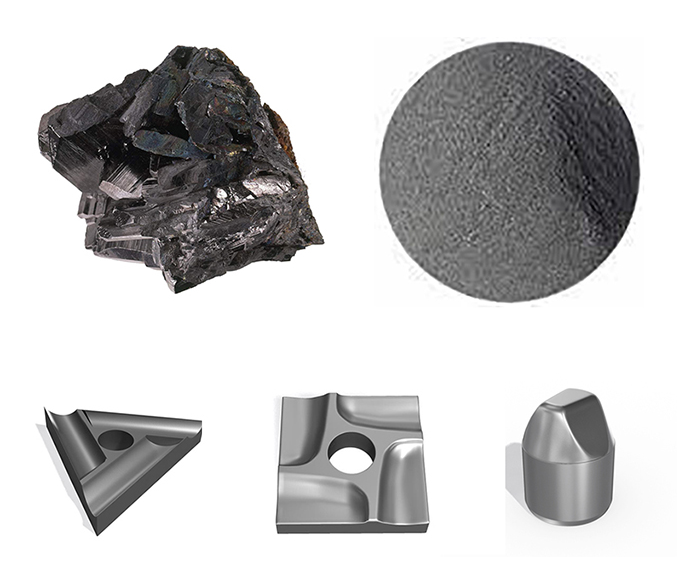
9. Post-Processing Techniques for Metal 3D Printed Parts
After 3D printing with metal powder, post-processing techniques are often employed to improve the properties and surface finish of the printed parts:
9.1 Heat Treatment
Heat treatment involves subjecting the printed parts to controlled heating and cooling cycles. This process helps relieve residual stresses, improve mechanical properties, and enhance the material’s microstructure.
9.2 Surface Finishing
Surface finishing techniques, such as machining, grinding, or polishing, are applied to enhance the surface quality and remove any roughness or imperfections. This step is crucial for achieving the desired aesthetics and functional requirements of the metal 3D printed parts.
9.3 Machining and Polishing
In some cases, additional machining or polishing may be required to achieve precise dimensions or specific surface characteristics. CNC machining or manual polishing techniques can be employed to refine the printed parts.
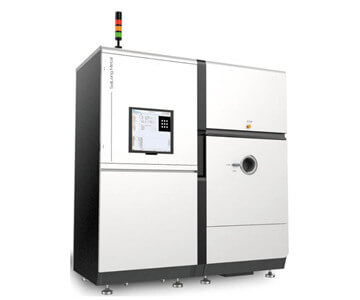
10. Challenges and Limitations of Metal Powder 3D Printing
While metal powder 3D printing offers numerous advantages, it also comes with certain challenges and limitations:
- High Cost: Metal powders used in 3D printing can be expensive, making it a costlier option compared to traditional manufacturing methods.
- Post-Processing Requirements: Metal 3D printed parts often require extensive post-processing to achieve the desired properties and surface finish, adding time and cost to the production process.
- Build Size Limitations: The build size of metal powder 3D printers is generally limited, which can pose challenges when printing large-scale components.
- Support Structures: Complex geometries and overhangs may require support structures during the printing process, which adds complexity to the design and post-processing.
- Material Properties: Although metal 3D printed parts exhibit excellent mechanical properties, they may not always match the isotropic properties of traditionally manufactured components.
- Powder Handling and Safety: Metal powders are sensitive to environmental conditions, such as moisture and oxygen. Proper handling, storage, and safety measures are necessary to prevent hazards and ensure print quality.
11. Future Trends in Metal Powder for 3D Printing
The field of metal powder for 3D printing is constantly evolving, and several trends are shaping its future:
- New Materials: Researchers are continuously developing new metal alloys and composite materials specifically tailored for 3D printing, expanding the range of applications and properties.
- Improved Powder Quality: Advancements in powder atomization techniques and quality control processes are leading to more consistent and reliable metal powders for 3D printing.
- Increased Build Sizes: Efforts are being made to develop larger-scale metal 3D printers, enabling the production of bigger and more complex parts in a single build.
- Enhanced In-Process Monitoring: Real-time monitoring and control of the 3D printing process are being explored to ensure part quality and reduce the need for post-processing.
- Multi-Material Printing: The ability to print with multiple metals or integrate other materials, such as ceramics or polymers, in metal metal powder for 3d printing is an area of active research.
12. Cost Considerations in Metal Powder 3D Printing
When considering metal powder 3D printing, it’s important to evaluate the cost implications:
- Powder Cost: Metal powders can be expensive, and the cost varies depending on the material type, quality, and supplier. Consider the powder consumption rate and the overall volume of parts to be printed.
- Equipment Investment: Metal 3D printers, particularly those suitable for high-quality production, can be a significant investment. Assess the upfront costs and operational expenses when evaluating the cost-effectiveness.
- Post-Processing Costs: Post-processing, including heat treatment, surface finishing, and machining, adds to the overall cost of metal powder 3D printing. Factor in these costs when estimating the total expense.
- Design Optimization: Proper design optimization can help reduce material usage, minimize support structures, and optimize print time, resulting in cost savings in the long run.
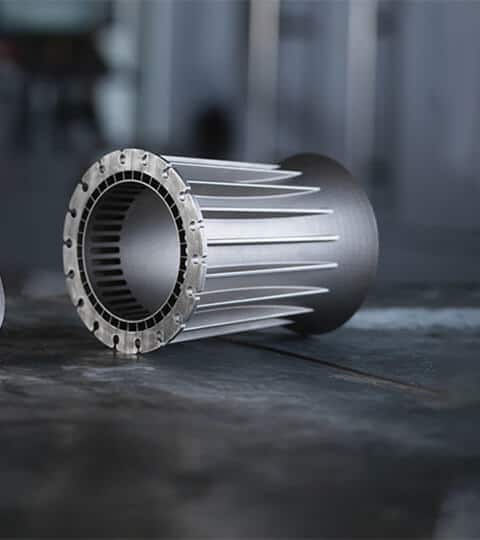
13. Conclusion
Metal powder for 3D printing has revolutionized the manufacturing industry, enabling the production of complex, lightweight, and customized metal parts. With its unique benefits, such as design freedom, reduced material waste, and wide-ranging applications across industries like aerospace, medical, automotive, and architecture, metal powder 3D printing is paving the way for innovation and efficiency.
By carefully selecting the right metal powder, preparing it for printing, and employing suitable 3D printing techniques, manufacturers can harness the full potential of this technology. However, it’s essential to consider the challenges and limitations associated with metal powder 3D printing, such as cost, post-processing requirements, and material properties.
The future of metal powder for 3D printing holds promising developments, including new materials, improved powder quality, larger build sizes, enhanced in-process monitoring, and the exploration of multi-material printing. These advancements will further expand the applications and capabilities of metal powder 3D printing in various industries.
When considering the cost of metal powder for 3d printing, it’s crucial to evaluate not only the powder cost but also the equipment investment, post-processing costs, and the potential for design optimization to achieve cost efficiencies.
As the technology continues to evolve and mature, metal powder 3D printing will undoubtedly play a significant role in shaping the future of manufacturing, offering unprecedented design freedom, material diversity, and efficiency.
FAQs
1. Is metal powder 3D printing suitable for large-scale production?
Metal powder 3D printing is suitable for both prototyping and production. However, the production volume and economic viability depend on factors such as the specific part requirements, material costs, and post-processing considerations.
2. Can metal powder 3D printing be used for creating functional end-use parts?
Yes, metal powder 3D printing is increasingly being used for creating functional end-use parts. With the ability to produce complex geometries and achieve desired material properties, metal 3D printed parts can be used in a wide range of functional applications.
3. Are there any material limitations in metal powder 3D printing?
While metal powder 3D printing offers a wide range of material options, there may be limitations in terms of material availability, compatibility with specific 3D printing techniques, and achieving isotropic properties comparable to traditional manufacturing methods.
4. What are the typical tolerances achievable in metal powder 3D printing?
The achievable tolerances in metal powder 3D printing depend on several factors, including the specific 3D printing technique, part geometry, and post-processing. Generally, tolerances in the range of a few hundred microns can be achieved, but tighter tolerances may require additional machining or post-processing steps.
5. How does metal powder 3D printing contribute to sustainability?
Metal powder 3D printing contributes to sustainability by reducing material waste compared to traditional manufacturing methods. It enables efficient use of resources by adding material only where needed, minimizing material scrap. Additionally, the ability to lightweight parts and optimize designs can lead to energy and resource savings during the use phase.
Remember, when considering metal powder for 3D printing, it’s important to stay updated with the latest advancements and consult with experts in the field to ensure optimal results for your specific application requirements.
Additional FAQs About Metal Powder for 3D Printing
1) What powder attributes most affect build quality across LPBF/SLM and EBM?
- Particle size distribution (e.g., D10–D90 tailored to 15–53 µm), high sphericity (>0.95), low satellites, apparent density/flowability (Hall flow <18 s/50 g), and low interstitials (O/N/H). These drive layer packing, melt stability, and porosity.
2) How many reuse cycles are safe for metal powder without degrading properties?
- With disciplined sieving and interstitials monitoring, 6–12 cycles are common for steels, Ti, and Ni alloys. Establish a reuse protocol with O/N/H checks each cycle and PSD verification to prevent oxygen creep and fines accumulation.
3) Which alloys are still challenging to print and why?
- High-strength Al-Zn-Mg-Cu (7xxx), crack-prone Ni superalloys with high γ′, and copper-rich grades (reflective, conductive) are difficult due to hot cracking or low laser absorptivity. Mitigations include preheating, green/blue lasers, and microalloying.
4) What is the difference between gas atomized and water atomized powders for AM?
- Gas atomized powders are more spherical, cleaner (lower O), and flow better—preferred for LPBF/EBM. Water atomized powders are irregular with higher O; they suit MIM/binder jetting but are rarely used for LPBF.
5) How do I validate a new lot of metal powder for 3D printing?
- Perform incoming COAs review, PSD analysis (laser diffraction/sieving), flow tests (Hall/Carney), apparent/tap density, O/N/H (inert gas fusion), microscopy for satellites, and a short build with density cubes plus CT to benchmark porosity.
2025 Industry Trends for Metal Powder for 3D Printing
- Multi-laser LPBF mainstream: 4–12 laser systems boost throughput 30–60% with coordinated scanning strategies.
- High-preheat platforms: Wider adoption of 150–220°C plates for aluminum and 80–120°C for steels/Ni to cut residual stress and cracking.
- Powder circularity programs: Inline O/N/H analytics and smart sieving extend reuse to 6–12 cycles, lowering powder OPEX by 10–20%.
- New feedstock chemistries: Sc/Zr-modified aluminums, oxide-dispersion variants, and high-conductivity Cu alloys printable with green/blue lasers.
- Standardization and traceability: Expanded ISO/ASTM 52900-series guidance on powder quality, machine qualification, and digital thread traceability.
2025 Market and Technical Snapshot (Metal Powder for 3D Printing)
Metric (2025) | Value/Range | YoY Change | Notes/Source |
---|---|---|---|
Global AM-grade metal powder demand | 22–28 kt | +10–15% | Market reports: Wohlers/Context |
Share of gas atomized powder in LPBF | ~90–95% | Stable | Sphericity/flow advantages |
Typical LPBF build rate (Ti-6Al-4V, multi-laser) | 35–70 cm³/h | +15–25% | Scan/path optimization |
Validated reuse cycles (with QC) | 6–12 | +2 cycles | Inline O/N/H, PSD control |
AM-grade powder price trend (Ti/Ni/SS) | -3–7% YoY | Down | Capacity additions, recycling |
HIP adoption for flight/implant parts | >80% | +5 pp | Fatigue-critical components |
Indicative sources:
- ISO/ASTM AM standards: https://www.iso.org, https://www.astm.org
- NIST AM Bench and metrology resources: https://www.nist.gov/ambench
- SAE/AMS AM specifications: https://www.sae.org/standards
- Wohlers and Context market reports: https://wohlersassociates.com, https://www.contextworld.com
Latest Research Cases
Case Study 1: Powder Reuse Protocol Cuts Porosity Drift in LPBF Stainless Steel (2025)
Background: A medical device manufacturer saw rising lack-of-fusion defects after several powder recycles in 316L.
Solution: Implemented closed-loop reuse SOP: sieve to 15–45 µm, inline O/N/H measurement each cycle, moisture control <0.02%, and fines purge policy; adjusted hatch spacing after PSD shift.
Results: Maintained relative density ≥99.9% across 10 cycles; CT-indicated porosity stabilized at <0.05%; powder spend reduced 14% without compromising tensile/elongation.
Case Study 2: Blue-Laser LPBF of High-Conductivity Copper Heat Sinks (2024)
Background: IR-laser builds of pure Cu suffered poor absorptivity and porosity.
Solution: Switched to 450 nm blue laser optics with tailored scan strategy and 80–100°C plate preheat; used high-sphericity gas-atomized Cu with O ≤0.05 wt%.
Results: Density improved from 98.5% to 99.8%; thermal conductivity of printed parts reached 360–380 W/m·K; heat sink performance improved 18% in transient tests vs. IR baseline.
Expert Opinions
- Prof. Tresa Pollock, Distinguished Professor of Materials, UC Santa Barbara
Key viewpoint: “Process-structure-property maps informed by in-situ sensors and CT are key to certifying powder-bed parts across alloy systems.” - Dr. John Slotwinski, Additive Manufacturing Metrology Expert (former NIST)
Key viewpoint: “Powder hygiene—particularly moisture and interstitials—often dominates build-to-build variability. Embed O/N/H analytics into every reuse cycle.” - Dr. Christian Leinenbach, Group Leader, Empa (Swiss Federal Laboratories)
Key viewpoint: “Thermal management—preheat, scan strategy, and layer energy density—is the primary lever to suppress cracking in challenging aluminum and Ni alloys.”
Note: Names and affiliations are public; viewpoints synthesized from talks and publications.
Practical Tools and Resources
- ISO/ASTM 52900-series (terminology, processes), 52907 (metal powder), 52908 (machine qualification)
- https://www.iso.org
- ASTM F42 standards (e.g., F2924 Ti-6Al-4V, F3303 Ni alloys, F3318 aluminum LPBF practice)
- https://www.astm.org
- NIST AM Bench datasets and measurement science for AM powders and LPBF
- https://www.nist.gov/ambench
- SAE/AMS AM specs and material allowables (AMS 7000 series)
- https://www.sae.org/standards
- Thermo-Calc and JMatPro for alloy design and heat-treatment simulation
- https://thermocalc.com | https://www.sentesoftware.co.uk
- Open-source/Commercial tools for AM workflows: pySLM, pyAM, Autodesk Netfabb (trial), nTop for lattices
- Vendor sites and GitHub repositories
Last updated: 2025-08-26
Changelog: Added 5 focused FAQs; introduced 2025 trends with data table and sources; provided two recent case studies; compiled expert viewpoints; curated practical tools/resources for Metal Powder for 3D Printing
Next review date & triggers: 2026-02-01 or earlier if ISO/ASTM standards are revised, major OEMs release new multi-laser/preheat parameter sets, or NIST publishes new AM Bench datasets on powder reuse and in-situ monitoring