Plasma Rotating Electrode Process (PREP)
Shanghai Truer Industrial Development Co., Ltd
Plasma Rotating Electrode Process Powders:
What is Plasma Rotating Electrode Process (PREP)?
Plasma Rotating Electrode Process (PREP) is considered as an excellent method to produce the sphefical powders for electric-conductive materials. and its principle and detailed processes are like:
The high-speed rotating electrode (raw material) is melted by the plasma arc under the protection of the high purity inert atmosphere, and the molten metal is thrown out by big centrifugal force to be atomised by the inert atmosphere and condensed into spherical powders when contacting to the internal wall of the cold chamber.
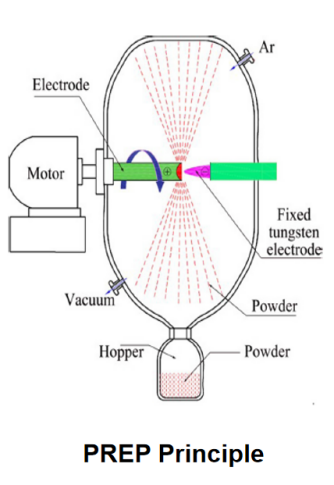
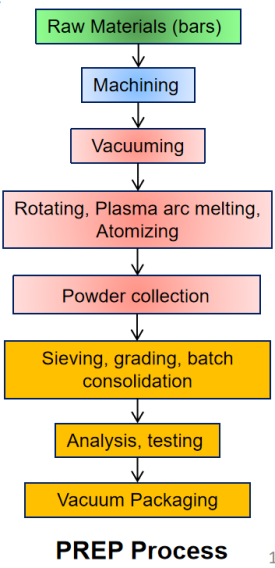
Plasma Rotating Electrode Process Powder characteristics:
1) Low increment of oxygen and other impurities (high purity)
2) Perfectly spherical and essentially satellite-free
3) Narrow particle size distribution, high flowability and high apparent/packing density
4) Low internal porosity
So the PREPed metallic powders can be applied for SEBM, SLM, DED, Binder jetting, Laser cladding,PM, etc.
Advantages of Plasma Rotating Electrode Process:
The plasma rotating electrode process (PREP system) offers several advantages for the production of metal powders and coatings. Some of the key benefits include:
High-quality, spherical metal powders: The process produces fine, spherical metal powders with uniform size distribution and high sphericity. These characteristics are desirable in various applications, such as additive manufacturing, where consistent powder properties are crucial for optimal performance.
Wide range of materials and alloys: PREA/REP can process a broad range of metals and alloys, including refractory metals, high-temperature materials, and advanced alloys. This versatility makes it suitable for many industries with different material requirements.
Controlled particle size and distribution: The process parameters, such as electrode rotation speed, plasma gas flow rate, and power input, can be adjusted to control the particle size and distribution of the produced metal powders. This flexibility allows for the production of powders with tailored properties for specific applications.
Low contamination levels: Due to the non-contact nature of the process, the risk of contamination from the surrounding environment or other sources is minimal. This results in high-purity metal powders suitable for applications with strict purity requirements, such as aerospace and medical devices.
Customizable process parameters: The plasma rotating electrode process can be adapted to meet specific application requirements by adjusting the process parameters. This adaptability allows for the production of metal powders with tailored properties, such as particle size, morphology, and chemical composition.
High production rates: Compared to other powder production methods like gas atomization, PREA/REP can achieve higher production rates due to its continuous nature and efficient conversion of the electrode material into powders.
Efficient material utilization: The process is efficient in converting the electrode material into fine powders, resulting in minimal waste and higher material utilization compared to other powder production methods.
These advantages make the plasma rotating electrode process a valuable technique for producing high-quality metal powders for various applications in industries like aerospace, automotive, medical devices, and electronics.
Plasma Rotating Electrode Process Applications:
Some of the notable applications include:
Aerospace industry: a. Manufacturing of high-performance alloys: PREA/REP can produce advanced metal powders used in the production of high-strength, lightweight, and corrosion-resistant components for aircraft, spacecraft, and engines. b. Thermal barrier coatings: The process can be used to create thermal barrier coatings for turbine blades and other engine components, enhancing their performance and durability in high-temperature environments.
Automotive industry: a. Production of lightweight components: The metal powders produced through PREA/REP can be used to create lightweight and high-strength components for vehicles, contributing to fuel efficiency and reduced emissions. b. Wear-resistant coatings: The process can be utilized to produce wear-resistant coatings for engine components and other automotive parts that experience high wear, extending their service life.
Medical devices: a. Fabrication of biocompatible materials: The high-quality metal powders produced using PREA/REP can be employed in the manufacturing of biocompatible materials and implants, such as orthopedic and dental implants. b. Drug delivery systems: The process can be used to create specialized metal powders for controlled drug release systems, enhancing the effectiveness of medical treatments.
Electronics: a. Manufacturing of conductive materials: Metal powders produced through PREA/REP can be used to create conductive materials for electronic components, such as printed circuit boards, connectors, and sensors. b. Magnetic materials: The process can be used to produce magnetic materials for various electronic applications, including data storage devices, motors, and transformers.
Energy sector: a. Fuel cell components: PREA/REP can be used to produce metal powders for the fabrication of fuel cell components, such as catalysts and electrodes, improving the performance and efficiency of fuel cells. b. Solar energy applications: The process can produce metal powders for solar energy applications, such as photovoltaic cells and thermal energy storage systems.
Additive manufacturing: a. Production of metal powders for 3D printing: The high-quality, spherical metal powders produced by PREA/REP are ideal for additive manufacturing processes like selective laser sintering (SLS) and electron beam melting (EBM), enabling the creation of complex and customized components across various industries.
These applications showcase the versatility and value of the plasma rotating electrode process in producing high-quality metal powders and coatings for a wide range of industries and purposes.
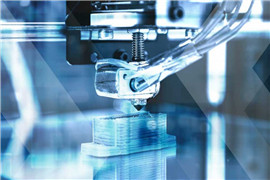
3D Printing
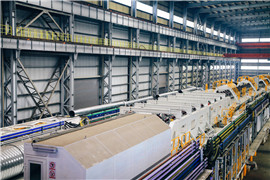
Mechanical Industry
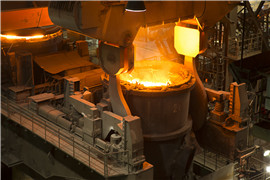
Metallurgical Industry
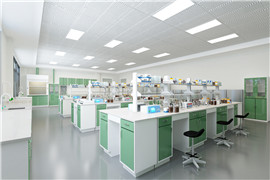
Medical Industry
Plasma Rotating Electrode Process Equipments:
The plasma rotating electrode process (PREP system) requires specific equipment to produce high-quality metal powders and coatings. Key components of the setup include:
Plasma torch: The plasma torch generates a high-velocity plasma jet that plays a vital role in melting and atomizing the metal from the rotating electrode. Common types of plasma torches used in PREA/REP are non-transferred arc torches, which maintain an electrical arc between the torch’s electrode and nozzle without making direct contact with the rotating electrode.
Power supply: A power supply is required to provide the necessary electrical energy to the plasma torch for generating and sustaining the plasma. The power supply should be capable of delivering the required voltage and current levels for the specific material being processed.
Rotating electrode: The rotating electrode is made of the metal or alloy to be processed into powders or coatings. It is mounted on a motor-driven spindle and rotated at high speeds, typically in the range of several thousand RPM. As the electrode rotates, the plasma jet impinges on its surface, melting and atomizing the material.
Motor and spindle system: The motor and spindle system is responsible for driving the rotation of the electrode. The system should be capable of delivering the required rotational speed and torque for the specific material and process parameters. It may also include a cooling mechanism to manage heat generated during the process.
Gas supply: The plasma gas supply is essential for generating and sustaining the plasma jet. Inert gases, such as argon, helium, or nitrogen, are commonly used in the process. The gas supply system should be capable of providing the required gas flow rate and pressure for the specific plasma torch and material being processed.
Collection system: A collection system is used to capture the produced metal powders or coatings. This may include a powder collection chamber or a filter system to separate the powders from the process gases. The design of the collection system may vary depending on the desired powder properties and particle size distribution.
Control system: A control system is responsible for managing and monitoring the various process parameters, such as plasma torch power, electrode rotation speed, and gas flow rate. The control system may include sensors, actuators, and a programmable logic controller (PLC) or computer-based system to regulate the process and ensure consistent production of high-quality metal powders or coatings.
These key components work together to facilitate the plasma rotating electrode process, enabling the production of high-quality metal powders and coatings for various applications across different industries.
SLPA-N
The medium-scale PREP system (SLPA-N) is purposely designed for continuous, industrial mass production of high quality spherical metal powders with the following characteristics:
- Reasonable cost for medium-batch production
- Ergonomics friendly, easy to operate
- Simple and professional man-machine interface design
- Relatively high fine powders output rate (average rotating speed: 30,000rpm)
- The produced powders have high sphericity (over 90%) and high quality, such as low porosity powders, low satellite powders, high purity (low oxygen increase,≤120ppm) due to atomizing in the inert protection atmosphere.
- Melting temperature ≥2600℃, suitable for production of Ti-alloys, Steels, Superalloys,
- Refractory alloys, high entropy alloys, etc.
SLPA-D
The small-scale PREP system (SLPA-D, desktop level) is purposely designed for R&D of novel alloy powders and small batch production of high quality powders with the following characteristics:
- Relatively lower cost for multi-small-batch production
- Quicker switch for multi-small-batch and diversified powder production (time reduction)
- Ergonomics friendly, easy to operate
- Simple and professional man-machine interface design
- High fine powders output rate due to high rotating speed (up to 50,000rpm)
- The produced powders have high sphericity (over 95%) and high quality, such as low porosity powders, low satellite powders, high purity (low oxygen increase,≤100ppm) due to atomizing in the inert protection atmosphere.
- Can produce nearly all metal powders which rods are electro-conductive, specially for refractory metals, high-activity metals, super-alloys, etc.
SLPA-H
The large-scale PREP equipment (SLPA-H) is purposely designed for continuous, industrial mass production of high quality spherical metal powders with the following characteristics:
- Reasonable cost for large-batch production
- Ergonomics friendly, easy to operate
- Simple and professional man-machine interface design
- Relatively lower fine powders output rate (rotating speed up to 20,000rpm)
- The produced powders have high sphericity (over 90%) and high quality, such as low porosity powders, low satellite powders, high purity (low oxygen increase,≤200ppm) due to atomizing in the inert protection atmosphere.
- Suitable for production of metal powders with melting point ≤2,600℃
about us
Truer Industry
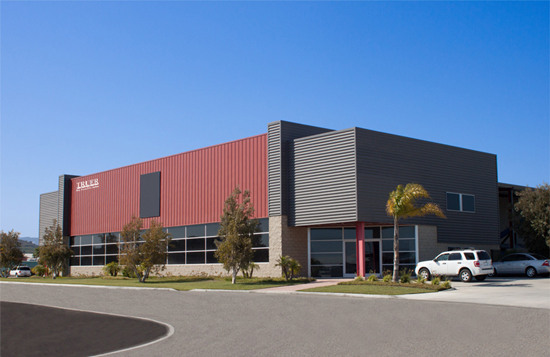
Shanghai Truer Industrial Development Co., Ltd. was established in 2009 and created the additive manufacturing business in 2019, which is dedicated to building integrating 3D printing powder making equipment and services, high quality 3D printing powders to help engineering applications of additive manufacturing.
The company not only provides professional selective electron beam melting (SEBM) technology and equipment, but also plasma rotating electrode process powder making (PREP) technology and equipment. We also have various grades of spherical metal powders, including TiNi, TiTa, TiAl, TiNbZr, CoCrMo and so on.
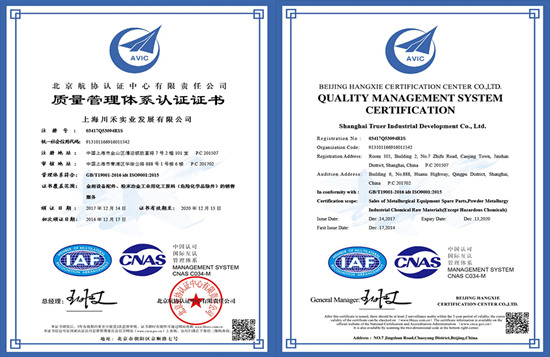
Send Us A Message
Contact us
sales
Cassiel Ding
+86 – 13611869448
[email protected]
Sales Manager
Lucy Wen
+86 – 15250232891
[email protected]
Quality Control
Mike Wu
+86 – 13862291355
[email protected]
sales
Joan Zhou
+86 – 17316565943
[email protected]
Customer Service
Luke Zhang
+86 – 15250014048
[email protected]