Metal injection molding (MIM technology)
Metal Injection Moulding technology(MIM technology) is a technology that combines powder metallurgy and injection moulding to break through the shape and strength limitations of traditional powder metallurgy, the strength limitations of die casting, the material flow limitations of press moulding, the mass production limitations of precision casting and the high cost limitations of turned parts.
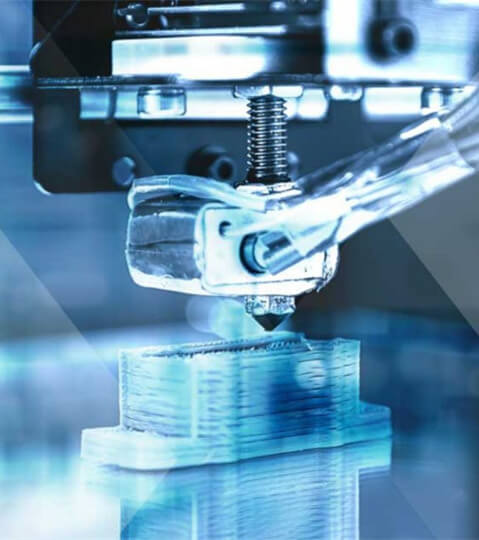
MIM technology
Metal Injection Moulding (MIM) uses fine metal powder and binder to mix with a mixing machine to obtain a malleable mixture, which is then injected into the blanks through an injection molding machine and then partially degreased or vacuum degreased and sintered into rough blanks. MIM parts have the advantages of complexity, small parts, internal homogeneity of the material, high mechanical strength, and thin walls.
MIM Technology Process principle
MIM products can be complex in shape, precise in size, high in strength, and produced automatically in large quantities, and can significantly reduce the complexity and cost of traditional metalworking. Small mechanical parts with complex shapes, high precision and high-performance materials such as 3C electronics, hand tools, remote control cars, locks, automobiles, watches and clocks, optoelectronics, weapons, biomedical and other products can be highly utilized and therefore metal injection molding is an essential choice for the development of your finished products.
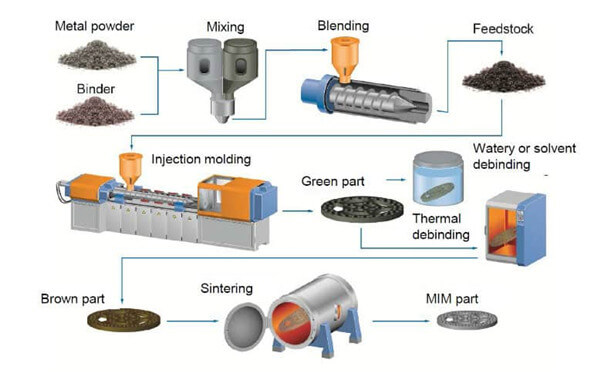
MIM Technology advantages
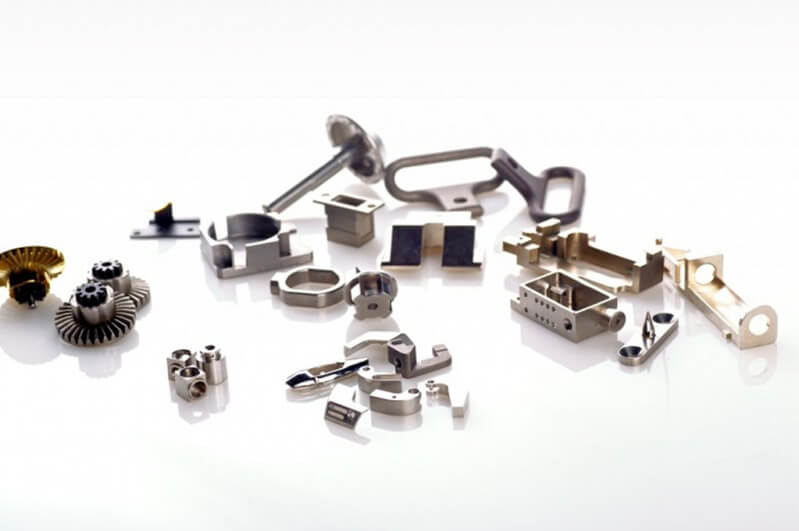
(1) Complex shaped parts can be formed in a single pass, reducing the cost of secondary processing.
(2) Excellent surface roughness for applications such as watches and decorative items where appearance is important.
(3) Better mechanical properties than conventional powder metallurgy products.
(4) High density, easy to the plating.
(5) Efficient mass production of parts with multiple cavities in one mold.
(6) Almost any metal material that can be made into a fine powder can be used in the MIM process.
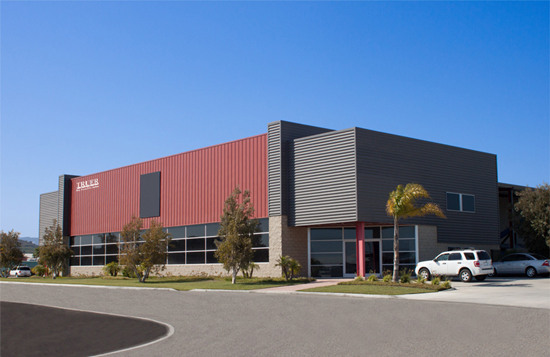
Shanghai Truer Industrial Development Co., Ltd. was established in 2009 and created the additive manufacturing business in 2019, which is dedicated to building integrating 3D printing powder making equipment and services, high quality 3D printing powders to help engineering applications of additive manufacturing.
- Professional Specialist
- Fair prices
- Top sales and quality
- Support customization
What We Offer?
The company not only provides professional selective electron beam melting (SEBM) technology and equipment, but also plasma rotating electrode process powder making (PREP) technology and equipment. We also have various grades of spherical metal powders, including TiNi, TiTa, TiAl, TiNbZr, CoCrMo, and so on.
Relying on the innovation platform of top labs, the company has established a joint innovation center for metal 3D printing and is working with high-level research institutions and well-known experts to carry out 3D printing innovation.
Shanghai Truer’s professional team continues to provide customers with personalized additive manufacturing solutions to promote industry technology development and expand the application areas of 3D printing. From testing to finished products, from professional customization to scale manufacturing, we continue to create value for the industry through technological innovation.
MIM Technology Applications
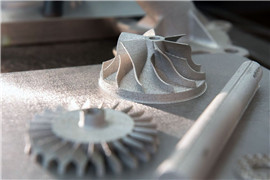
3D Printing
HIP technology is now widely used in cemented carbide sintering, densification of refractory metals and alloys such as tungsten, aluminium and titanium, defect repair of products (e.g. 3D printed metal parts)
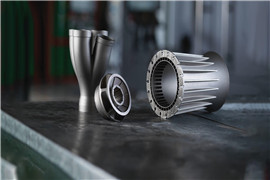
precision instruments
MIM products can be complex in shape, precise in size, high in strength and produced automatically in large quantities, and can significantly reduce the complexity and cost of traditional metalworking
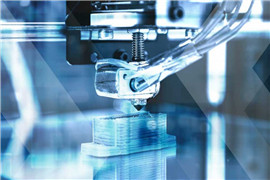
Complex moulds
SLM, also known as Selective Laser Melting, is similar in principle to SLS in that a laser is used to melt and solidify metal powder in a specified area, which is then moulded in a layer-by-layer stack.
We Provide the Best Service in AM Industry
We offer free expert consultation opportunities