Electron Beam Melting (EBM) technology introduction
Electron Beam Melting refers to a vacuum melting method in which the kinetic energy of a high speed electron beam stream is converted to heat as a heat source for melting metals under high vacuum. The abbreviation is EBM.
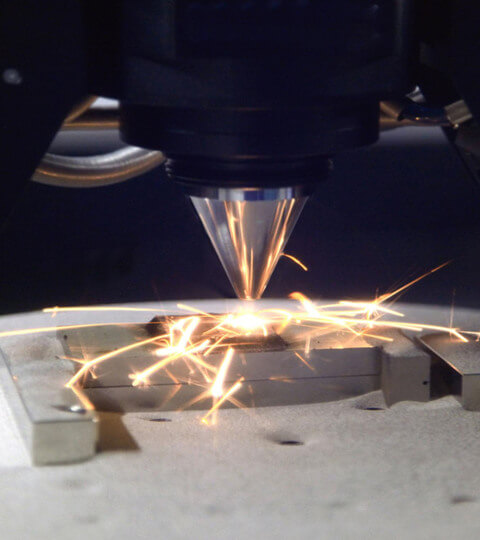
What is Electron Beam Melting?
This melting method has the characteristics of high melting temperature, adjustable furnace power and heating speed and good product quality, but there are also problems such as low metal yield, high specific power consumption and the need for melting under high vacuum.
Electron beam melting is not only used for the melting and refining of steel and rare metals, but is also widely used for welding and ceramic material melting and casting.
Electron Beam Melting Technology Process principle
Under high vacuum conditions, the cathode is heated by the high voltage electric field and emits electrons, which are collected into a beam. The electron beam moves towards the anode at a very high speed under the action of the accelerating voltage.
After passing through the anode, accurately bombards the bottom ingot and the material in the crystallizer under the action of the focusing and deflecting coils, causing the bottom ingot to be melted to form a molten pool and the material to be continuously melted and dripped into the pool, thus realizing the melting process.
The acceleration voltage of the electron beam furnace is generally used at around 30,000 volts, causing a maximum X-ray loss of no more than 0.5%, and the loss of secondary emission electrons will be even less. Therefore the energy of the electron beam is almost entirely converted from electrical energy to kinetic energy and then from kinetic energy to thermal energy.
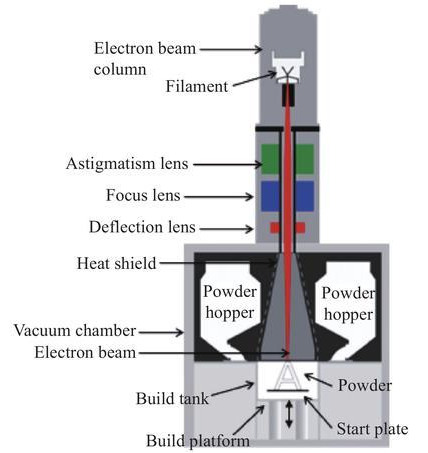
Electron Beam Melting Technology Process characteristics:
The electron beam melting process is characterized by a high vacuum environment for melting (the melting vacuum is generally between 10 and 10 Pa), the temperature of the melt pool and its distribution can be controlled during melting and the maintenance time of the melt pool can be adjusted within a wide range; the melting is carried out in a water-cooled copper crucible (crystallizer), which effectively prevents the metal liquid from being contaminated by refractory materials.
It can therefore be said that electron beam melting provides an indispensable means of refining some metallic materials, especially refractory metals.
There are three basic metallurgical reactions in the electron beam melting process:
(1) de-gassing. Electron beam melting removes hydrogen from most metals, and the removal of hydrogen is easy, generally before the furnace charge is melted clear: due to the high vacuum, the temperature of the melt pool and the time in the liquid state can be controlled, and the denitration effect is also high.
(2) Volatilization of metal impurities. At the electron beam melting temperature, all-metal impurities with a higher vapor pressure than the base metal are removed by volatilization to varying degrees.
(3) Removal of non-metallic inclusions. Oxide and nitride inclusions in the electron beam melting temperature and vacuum, it is possible to decompose [O] and [N] to be removed; [O] can also be removed through the carbon-oxygen reaction; in addition, the bottom-up sequential solidification characteristics of the ingot is also conducive to the floating of non-metallic inclusions.
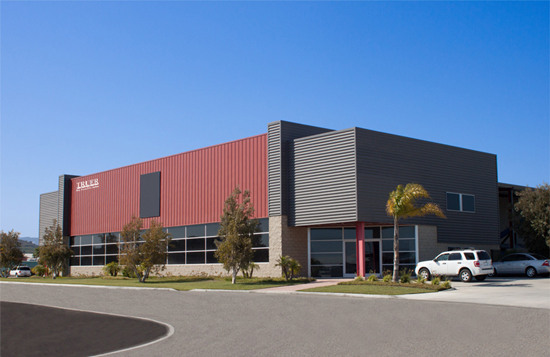
Shanghai Truer Industrial Development Co., Ltd. was established in 2009 and created the additive manufacturing business in 2019, which is dedicated to building integrating 3D printing powder making equipment and services, high quality 3D printing powders to help engineering applications of additive manufacturing.
- Professional Specialist
- Fair prices
- Top sales and quality
- Support customization
What We Offer
The company not only provides professional selective electron beam melting (SEBM) technology and equipment, but also plasma rotating electrode process powder making (PREP) technology and equipment. We also have various grades of spherical metal powders, including TiNi, TiTa, TiAl, TiNbZr, CoCrMo and so on.
Relying on the innovation platform of top labs, the company has established a joint innovation center for metal 3D printing, and is working with high-level research institutions and well-known experts to carry out 3D printing innovation.
Shanghai Truer’s professional team continues to provide customers with personalized additive manufacturing solutions to promote industry technology development and expand the application areas of 3D printing. From testing to finished products, from professional customization to scale manufacturing, we continue to create value to industry through technological innovation.
Applications
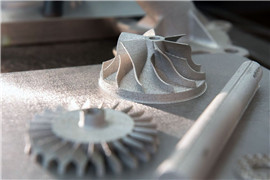
3D Printing
HIP technology is now widely used in cemented carbide sintering, densification of refractory metals and alloys such as tungsten, aluminium and titanium, defect repair of products (e.g. 3D printed metal parts)
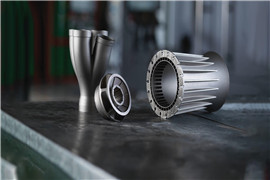
precision instruments
MIM products can be complex in shape, precise in size, high in strength and produced automatically in large quantities, and can significantly reduce the complexity and cost of traditional metalworking
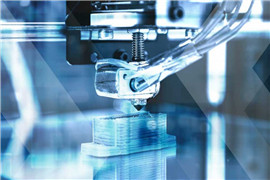
Complex moulds
SLM, also known as Selective Laser Melting, is similar in principle to SLS in that a laser is used to melt and solidify metal powder in a specified area, which is then moulded in a layer-by-layer stack.
We Provide the Best Service in AM Industry
We offer free expert consultation opportunities