Overview of Titanium Powder for 3D Printing
3D printing has revolutionized manufacturing, enabling the creation of complex structures and custom designs with precision. Titanium powder, a key material in this field, offers unmatched strength, lightweight properties, and biocompatibility. This article dives deep into the world of titanium powder for 3D printing, exploring its types, applications, properties, and much more. Ready to learn everything you need to know? Let’s dive in!
Types of Titanium Powder for 3D Printing
Titanium powders come in various models, each with unique characteristics tailored for specific applications. Here are some prominent ones:
Model | Composition | Properties | Characteristics |
---|---|---|---|
Ti-6Al-4V (Grade 5) | 6% Aluminum, 4% Vanadium, 90% Titanium | High strength, excellent corrosion resistance | Most commonly used alloy, versatile |
Ti-6Al-2Sn-4Zr-2Mo (Grade 6) | 6% Aluminum, 2% Tin, 4% Zirconium, 2% Molybdenum | Good weldability, high creep resistance | Ideal for high-temperature applications |
Ti-6Al-6V-2Sn (Grade 12) | 6% Aluminum, 6% Vanadium, 2% Tin | Enhanced strength, good formability | Suitable for heavy-duty applications |
Ti-3Al-2.5V (Grade 9) | 3% Aluminum, 2.5% Vanadium | Excellent ductility, moderate strength | Common in aerospace and sports equipment |
Ti-6Al-7Nb | 6% Aluminum, 7% Niobium | Biocompatible, corrosion-resistant | Preferred for medical implants |
Ti-5Al-2.5Sn | 5% Aluminum, 2.5% Tin | Good fatigue resistance, weldability | Used in aerospace and marine industries |
Ti-8Al-1Mo-1V | 8% Aluminum, 1% Molybdenum, 1% Vanadium | High strength, lightweight | Ideal for structural applications |
Ti-0.2Pd (Grade 7) | 0.2% Palladium | Enhanced corrosion resistance | Suitable for chemical processing environments |
Ti-15Mo-3Nb-3Al-0.2Si | 15% Molybdenum, 3% Niobium, 3% Aluminum, 0.2% Silicon | High strength, excellent corrosion resistance | Used in biomedical and marine applications |
Ti-10V-2Fe-3Al | 10% Vanadium, 2% Iron, 3% Aluminum | High strength, good toughness | Common in aerospace structures |
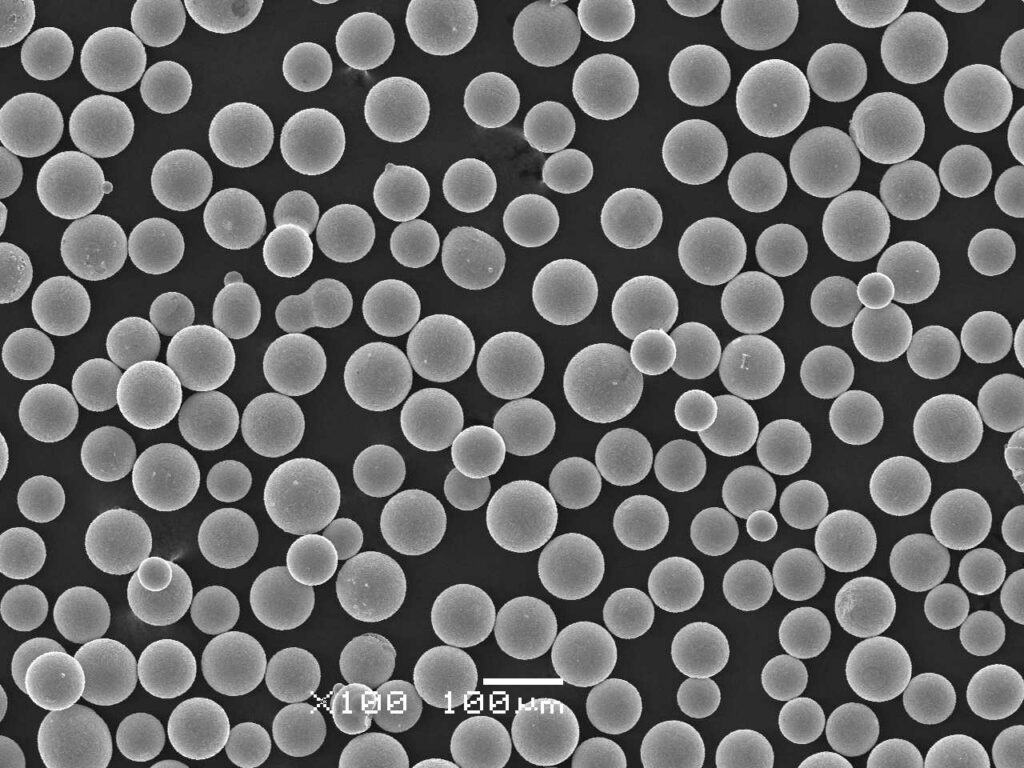
Applications of Titanium Powder for 3D Printing
Titanium powder is a game-changer in various industries due to its exceptional properties. Here are some of its key applications:
Industry | Applications |
---|---|
Aerospace | Engine components, airframes, brackets |
Medical | Orthopedic implants, dental implants, surgical instruments |
Automotive | Engine parts, lightweight structural components |
Marine | Propellers, hull components, underwater equipment |
Defense | Armor plating, missile components, military vehicles |
Industrial | Chemical processing equipment, heat exchangers |
Consumer Goods | Sports equipment, eyewear frames, jewelry |
Properties and Characteristics of Titanium Powder
Titanium powder boasts several properties that make it ideal for 3D printing. Let’s break down its core characteristics:
Mechanical Properties
Property | Value |
---|---|
Density | 4.5 g/cm³ |
Melting Point | 1,668°C |
Young’s Modulus | 110 GPa |
Tensile Strength | 1,000 MPa |
Yield Strength | 930 MPa |
Hardness | 36 HRC |
Physical and Chemical Properties
Property | Value |
---|---|
Corrosion Resistance | Excellent |
Thermal Conductivity | 15 W/m·K |
Electrical Resistivity | 420 nΩ·m |
Biocompatibility | High |
Characteristics
- Lightweight: Titanium is significantly lighter compared to other metals like steel.
- High Strength: Offers exceptional strength-to-weight ratio.
- Corrosion Resistant: Excellent resistance to rust and corrosion, making it ideal for harsh environments.
- Biocompatible: Perfect for medical implants due to its non-reactive nature with body tissues.
Specifications, Sizes, Grades, Standards
Titanium powder is available in various specifications, ensuring it meets the diverse needs of different industries.
Specifications
Specification | Details |
---|---|
Particle Size | 15-45 µm, 45-90 µm |
Purity | ≥ 99.5% |
Density | 4.51 g/cm³ |
Flowability | High |
Sphericity | ≥ 98% |
Sizes and Grades
Grade | Size Range |
---|---|
Grade 1 | 5-20 µm |
Grade 2 | 20-45 µm |
Grade 3 | 45-90 µm |
Grade 4 | 90-150 µm |
Standards
Standard | Details |
---|---|
ASTM B348 | Titanium and Titanium Alloy Bars and Billets |
ASTM F67 | Unalloyed Titanium for Surgical Implant Applications |
ASTM F136 | Titanium Alloy for Surgical Implants |
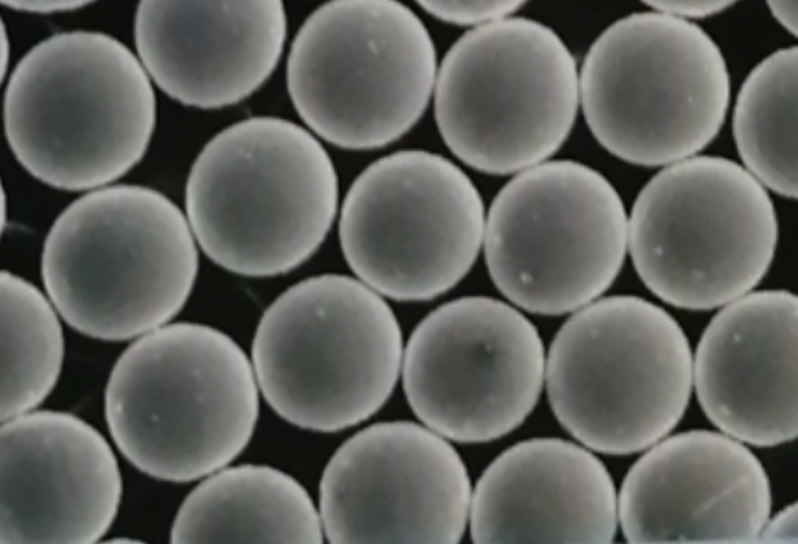
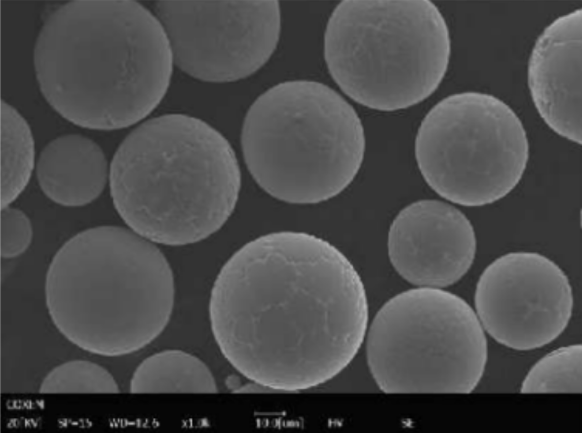
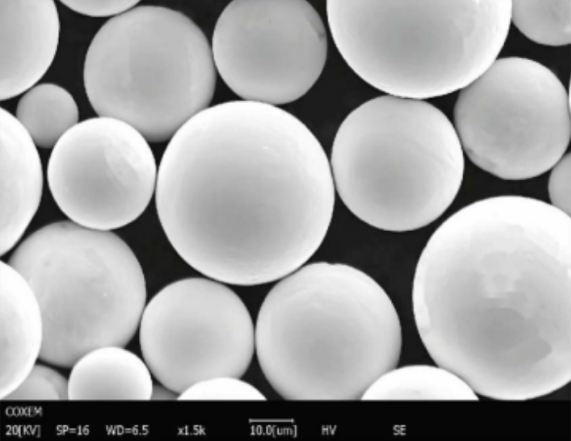
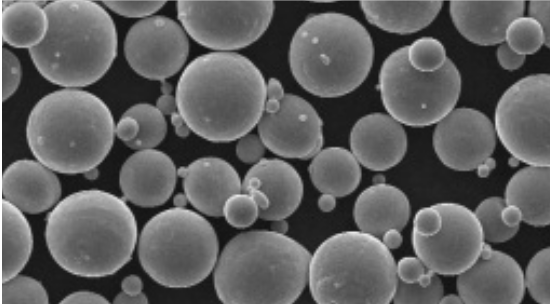
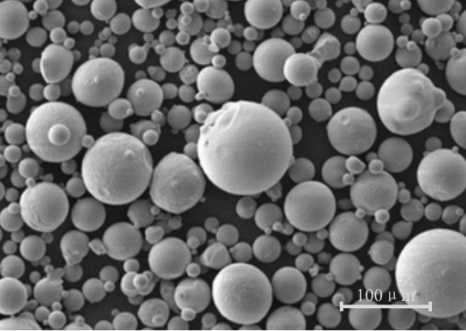
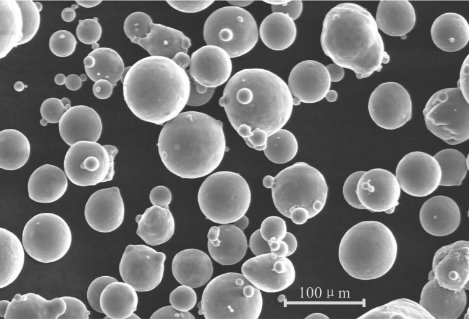
Suppliers and Pricing Details
Finding reliable suppliers for titanium powder is crucial for maintaining quality in 3D printing projects. Here are some top suppliers and their pricing details:
Top Suppliers
Supplier | Location | Contact |
---|---|---|
AP&C (Advanced Powders & Coatings) | Canada | apc-powder.com |
Tekna | Canada | tekna.com |
Carpenter Additive | USA | carpenteradditive.com |
Praxair Surface Technologies | USA | praxairsurfacetechnologies.com |
Sandvik | Sweden | home.sandvik |
Pricing Details
Supplier | Model | Price (USD/kg) |
---|---|---|
AP&C | Ti-6Al-4V | $300 |
Tekna | Ti-6Al-7Nb | $350 |
Carpenter Additive | Ti-3Al-2.5V | $325 |
Praxair Surface Technologies | Ti-6Al-2Sn-4Zr-2Mo | $400 |
Sandvik | Ti-10V-2Fe-3Al | $375 |
Comparing Pros and Cons of Titanium Powder for 3D Printing
Like any material, titanium powder has its advantages and limitations. Here’s a detailed comparison:
Advantages
Aspect | Description |
---|---|
Strength-to-Weight Ratio | Superior strength while being lightweight |
Corrosion Resistance | Excellent resistance to rust and corrosion |
Biocompatibility | Ideal for medical implants and devices |
Durability | Long-lasting and resilient material |
Versatility | Suitable for a wide range of industries |
Disadvantages
Aspect | Description |
---|---|
Cost | Expensive compared to other metals |
Processing Difficulty | Requires specialized equipment and expertise |
Powder Handling | Needs careful handling to prevent oxidation |
Recycling | Recycling titanium powder can be challenging |
Application-Specific Insights
Aerospace: Titanium Powder in Engine Components
In the aerospace industry, titanium powder is extensively used for manufacturing engine components due to its high strength and low weight. For instance, jet engine blades made from Ti-6Al-4V exhibit excellent performance under extreme conditions. Compared to traditional materials like steel, titanium provides better fuel efficiency and longer service life.
Medical: Biocompatibility of Titanium Implants
The medical sector leverages titanium powder’s biocompatibility for creating implants such as hip joints, dental implants, and bone plates. Ti-6Al-7Nb, known for its non-reactivity with body tissues, ensures patient safety and longevity of the implants. Compared to stainless steel, titanium implants reduce the risk of allergic reactions and corrosion within the body.
Automotive: Lightweight and Strong Parts
Automotive manufacturers use titanium powder to produce lightweight yet strong components like engine parts and structural elements. This not only enhances vehicle performance but also improves fuel efficiency. For example,
Ti-3Al-2.5V is preferred for its excellent ductility and strength, making it ideal for both high-performance sports cars and everyday vehicles.
Comparison of Titanium Powder Grades
Grade 5 vs. Grade 9
Ti-6Al-4V (Grade 5) is the most commonly used titanium alloy in 3D printing due to its balanced properties of strength, corrosion resistance, and weldability. It is versatile and suitable for various applications, from aerospace to medical devices.
Ti-3Al-2.5V (Grade 9), on the other hand, offers slightly lower strength but better ductility and formability. It is commonly used in applications where flexibility and ease of fabrication are more critical, such as in aerospace tubing and sports equipment.
Grade 7 vs. Grade 23
Ti-0.2Pd (Grade 7) is known for its superior corrosion resistance, making it ideal for chemical processing and marine applications. The addition of palladium enhances its ability to withstand harsh environments.
Ti-6Al-4V ELI (Grade 23) is an extra-low interstitial variant of Grade 5, offering improved fracture toughness and biocompatibility. This makes it a top choice for critical medical implants and components that require high reliability.
Technical Considerations for 3D Printing with Titanium Powder
When working with titanium powder for 3D printing, several technical considerations must be addressed to ensure successful outcomes:
Powder Quality
High-quality titanium powder is essential for achieving optimal print results. Factors such as particle size distribution, sphericity, and purity directly impact the mechanical properties and surface finish of the printed parts.
Printing Environment
Titanium powder is highly reactive, especially when exposed to oxygen and moisture. Therefore, 3D printing should be conducted in a controlled environment, typically using inert gases like argon or nitrogen to prevent oxidation and contamination.
Post-Processing
Post-processing steps, such as heat treatment, machining, and surface finishing, are crucial for enhancing the mechanical properties and appearance of the printed parts. These processes help relieve internal stresses, improve dimensional accuracy, and achieve the desired surface quality.
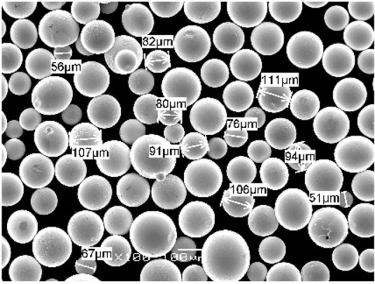
FAQs
Q: What is the primary advantage of using titanium powder for 3D printing?
A: The primary advantage of using titanium powder for 3D printing is its excellent strength-to-weight ratio. This makes it ideal for applications where both durability and lightweight properties are essential, such as in aerospace and medical industries.
Q: How does the cost of titanium powder compare to other metal powders?
A: Titanium powder is generally more expensive than other metal powders like aluminum or steel. However, its superior properties, such as corrosion resistance and biocompatibility, often justify the higher cost, especially in critical applications.
Q: Can titanium powder be recycled for 3D printing?
A: Yes, titanium powder can be recycled, but the process can be challenging. It requires careful handling to avoid contamination and ensure the recycled powder maintains its quality and properties.
Q: What are the safety precautions when handling titanium powder?
A: When handling titanium powder, it is essential to wear appropriate personal protective equipment (PPE), including gloves, safety goggles, and respirators. Additionally, work in a well-ventilated area and use proper storage containers to prevent oxidation and moisture absorption.
Q: What post-processing techniques are used for titanium 3D-printed parts?
A: Common post-processing techniques for titanium 3D-printed parts include heat treatment, machining, polishing, and surface coating. These techniques enhance the mechanical properties, dimensional accuracy, and surface finish of the parts.
Q: Which industries benefit the most from titanium powder for 3D printing?
A: Industries such as aerospace, medical, automotive, and defense benefit the most from titanium powder for 3D printing due to its exceptional properties, including high strength, lightweight, corrosion resistance, and biocompatibility.
Conclusion
Titanium powder for 3D printing is a transformative material, offering unparalleled strength, lightweight properties, and versatility across various industries. From aerospace components to medical implants, titanium’s unique properties make it a preferred choice for high-performance applications. By understanding the different types, applications, and technical considerations, you can make informed decisions and leverage the full potential of titanium powder in your 3D printing projects.
Whether you’re an engineer, designer, or manufacturer, the insights provided in this comprehensive guide will help you navigate the complexities of using titanium powder for 3D printing. Embrace the future of manufacturing with titanium powder, and unlock new possibilities in design and production.