Plasma atomization is an advanced technique utilized in the manufacturing of metal powders, renowned for its precision and efficiency. This article delves deep into the intricacies of plasma atomization, exploring its various facets, applications, and the specific models of metal powders produced through this method. By the end of this comprehensive guide, you’ll have a thorough understanding of plasma atomization and its significant impact on modern manufacturing.
Overview of Plasma Atomization
Plasma atomization is a process used to produce high-quality metal powders by converting a metal wire into fine particles through the application of a high-temperature plasma torch. This method is preferred for its ability to produce spherical powders with narrow particle size distributions, essential for applications in additive manufacturing, aerospace, and medical devices.
Key Details
- Process: Conversion of metal wire into powder using plasma torch
- Applications: Additive manufacturing, aerospace, medical devices
- Benefits: High-quality, spherical powders with narrow size distribution
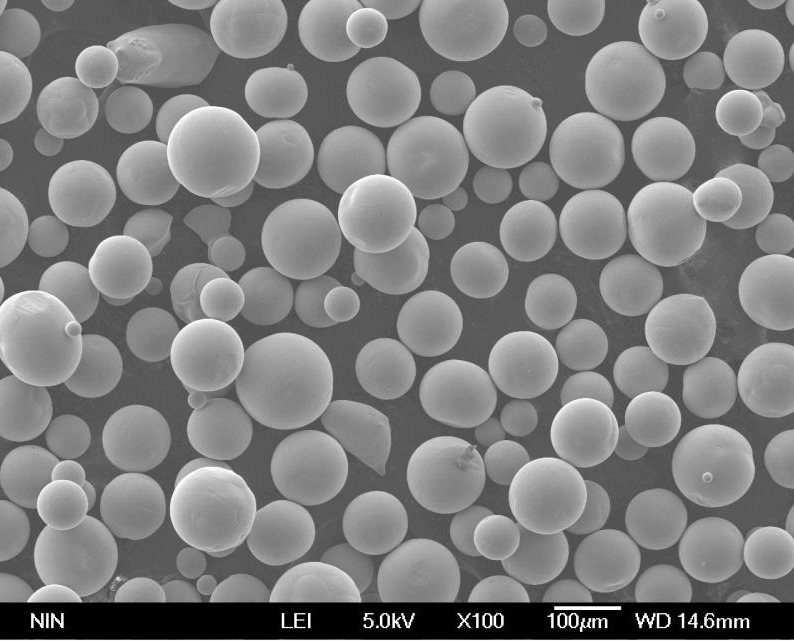
Types of Metal Powders Produced by Plasma Atomization
Table: Types and Characteristics of Metal Powders
Metal Powder Model | Composition | Properties | Characteristics |
---|---|---|---|
Ti-6Al-4V | Titanium alloy with Al and V | High strength, corrosion resistance | Ideal for aerospace and medical applications |
316L Stainless Steel | Iron, Chromium, Nickel, Molybdenum | High corrosion resistance, good mechanical properties | Used in medical and marine environments |
Inconel 718 | Nickel-Chromium alloy | Excellent high-temperature strength | Suitable for aerospace turbines |
AlSi10Mg | Aluminum with Silicon, Magnesium | Lightweight, good thermal properties | Common in automotive and aerospace sectors |
CoCrMo | Cobalt-Chromium-Molybdenum alloy | High wear resistance, biocompatibility | Used in medical implants |
Hastelloy X | Nickel-based alloy | High oxidation resistance, high strength | Ideal for high-temperature environments |
CuNi2SiCr | Copper-Nickel-Silicon-Chromium | High strength, electrical conductivity | Used in electrical and marine applications |
Ti-48Al-2Cr-2Nb | Titanium-Aluminum alloy | High temperature and oxidation resistance | Suitable for turbine blades and automotive |
316F Stainless Steel | Iron, Chromium, Nickel, Sulfur | Free-machining, high corrosion resistance | Preferred in medical tools and components |
NiCrMo-4 | Nickel-Chromium-Molybdenum alloy | High corrosion resistance, good weldability | Used in chemical processing equipment |
Applications of Plasma Atomization Metal Powders
Table: Applications and Uses
Application Area | Specific Uses |
---|---|
Additive Manufacturing | 3D printing of complex components, prototypes, custom parts |
Aerospace | Turbine blades, structural components, engine parts |
Medical Devices | Implants, surgical tools, prosthetics |
Automotive | Lightweight components, engine parts, heat exchangers |
Marine | Corrosion-resistant components, propellers, valves |
Electrical | Conductive materials, connectors, thermal management |
Chemical Processing | High-temperature reactors, corrosion-resistant equipment |
Specifications and Standards of Plasma Atomization Metal Powders
Table: Specifications, Sizes, Grades, and Standards
Metal Powder Model | Specifications | Sizes Available | Grades | Standards |
---|---|---|---|---|
Ti-6Al-4V | ASTM B348, AMS 4928 | 15-45 µm, 45-106 µm | Grade 5 | ASTM, AMS |
316L Stainless Steel | ASTM A276, ASTM A240 | 20-53 µm, 53-150 µm | Grade 316L | ASTM, AMS, ISO |
Inconel 718 | AMS 5662, AMS 5596 | 15-45 µm, 45-106 µm | Grade 718 | AMS, ASTM, ISO |
AlSi10Mg | ISO 3522, DIN EN 1706 | 20-63 µm, 63-150 µm | Grade A360 | ISO, DIN |
CoCrMo | ASTM F75, ASTM F1537 | 15-45 µm, 45-106 µm | Grade 1 | ASTM, ISO |
Hastelloy X | AMS 5536, AMS 5754 | 15-45 µm, 45-106 µm | Grade X | AMS, ASTM, ISO |
CuNi2SiCr | ASTM B151, ASTM B122 | 20-53 µm, 53-150 µm | Grade 1 | ASTM, ISO |
Ti-48Al-2Cr-2Nb | ASTM B988, AMS 4911 | 15-45 µm, 45-106 µm | Grade 1 | ASTM, AMS |
316F Stainless Steel | ASTM A276, ASTM A240 | 20-53 µm, 53-150 µm | Grade 316F | ASTM, AMS, ISO |
NiCrMo-4 | ASTM B575, ASTM B619 | 15-45 µm, 45-106 µm | Grade 4 | ASTM, ISO |
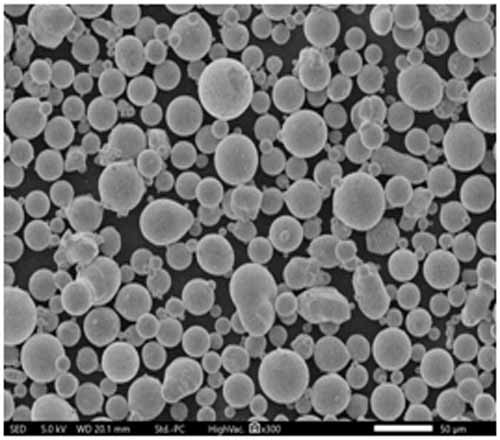
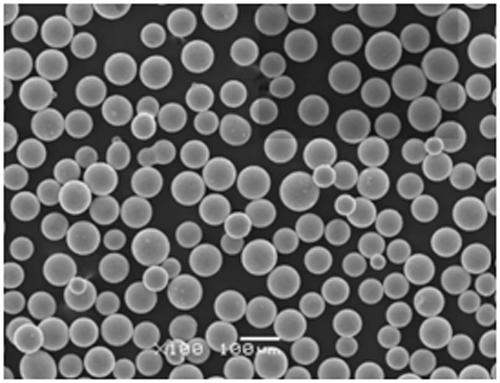
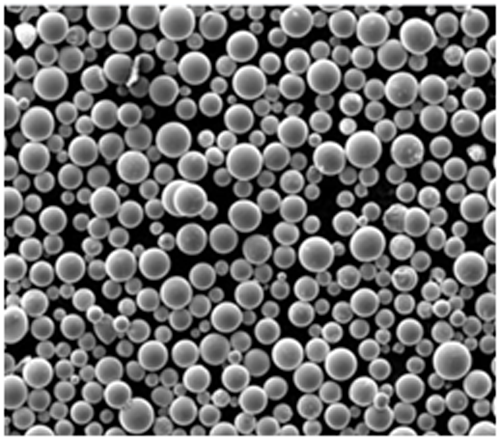
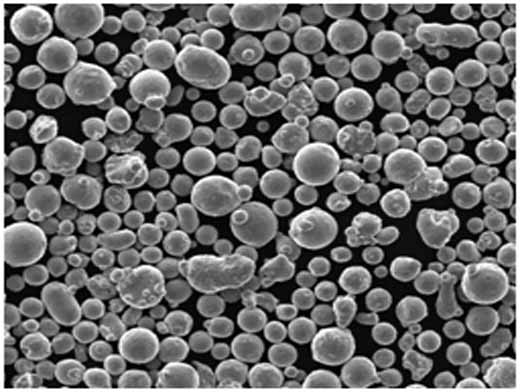
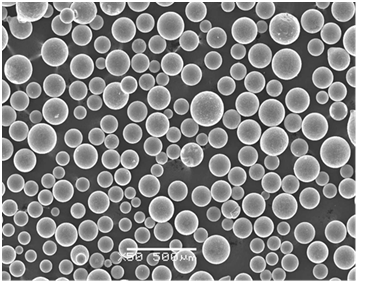
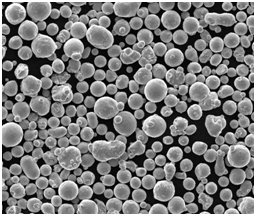
Suppliers and Pricing Details
Table: Suppliers and Pricing
Supplier | Metal Powder Models | Pricing (per kg) | Additional Services |
---|---|---|---|
GKN Additive | Ti-6Al-4V, 316L Stainless Steel, Inconel 718 | $300 – $500 | Custom powder production |
Höganäs AB | AlSi10Mg, CoCrMo, Hastelloy X | $250 – $450 | Technical support, R&D services |
LPW Technology | CuNi2SiCr, Ti-48Al-2Cr-2Nb, 316F Stainless Steel | $350 – $600 | Powder characterization, testing |
Carpenter Additive | NiCrMo-4, Ti-6Al-4V, Inconel 718 | $280 – $550 | Application engineering support |
AP&C (GE Additive) | Ti-6Al-4V, AlSi10Mg, CoCrMo | $320 – $480 | Large-scale production, quality control |
Sandvik Osprey | 316L Stainless Steel, Hastelloy X | $260 – $470 | Metal powder recycling services |
Praxair Surface Technologies | AlSi10Mg, CuNi2SiCr, NiCrMo-4 | $270 – $500 | Advanced coatings, surface treatments |
Aubert & Duval | Ti-48Al-2Cr-2Nb, 316F Stainless Steel | $290 – $520 | Customized alloys, special grades |
Arcam AB (GE Additive) | Ti-6Al-4V, Inconel 718 | $310 – $530 | Additive manufacturing solutions |
Vacuumschmelze GmbH | CoCrMo, Hastelloy X, NiCrMo-4 | $300 – $490 | High-purity metal powders |
Advantages and Limitations of Plasma Atomization
Table: Comparing Pros and Cons
Aspect | Advantages | Limitations |
---|---|---|
Powder Quality | High sphericity, uniform particle size | Initial setup cost is high |
Material Range | Can process a wide range of metals and alloys | Some materials may require specific plasma settings |
Production Efficiency | High yield, minimal waste | Energy-intensive process |
Application Versatility | Suitable for various high-tech applications | Requires skilled operation and maintenance |
Scalability | Scalable for industrial production | Equipment and maintenance costs |
Environmental Impact | Less waste compared to other methods | Still reliant on non-renewable energy sources |
Characteristics of Plasma Atomization Metal Powders
Table: Composition and Characteristics
Metal Powder Model | Composition | Characteristics |
---|---|---|
Ti-6Al-4V | 90% Ti, 6% Al, 4% V | High strength-to-weight ratio, corrosion-resistant |
316L Stainless Steel | 64% Fe, 18% Cr, 14% Ni, 2% Mo | Excellent corrosion resistance,biocompatible |
Inconel 718 | 50-55% Ni, 17-21% Cr, 4.75-5.5% Nb, 2.8-3.3% Mo | High-temperature performance, oxidation-resistant |
AlSi10Mg | 89% Al, 10% Si, 1% Mg | Lightweight, good thermal conductivity |
CoCrMo | 60-65% Co, 26-30% Cr, 5-7% Mo | High wear resistance, biocompatible |
Hastelloy X | 47% Ni, 22% Cr, 18% Fe, 9% Mo | Excellent high-temperature strength |
CuNi2SiCr | 97% Cu, 2% Ni, 0.6% Si, 0.4% Cr | High electrical conductivity, corrosion-resistant |
Ti-48Al-2Cr-2Nb | 48% Ti, 48% Al, 2% Cr, 2% Nb | High temperature and oxidation resistance |
316F Stainless Steel | 64% Fe, 18% Cr, 14% Ni, 2% Mo, 0.15% S | Free-machining, high corrosion resistance |
NiCrMo-4 | 56-60% Ni, 20-22% Cr, 8-10% Mo | Corrosion-resistant, good weldability |
Comparing Plasma Atomization to Other Methods
Plasma atomization stands out among other powder production methods such as gas atomization and mechanical milling due to its ability to produce high-quality, uniform powders. But how does it truly compare?
Table: Plasma Atomization vs. Other Methods
Method | Plasma Atomization | Gas Atomization | Mechanical Milling |
---|---|---|---|
Powder Quality | High sphericity, narrow size distribution | Good sphericity, broader size range | Irregular shapes, wide size distribution |
Material Versatility | Wide range of metals and alloys | Wide range but some limitations | Limited to certain materials |
Efficiency | High yield, minimal waste | Moderate yield, some waste | Lower yield, significant waste |
Scalability | Scalable for industrial production | Scalable but less efficient at large scale | Limited scalability |
Cost | High initial setup, lower operational costs | Moderate setup and operational costs | Lower setup cost, higher operational costs |
Energy Consumption | Energy-intensive | Less energy-intensive than plasma | Moderate energy consumption |
Applications | High-tech applications | Broad range including high-tech | Less suited for high-tech applications |
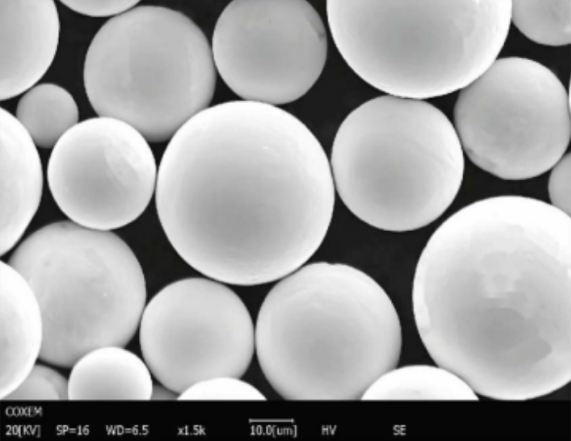
FAQ
Table: FAQs on Plasma Atomization
Question | Answer |
---|---|
What is plasma atomization? | It’s a process where metal wire is converted into fine powders using a high-temperature plasma torch. |
What are the benefits of plasma atomization? | Produces high-quality, spherical powders with narrow size distributions, ideal for advanced manufacturing applications. |
Which industries use plasma-atomized powders? | Aerospace, medical devices, automotive, marine, electrical, and chemical processing industries. |
How does plasma atomization compare to other methods? | It offers higher quality powders with better sphericity and uniformity but comes with higher initial setup costs. |
What materials can be processed using plasma atomization? | A wide range including titanium alloys, stainless steels, nickel alloys, aluminum alloys, and more. |
Is plasma atomization environmentally friendly? | It produces less waste compared to other methods but is energy-intensive, relying on non-renewable energy sources. |
Can plasma atomization be scaled for large production? | Yes, it is scalable for industrial production, making it suitable for high-volume manufacturing. |
What are the limitations of plasma atomization? | High initial setup costs, energy consumption, and the need for skilled operation and maintenance. |
How does the powder quality from plasma atomization benefit additive manufacturing? | The high sphericity and uniform particle size improve the consistency and quality of 3D-printed parts. |
Are there any safety concerns with plasma atomization? | Safety measures are necessary due to the high temperatures and energy involved, but with proper protocols, it is safe. |